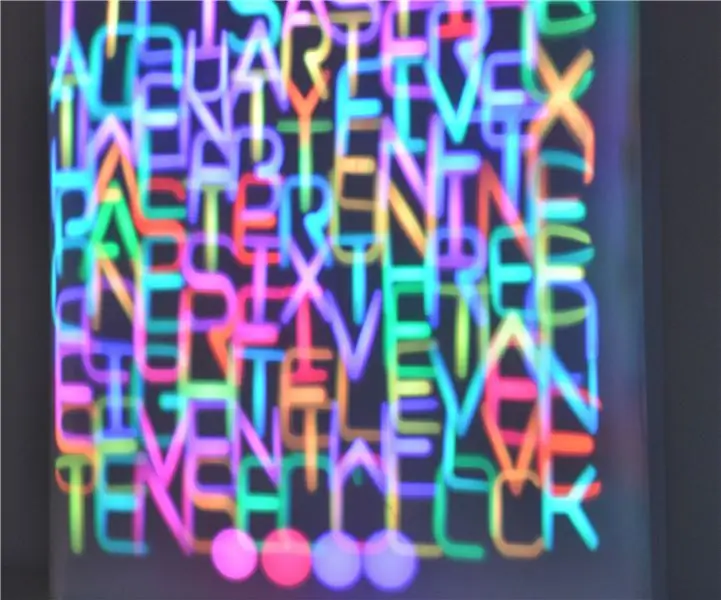
Índice:
- Etapa 1: Design
- Etapa 2: coleta de materiais
- Etapa 3: componentes impressos em 3D
- Etapa 4: Construindo a Estrutura
- Etapa 5: montagem das caixas de correio
- Etapa 6: montagem dos atuadores
- Etapa 7: fazendo a placa traseira
- Etapa 8: Conecte os componentes à placa traseira e à fiação
- Etapa 9: Anexando a placa traseira à estrutura
- Etapa 10: Calibrando os Servos
- Etapa 11: enviando o código
- Etapa 12: anexando a tela
- Etapa 13: Prendendo as tampas superior e inferior
- Etapa 14: Relógio e resumo finalizados
2025 Autor: John Day | [email protected]. Última modificação: 2025-01-23 15:03
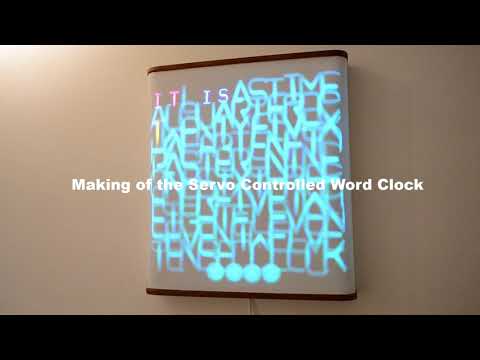
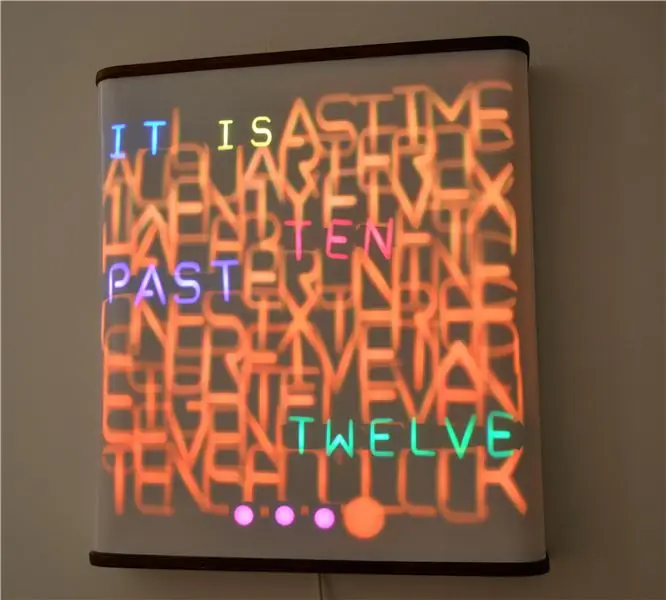
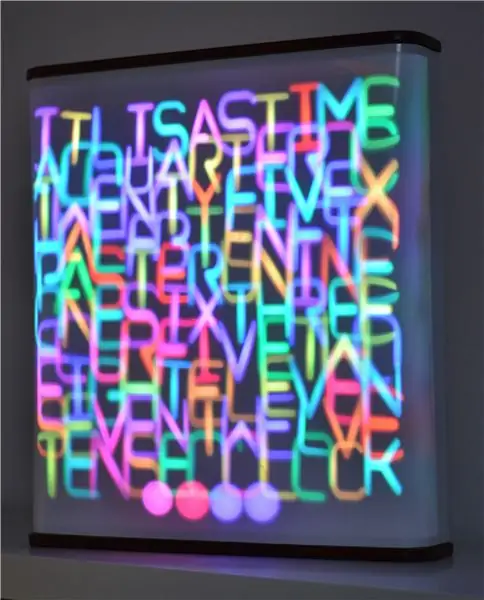
Projetos Fusion 360 »
O que tem 114 LEDs e está sempre funcionando? Como você deve saber, a resposta é um wordclock. O que tem 114 LEDs + 114 servos e está sempre em movimento? A resposta é este word clock controlado por servo.
Para este projeto eu me associei a um amigo meu que acabou se tornando uma obrigação devido ao grande esforço desta construção. Além disso, minhas habilidades eletrônicas e mecânicas se complementavam muito bem. A ideia para esta adaptação do popular word clock surgiu enquanto fazíamos um normal como presente de natal. Lá, percebemos que também é possível projetar as letras do verso em uma folha de papel branca. Na época, essa era apenas uma solução alternativa para esconder nosso péssimo trabalho artesanal, já que acabamos com um monte de bolhas enquanto colávamos um adesivo de vinil com as letras na parte de trás de uma placa de vidro. Percebemos então que é possível obter efeitos interessantes ao dobrar a folha de papel, pois as letras mudam de tamanho e ficam borradas. Isso nos deu a ideia de fazer um wordclock em que as letras são projetadas de trás para uma tela e podem ser movidas para frente e para trás para alterar o tamanho da imagem projetada. No início, estávamos um pouco relutantes em construir este projeto por causa dos custos e do esforço necessário para mover cada uma das 114 letras individualmente. Então, tivemos a ideia de fazer uma versão em que apenas cada palavra usada para exibir a hora pudesse ser movida para frente e para trás. No entanto, depois de ver que o concurso Epilog estava chegando no Instructables pedindo projetos épicos, e também depois de encontrar servo motores relativamente baratos, decidimos ir até o fim e fazer uma versão apropriada onde cada letra é controlada individualmente por um servo.
ATENÇÃO: Esta não é uma construção de um dia!
Para se ter uma ideia do esforço envolvido neste projeto, considere os seguintes números. O relógio finalizado contém
- 798 modelos impressos em 3D individuais (tempo total de impressão ~ 200 horas)
- ~ 600 parafusos + ~ 250 porcas e arruelas
- ~ 500 fios (comprimento total ~ 50 m). Sem contar os fios que já estavam presos aos servos.
Etapa 1: Design
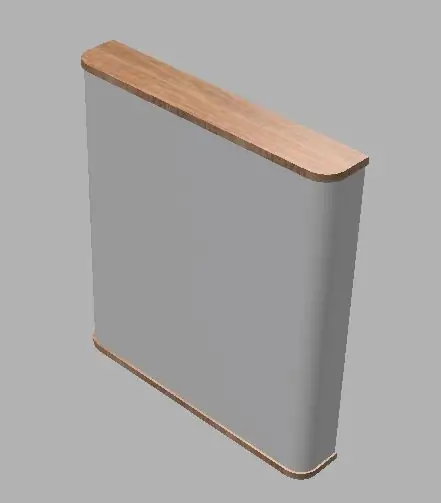
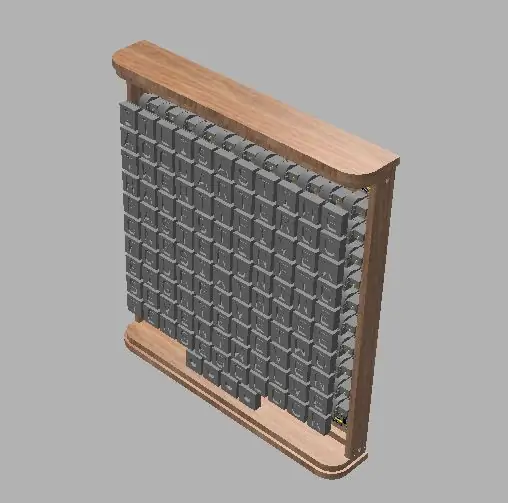
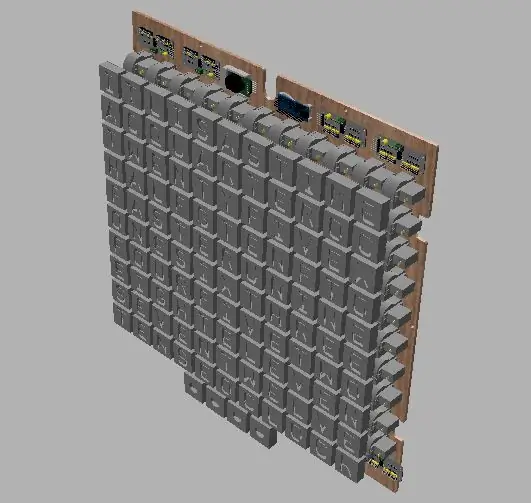
O relógio foi projetado com Autodesk Fusion 360 e Inventor. Como você pode ver, o relógio consiste em 114 caixas de correio que são movidas por atuadores lineares que, por sua vez, são acionados por servo motores. Cada caixa de correio contém um LED que projeta a letra na parte de trás de uma tela feita de folha de PVC branca. Todos os componentes estão alojados em uma estrutura de madeira.
