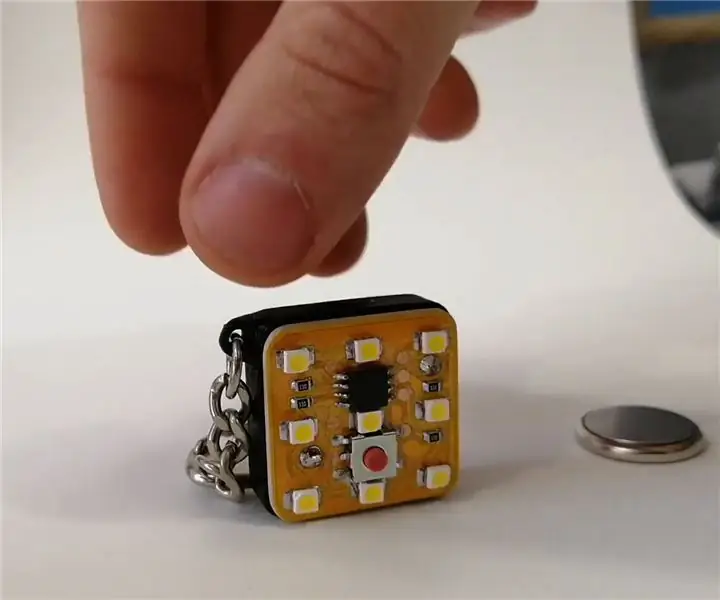
Índice:
- Etapa 1: materiais, suprimentos e ferramentas
- Etapa 2: prepare todos os adesivos
- Etapa 3: Etch o Cobper Clad
- Etapa 4: cortar e lixar os dados
- Etapa 5: aplicando os adesivos da máscara de solda Kapton
- Etapa 6: Monte os Dados: Aplicação da Pasta de Solda
- Etapa 7: População e solda por refluxo
- Etapa 8: imprimir em 3D as capas das chaves
- Etapa 9: Faça um gabarito de programação
- Etapa 10: Programando os dados
2025 Autor: John Day | [email protected]. Última modificação: 2025-01-23 15:03
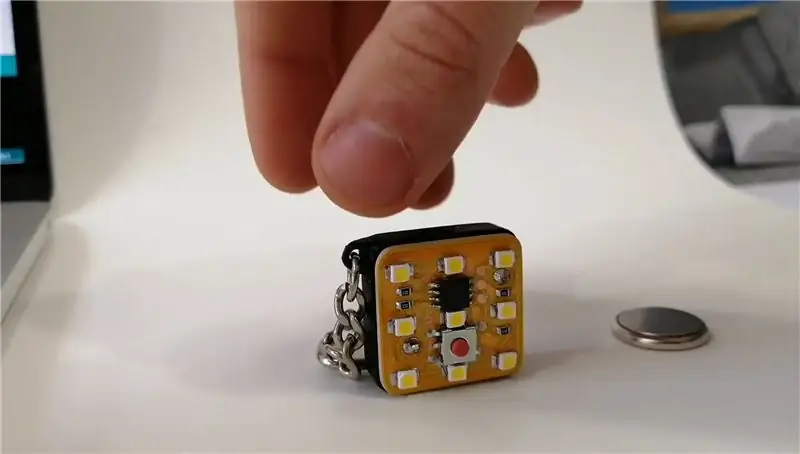
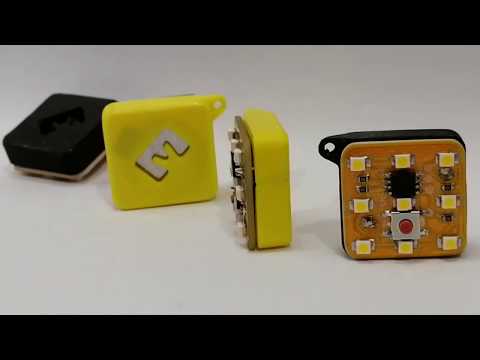
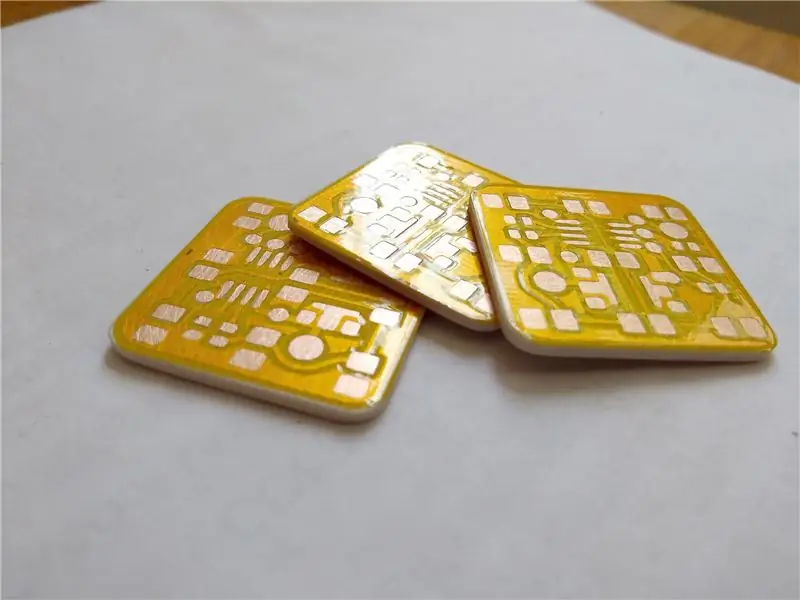
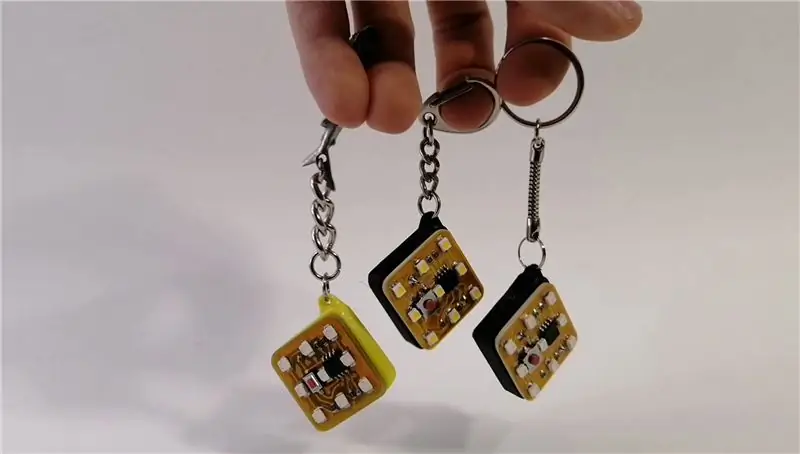
Este instrutivo consiste em um guia passo a passo que documenta um método de fabricação de PCBs de qualidade profissional em casa por meio do uso de um cortador de vinil, de maneira confiável, simples e eficiente. Este método permite a produção de PCBs consistentes e de alta qualidade em casa com poucos materiais comuns e em um período de tempo muito curto. Com todos os arquivos prontos, todo o processo pode ser realizado em poucas horas.
Assunto do guia, tinyDice:
Para efeito deste guia, o processo será ilustrado com a produção de um lote de 3 tinyDice, um dado eletrônico baseado no microcontrolador atTiny85 com software charlieplexing, que permite o controle de 9 LEDs com apenas 4 pinos e 4 resistores. É uma versão melhorada do meu tinyDice original (2014), e todos os arquivos de origem necessários para este Instructable estão disponíveis para download como um pacote compactado na etapa de suprimentos.
Origem do método:
Como um entusiasta da eletrônica, tive minha cota de experiência com a fabricação de PCBs no passado, mas a maioria dos métodos domésticos são excessivamente não confiáveis, como o método de transferência de toner, ou excessivamente complexos e trabalhosos, como o método de roteador CNC ou UV método fotorresistente (que já cobri no tinyDice original). Além disso, a qualidade final dos produtos tende a ser bastante ruim, especialmente se você tentar implementar máscaras de solda UV com tok.
A partir dessas experiências insatisfatórias, decidi explorar métodos alternativos para criar PCBs em casa. Como comecei recentemente a experimentar um cortador de vinil de mesa, me ocorreu que um selo de vinil poderia ser uma máscara excelente e confiável para gravação de PCB. Na pesquisa online inicial, não encontrei nenhuma referência de pessoas usando carimbos de vinil para fazer PCBs, o que me surpreendeu, pois parece muito plausível. Isso me motivou a experimentar o processo e descobrir se ele poderia funcionar de forma confiável e eficiente para transferir traços de PCB do computador para o cobre.
Desenvolvimento dos processos:
Fazer traços de cobre limpos e consistentes em um PCB doméstico é em si uma conquista, mas para que os PCBs funcionem corretamente e durem muito, eles requerem algum tipo de máscara de solda, que evita pontes de solda indesejadas e protege os traços de cobre da corrosão. Tradicionalmente, a máscara de solda usada tem a forma de uma resina curável por UV, que na prática é bastante difícil de trabalhar.
Originalmente, eu pretendia usar vinil doentio indiretamente como uma máscara para curar a máscara de solda UV. No entanto, em várias tentativas, não consegui fazer a máscara de solda UV curar de forma confiável apenas nos locais pretendidos e nunca fui capaz de fazer uma camada suficientemente fina e uniforme, o que acabou resultando em um monte de placas estragadas. Assim, descartei a ideia e me ocorreu que talvez algum tipo de carimbo também pudesse ser usado diretamente como máscara de solda, embora certamente não pudesse ser de vinil, pois não suportaria o calor da solda por refluxo.
Com isso em mente, procurei a fita Kapton, que é autoadesiva, fina e promete resistir a altas temperaturas o suficiente para a soldagem. A fita Kapton é vendida em rolos, mas me ocorreu que, se fosse aplicada sobre o verso de um vinil convencional, poderia ser cortada diretamente no cortador de vinil e usada diretamente como selo. Desde a primeira tentativa, ficou evidente que a fita Kapton se comportou de maneira bastante promissora no cortador de vinil, embora todos os cortes que passaram por pequenas bolhas fossem irregulares ou incompletos, então a chave para os selos Kapton perfeitos era aplicar a fita perfeitamente no forro de vinil sem permitir que o ar fique preso embaixo. Isso inicialmente provou ser bastante complicado, já que Kapton é excessivamente fino e pegajoso, mas ao tentar colocá-lo em um cartão de plástico padrão, percebi que poderia ser feito perfeita e facilmente dessa forma.
Por meio desses testes iterativos, também observei algumas das limitações práticas do processo, que mailny tem a ver com a máscara de cobre ser originalmente um selo. Essas limitações evoluíram para um conjunto de diretrizes de design para tornar esse processo confiável.
