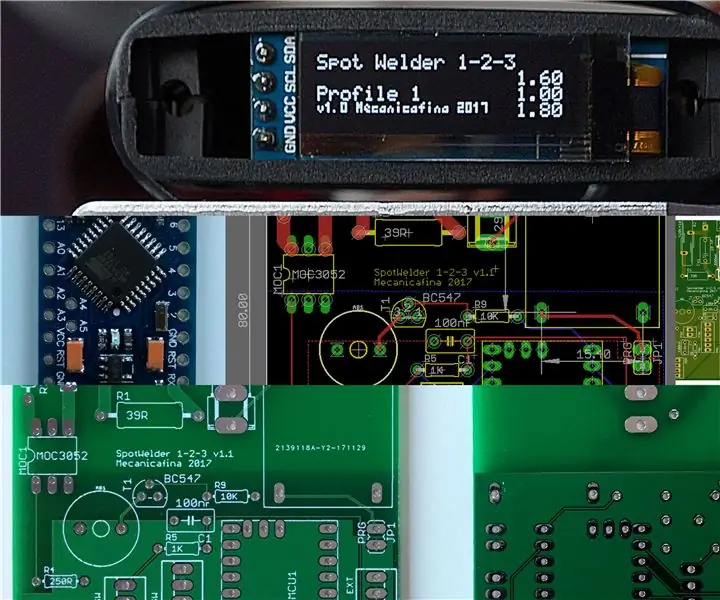
Índice:
2025 Autor: John Day | [email protected]. Última modificação: 2025-01-23 15:03
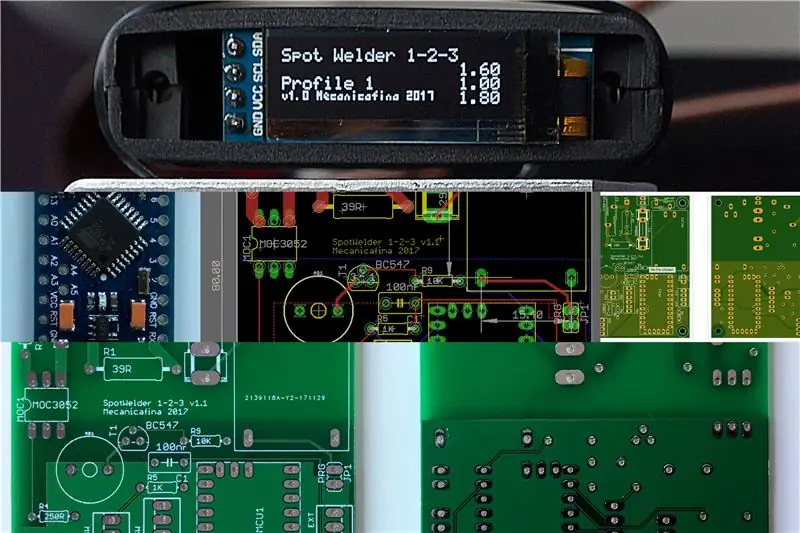
Algum tempo atrás eu escrevi um instrutível onde expliquei como controlar um soldador por pontos de uma maneira sofisticada usando Arduino e peças comumente disponíveis. Muitas pessoas construíram o circuito de controle e recebi um feedback bastante encorajador.
Este é um circuito operando com tensão de rede e altas correntes, portanto a qualidade da construção é importante para garantir operações seguras. Embora seja normal prototipar o soldador esportivo usando uma configuração não permanente, se você planeja construir e realmente usá-lo, um bom PCB ajudará muito a alcançar um resultado profissional e seguro.
Por favor, leia o primeiro instrutível, chamado Parte I para abreviar a seguir, se você ainda não o fez. Há muitas informações lá que não serão repetidas aqui.
AVISO LEGAL: Estou fornecendo alguns links e sugestões para vendedores / fabricantes terceirizados exclusivamente para sua conveniência e para antecipar as perguntas que sei que virão. Não tenho qualquer relação nem interesse em nenhum dos terceiros que mencionei. Eles puramente funcionaram bem para mim.