Etapa 2: coleta de materiais
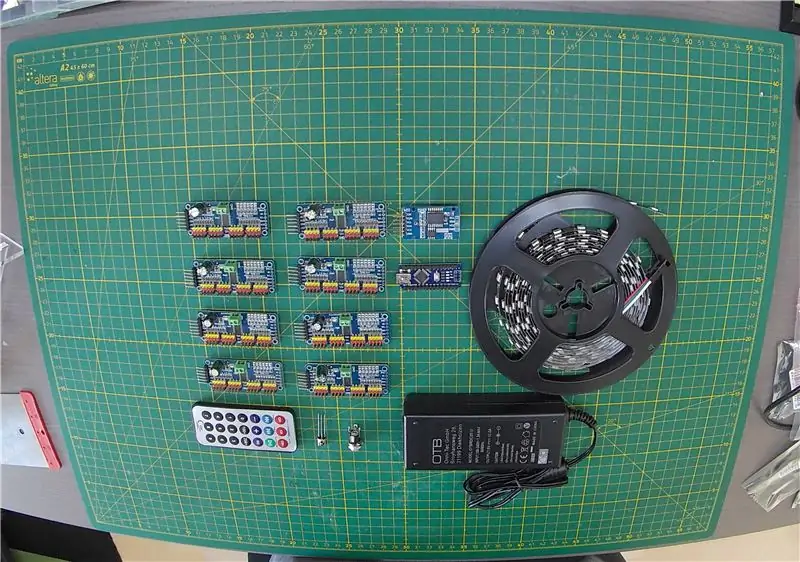
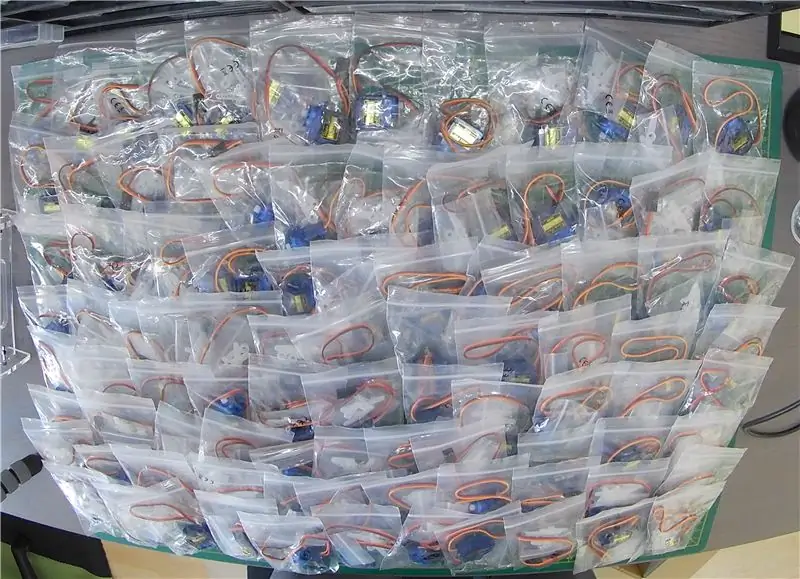
Componentes eletrônicos
Microsservo motores 114x SG90 (ebay.de)
Embora os servos tenham sido rotulados com o nome da popular marca "Tower Pro", eles são certamente cópias mais baratas. No entanto, como o preço da cópia é de cerca de 1 EUR em comparação com os 3 EUR do original, isso torna todo o projeto muito mais acessível. Aparentemente, os knockoffs também consomem menos corrente (é claro que isso também implica menos torque), o que tornou mais fácil encontrar uma fonte de alimentação adequada para todo o projeto.
- Faixa de LED WS2812B de 5 m, 60 LEDs / m (ebay.de)
- 8x 16 Ch PWM servo driver PCA9685 (ebay.de)
- Módulo DS3231 RTC (ebay.de)
- Arduino nano (ebay.de)
- Receptor IR VS1838B + remoto (ebay.de)
- Fonte de alimentação 5 V, 10 A (ebay.de)
- Cabo de extensão servo 20x 15 cm (ebay.de)
- cabo DC soquete para fio desencapado (conrad.de)
- Resistor de 300-500 Ohm
- Capacitor 1000 µF (> 5 V)
Materiais para moldura
- ripas de madeira
- 2 peças 40 x 10 x 497 mm
- 2 peças 12 x 12 x 461 mm
- 2 peças 12 x 12 x 20 mm
-
multiplex
- 2 peças 12 x 77 x 481 mm
- 2 peças 12 x 84 x 489 mm
- folha de PVC branca (700 x 1000 x 0,3 mm) (modulor.de)
- Placa HDF de 500 x 500 mm, 3 mm de espessura
Parafusos, cabos, etc
- Parafusos M2 228x, 8 mm de comprimento + arruelas + porcas sextavadas
- Parafusos auto-roscantes 228x M2.2, 6,5 mm de comprimento
- vários parafusos de madeira
- 50 m, fio de 0,22 mm2 (24 AWG)
Além disso, este projeto exigiu uma grande quantidade de impressão 3D e solda. A placa traseira foi produzida por corte a laser. A estrutura foi construída com serra circular, serra de vaivém e furadeira. Como em todo projeto decente, também usamos muita cola quente, um pouco de epóxi e cola plástica.
Os custos totais para este projeto foram de cerca de 350 EUR.
Etapa 3: componentes impressos em 3D
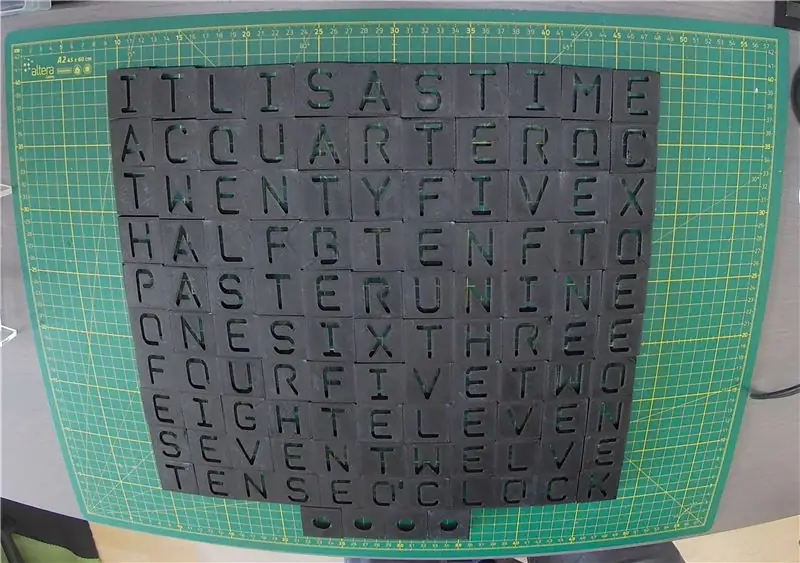
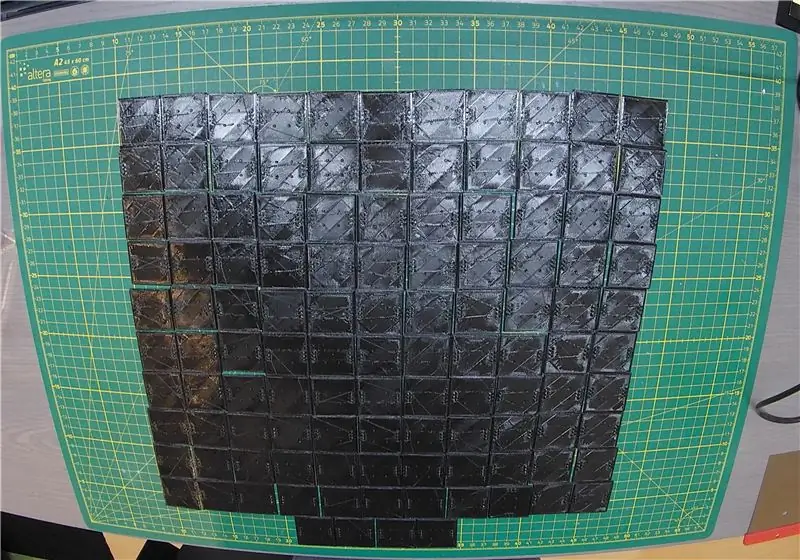
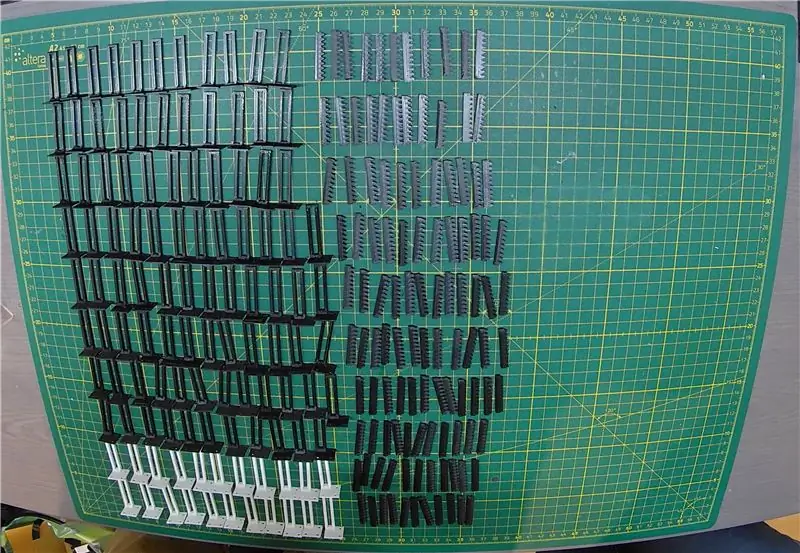
Caixas de correio
Cada caixa de correio consiste em uma capa impressa em 3D que atua como máscara de sombra e uma placa de base na qual um LED será conectado. A placa de base inclui quatro pinos guia para ajudar no alinhamento com o atuador e seis orifícios para alimentação através dos cabos de LED. No total, são 228 modelos que foram todos impressos em PLA preto (Formfutura EasyFill PLA) com camada de 0,4 mm de altura. O tempo total de impressão em meu Anycubic Kossel Linear Plus foi de cerca de 23 horas para as capas das cartas e 10 horas para as placas de base. Todos os arquivos stl podem ser encontrados no arquivo zip anexado.