Etapa 1: materiais, suprimentos e ferramentas
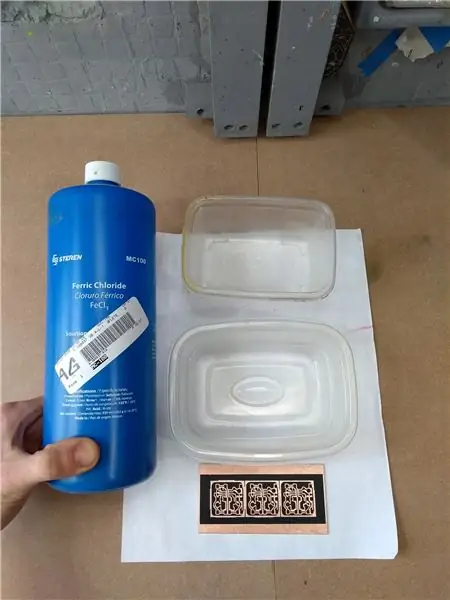
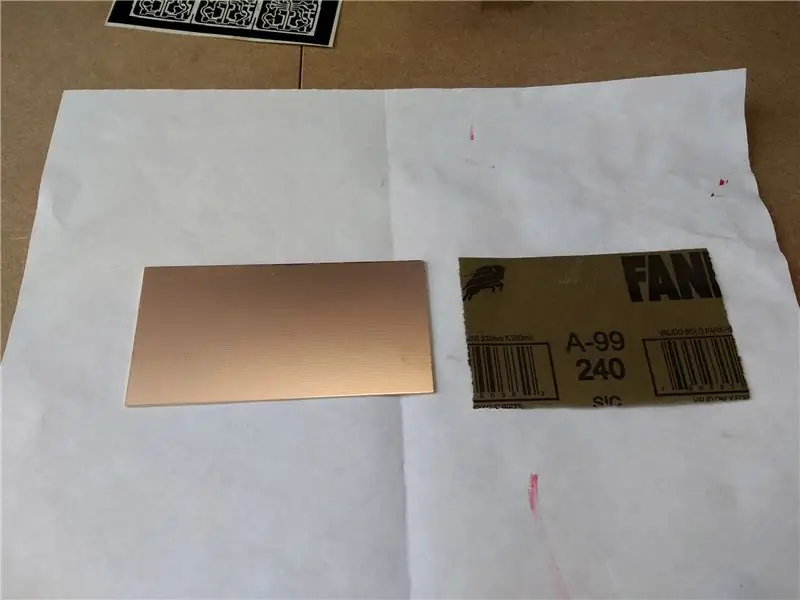
Materiais:
- PCB vazio de 5 x 10 cm
- Vinil autoadesivo de 10 x 15 cm
- Fita Kapton de 50 mm de largura
- Filme de transferência de vinil de 10 x 15 cm
Suprimentos:
- Cloreto férrico etchant
- Álcool isopropílico
- Pasta de Solda
- Filamento PETG (para a caixa do chaveiro)
Ferramentas:
- cortador de vinil de mesa (eu uso a Silhouette Cameo 3, mas qualquer máquina básica funciona)
- Estação de retrabalho de ar quente (não indispensável, mas útil)
- ferro de solda
- cartão de plástico (carteira de identidade antiga ou qualquer tipo)
- USBtinyISP ou Arduino como ISP
- cortador manual de acrílico (pode ser feito em casa a partir de uma seção de lâmina de serra antiga)
- Lixa 220 e 400
- Impressora 3D (opcional, apenas para fazer a capa do chaveiro)
Programas:
- Silhouette Studio (ou equivalente para outras marcas de cortadores de vinil)
- EAGLE CAD (não necessário se você não pretende modificar o design)
- Photoshop ou qualquer editor de imagens (não é necessário se você não pretende modificar o design)
- Arduino IDE + atTinyCore
- AVRDUDESS
- Slic3r ou qualquer outro software de impressão 3D.
-
pacote de recursos tinyDice, (disponível para download nesta etapa como um arquivo RAR)
Componentes:
para cada tinyDice85:
- 9 LEDs SMD 3528 (de qualquer cor, recomendados todos iguais)
- 1x attiny85 (SOIC)
- 4x 33 ohm 0805 resistores (o valor exato não é crítico, use qualquer valor semelhante, mas todos iguais!)
- 1x botão SMD
- 1 clipe de bateria CR20XX
- 1 bateria CR2032
Para o gabarito de programação:
- 6 pinos pogo
- 1x cabeçalho macho 2x3 (para ISP)
- 1x conector macho 2x1 (para fonte VCC externa)
- 1 regulador AMS1117 3.3v LDO (SOT-23)
Etapa 2: prepare todos os adesivos
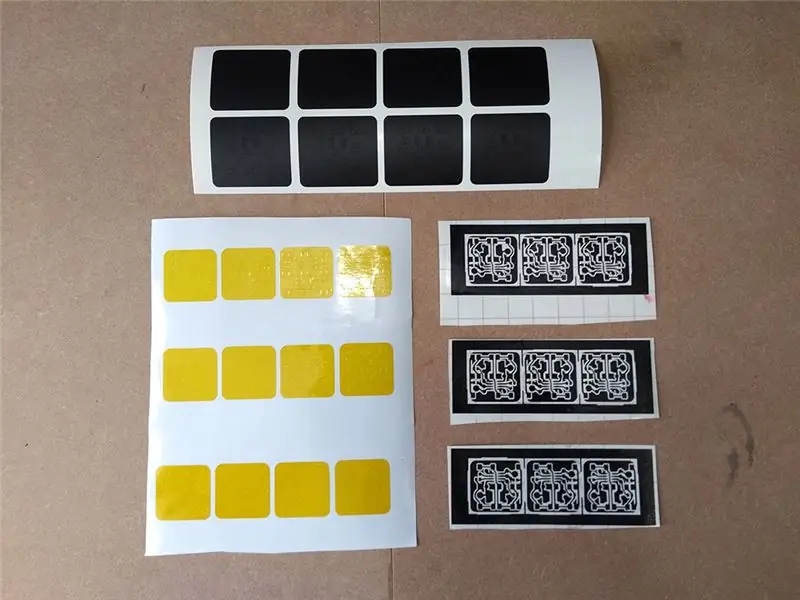
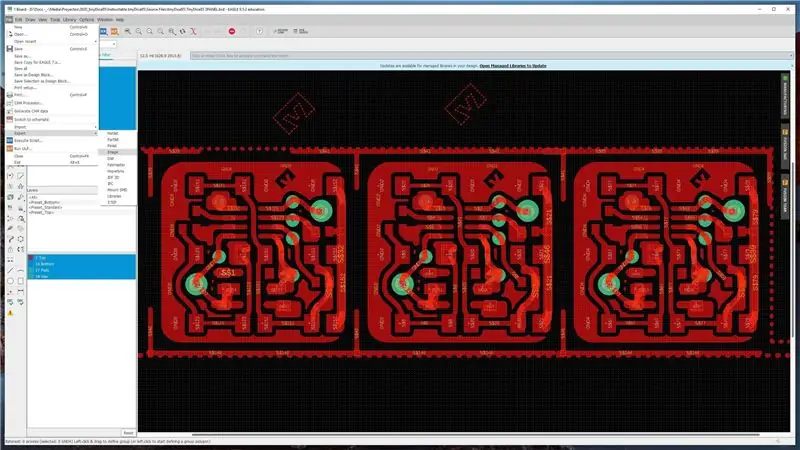
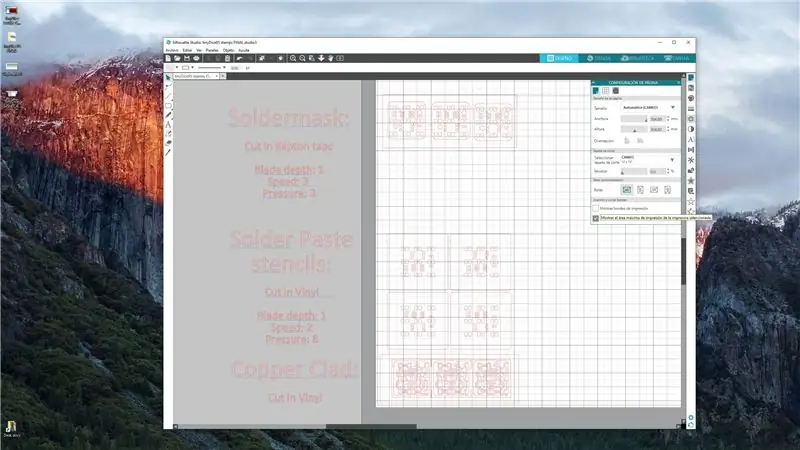
Para esse processo de fabricação de PCBs em casa, os adesivos estão envolvidos em três estágios; Como máscara para gravar o cobre revestido, como máscara de solda para proteger os vestígios e limitar a solda e como estêncil para aplicar pasta de solda nas almofadas. Para otimizar o processo ao máximo, todos os adesivos podem ser preparados em um único assento.
Preparando as limas para corte:
Se você não pretende modificar o design, pode usar diretamente as imagens preparadas ou o arquivo Silhouette Studio com todos os adesivos. Se estiver usando outro desenho, faça o seguinte para preparar o arquivo para corte:
Como a maioria dos softwares de vinil grátis trabalha com imagens, devemos exportar o design do EAGLE como uma imagem de alta resolução. Para isso, primeiro oculte toda a camada exceto TOP e VIAS, então exporte o painel como uma imagem em MONOCROMÁTICO e pelo menos 1500 dpi. Em seguida, repita o processo, mas apenas com a camada Tstop, para obter apenas as almofadas.
Depois de exportar as imagens, é aconselhável fazer um pouco de limpeza no photoshop para aumentar a confiabilidade do processo. Para a imagem revestida de cobre, isso consiste em apagar todas as pequenas áreas isoladas de cobre ou conectá-las a áreas maiores, apagando o centro de todos os orifícios passantes e aumentando a folga em torno das térmicas. Para a imagem das almofadas, você deve ajustá-las sobre uma forma preta que transborde um pouco todo o revestimento de cobre.
Em seguida, importe as imagens para o software do cortador de vinil, trace-as e dimensione-as para um tamanho de 100 x 100 mm. Uma vantagem do painel de PCBs é que você tem uma referência consistente para escalá-los adequadamente, independentemente da resolução.
Preparando a fita Kapton para corte:
A fita Kapton é um ótimo material, no entanto, para usá-la como adesivo, devemos primeiro colocá-la sobre um suporte plano. Para isso vamos utilizar o forro da fita de transferência de vinil, por isso retire o patê e reserve temporariamente, tomando cuidado para mantê-lo limpo. Em seguida, desenrole um segmento de fita adesiva e aplique-o com cuidado no papel de cera usando um cartão de plástico como rodo para garantir que nenhuma bolha fique presa por baixo. Eu recomendo preparar mais do que você espera utilizar, pois alguns adesivos podem não sair perfeitamente.
