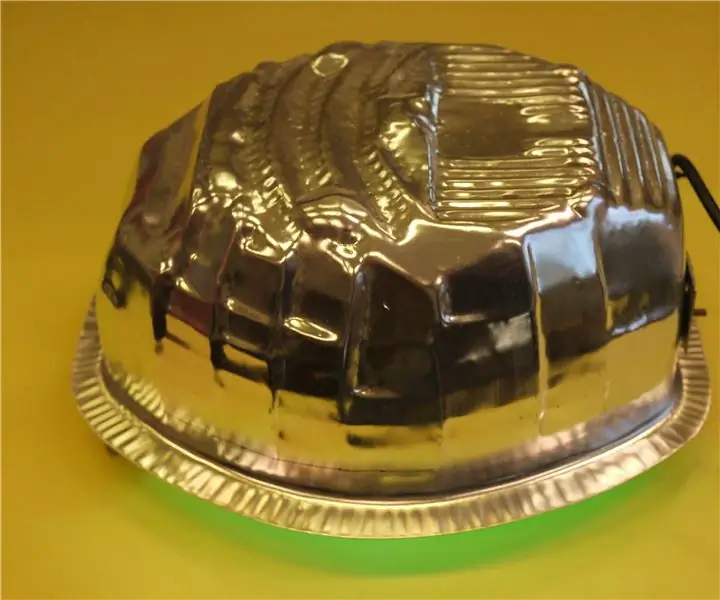
Índice:
2025 Autor: John Day | [email protected]. Última modificação: 2025-01-23 15:03
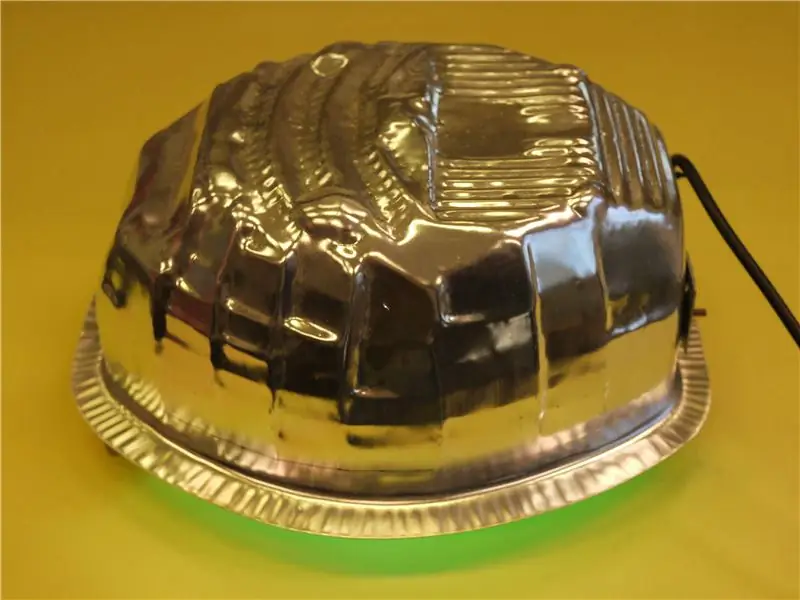
Dispositivos microfluídicos fabricados em termoplásticos estão cada vez mais sendo usados devido à rigidez, transparência, permeabilidade a gases reduzida, biocompatibilidade e tradução mais fácil para métodos de produção em massa, como moldagem por injeção. Os métodos de ligação para termoplásticos geralmente envolvem o aumento da temperatura acima da Tg do polímero (temperatura de transição vítrea) ou o uso de solventes que podem levar à deformação do canal ou lixiviação de substâncias indesejadas do substrato. Os processos de colagem assistidos por UV produzem resultados limpos, sem necessidade de solventes e sem deformação das microestruturas [1]. No entanto, o equipamento comercial de irradiação UV é bastante caro (> 2000 USD). Seguindo este tutorial, você pode construir uma alternativa DIY de baixo custo que tem um desempenho semelhante ao de equipamentos profissionais e produz uma ligação reproduzível e permanente de chips microfluídicos de PMMA por menos de 100 USD.