Etapa 1: PCB esquemático atualizado
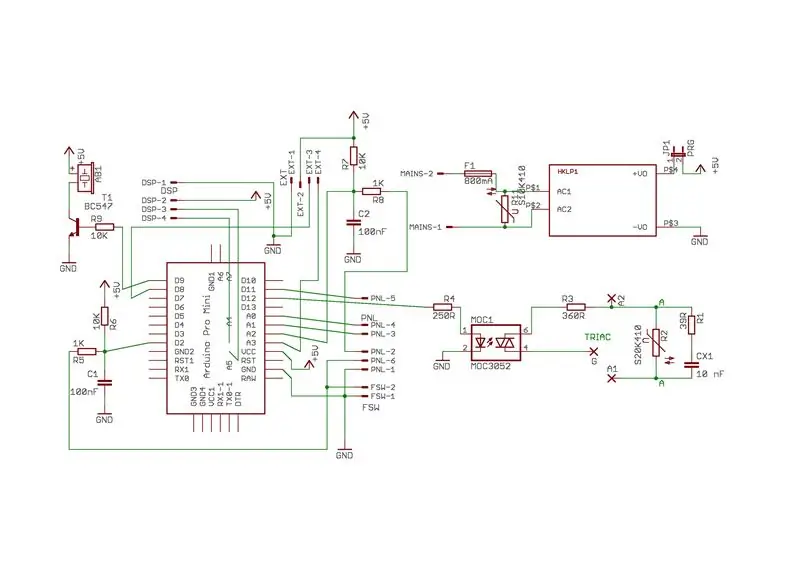
Combinei o controle e o circuito de alimentação em um esquema completo, onde vários componentes são adicionados ao simplificado (embora funcional) na Parte I.
Isso inclui agora fusível e proteção de linha a bordo, e uma campainha para apoiar a produção de sons (um som de clique quando o codificador é girado e um tom contínuo durante a soldagem são bastante bons). Um pino MCU adicional é exposto em um conector para expansão ou modificação de firmware, a fim de adicionar novos recursos (conector EXT), por exemplo, um controle de temperatura ou ventilador de resfriamento. A ativação da campainha e do conector EXT exigirá melhorias futuras de firmware.
Etapa 2: Layout da placa
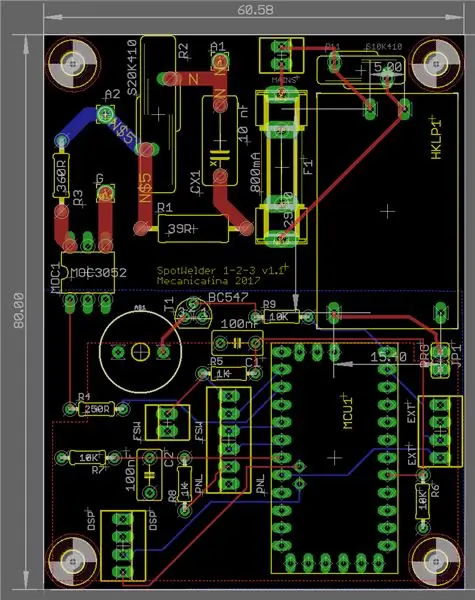
O PCB é um layout padrão de 2 camadas e na imagem você pode ver como os componentes foram organizados usando o software de layout EagleCAD.
Eu tentei manter as coisas bem compactas usando apenas um lado da placa para os componentes e separei a bordo o lado quente e o lado frio (jargão para circuitos de tensão AC e 5V DC). A placa tem cerca de 60 x 80 mm (menos de 2,5 x 3,5 polegadas), portanto, caberá em um gabinete compacto.
Montagem TRIAC. Leia atentamente as considerações sobre isso na Etapa 6 da Parte I. Com relação à seção transversal do fio para as conexões ao TRIAC, usei fio de 1,5 mm2 (AWG 15-16) para os fios que conectam as pastilhas de arame A1, A2 e G aos terminais TRIAC e 2,5 mm2 (AWG 13) para os fios que conectam os terminais TRIAC ao MOT (fios marrons marcados com A na imagem na Etapa 6 da Parte I). Mantenha essas conexões razoavelmente curtas, não deve haver necessidade de que excedam o comprimento de 20-30 cm (8-12”).
Etapa 3: Obtendo o PCB
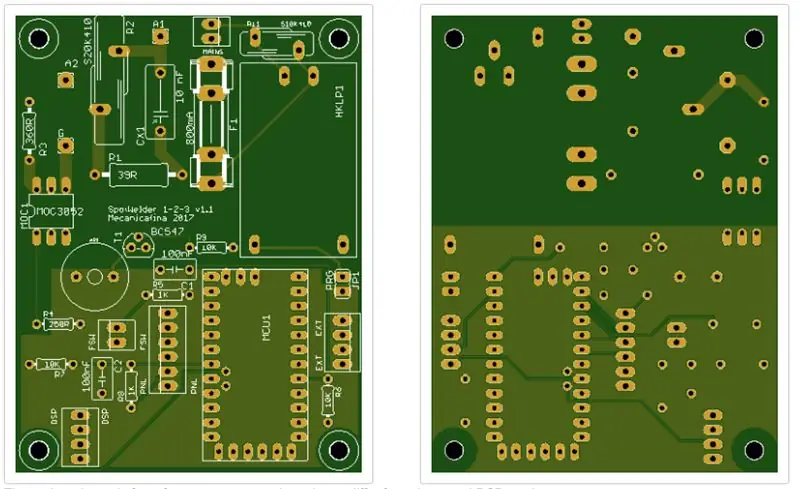
Você pode solicitar o PCB de sua fábrica preferida, se tiver uma. Eu uso o JLCPCB (www.jlcpcb.com) e, em minha opinião, eles fazem um excelente trabalho a um preço muito razoável.