Cortando os adesivos:
Depois de rastrear e dimensionar todos os adesivos no software do cortador de vinil, coloque o material de vinil autoadesivo em um canto da esteira de corte e a fita Kapton posterior em outro canto.
Em seguida, no software, coloque apenas os desenhos de estêncil de cobre e pasta de solda sobre a área correspondente ao vinil e defina os parâmetros de corte para: Velocidade 3, Profundidade da lâmina 1, Pressão 8. Envie o trabalho para corte e deixe a máquina fazer é coisa.
Finalmente, afaste os desenhos usados anteriormente e coloque apenas o desenho da máscara de solda sobre a área correspondente à fita Kapton. Defina os parâmetros de corte para: Velocidade 1, Profundidade da lâmina 1, Pressão 3. Continue enviando o trabalho para a máquina e, uma vez terminado, remova cuidadosamente o vinil autoadesivo e os materiais Kapton da esteira de corte. Tenha cuidado para não fazer vincos ao removê-los.
Removendo as ervas daninhas:
Para transferir os adesivos de vinil para o PCB, devemos usar um filme de transferência de vinil para garantir que todas as regiões sejam transferidas no lugar. Para poder transferir apenas os segmentos pretendidos do selo, devemos remover todas as áreas indesejadas antes de aplicar o filme de transferência. Para isso, use um cortador e levante cuidadosamente um canto da área indesejada. Enfie o cortador por baixo e pressione o vinil na lâmina para prendê-lo. Em seguida, puxe o cortador para longe e o excesso deve começar a descascar. Dependendo do desenho, todas as áreas indesejadas podem sair como uma única peça. Depois de capinar, coloque o filme de transferência APENAS sobre os adesivos revestidos de cobre e descarte todo o excesso. Neste ponto, os adesivos de vinil estão prontos para uso. Os adesivos da fita Kapton são uma única peça, portanto, podem ser transferidos diretamente, sem o filme de transferência.
Etapa 3: Etch o Cobper Clad
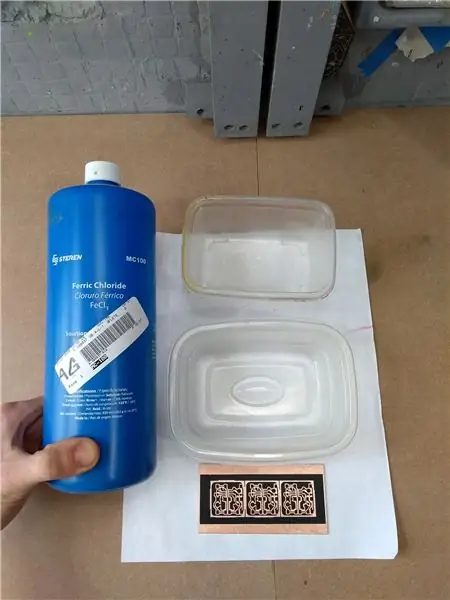
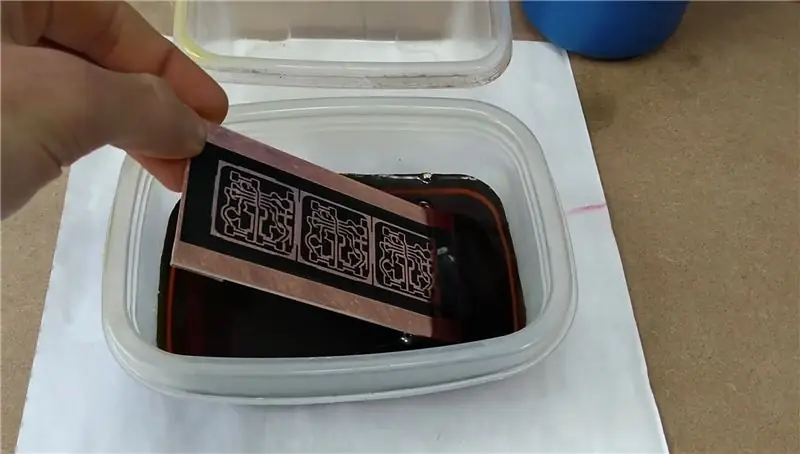
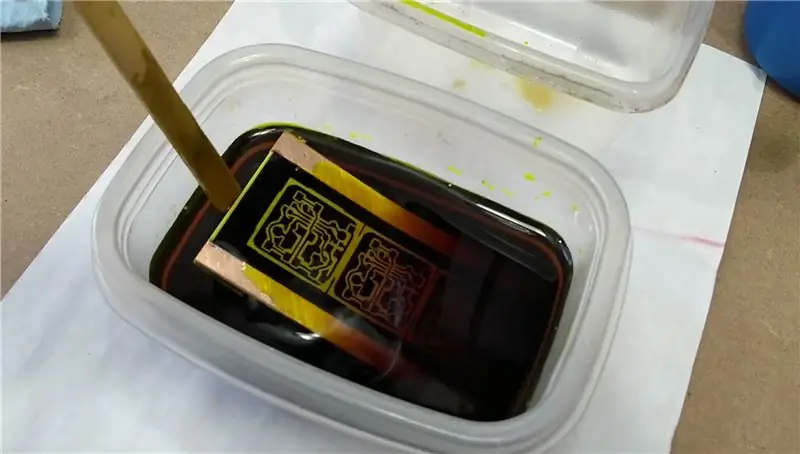
Esta é a etapa mais importante do processo, pois a qualidade dos traços de cobre determinará a taxa de sucesso dos produtos finais. Se feito com cuidado, pode ser 100%.
Transferindo o adesivo CLAD para o cobre:
Para garantir resultados limpos e confiáveis, primeiro você deve desengordurar o PCB em branco com álcool isopropílico. Se a peça em branco for velha, recomenda-se lixar bem a superfície com uma lixa 320-400 fazendo pequenos círculos em toda a placa.
Depois de totalmente limpo, é hora de transferir o adesivo para o cobre. Para isso, primeiro descasque um canto do filme de transferência e, em seguida, coloque o adesivo de cabeça para baixo em uma mesa limpa. Em seguida, descasque lentamente o papel do decalque, fazendo um vinco acentuado e puxando ao longo da mesa. Dessa forma, mesmo as pequenas almofadas devem grudar na transferência e não permanecer no papel. Não se preocupe se um ou dois blocos ficarem para trás, você pode colocá-los manualmente mais tarde.
Em seguida, segure o transfer de vinil com o adesivo usando as pontas dos dedos (cole-os levemente na borda) e alinhe lentamente o adesivo sobre a placa antes de colocá-lo. Uma vez alinhado, coloque-o sobre o cobre e pressione levemente com os dedos FORMA O CENTRO PARA FORA, para evitar bolhas presas. Em seguida, use um cartão plástico para esmagar toda a superfície para garantir que o vinil grude fortemente no cobre. Continue a retirar o filme de transferência de vinil do revestimento de cobre da mesma maneira que você removeu o papel de trás e coloque manualmente quaisquer almofadas que tenham ficado para trás. Se o adesivo não cobrir todo o espaço em branco, você pode cobrir todas as áreas restantes com fita adesiva transparente para evitar o excesso de cobre e o uso excessivo dos suprimentos.
Gravando o revestimento de cobre:
Para o processo de gravação, você precisará de 2 recipientes retangulares do tipo Tupperware, um pequeno bastão de madeira e o ácido clorídrico de cloreto férrico.
A placa preparada com o carimbo CLAD está quase pronta para o ataque ácido, mas é muito importante limpá-la mais uma vez com álcool isopropílico para remover qualquer resíduo do filme de transferência e garantir uma corrosão uniforme e completa, sem resíduos indesejados de cobre.
Para preparar o cloreto férrico para o ataque, despeje-o em um dos recipientes até cerca de meio cheio e adicione cerca de 30% a mais de água. Neste ponto, a solução está pronta para o ataque, no entanto, você pode opcionalmente aquecê-lo no forno de micro-ondas por 15 segundos ANTES da colocação no PCB para acelerar o processo de corrosão.
Por fim, coloque a placa no cloreto férrico e deixe-a afundar. O processo pode demorar um pouco, mas é importante voltar a cada 10 a 15 minutos para mexer a solução e verificar o andamento. Para isso, basta usar um pequeno pedaço de madeira para alcançar a placa e inclinar para dentro e para fora da solução algumas vezes. Isso moverá a solução para garantir que ela reaja uniformemente e permitir que você veja quanto do cobre foi removido. Continue fazendo isso até que você não veja mais cobre exposto, mas não espere mais, pois o acondicionador pode começar a romper sob o adesivo e danificar os vestígios. Nesse ínterim, deixe o palito no outro recipiente para evitar manchar qualquer coisa com a solução acondicionadora, pois é muito propenso a manchas e também possui um odor ferroso muito forte.
Uma vez feito isso, retire a placa do acondicionador e enxágue-a abundantemente com água e sabão em abundância. Depois disso, pegue um funil ou faça um com uma folha de plástico e fixe-o sobre uma garrafa de PP vazia para recuperar e armazenar o acondicionador. NUNCA descarte o cloreto férrico gasto pelo ralo, reutilize-o tanto quanto possível e descarte-o deixando-o secar e, em seguida, descarte-o como sólido.
A gravação é a etapa mais demorada do processo. Se feito com cloreto férrico fresco, pode ser feito em menos de uma hora, no entanto, com suprimentos reutilizados pode levar mais de 4 horas para ser concluído, então seja paciente e verifique periodicamente.