Suprimentos
- Lâmpada de vapor de mercúrio de 250 W (como Osram HQL ou Philips HPL)
- Balastro de 250 W para lâmpadas de vapor de mercúrio
- Caixa de holofote com um soquete correspondente para a lâmpada
- Fios (seção mínima de 0,5 mm2)
- Martelo pequeno
- Prego de metal de aço
- Alicate de ponta fina
- Saco de tecido grosso e saco de plástico grosso
- Ar comprimido isento de óleo ou gás inerte
- Equipamento de proteção individual: luvas, máscara contra poeira e óculos de segurança
Etapa 1: Etapa 1
Use o equipamento de proteção individual mencionado em todos os momentos durante este processo
Etapa 2: Etapa 2
Com cuidado, coloque a lâmpada de vapor de mercúrio dentro do saco plástico e, posteriormente, dentro do saco de tecido para evitar que resíduos de vidro e pó fluorescente se espalhem
Etapa 3: Etapa 3
Ao ar livre (ou em uma área bem ventilada), use o martelo e o prego para quebrar o vidro externo da lâmpada, tomando cuidado extra para não destruir a lâmpada interna. AVISO: fluorescente (branco) o pó pode ser tóxico, portanto, evite respirar ou tocá-lo
Etapa 4: Etapa 4
Retire a lâmpada (sempre segurando pelo fio) do saco e remova qualquer vidro remanescente (até o fio de metal da lâmpada) com a ajuda do alicate. AVISO: os fragmentos de vidro podem ser muito afiados
Etapa 5: Etapa 5
Limpe a lâmpada com ar comprimido e armazene-a adequadamente. Evite tocar na lâmpada com as mãos desprotegidas. Descarte os resíduos de vidro de acordo com os regulamentos locais.
Etapa 6: Etapa 6
Ligue o soquete da lâmpada ao reator e ao cabo de alimentação. AVISO: Lembre-se de que a fiação de circuitos elétricos apresenta riscos substanciais. Se a fiação não estiver correta, você pode receber um choque, ser eletrocutado ou o dispositivo pode causar um incêndio. Se você não tem certeza do que está fazendo, deve deixar alguém mais habilidoso em fiação elétrica fazer o trabalho
Etapa 7: Etapa 7
Aparafuse a lâmpada (lâmpada de mercúrio) ao casquilho da lâmpada na caixa. AVISO: radiação UV perigosa e ozônio são gerados pela lâmpada quando a tampa externa é removida. Sempre use proteção adequada para os olhos e a pele e use o sistema em um ambiente ventilado
Etapa 8: Figura 1
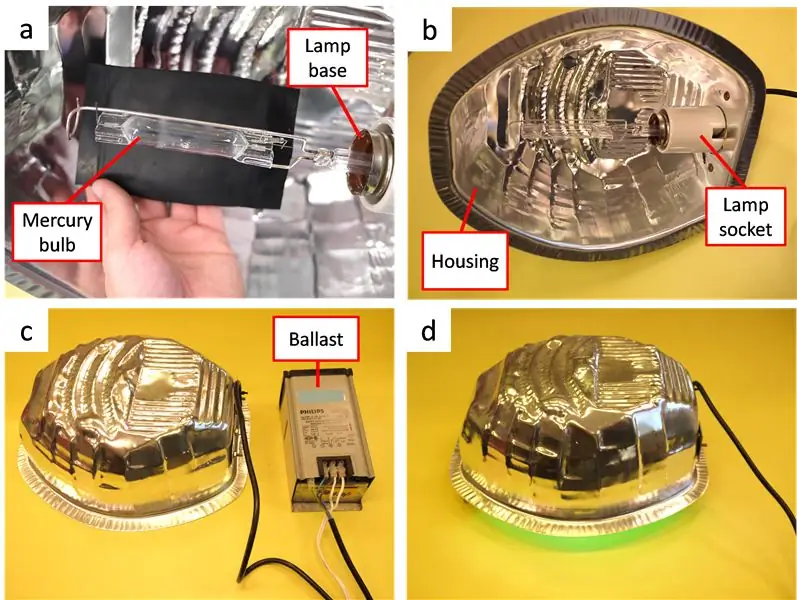
Figura 1. a) Detalhe do bulbo exposto de quartzo mercúrio, a borracha preta está ali apenas para fins de visualização. b) Fotografia da carcaça, lâmpada e soquete da lâmpada. c) Fotografia do holofote e do reator. d) Fotografia da lâmpada UV LIGADA
Etapa 9: O que mais eu preciso saber?
O objetivo deste tutorial é mostrar como construir uma luz de inundação UV de baixo custo para realizar a fotodegradação de amostras de PMMA para ligação. Os parâmetros de colagem devem ser otimizados de acordo com a lâmpada, carcaça, distância da fonte de UV, tipo de PMMA, etc. Para mais informações consulte a literatura [1].
Os chips microfluídicos como o mostrado na Figura 2 podem ser obtidos usando esta lâmpada de ligação.