Atuadores
O projeto do atuador foi adaptado do Linear Servo Extender de Roger Rabbit, que foi muito útil. Como as peças se encaixam perfeitamente, elas devem ser impressas em uma impressora 3D decente. A altura da camada pequena não é tão importante (0,2 mm é bom) como um diâmetro de bico pequeno (recomendamos 0,4 mm). As peças devem ser impressas na orientação mostrada. Cada atuador consiste em 5 peças individuais, visto que precisávamos de 114 atuadores, isso significa 570 peças (!) No total. Para imprimi-los, usamos o poder combinado de várias impressoras 3D profissionais (Ultimaker S2 +, Ultimaker S5, Lulzbot TAZ6, Sindoh 3D Wox DP200). Mesmo assim tivemos muitas impressões falhadas nas peças e incluí algumas fotos para sua diversão. O tempo total de impressão foi de cerca de 150 horas (!). Novamente, os arquivos stl podem ser encontrados no arquivo zip anexado.
Etapa 4: Construindo a Estrutura
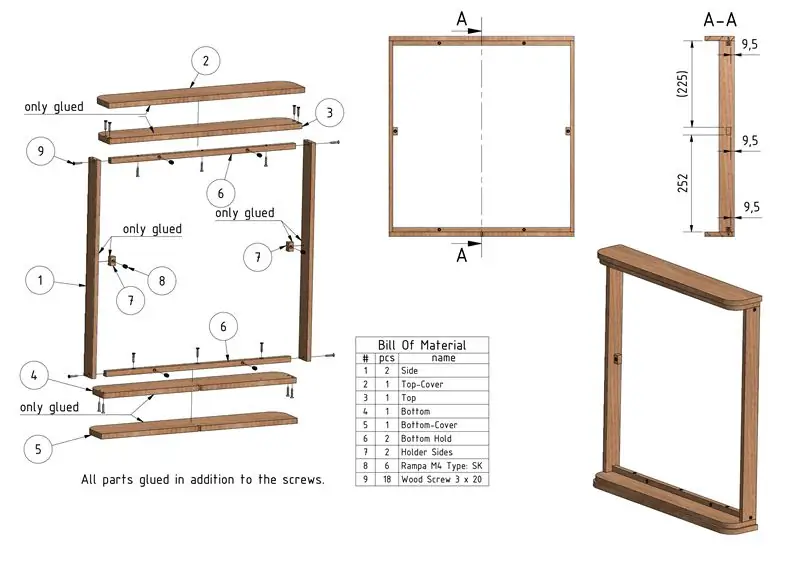
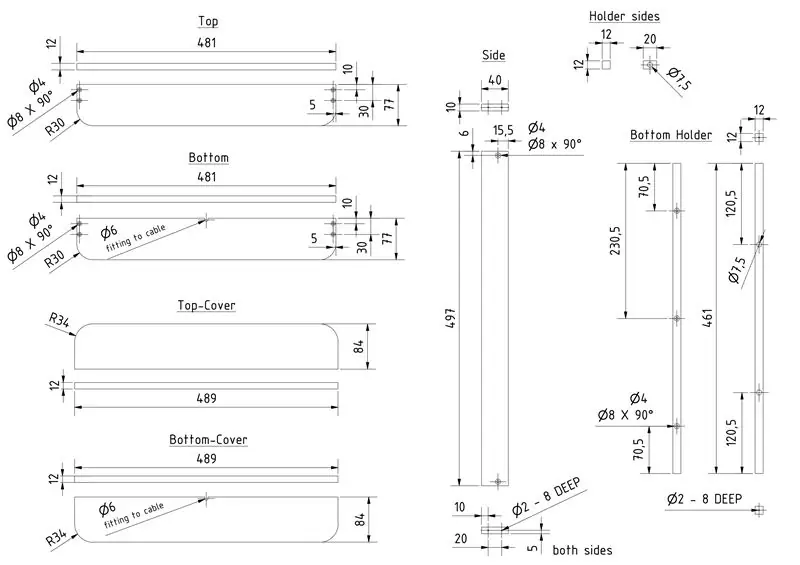

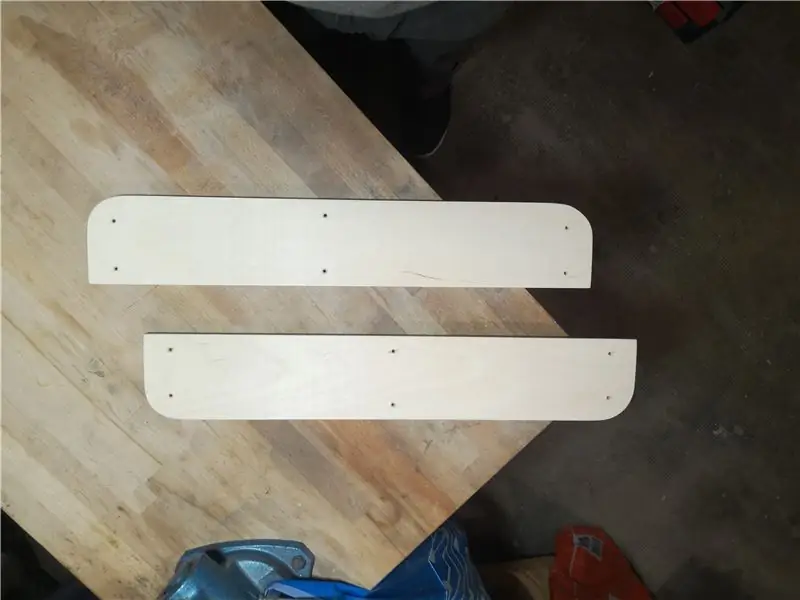
A estrutura foi construída com ripas de madeira e placa multiplex. As peças foram cortadas com serra circular e quebra-cabeças e depois fixadas com cola para madeira e parafusos para madeira. A capa superior e inferior também foram manchadas para dar uma aparência mais agradável. Uma descrição detalhada das peças, incluindo todas as dimensões, pode ser encontrada nos desenhos anexos.