Etapa 4: cortar e lixar os dados
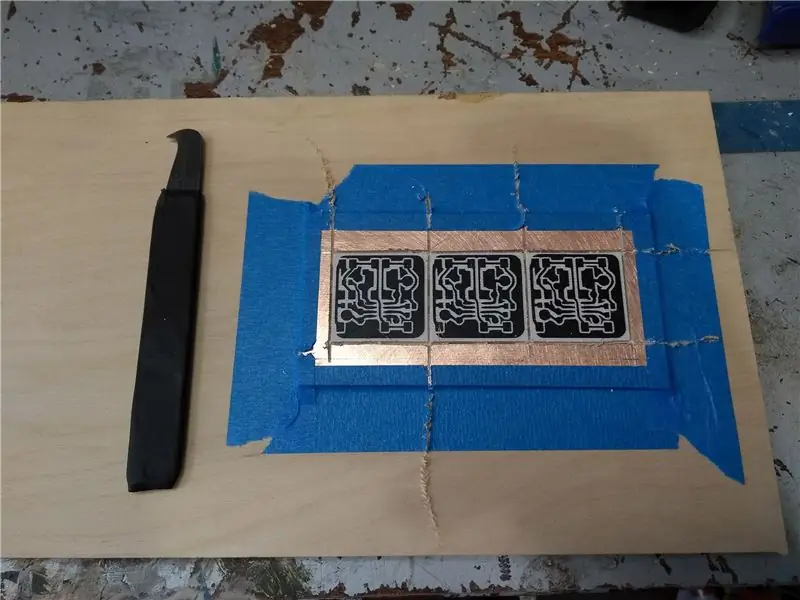
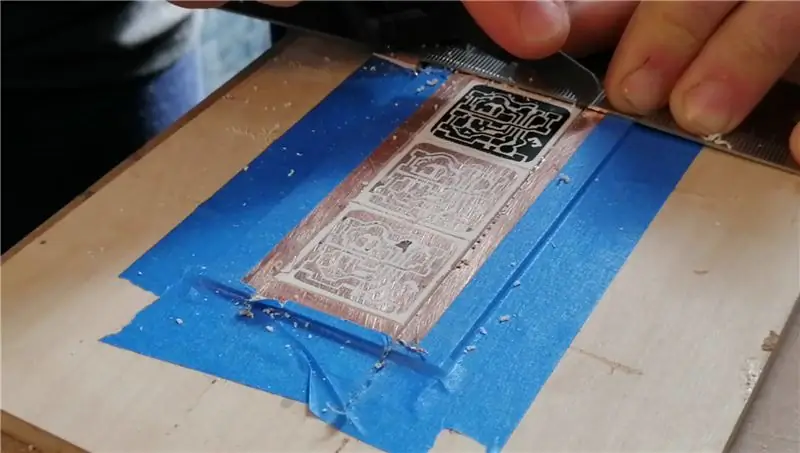
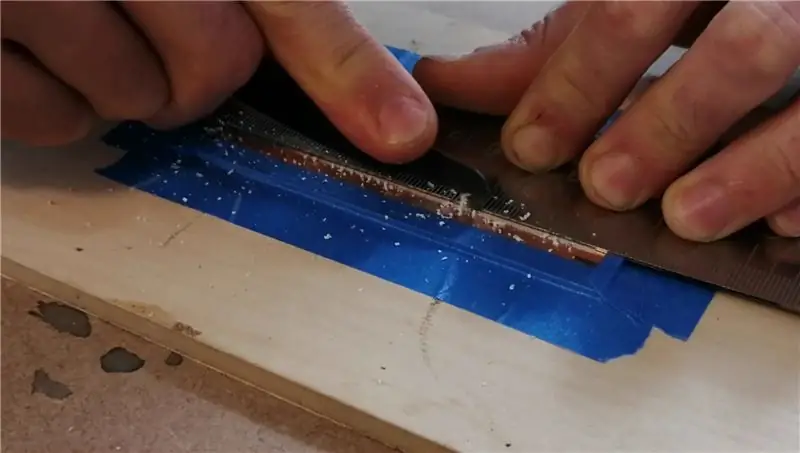
Uma vantagem de painéis PCBs é que você pode usar o painel como um guia para o corte, além de ser mais fácil de manusear uma placa maior. Para separar as pranchas e dar-lhes um acabamento adequado, devemos primeiro cortá-las e lixar as arestas e cantos.
O corte do PCB não pode ser feito com um cortador comum, tesoura ou serra, pois esses processos quase certamente falhariam ou danificariam as placas. Para o corte, utilizaremos uma ferramenta de garra simples que gradualmente raspa as camadas em cada passagem, abrindo uma ranhura em todo o caminho. Essas lâminas são vendidas comercialmente como cortadores de acrílico, mas também podem ser feitas em casa com algumas lâminas de serra quebradas. é aconselhável afiar a lâmina durante o processo, pois as placas de fibra de vidro desgastam rapidamente. Não é necessário cortar todo o caminho, apenas a maior parte do caminho, e depois, basta quebrar cada pedaço.
Após o corte, as arestas são bastante ásperas e irregulares, por isso devemos lixá-las bem primeiro com uma lixa 240 e depois com cerca de 400 para obter uma lixa extra. Certifique-se também de arredondar os cantos, seguindo a forma do revestimento de cobre.
Por fim, use um cortador para retirar cuidadosamente os adesivos das placas. Isso pode ser feito antes do corte, mas os adesivos ajudam a proteger o cobre durante o processo de corte.
Etapa 5: aplicando os adesivos da máscara de solda Kapton
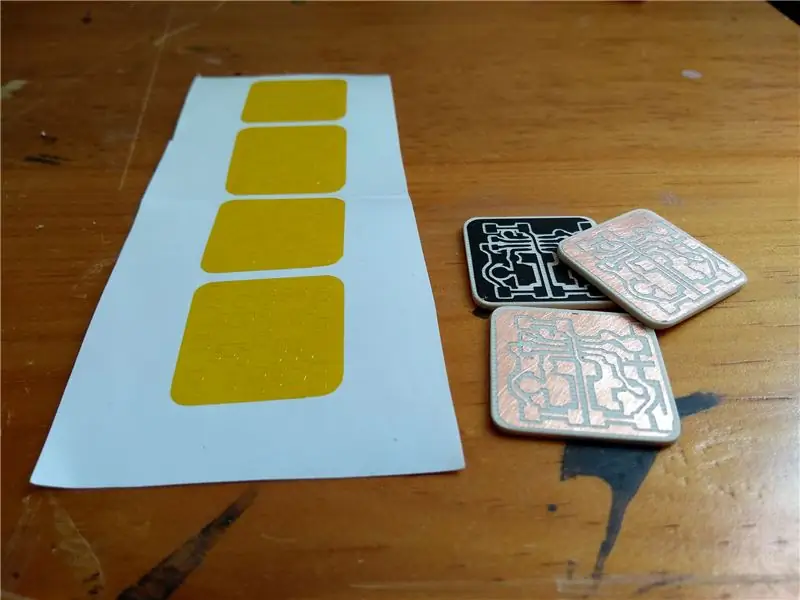
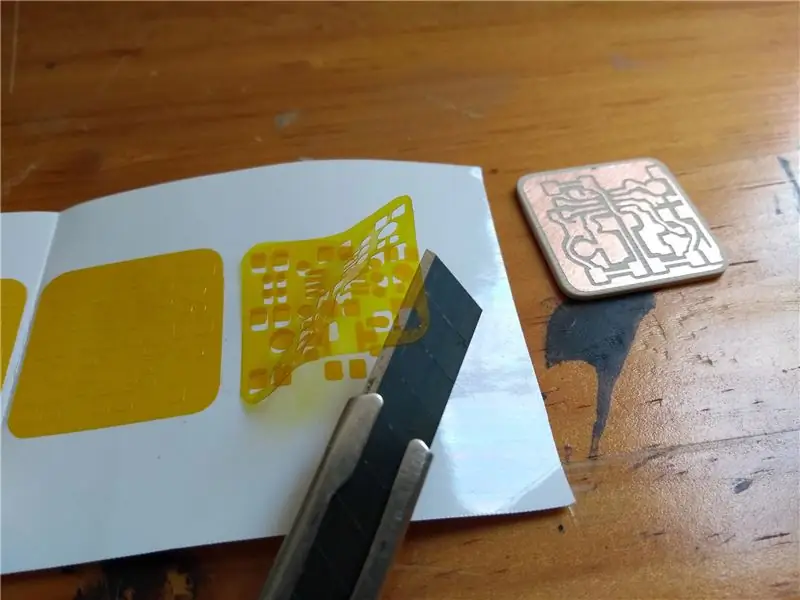
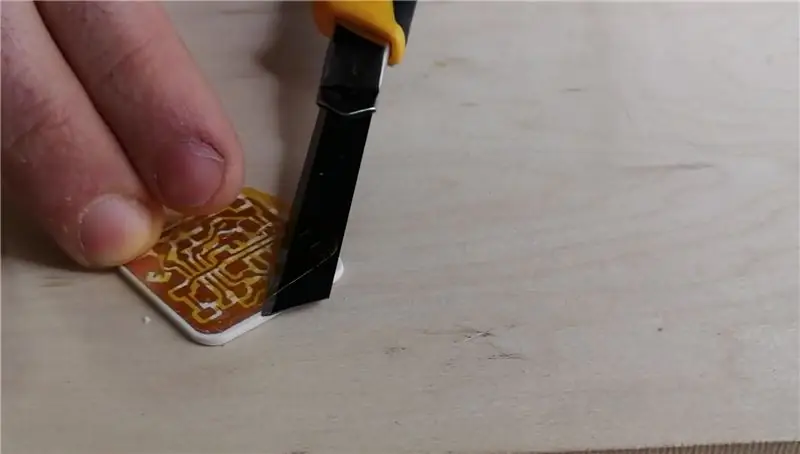
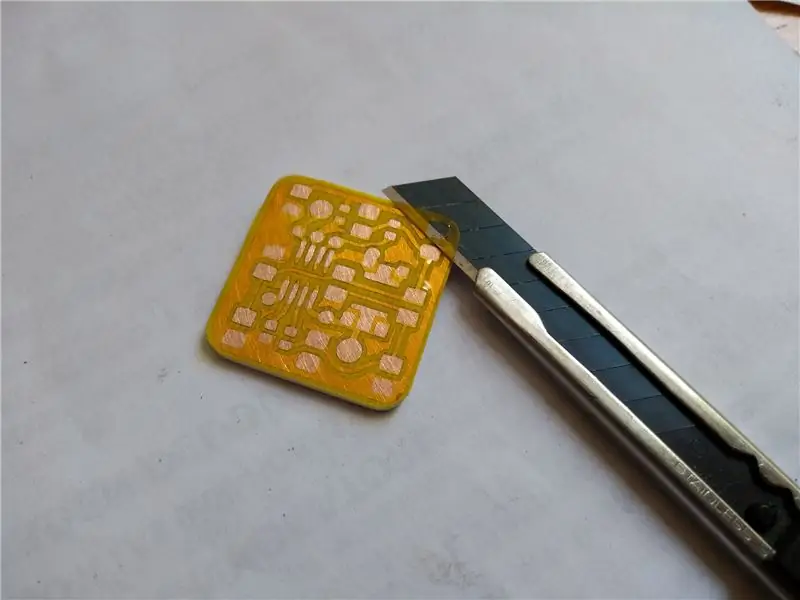
Já com as placas cortadas, estamos quase prontos para montar o circuito, porém, para garantir que os vestígios de cobre fiquem protegidos a longo prazo e a solda fique apenas onde deveria, exigimos uma máscara de solda, que é feita de forma convencional com resinas de cura UV. O processo tradicional é bastante tóxico, confuso e não confiável, portanto, é necessária uma alternativa mais prática para a fabricação doméstica.
Neste caso, exploramos a fita Kapton como máscara de solda devido à sua resistência a altas temperaturas e propriedades autoadesivas. Para transferir os adesivos para os PCBs, usaremos novamente o cortador como suporte. Antes de transferir os adesivos, limpe bem os PCBs com álcool isopropílico para remover qualquer gordura ou resíduo do vinil. Em seguida, comece a levantar cuidadosamente o adesivo Kapton do papel de suporte com o cortador (veja a imagem 2). Para isso, primeiro levante um pequeno canto do adesivo com o cortador e pressione-o contra a lâmina para fazê-lo grudar, em seguida, puxe lentamente o cortador para longe do papel sem fazer um vinco na borda afiada até que todo o adesivo saia do papel e fica preso à lâmina.