Etapa 10: Figura 2
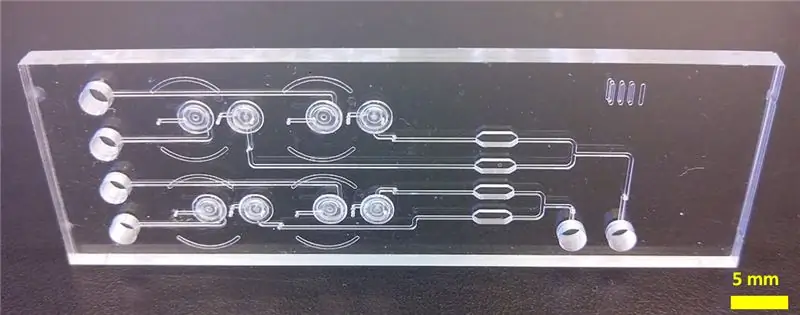
Figura 2. Chip microfluídico multicamada PMMA ligado com a lâmpada UV apresentada
Etapa 11: Referências
1- Truckenmüller, R., Henzi, P., Herrmann, D. et al. Microsystem Technologies (2004) 10: 372
Recomendado:
Comunicação sem fio LoRa de 3 km a 8 km com dispositivo E32 (sx1278 / sx1276) de baixo custo para Arduino, Esp8266 ou Esp32: 15 etapas
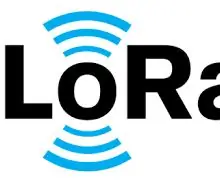
LoRa 3Km a 8Km de comunicação sem fio com baixo custo E32 (sx1278 / sx1276) Dispositivo para Arduino, Esp8266 ou Esp32: Eu crio uma biblioteca para gerenciar EBYTE E32 baseada na série Semtech de dispositivos LoRa, um dispositivo muito poderoso, simples e barato. Você pode encontrar Versão de 3Km aqui, versão de 8Km aqui Eles podem trabalhar em uma distância de 3000m a 8000m, e têm muitos recursos e
Câmera 3D Fpv de baixo custo para Android: 7 etapas (com imagens)
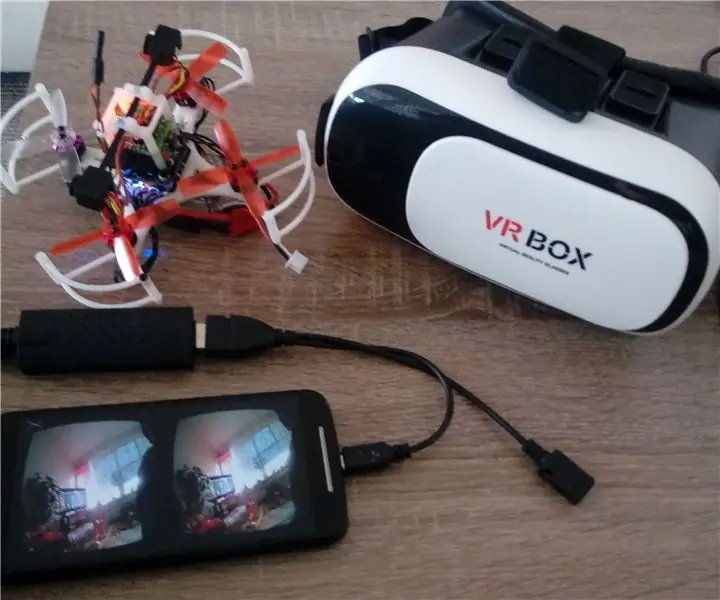
Câmera 3D Fpv de baixo custo para Android: FPV é uma coisa muito legal. E seria ainda melhor em 3D. A terceira dimensão não faz muito sentido em grandes distâncias, mas para um Micro Quadcopter interno é perfeita. Então, dei uma olhada no mercado. Mas as câmeras que encontrei eram todas ele
Rede de sensores sem fio de baixo custo na banda de 433 MHz: 5 etapas (com imagens)