Etapa 5: montagem das caixas de correio
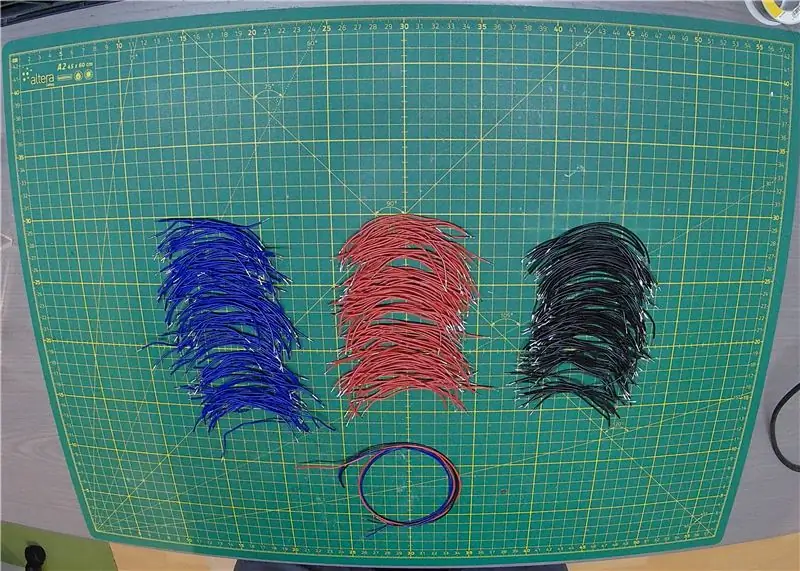
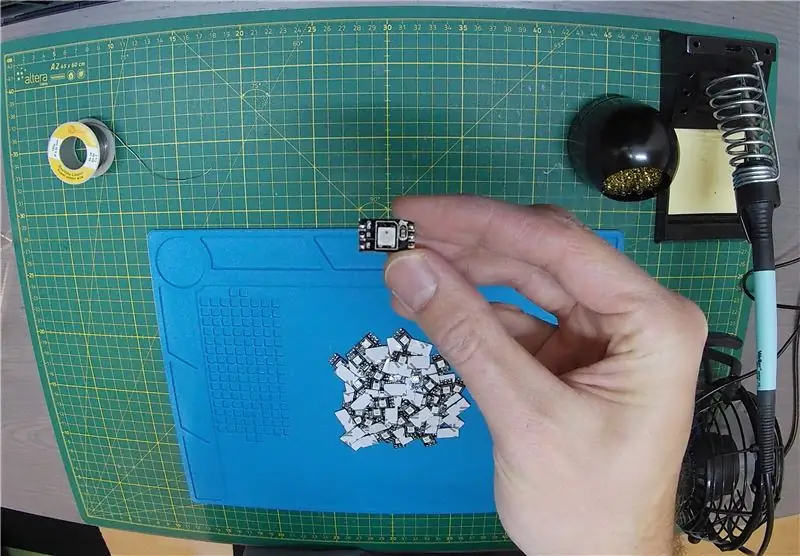
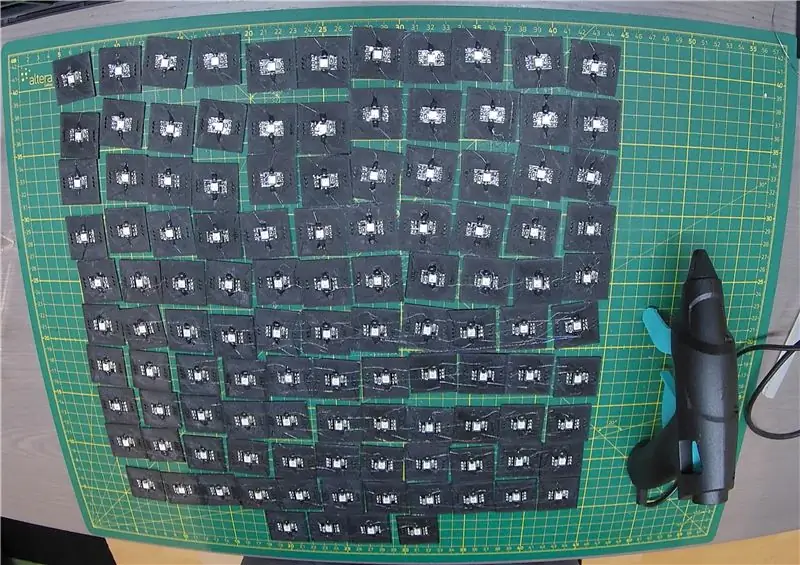
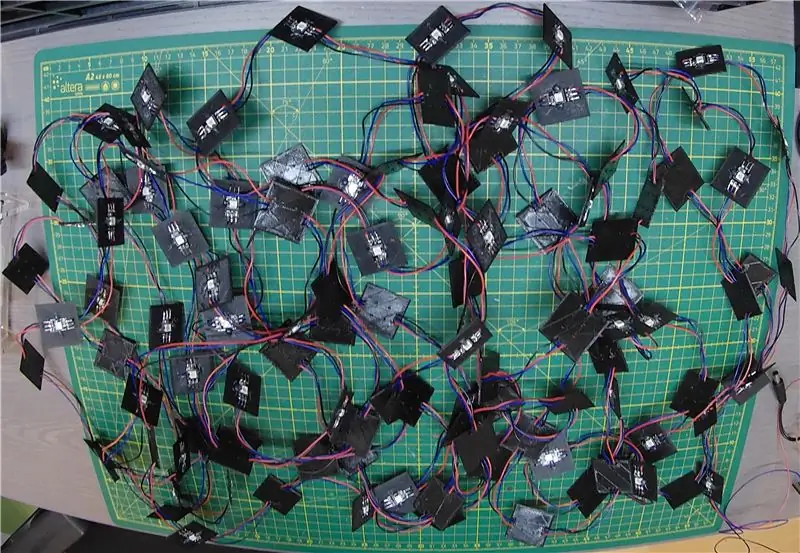
A montagem das caixas de correio deu muito trabalho e demorou muito, principalmente a soldagem. Isso ocorre porque cada passo que você dá deve ser repetido 114 vezes.
- Corte 114 peças individuais da tira de LED
- Estanhar todas as almofadas de LED
- Conecte cada LED à placa traseira impressa em 3D de uma caixa de correio. O LED deve estar centralizado. Também o fixamos com cola quente.
- Em seguida, preparamos 3x114 = 442 fios, ou seja, cortando no comprimento certo, descascando as pontas e estanhando-as. O comprimento de cada fio era de 10 cm cada, exceto para os fios que conectam a última letra aos pontos que devem ser mais longos (~ 25 cm). Além disso, os fios conectados à primeira letra que serão conectados ao arduino e à fonte de alimentação devem ser mais longos.
- Diasy chain LEDs com fios. Os fios são alimentados através dos orifícios na placa traseira impressa em 3D de cada caixa de correio.
- A capa da caixa de correio foi fixada com cola
- Partes do rack linear para o atuador precisam ser coladas
- O suporte linear é preso na parte de trás da caixa de correio usando cola
Etapa 6: montagem dos atuadores
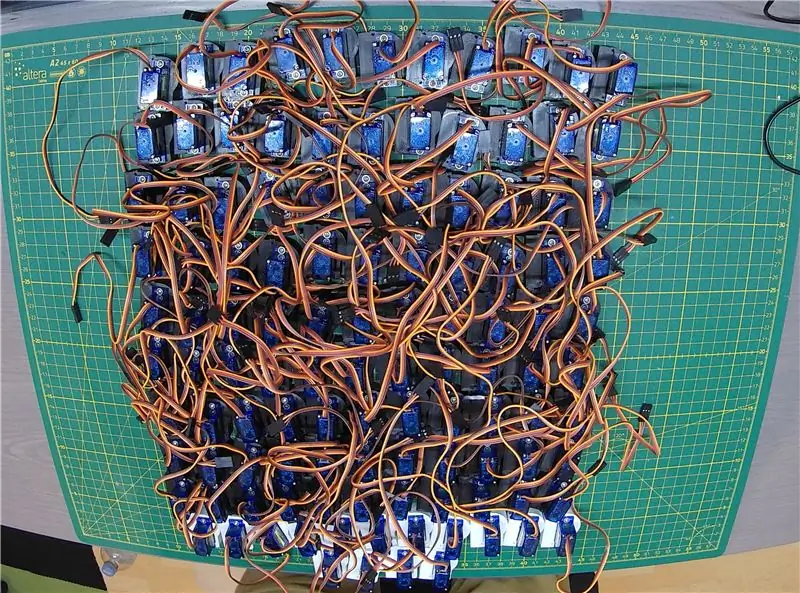
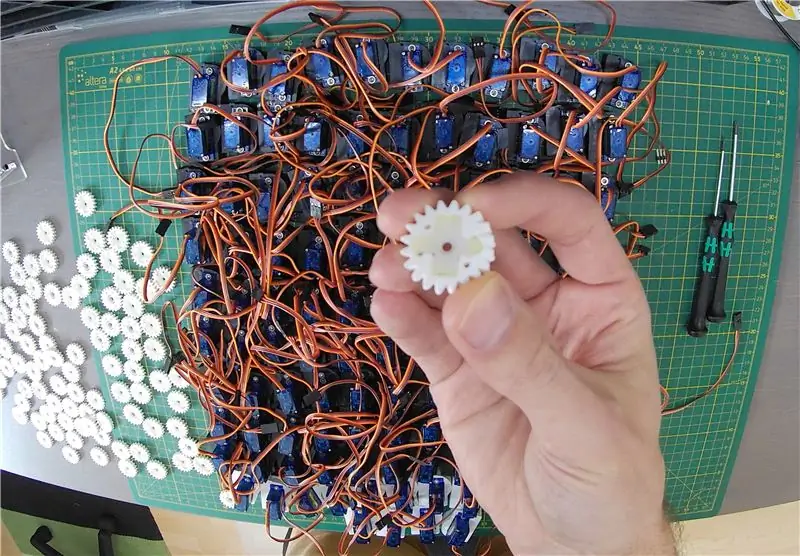
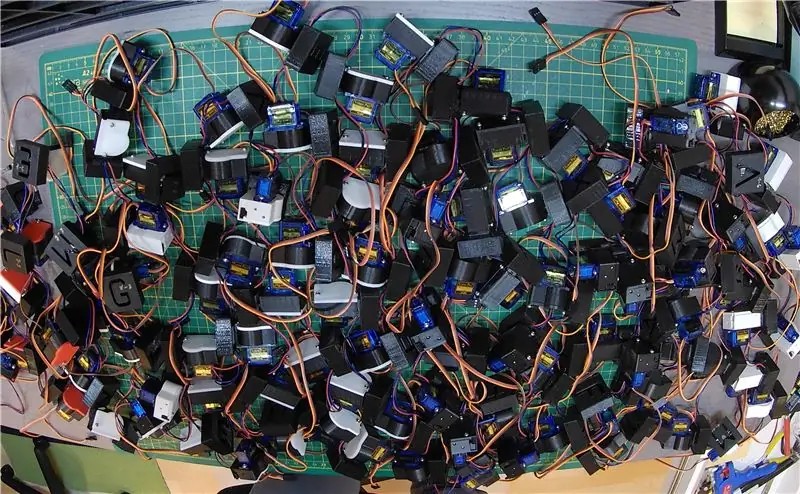
A nova montagem dos atuadores foi um procedimento muito tedioso e demorou muito tempo.
- Anexe o servo ao alojamento impresso em 3D usando os parafusos incluídos
- A engrenagem redonda é presa ao servo usando a cruz de plástico incluída, mas primeiro a cruz precisa ser cortada no formato e presa à engrenagem usando epóxi.