Finalmente, é importante garantir que o adesivo esteja devidamente alinhado com as almofadas antes de fixá-lo no lugar, então traga-o suavemente sobre a PCB com o cortador e escove-o levemente sobre a placa algumas vezes, isso irá carregá-lo com estática e fazer ele meio que flutua na superfície, o que permitirá que você ajuste o posicionamento antes de pressioná-lo no lugar. Se o carimbo grudar prematuramente, retire-o com cuidado do cartão ao retirá-lo do papel e repita o alinhamento. Uma vez devidamente alinhado, pressione-o firmemente no PCB com os dedos e retire cuidadosamente o cortador do adesivo para terminar de colocá-lo. Em seguida, limpe as placas novamente com álcool e agora os PCBs estão oficialmente finalizados. Eles podem ser usados imediatamente ou estocados para uso posterior.
Etapa 6: Monte os Dados: Aplicação da Pasta de Solda
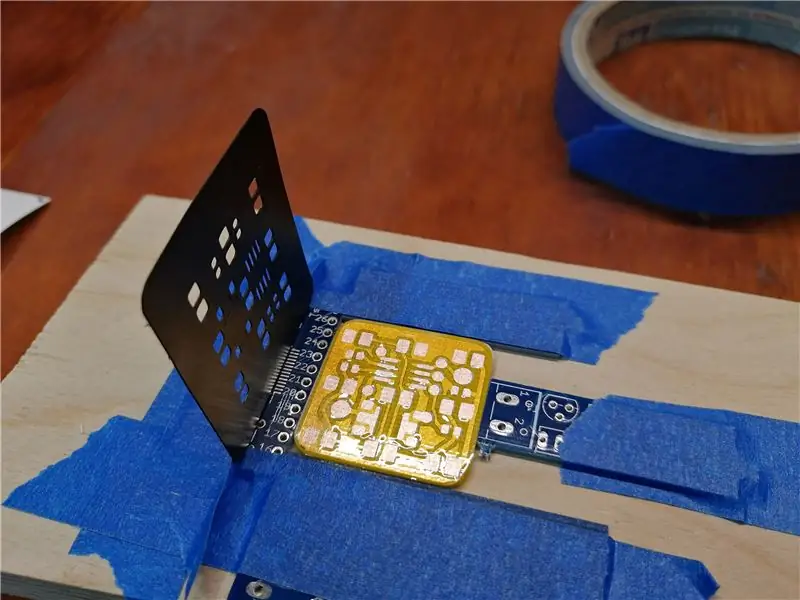
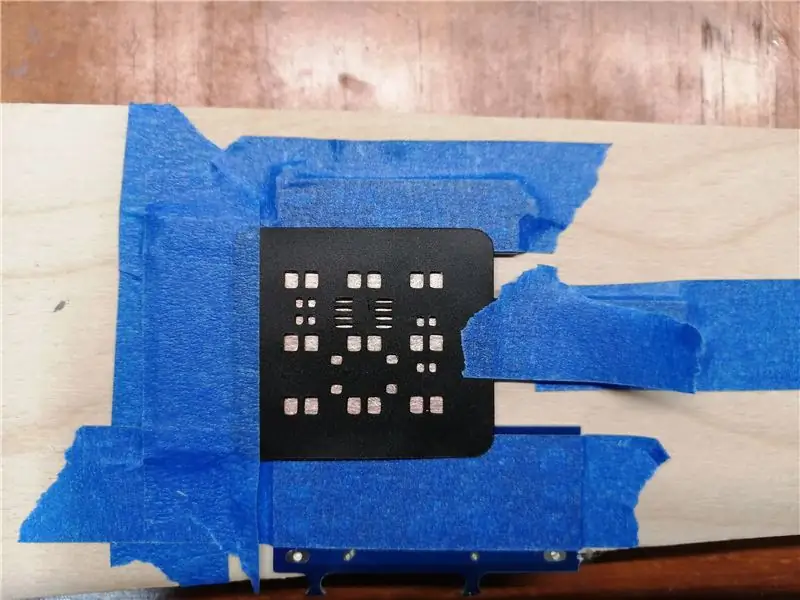
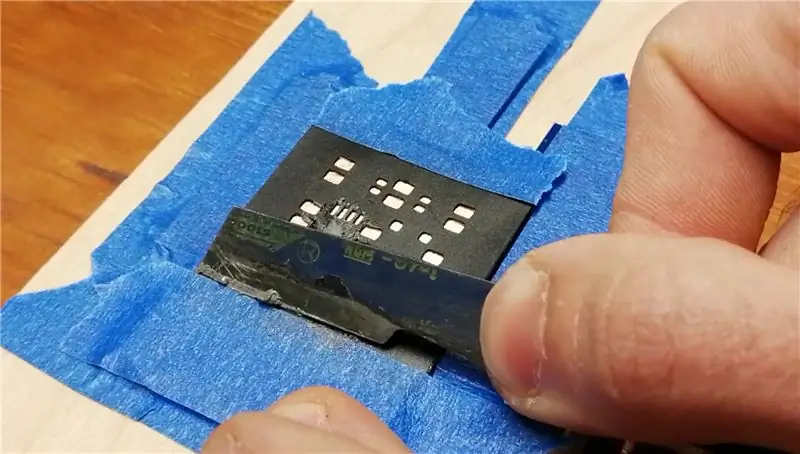
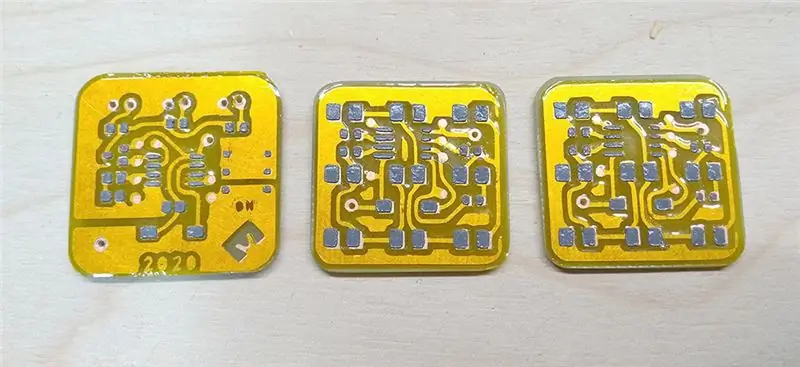
Uma vantagem dos circuitos SMD é que eles podem ser soldados com pasta de uma maneira muito confiável e rápida, usando um estêncil simples para aplicá-lo apenas nas almofadas, que podem ser reutilizadas em qualquer número de unidades. Os estênceis SMD convencionais são fabricados em aço, por isso são bastante caros e pouco práticos para a prototipagem; no entanto, o estêncil também pode ser feito de adesivos de vinil. Para isso, utilizamos o original e uma versão espelhada do adesivo para criar um estêncil de plástico que não seja autoadesivo.
Pasta de solda contém uma grande quantidade de fluxo, portanto, reduz significativamente ao refluir. Portanto, precisamos aplicar uma camada espessa o suficiente para garantir que as juntas sejam preenchidas corretamente com a solda. Para fazer o estêncil da espessura adequada, devemos colocar 4 adesivos de vinil juntos. Faça isso com cuidado para garantir que os orifícios estejam perfeitamente alinhados em toda a extensão.
Em seguida, construa uma pequena borda em torno de uma placa de PCBs ou qualquer outro material da mesma espessura e fixe o estêncil no lugar por um único lado para servir como uma dobradiça, garantindo o alinhamento adequado do estêncil sobre as almofadas (ver imagem 2)
Finalmente, usando qualquer tipo de ferramenta de ponta reta, pegue um pouco de pasta de solda e comece a espalhar sobre o estêncil até que todos os buracos sejam preenchidos, e raspe o restante de volta para o frasco com a mesma ferramenta. Não toque na pasta de solda diretamente, pois ela contém chumbo, que deve ser evitado. Não se preocupe se você tocar nele, apenas limpe-o completamente.
Levante o estêncil e remova a placa do gabarito. Repita o processo para todas as placas que pretende montar. Agora as placas estão prontas para preencher e soldar.
