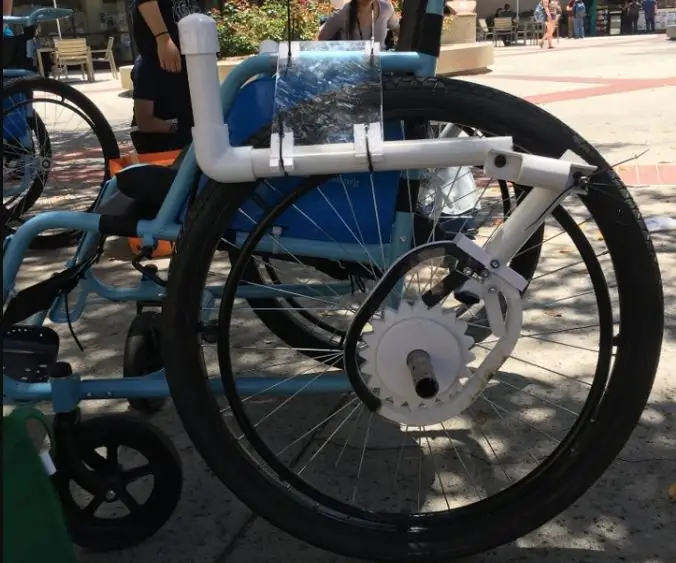
Índice:
- Etapa 1: Crie a tampa do revestimento externo para o corpo no SolidWorks
- Etapa 2: crie o corpo no SolidWorks
- Etapa 3: Crie a junta no SolidWorks
- Etapa 4: Crie o braço de alavanca / alça no SolidWorks
- Etapa 5: Crie o descanso de braço no SolidWorks
- Etapa 6: Crie a engrenagem no SolidWorks
- Etapa 7: Criar Pawl no SolidWorks
- Etapa 8: Criar botão de direção no SolidWorks
- Etapa 9: Crie o suporte de tubo
- Etapa 10: Comece a montagem no SolidWorks
- Etapa 11: Solicite peças da McMaster-Carr
- Etapa 12: Obtenha as peças na loja de ferragens
- Etapa 13: fabricando as peças
- Etapa 14: Junte todas as peças
- Etapa 15: Teste Iterativo
- Etapa 16: Página de contribuições
2025 Autor: John Day | [email protected]. Última modificação: 2025-01-23 15:03
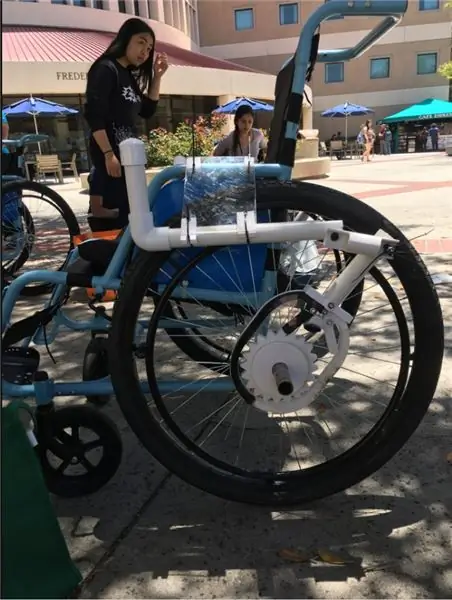
A cadeira de rodas comum contém muitas falhas para pessoas com fraqueza nas extremidades superiores ou recursos limitados. Nossa equipe foi encarregada de projetar um acionador de alavanca de cadeira de rodas para as cadeiras de rodas da Missão para Cadeira de Rodas Livre que permitiria aos usuários ir mais longe em suas cadeiras e ajudar aqueles com fraqueza nas extremidades superiores a usar as cadeiras. O acionador de alavanca para cadeira de rodas do Support System é um dispositivo de baixo custo que reduz substancialmente a necessidade de movimento do ombro e aborda os níveis de fadiga, utilizando acionadores de alavanca horizontal em vez de vertical, o que seria adequado para pacientes debilitados e pacientes em áreas rurais. O acionador de braço de alavanca vertical típico concentra-se muito nos músculos dos braços e ombros, o que pode causar complicações para pacientes com fraqueza nos membros superiores. Portanto, nossa equipe projetou um driver de alavanca horizontal que visa o uso dos músculos do peito para trazer facilidade para as pessoas que não podem utilizar os músculos do ombro.