Estou fornecendo os arquivos Gerber necessários em um arquivo de dados, então você não precisa ser capaz de usar o EagleCAD para solicitar um PCB, apenas atualize o arquivo zip no site da fab house e você estará no negócio. Outros fornecedores trabalharão de maneira semelhante.
Os componentes necessários para este circuito são muito fáceis de obter. De qualquer forma, estou fornecendo uma lista de materiais para sua conveniência, com links para as fontes que usei para obter as menos óbvias.
Tenha cuidado ao solicitar o Pro Mini. Existem vários layouts ao redor, mas o PCB é dimensionado para caber na embalagem da versão Pro Mini mostrada na imagem a seguir. Outras geometrias não se encaixam no padrão de orifício do PCB.
O PCB requer a versão 3W do módulo de fonte de alimentação Hi-Link (HLK-PM01 3W). A variante 5W não caberá.
O jumper JP1 marcado com PRG deve ser aberto para atualizar o firmware sem remover o Pro Mini do PCB e, obviamente, mantido fechado para operação normal.
Esta é a versão 1.1 do PCB e requer o firmware da versão 1.1
Este PCB suporta um buzzer para enriquecer a interface com sons, porém o firmware da versão 1.1 não faz uso do hardware do buzzer (desculpas por não deixar isso claro)
Etapa 4: Downloads
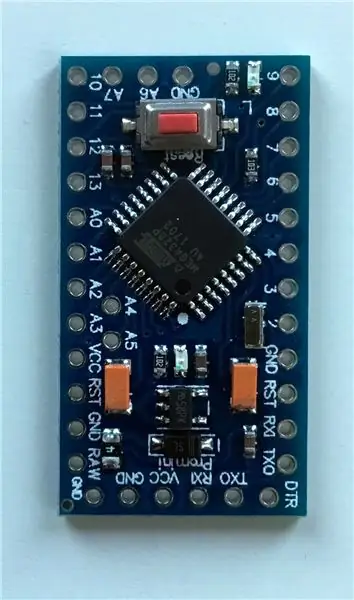
Os arquivos de dados do PCB podem ser baixados do repositório do SpotWelder 1-2-3 PCB (este é o PCB versão 1.1 e requer o firmware da versão 1.1).
No arquivo REAME do repositório, você encontrará um índice.
Divirta-se!
Recomendado:
Como soldar LEDs piscantes em uma placa de circuito impresso em branco: 5 etapas
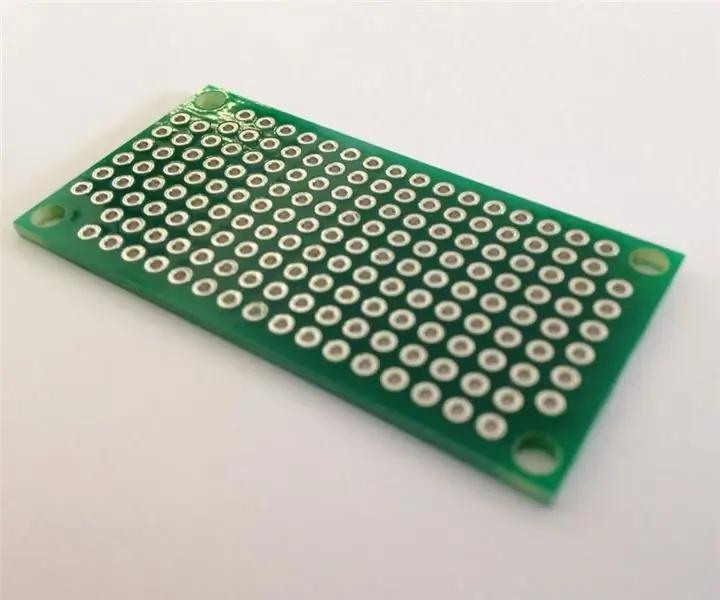