Etapa 7: População e solda por refluxo
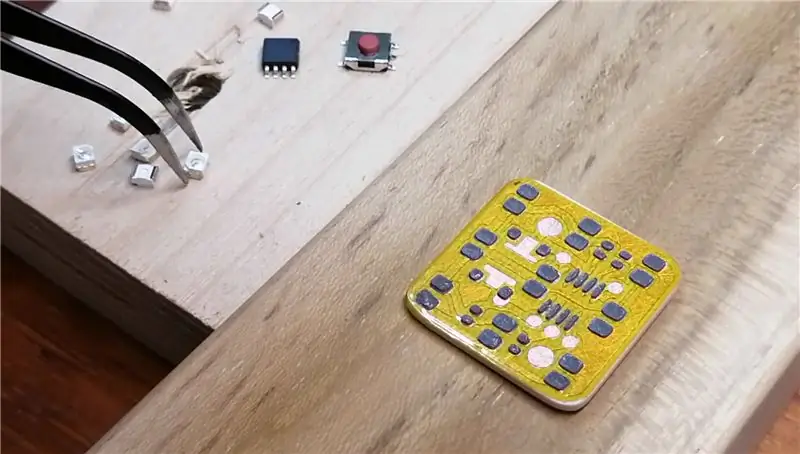
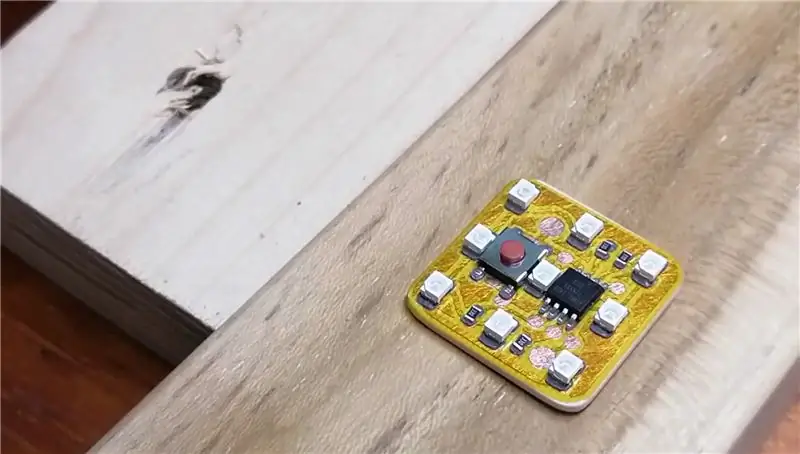
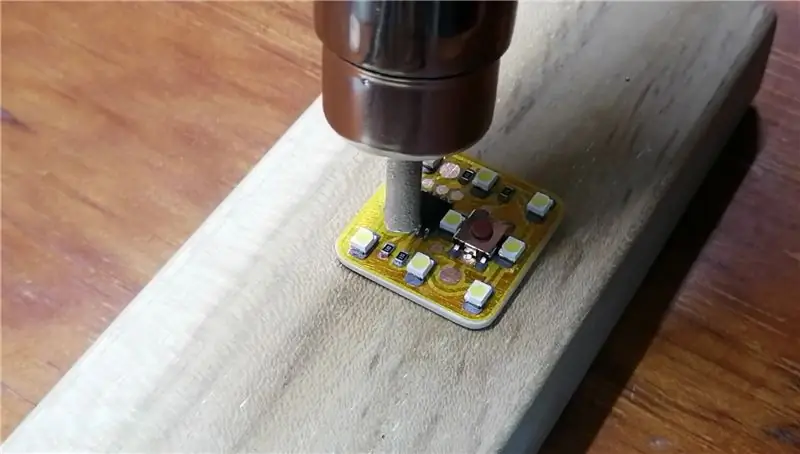
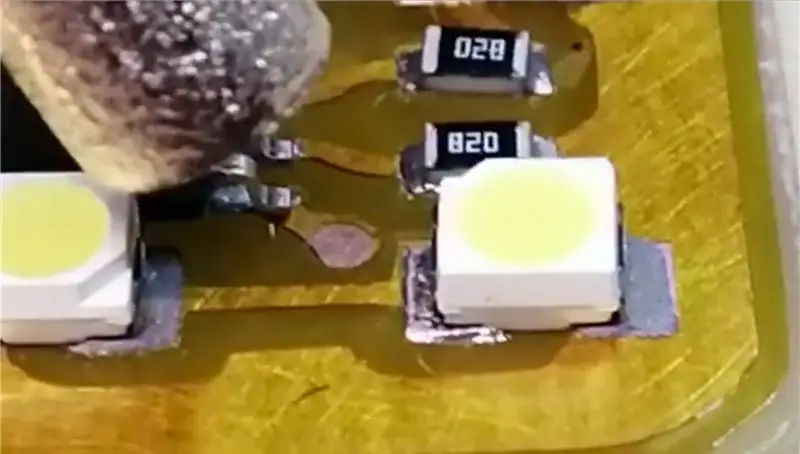
Com a pasta de solda nas placas, é hora de preencher todos os componentes. Para isso, use uma pinça de ponta fina e coloque com cuidado cada componente sobre as suas almofadas, garantindo a orientação e o alinhamento corretos (ver imagem 2). Leve o seu tempo fazendo isso e corrigindo quaisquer erros. Assim que todos os componentes estiverem colocados, ligue a ferramenta de refluxo de ar e comece gradualmente a pré-aquecer toda a placa, pairando em círculos sobre ela (veja a imagem 3). Em seguida, direcione o ar quente diretamente sobre cada almofada até que reflua totalmente (imagem 4). Quando terminar de refluir, é hora de adicionar o clipe da bateria. Para isso, fure os centros das 2 almofadas redondas maiores e coloque o clipe da bateria na parte de baixo da placa. É aconselhável também colar o clipe da bateria na placa com epóxi para aliviar qualquer tensão dos pinos de alimentação, pois o clipe vai segurar a placa no gabinete. Neste ponto, a placa de circuito impresso está totalmente montada e pronta para programação.
Etapa 8: imprimir em 3D as capas das chaves
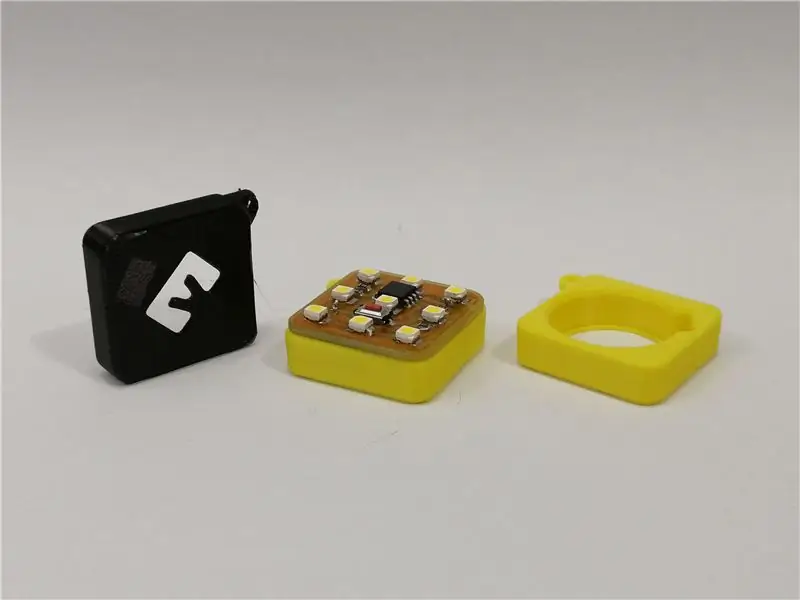

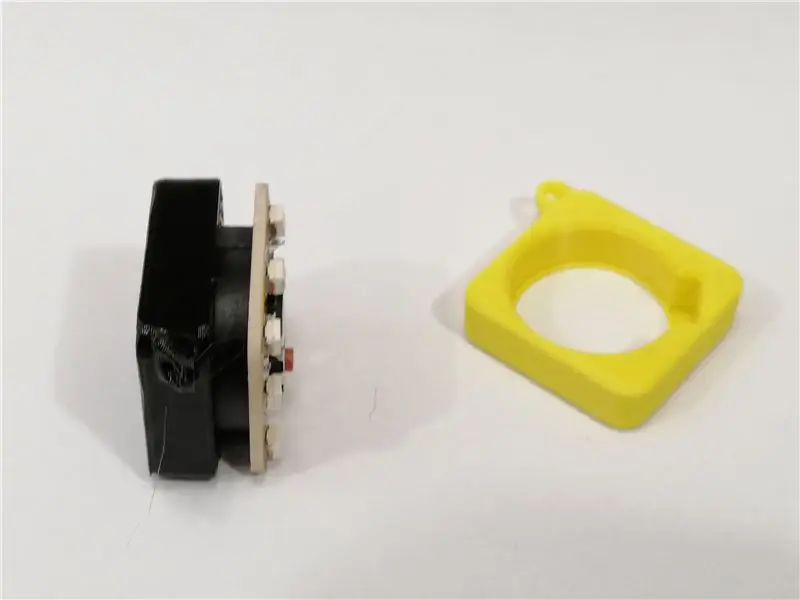
Os estojos impressos em 3D são opcionais, mas altamente recomendados, pois adicionam muito caráter ao objeto, transformando-o em um chaveiro, ao mesmo tempo em que protegem a matriz. É obrigatório imprimi-los em PETG para garantir alta durabilidade, pois o PLA provavelmente se romperá muito rapidamente. Fiz duas versões do case, uma com fundo oco para remover a bateria e outra com meu logotipo na parte traseira, o que mantém a bateria segura e escondida. Como o circuito consome muito pouca energia, a bateria pode ficar presa dentro do case sem qualquer problema.
Para montar a caixa, basta encaixar o clipe da bateria na impressão 3D até que a placa fique alinhada com a borda. Dependendo do clipe exato da bateria, talvez seja necessário lixá-lo levemente ou aumentar a altura do gabinete para garantir que ele se encaixe totalmente, portanto, certifique-se de verificar antes de montar. Se necessário, no entanto, a caixa pode ser aberta puxando lentamente a placa para fora ao redor da borda.
Etapa 9: Faça um gabarito de programação
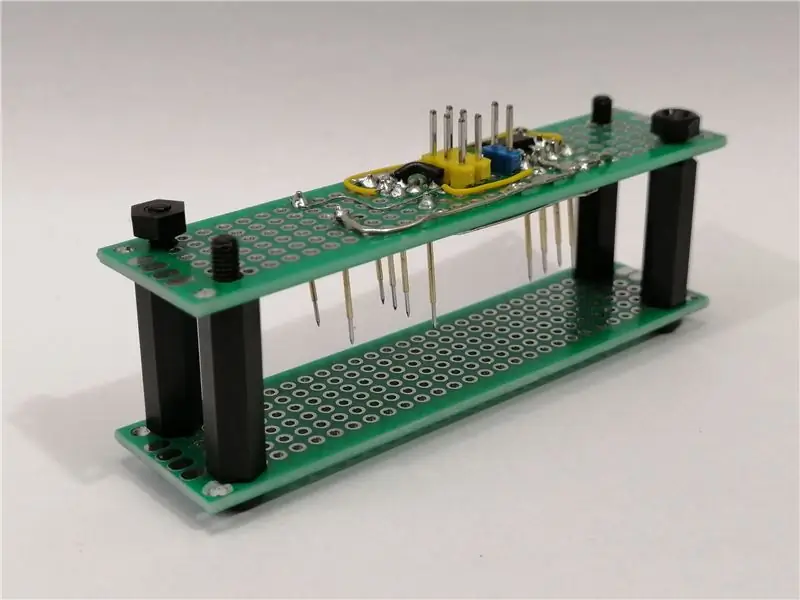
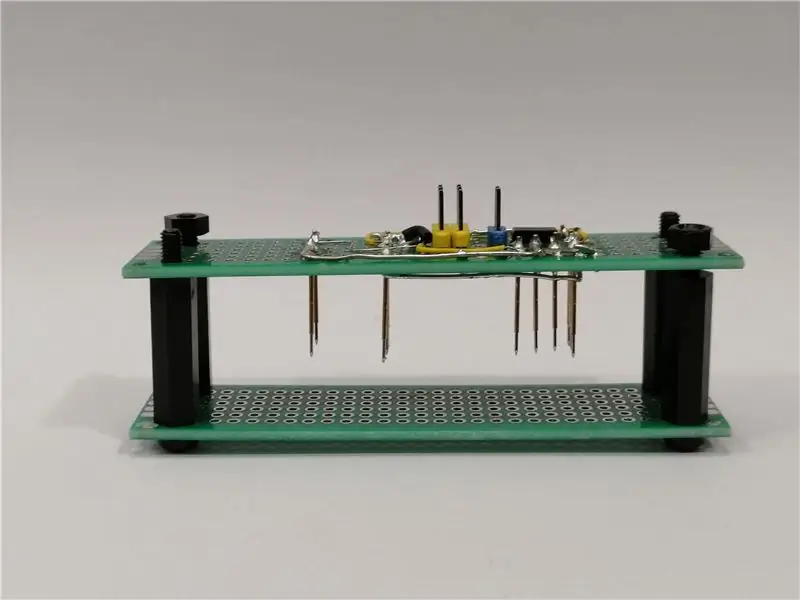
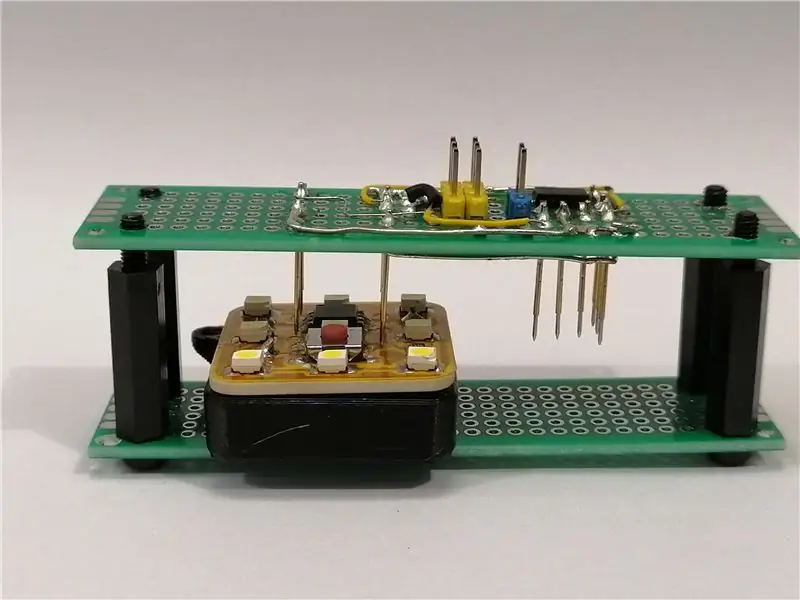
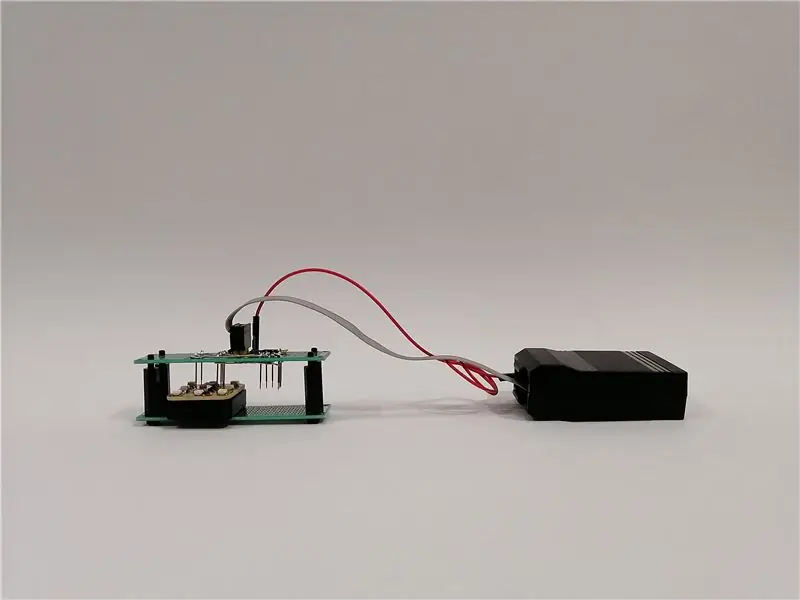