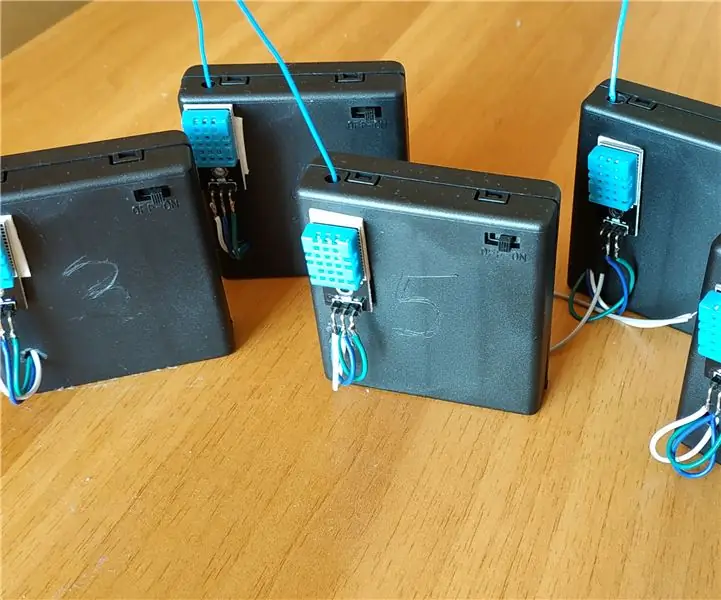
Rede de sensores sem fio de baixo custo na banda de 433 MHz: Muito obrigado a Teresa Rajba por gentilmente me dar sua aceitação em usar os dados de suas publicações neste artigo. * Na imagem acima - as cinco unidades de sensor remetente que usei para testar o que são sensores sem fio redes? Uma definição simples seria
Faça uma 'mão' de 3 graus de liberdade para ajudar no trabalho de solda / colagem: 6 etapas
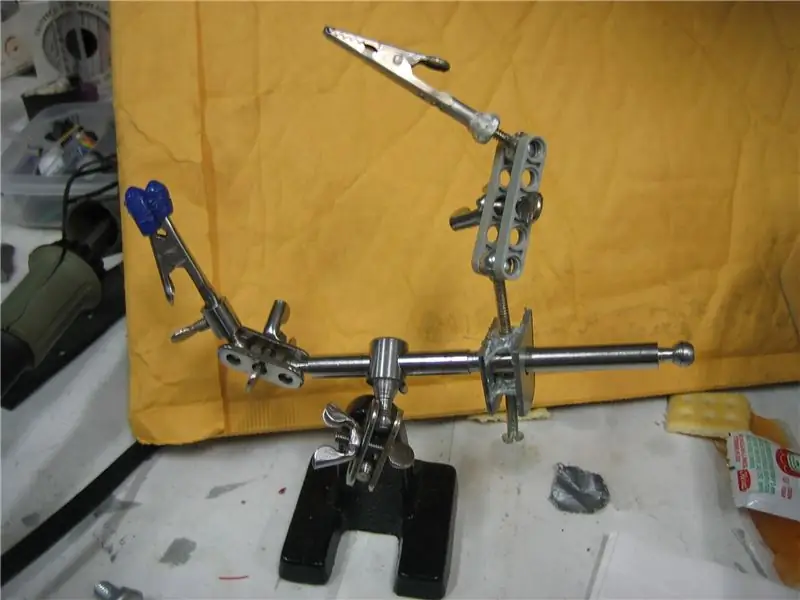
Faça uma 'mão' de 3 graus de liberdade para ajudar no trabalho de solda / colagem: Como fazer uma nova mão de três graus de liberdade para suas 'mãos que ajudam'. O design permite que você faça peças finais comutáveis e personalizadas (além da presilha jacaré padrão)
Resfriador / suporte de laptop de custo zero (sem cola, sem perfuração, sem porcas e parafusos, sem parafusos): 3 etapas
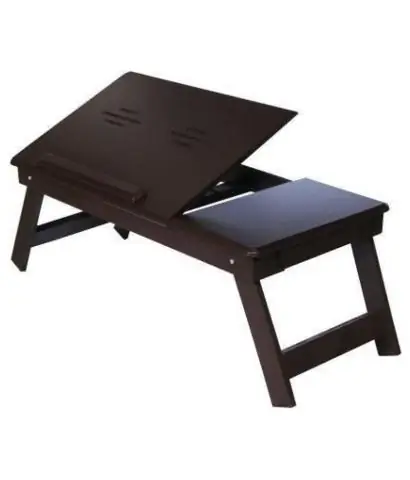
Resfriador / suporte para laptop de custo zero (sem cola, sem furação, sem porcas e parafusos, sem parafusos): ATUALIZAÇÃO: ATUALIZAÇÃO ESPECIALMENTE VOTE MEU INSTRUTÁVEL, OBRIGADO ^ _ ^ VOCÊ TAMBÉM PODE GOSTAR DE VOTO EM MEU OUTRO CONCURSO INSCREVA-SE EM www.instructables.com/id/Zero-Cost-Aluminum-Furnace-No-Propane-No-Glue-/ OU TALVEZ VOTE NO MEU MELHOR AMIGO