Proposta de Mercado e Valor
Uma maneira de lidar com a dor no ombro e a fadiga associada ao uso de cadeira de rodas em indivíduos particularmente de vilarejos rurais com estradas não pavimentadas, nosso acionador de alavanca visa aliviar o problema usando o movimento para frente / para trás em vez de um movimento para cima / para baixo junto com um apoio de braço aprimorado para maior conforto e suporte. Como as vilas rurais e as estradas não pavimentadas são geralmente muito rochosas e não lisas, o paciente teria que usar ainda mais força no braço de alavanca para mover sua cadeira de rodas a uma certa distância em comparação com um caminho liso. Portanto, as pessoas com fraquezas nas extremidades superiores nas áreas rurais são ainda mais prejudicadas porque precisam de mais movimento e força para se mover de um lugar para outro, o que causa problemas à medida que enfraquecem continuamente à medida que continuam a utilizar os músculos do ombro no dia a dia. Assim, ao implementar uma chave de alavanca horizontal, os indivíduos de áreas rurais com fraquezas nas extremidades superiores não só serão capazes de se mover livremente, mas também de uma forma que reduz o uso extenuante dos músculos do ombro, pois eles usam a força em seu peito.
Análise de Custo
Decidimos usar PVC, acrílico e ABS. Foi um compromisso de força e custo. Os três materiais são relativamente mais baratos, mas resistentes o suficiente para funcionar corretamente. O custo estimado é de cerca de US $ 170. Originalmente, planejamos usar alumínio para a maioria dos componentes de nosso acionador de alavanca, como a caixa externa e as alças do braço, porque o alumínio é mais barato do que o aço. No entanto, depois de fazer pesquisas, vimos que o uso de folhas grossas e hastes de alumínio não seria o ideal devido aos custos pendentes para obter quantidades substanciais de metal. Em vez disso, encontramos alternativas mais baratas usando materiais diferentes para peças diferentes. Usamos uma grande folha de acrílico para o revestimento externo e cortamos a folha a laser em partes menores, que custaram cerca de US $ 25. Em comparação, grandes folhas de alumínio custariam mais de US $ 70. Além disso, também decidimos usar tubos de PVC em nossas alças de braço em vez de hastes de metal, porque os tubos de PVC não são apenas resistentes, mas também extremamente baratos. Embora as hastes de alumínio possam ter sido mais resistentes, gastaríamos cerca de US $ 30 em cada lado da cadeira de rodas. Em contraste, os tubos de PVC custaram cerca de US $ 5. A maior parte do nosso custo vem da impressão 3D ABS. Como imprimimos três partes do nosso sistema, o tempo total para imprimir todas essas peças levou cerca de 32 horas. Como resultado, com a taxa horária para usar a impressora 3D, o total chegou a $ 130.
Materiais e Design de Prototipagem
- Tubo de PVC ~ $ 2,16
- Tampa do soquete de PVC ~ $ 1,66
- cotovelo de 90 graus em PVC ~ $ 2,28
- Folha de acrílico ~ $ 24,98
- Engrenagens ABS, linguetas ABS, botões ABS ~ $ 130
- Parafusos de aço ~ $ 6,92
- Elásticos ~ $ 3,18
- Adesivo para artesanato E6000 ~ $ 4,29
Etapa 1: Crie a tampa do revestimento externo para o corpo no SolidWorks
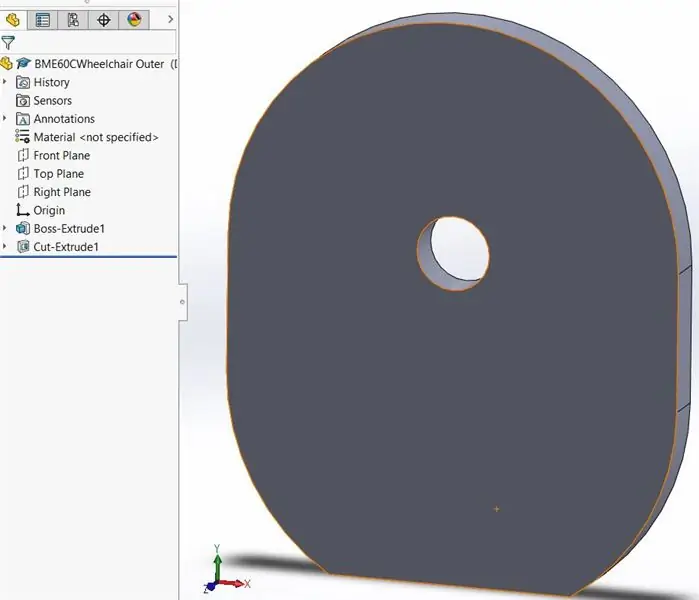
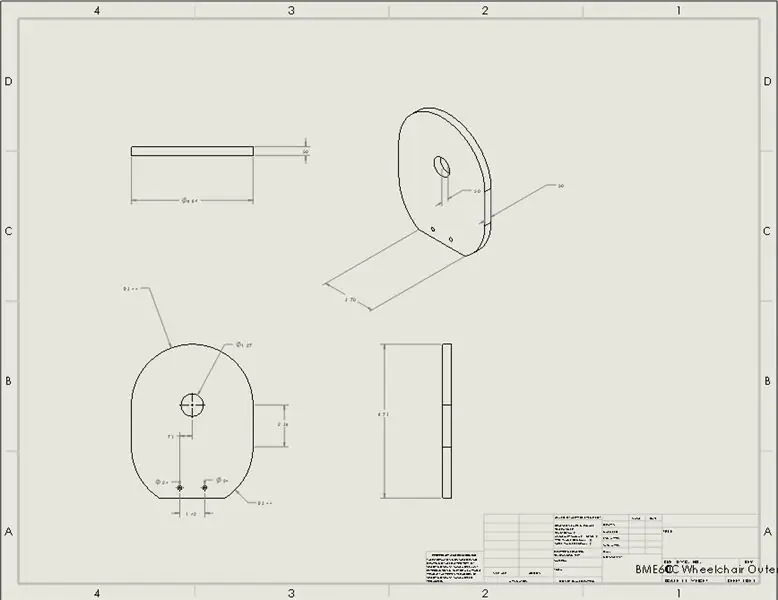
Antes de iniciar todo o projeto, defina as dimensões usando MMGS.