Agora os tinyDice estão totalmente montados, porém devemos programá-los para que funcionem como deveriam. Para isso, utilizamos um pogo pin jig que contata todos os pads de programação da placa e se conecta a um programador ISP, que pode ser um USBtinyISP ou qualquer Arduino como ISP. o tinyDice possui todos os pinos de programação disponíveis em blocos com espaçamento padrão de 100 fresas (2,54 mm), para permitir a montagem do gabarito em placa perfurada padrão. Siga o diagrama de conexão para vincular cada pino de pogo ao cabeçalho do ISP. Para fins de desenvolvimento, fiz um gabarito duplo que também serve para outra placa em que estou trabalhando e incorporei um regulador LDO para evitar o esgotamento das baterias durante o teste, mas para uma programação podemos utilizar a energia diretamente da bateria
tinyDice foi projetado para funcionar a 3 volts, portanto programá-los a 5 volts apresenta o risco de danificar os pinos IO do microcontrolador, os LEDs ou mesmo o programador, pois muita corrente seria puxada pelos resistores limitadores de corrente do LED. Portanto, para programar o chip sem danificar nada, devemos utilizar a voltagem nativa da bateria. Se estiver usando um USBtinyISP, simplesmente remova seu jumper de alimentação, que irá alimentar o Logic Lever Shifter da bateria do tinyDice, e se estiver usando um Arduino, simplesmente deixe a alimentação desligada para alimentar apenas o dado com a bateria e adicione um resistor série 5k para cada linha de dados.
Etapa 10: Programando os dados
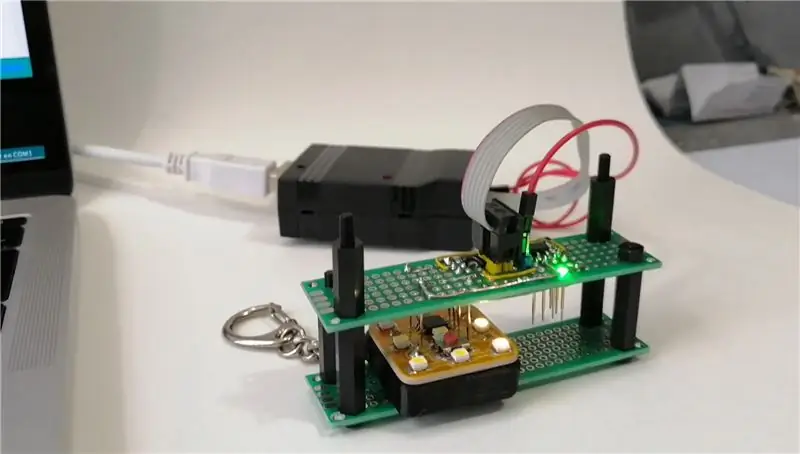
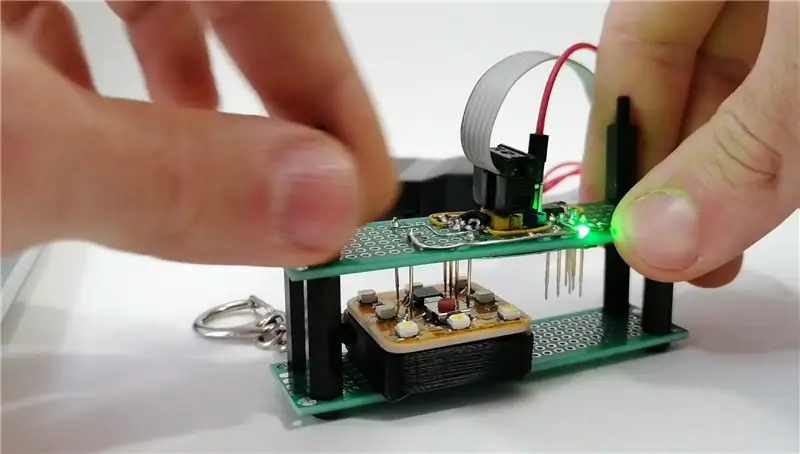
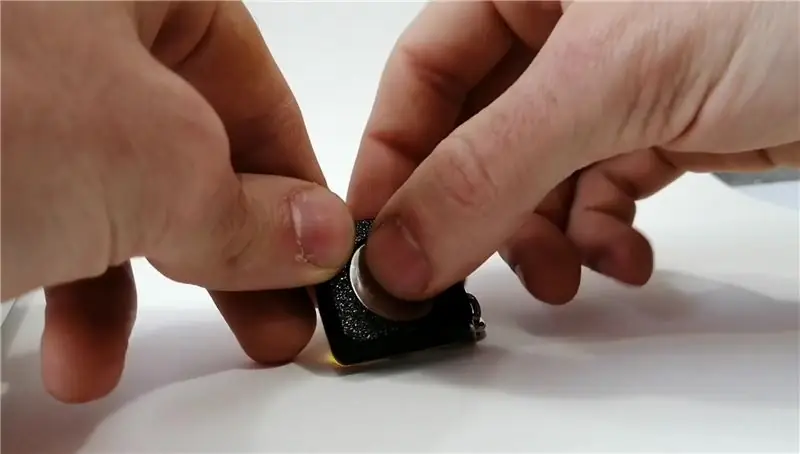
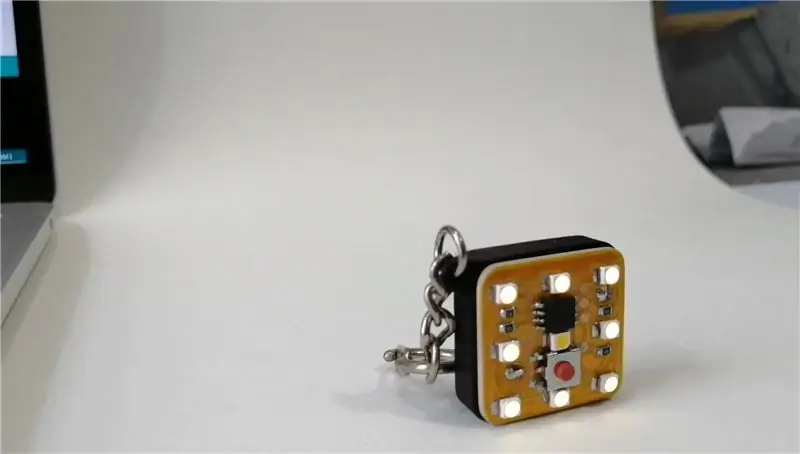
Para o processo de programação, monte cuidadosamente o gabarito sobre os dados usando espaçadores e certifique-se de que todos os pinos do pula-pula sejam pressionados corretamente nos blocos correspondentes. Tenha cuidado e não deslize o dado sob os pinos, pois é muito fácil quebrá-los. Em seguida, conecte o USBtinyISP ao gabarito e ao computador.
Abra o IDE do Arduino, carregue o esboço tinyDice e selecione o chip atTiny85 com o USBtinyISP como programador. Aperte o botão de upload e verifique os dados, 2 LEDs devem começar a piscar por um tempo. Se tudo der certo, agora o tinyDice está programado, finalizado e pronto para uso. Repita o processo de programação para todas as unidades que você fez e depois guarde o gabarito totalmente montado para proteger os pinos do pogo.
O código:
O programa do tinyDice é tal que primeiro exibe uma animação de "pensamento" e, em seguida, gera um número aleatório entre 0 e 9 que é exibido por alguns segundos. Todas as transições são feitas com PWM para cada LED para permitir fades. Depois de exibir o número e desaparecer, o processador entra no modo de hibernação, o que basicamente interrompe o consumo da bateria, de modo que a bateria deveria teoricamente durar cerca de 6.000 "jogadas" de dados.
Todo o código é estruturado em torno de uma interrupção de temporizador de 8 Khz que lida com o charlieplexing e o PWM de 10 passos para cada LED, bem como o avanço das animações. Explicações mais detalhadas de cada função são comentadas no esboço do Arduino.