- Anexe a engrenagem ao servo usando o parafuso incluído
- Antes de inserir o rack linear, cada servo foi zerado para a mesma posição
- Inserindo o rack linear com a caixa de correio
- Inserindo duas porcas hexagonais M2 na caixa impressa em 3D que será usada para fixá-la à placa posterior mais tarde
- Feche a caixa com a tampa impressa em 3D usando os parafusos auto-roscantes M2.2
No final, acabamos com uma grande confusão de atuadores em cadeia diasy, como mostrado na imagem acima
Etapa 7: fazendo a placa traseira
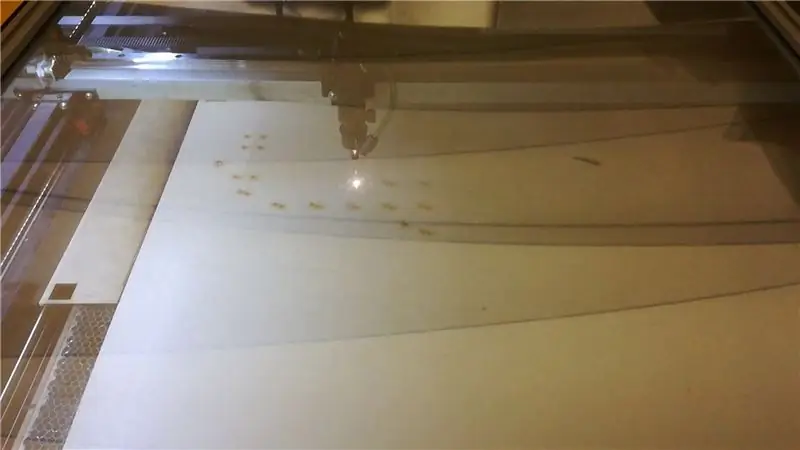
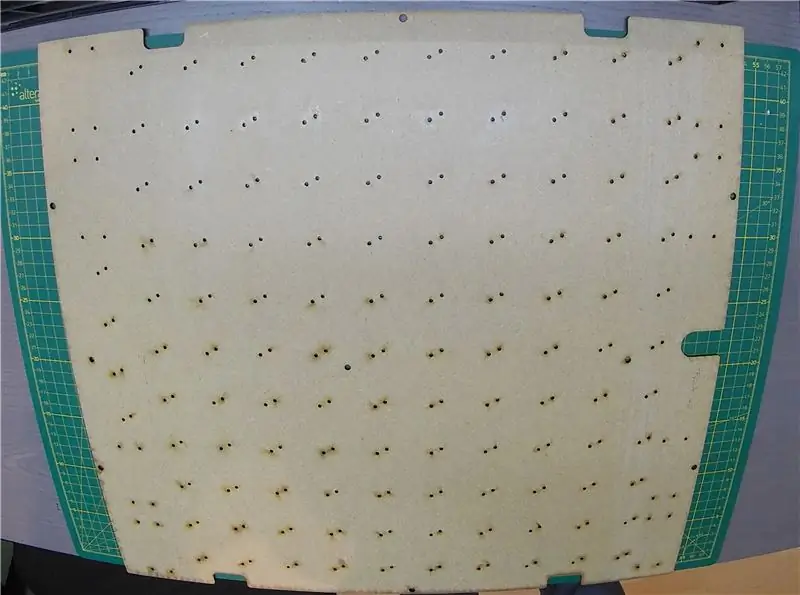
A placa traseira foi cortada a laser de madeira HDF de 3 mm de espessura usando um cortador a laser de CO2 de nosso criador local. No início, testamos o compensado, mas acabou sendo muito frágil para suportar o peso de todos os componentes. Teria sido ainda melhor usar alumínio neste caso, mas é claro que é mais caro e não pode ser cortado com um laser de CO2. O arquivo dxf para a placa traseira está anexado.
Etapa 8: Conecte os componentes à placa traseira e à fiação
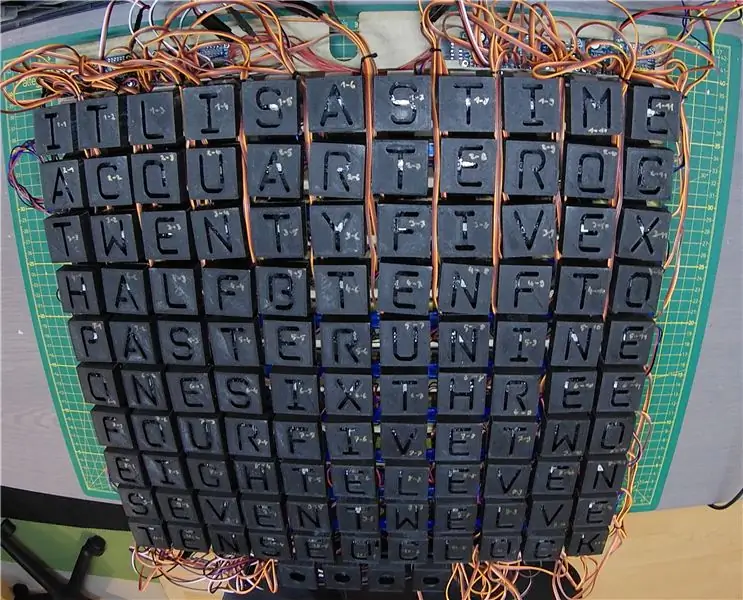
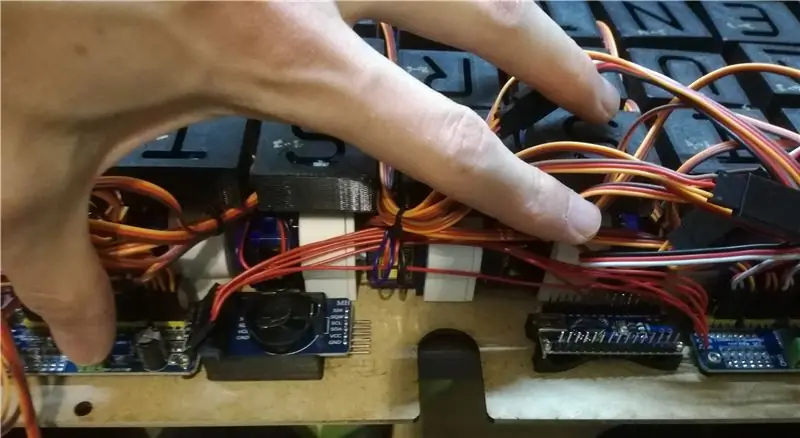
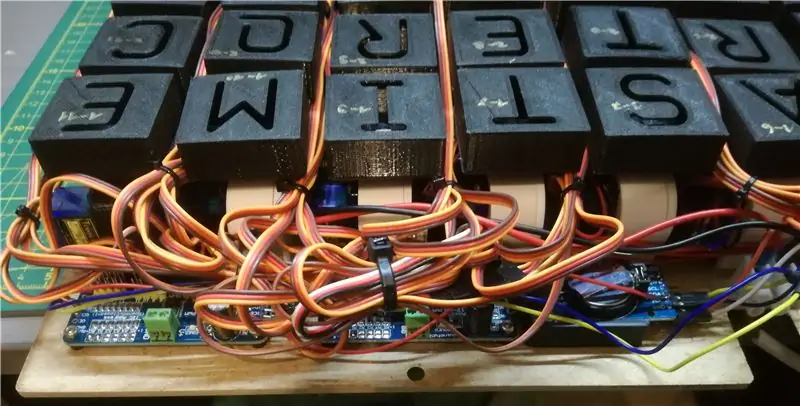
A princípio, as placas PCA9685 devem ser conectadas à placa traseira usando espaçadores de PCB. Em seguida, o Arduino nano e o módulo RTC podem ser colocados conforme mostrado na imagem acima. Para os dois últimos, usamos suportes impressos em 3D que foram fixados com cola quente. Os componentes foram conectados conforme mostrado no diagrama de fiação. Observe que é melhor alimentar cada PCA9685 separadamente por meio do bloco de terminais. Inicialmente conectamos também os conectores V + e GND e conectamos apenas o bloco terminal da primeira placa (como sugerido na página adafruit), porém, neste caso toda a corrente está passando pela primeira placa e acabamos queimando o MOSFET do circuito de proteção reversa. Também há uma planilha anexada mostrando o cabeamento dos servos. Os cabos de extensão para os servos foram usados sempre que necessário. Observe que você deve atribuir diferentes endereços I2C a cada PCA9685, conforme explicado na página adafruit.
Os atuadores foram então fixados à placa traseira usando parafusos 228x M2. O trabalho foi novamente muito monótono mas depois de terminado o relógio já começava a ganhar forma. Nós também tentamos organizar os servo cabos da melhor forma possível, mas no final o cabeamento ainda estava muito bagunçado.
A energia era fornecida passando o cabo DC pela placa traseira e conectando-o a um bloco de terminais.