Como soldar LEDs piscantes em um PCB vazio: Um PCB é um acrônimo para " Placa de circuito impresso ". Em um PCB, você vai. Um PCB tem orifícios onde você pode deslizar no componente e, no outro lado, você pode soldar as pernas dos componentes para mantê-los no lugar. Soldar também é v
Placa de circuito impresso de programação ESP01: 5 etapas
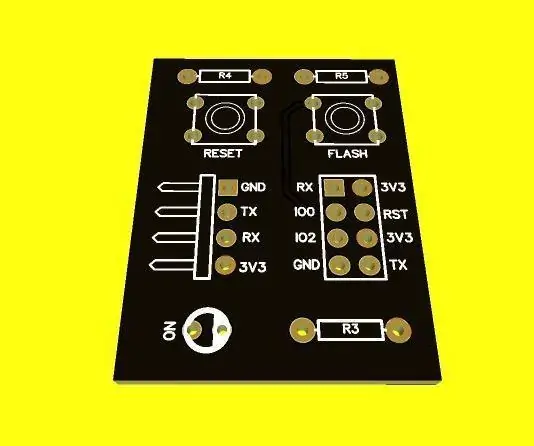
Placa de circuito impresso de programação ESP01: Recentemente, tive que escrever um código no meu ESP01 e decidi usar um adaptador para transferir o código para o CHIP. Porém, foi necessário fazer algumas modificações no adaptador para que o código pudesse ser transferido. Ou seja, o adaptador não estava inteiro
Caneta de soldador local super simples DIY (Caneta de soldador com guia de bateria MOT) 10 $: 7 etapas (com fotos)
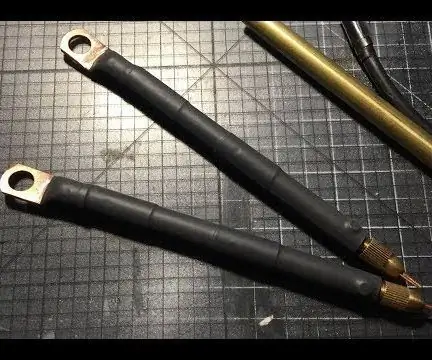
Caneta de soldador Spot DIY Super Simples (MOT Battery Tab Welder Pen) 10 $: Eu estava olhando todos os sites online que vendiam canetas de soldador Spot e vi como muitas delas foram montadas. Eu me deparei com um conjunto que era mais barato do que o resto, mas ainda um pouco mais do que eu poderia pagar. Então eu percebi algo. Tudo que eles
Como fazer um circuito de pisca-pisca de LED duplo na placa de circuito impresso: 11 etapas
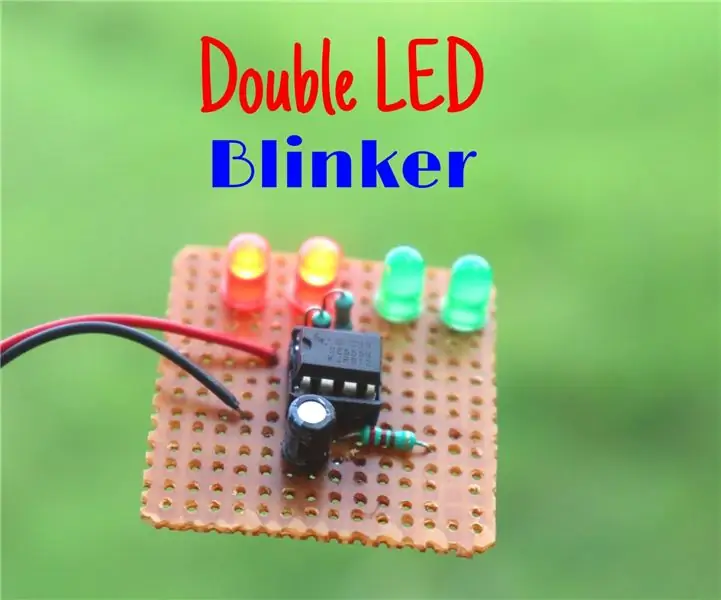
Como fazer um circuito de pisca-pisca de LED duplo na placa de circuito impresso: Olá amigo, Hoje vou fazer um circuito de projeto de pisca-pisca de duplo LED. Este circuito é feito por Timer IC 555. Vamos começar
Como fazer uma placa de circuito impresso profissional: o guia completo: 10 etapas (com fotos)
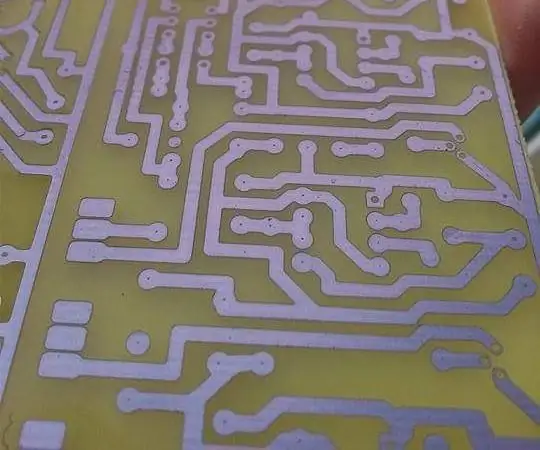
Como Fazer uma Placa de Circuito Impresso Profissional: o Guia Completo: Olá a todos, hoje vou mostrar como fazer uma PCB profissional, para melhorar seus projetos eletrônicos. Vamos começar