Conclusões:
Os resultados desse método para fabricação doméstica de PCBs excederam em muito minhas expectativas iniciais, pois descobri que ele pode ser extremamente confiável e produzir resultados de alta qualidade para a prototipagem fácil e rápida de SMD e circuitos through-hole. Por isso incentivo os DIYers a experimentar este método em seus próprios projetos e compartilhar seus resultados e descobertas com a comunidade.
Esta nova versão do tinyDice é por si só um objeto muito legal e divertido de se ter e compartilhar com os amigos, já que as animações e a capa do chaveiro o tornam único e interessante. Espero que tenha gostado deste instrutível e por favor, compartilhe seus comentários e experiências sobre o assunto para que o método continue a evoluir. Além disso, sinta-se à vontade para experimentar o código e compartilhar quaisquer variações interessantes para outras pessoas experimentarem.
Este guia está no concurso de design de PCB, portanto, vote nele se você o considerar válido e compartilhe-o com seus amigos e entusiastas de eletrônicos.
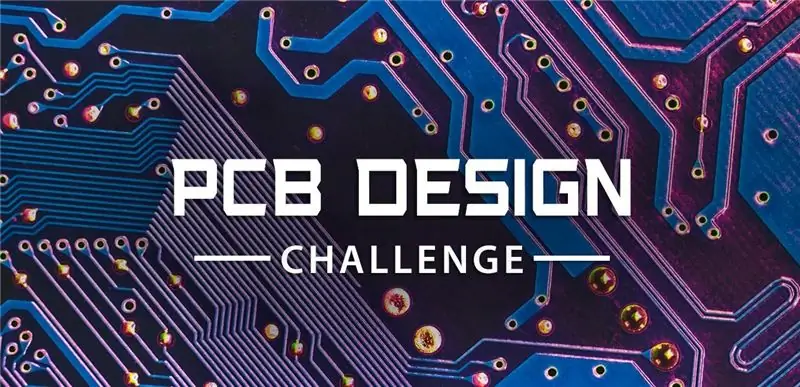
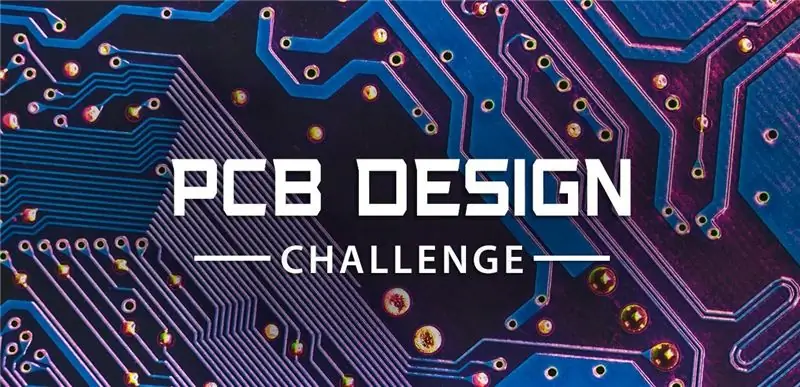
Segundo Prêmio no Desafio de Design PCB
Recomendado:
Instruções sobre como usar um cortador de vinil MH871-MK2: 11 etapas
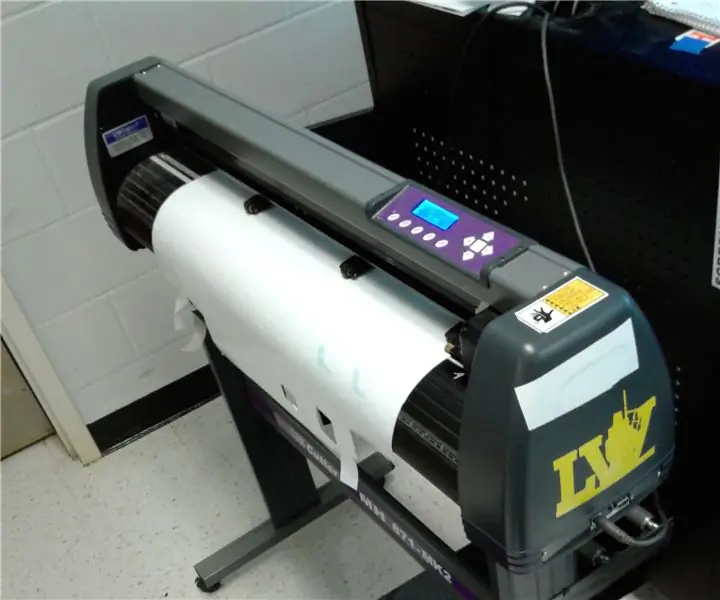
Instruções sobre como usar um cortador de vinil MH871-MK2: Olá, meu nome é Ricardo Greene e fiz instruções sobre como usar um cortador de vinil MH871-MK2
Usando um cortador de vinil para fazer um estêncil de aerógrafo: 5 etapas
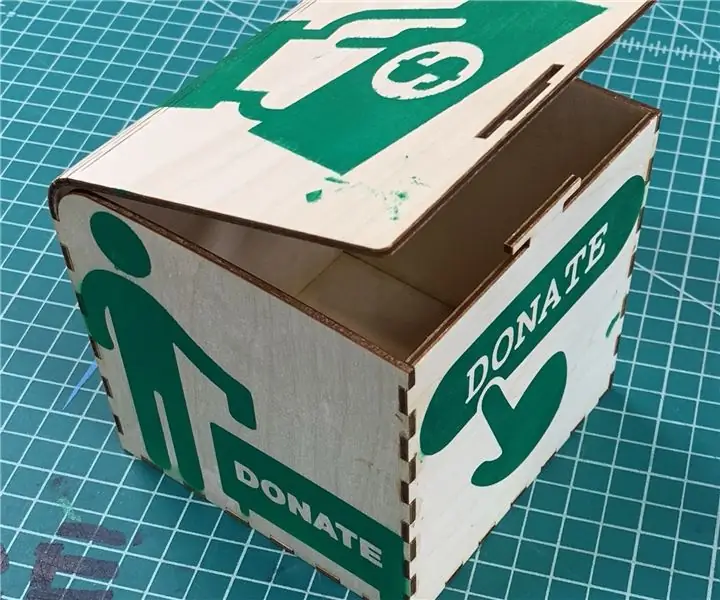
Usando um cortador de vinil para fazer um estêncil de aerógrafo: Neste instrutível, darei uma breve introdução ao processo de usar um cortador de vinil para fazer estênceis que você pode usar para pintar com uma configuração de aerógrafo ou, na verdade, com praticamente qualquer tipo de tinta. Nessas fotos, usei um aerógrafo boo
Fazendo PCBs em casa (método de transferência de toner): 8 etapas (com imagens)
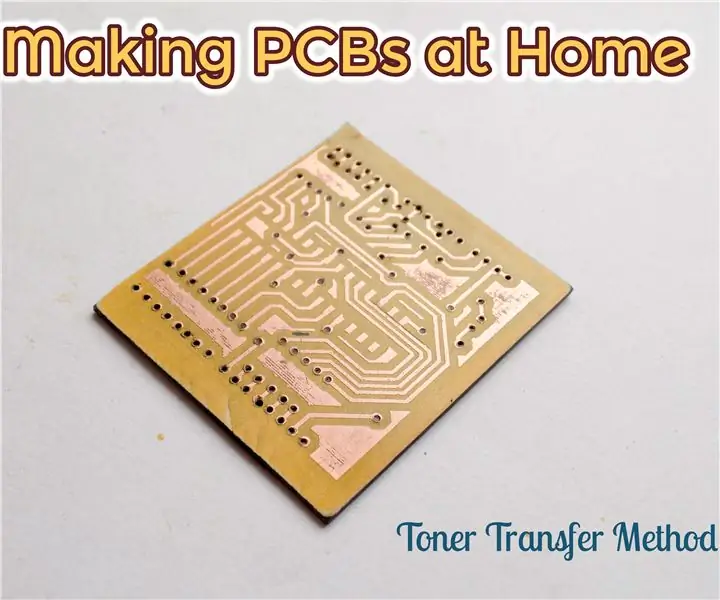
Fazendo PCBs em casa (método de transferência de toner): Muitas vezes, como fabricantes, enfrentamos obstáculos como complexidade do circuito, problemas de fiação e projetos desordenados ao usar placas de prototipagem. Uma vez que qualquer bom projeto deve ser limpo e organizado se for para fins de demonstração. Então, para g
Faça PCBs Hobbyist com ferramentas CAD profissionais modificando " Regras de design ": 15 etapas (com imagens)
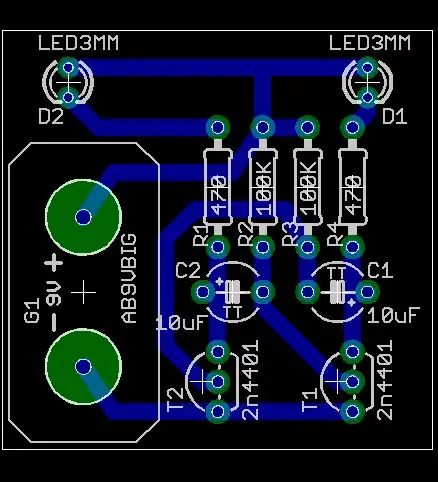
Faça PCBs para amadores com ferramentas CAD profissionais, modificando as " Regras de design ": É bom que haja algumas ferramentas de placa de circuito profissional disponíveis para os amadores. Aqui estão algumas dicas para usá-los em pranchas de design que não precisam de um fabricante profissional para FAZÊ-los de fato
PCBs profissionais quase mais baratos do que fabricá-los em casa: 14 etapas
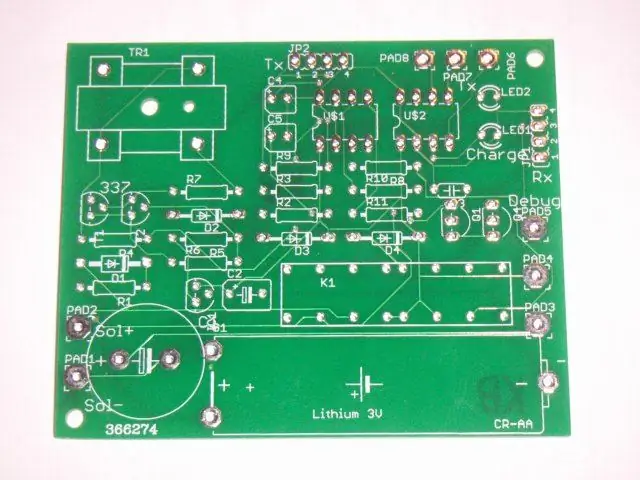
PCBs profissionais quase mais baratos do que fabricá-los em casa: Embora haja grande satisfação em construir PCBs em casa, somar o custo do PCB em branco, etchant e as brocas chega a mais de US $ 4 por placa. Mas, por US $ 6,25 a placa, tudo pode ser feito profissionalmente. Este Instructable leva você através