Etapa 9: Anexando a placa traseira à estrutura
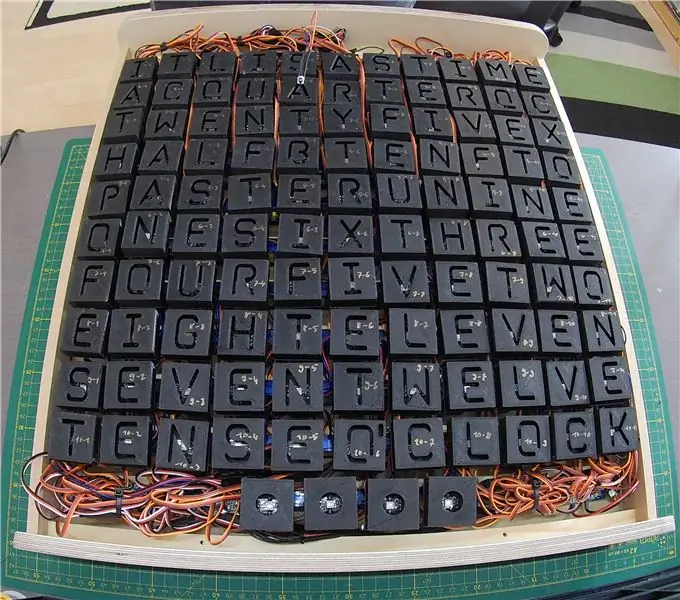
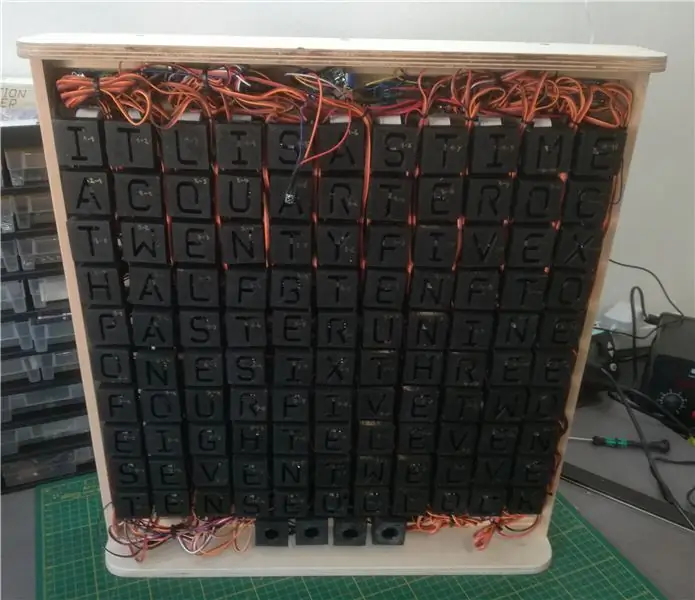
Depois que todos os componentes foram montados e os cabos organizados, prendemos a placa traseira à estrutura usando 6 parafusos M4. Infelizmente, deixamos muito pouco espaço para todos os cabos caberem, então eles tiveram que ser apertados um pouco.
Etapa 10: Calibrando os Servos
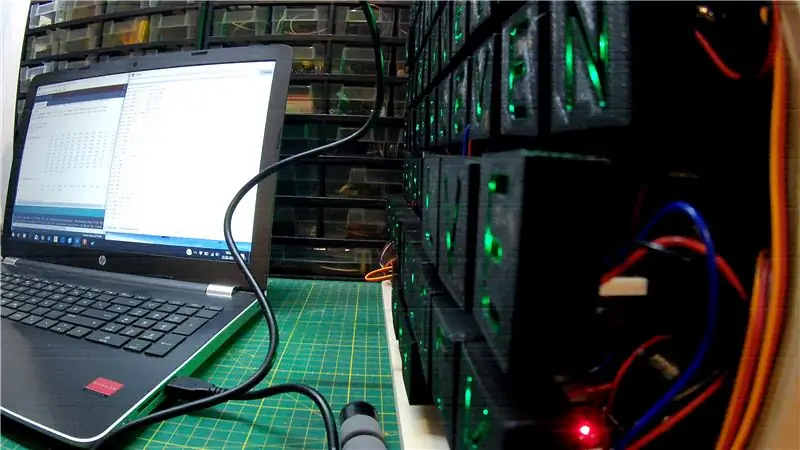
Como a altura de todas as caixas de correio era ligeiramente diferente após a montagem, usamos o código em anexo para calibrar todos os servos de forma que as caixas de correio tenham as mesmas posições mínima e máxima. Para a posição máxima, tentamos colocar a caixa de correio o mais próximo possível da tela. As posições mín. / Máx. Calibradas para cada servo são posteriormente inseridas no código principal.
Etapa 11: enviando o código
Em anexo está o código principal do word clock. Existem três tipos de efeitos para mostrar o tempo.
- Mova rapidamente todas as letras para trás (uma após a outra) e acenda LEDs com a mesma cor aleatória. Em seguida, mova rapidamente as letras que exibem a hora para a frente, uma após a outra, e iluminam cada palavra em uma cor aleatória.
- Mova rapidamente todas as letras para trás (uma após a outra) e acenda LEDs com a mesma cor aleatória. Mova lentamente cada palavra que exibe o tempo para a frente (todas as letras simultaneamente) e esmaece a cor da cor de fundo para um valor aleatório.
- Mova rapidamente todas as letras para uma posição aleatória (uma após a outra) e acenda LEDs com cores aleatórias diferentes. Em seguida, mova lentamente todas as letras para trás e esmaeça a cor. Continue com 1. ou 2.
Eu também queria implementar um efeito no qual o ponto que está mostrando o minuto atual está se movendo gradualmente para frente e desbotando a cor, de modo que esteja na posição frontal com a cor correta quando o minuto terminar. Infelizmente, ainda não o fiz funcionar porque parece que o receptor IR não responde.
Etapa 12: anexando a tela
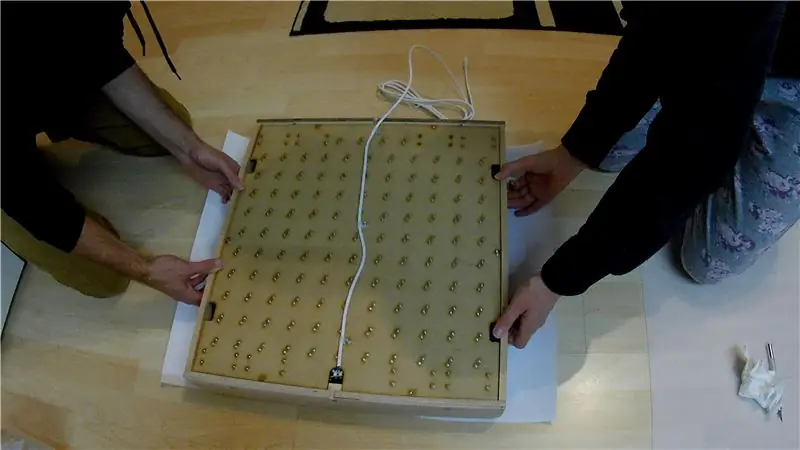
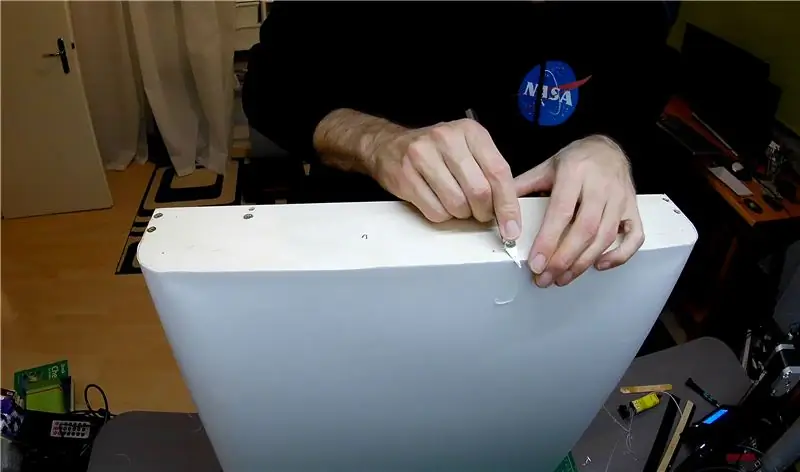
No início, queríamos usar tecido branco como tela. O problema é que depois de prendê-lo na moldura o tecido se dobrou no centro e acabamos com uma distorção de almofada de alfinetes. Decidimos então usar uma fina folha de PVC branca para a tela. A folha também é anunciada para fazer cortinas de abajur para que tenha uma transmissão razoável, mas não é transparente, de modo que as caixas de correio pretas ficam ocultas. Em nosso primeiro teste, aplicamos a folha com epóxi, mas ela não grudou muito bem, então mudamos para cola quente. No entanto, tome cuidado para que, se a cola estiver muito quente, ela pode realmente derreter o papel alumínio. O excesso de folha foi removido com uma faca de exacto.
Etapa 13: Prendendo as tampas superior e inferior
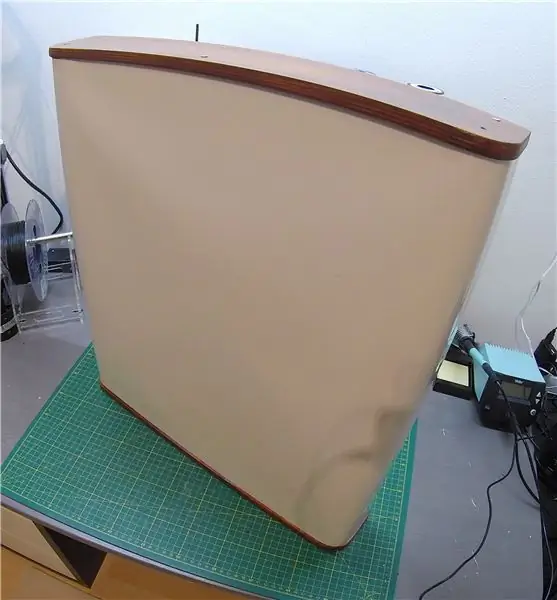
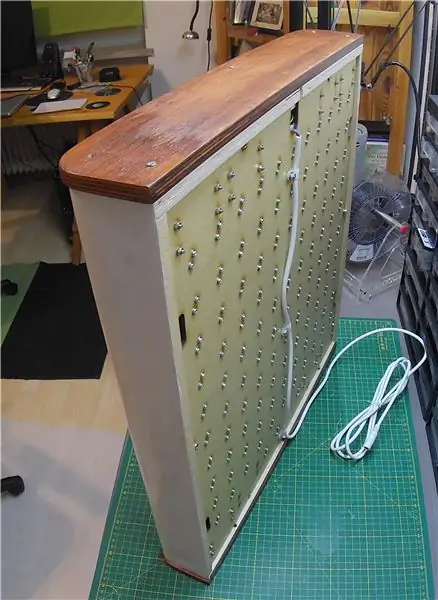
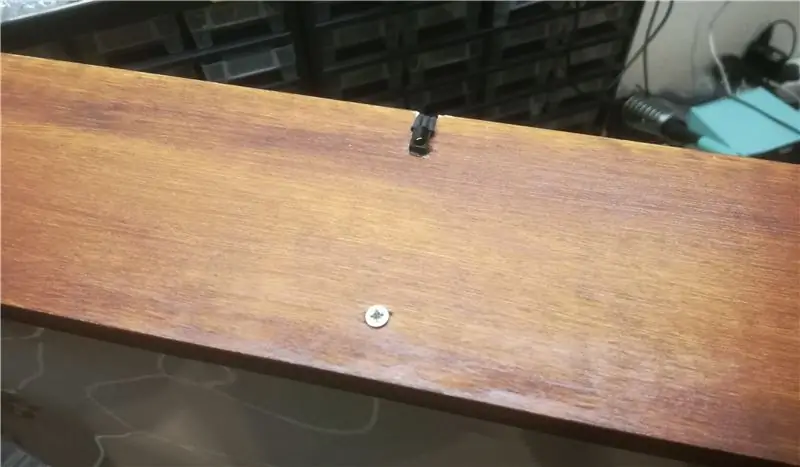
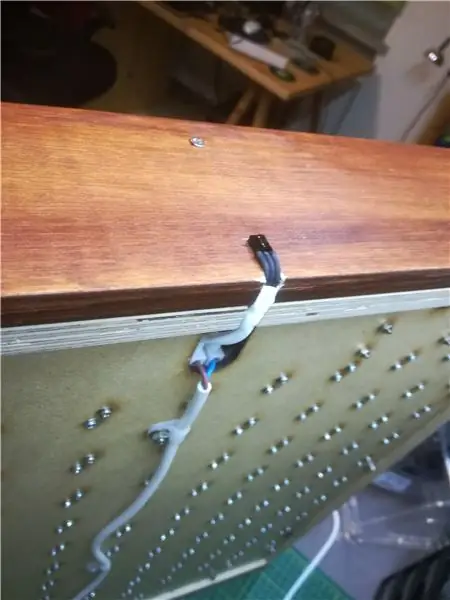
Por fim, as tampas de madeira manchadas foram fixadas na parte superior e inferior. A cor escura faz um bom contraste com a tela branca. O receptor IR foi alimentado através do orifício na placa traseira e fixado na tampa superior com cola quente.
Etapa 14: Relógio e resumo finalizados
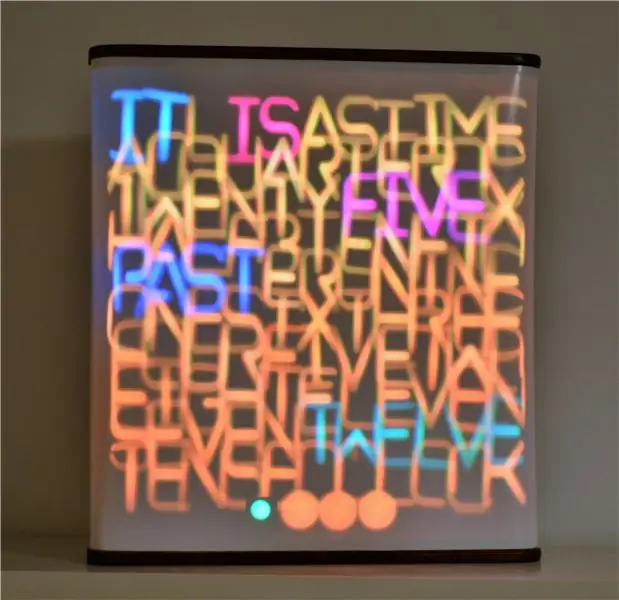
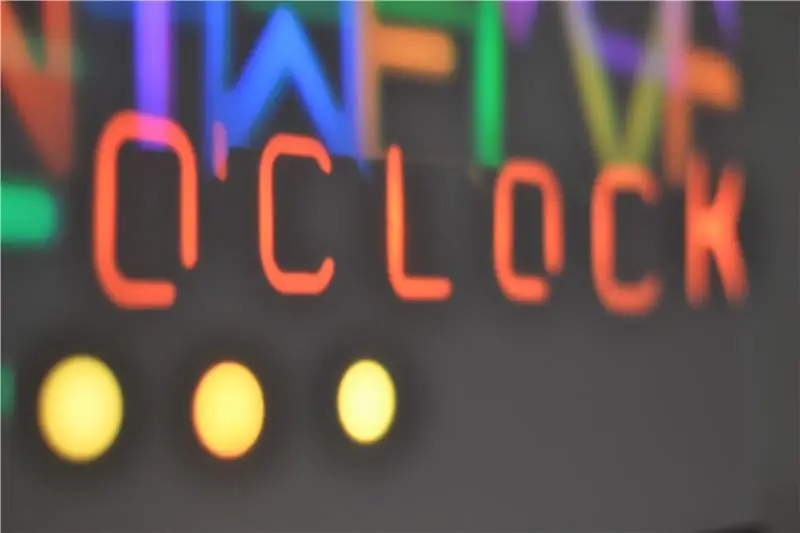
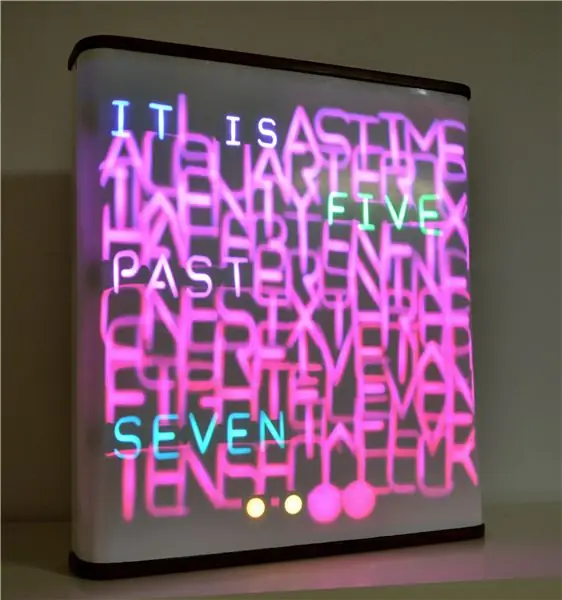
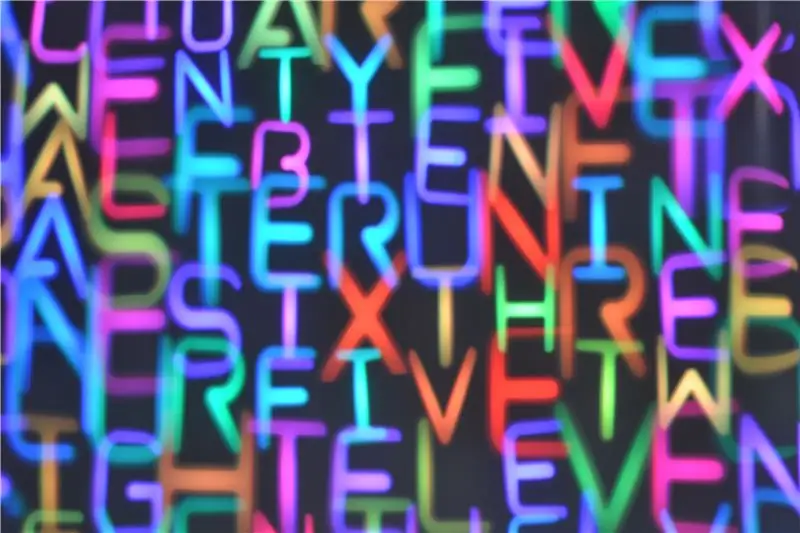
Após dois meses de trabalho intensivo, o relógio finalmente estava pronto e funcionando. No geral, estamos muito felizes com o resultado. Mover as letras atrás da tela em conjunto com a alteração das cores dos LEDs produz efeitos de aparência muito legais. No final, as letras não se alinhavam perfeitamente e a tela não era 100% plana, mas isso quase a torna ainda melhor. Certamente há coisas que podem ser melhoradas, mas eu não acho que haverá uma versão 2.0 por causa do esforço monumental desta construção, a menos que da próxima vez terceirizemos a produção para a China.
Se você gostou dessa compilação e conseguiu rolar para baixo até o final, vote em nós no concurso Epilog.
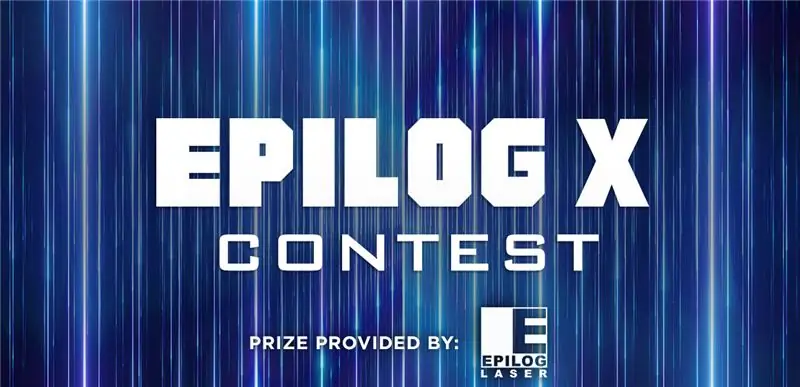
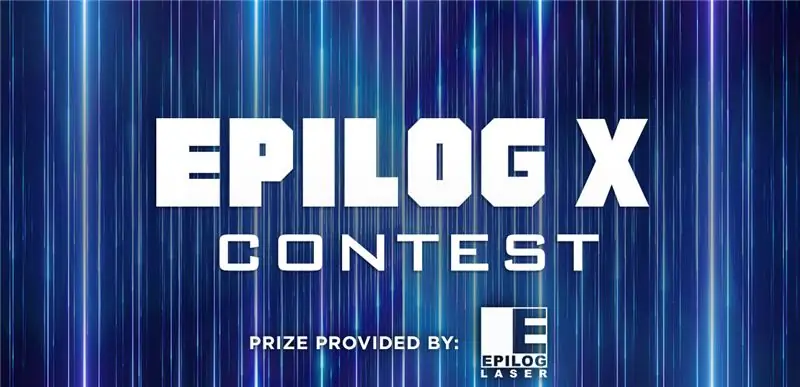
Primeiro prêmio no Epilog X Contest
Recomendado:
Faça você mesmo, Arduino, carro controlado por Bluetooth: 6 etapas (com imagens)
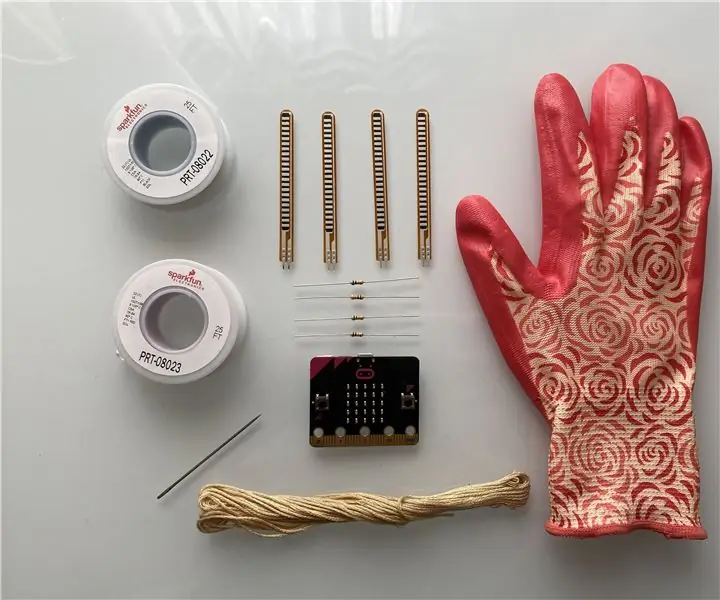
Carro controlado por Bluetooth DIY Arduino: Olá amigos! Meu nome é Nikolas, tenho 15 anos e moro em Atenas, Grécia. Hoje vou mostrar como fazer um carro controlado por Bluetooth de 2 rodas usando um Arduino Nano, uma impressora 3D e alguns componentes eletrônicos simples! Certifique-se de assistir meu
Sistema de irrigação controlado por WiFi 'inteligente' alimentado por energia solar: 6 etapas (com fotos)
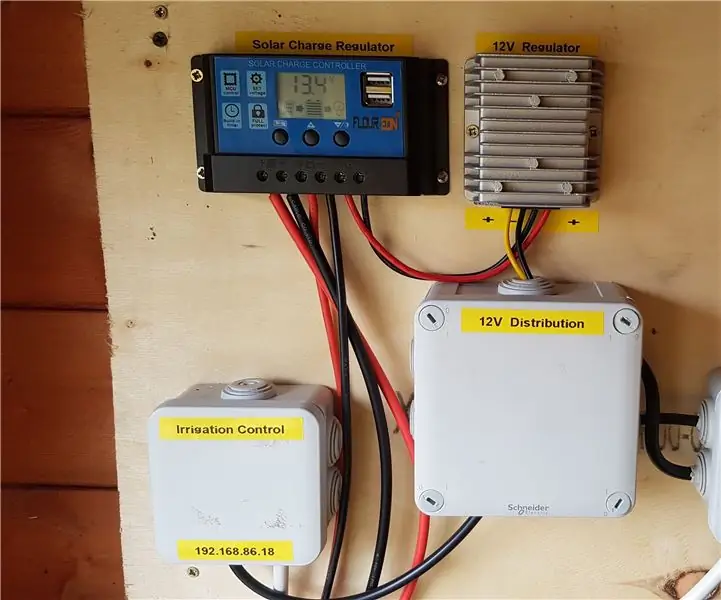
Sistema de irrigação controlado por Wi-Fi 'inteligente' alimentado por energia solar: este projeto usa peças solares DIY e 12v padrão do ebay, juntamente com dispositivos Shelly IoT e alguma programação básica em openHAB para criar uma rede elétrica de jardim e irrigação inteligente totalmente movida a energia solar setup.System Highlights: Fu
2 potenciômetros e 2 servos: movimento controlado com Arduino: 4 etapas
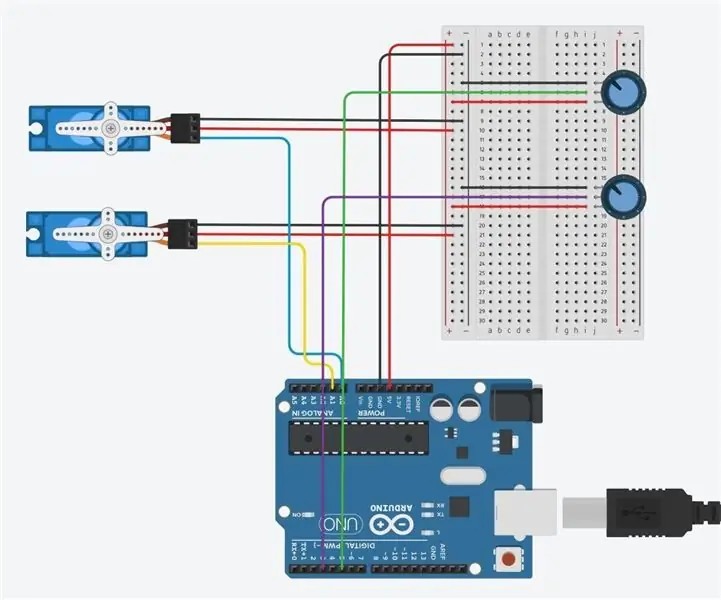
2 potenciômetros e 2 servos: movimento controlado com Arduino: primeiro você precisa reunir materiais relevantes para montar este circuito
Gesture Hawk: robô controlado por gestos manuais usando interface baseada em processamento de imagens: 13 etapas (com imagens)
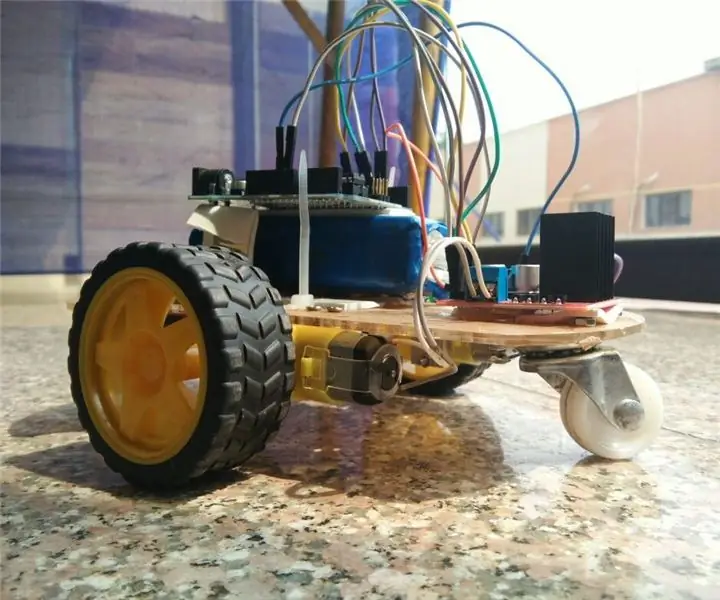
Gesture Hawk: Robô controlado por gestos manuais usando uma interface baseada em processamento de imagem: Gesture Hawk foi apresentado no TechEvince 4.0 como uma interface homem-máquina baseada em processamento de imagem simples. Sua utilidade reside no fato de que nenhum sensor adicional ou vestível, exceto uma luva, é necessário para controlar o carro robótico que funciona em diferentes
Faixas de luz LED com desvanecimento controlado por sensor e alimentadas por Arduino: 6 etapas (com imagens)
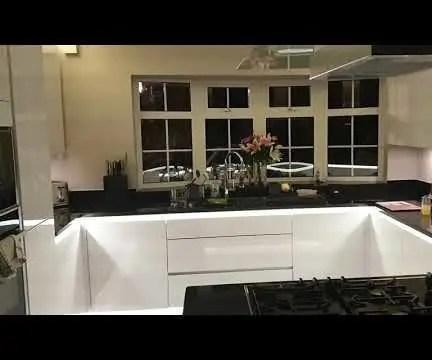
Faixas de luz LED com desvanecimento controlado por sensor e alimentadas por Arduino: Recentemente, atualizei minha cozinha e sabia que a iluminação iria "melhorar" a aparência dos armários. Eu optei por ‘True Handless’ então tenho um espaço sob a superfície de trabalho, bem como um kickboard, debaixo do armário e na parte superior dos armários disponíveis e