Usando o plano frontal, crie um novo esboço e desenhe um círculo na origem com um diâmetro de 175 mm. Em seguida, esboce duas linhas verticais nas tangentes do círculo, ambas de 60 mm. Depois, desenhe arcos tangentes no final de ambas as linhas e conecte-os com uma linha horizontal. Em seguida, usando o recurso "aparar entidades", apare a metade inferior do círculo dentro da região.
Assim que o esboço estiver concluído, faça a extrusão da saliência do esboço usando uma extrusão cega de 12,70 mm. Quando a extrusão estiver concluída, abra um novo esboço e desenhe um círculo alinhado com o topo das linhas tangentes com o diâmetro de 32,20 mm e corte a extrusão usando "through all" e faça um furo.
Para fazer os dois círculos inferiores, abra um novo esboço e desenhe dois círculos com o diâmetro de 6 mm e faça-os a 15 mm de distância da parte inferior e 58,84 mm de distância do centro do arco tangente. Quando o esboço estiver concluído, use extrusão de corte usando "através de todos" para fazer dois furos.
Etapa 2: crie o corpo no SolidWorks
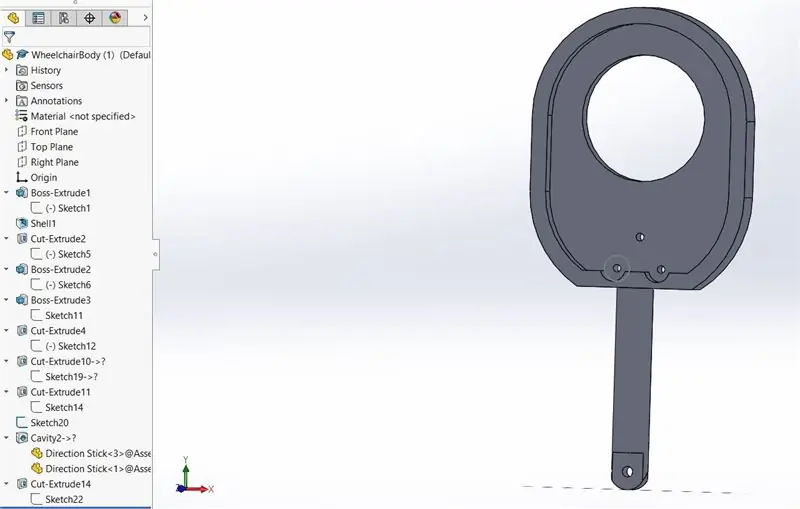
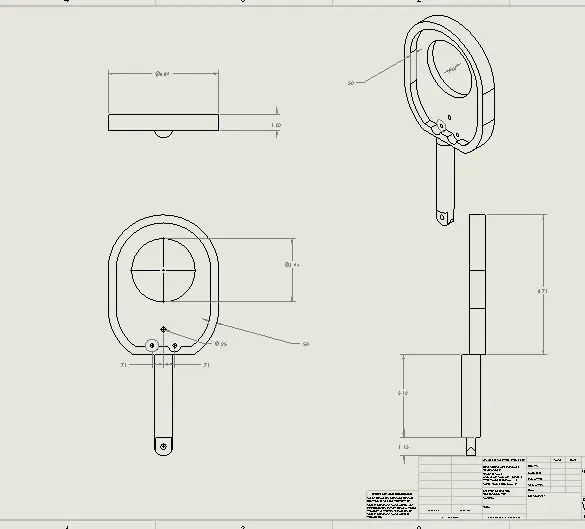
Para iniciar o corpo, repita o esboço como na primeira parte para criar a forma geral do corpo e extrudá-lo em 25,40 mm. Após a extrusão da peça, use a opção de casca em uma das faces da peça com a dimensão de 12,70 mm.
Depois, abra um novo sketch e desenhe um círculo no centro da peça com o diâmetro de 100mm que está a 133,84mm da parte inferior e 87,50mm longe dos lados da peça. Quando o esboço estiver concluído, corte a extrusão usando "através de todos" mais uma vez para criar um furo.
Para criar a alavanca, crie um novo esboço no plano superior e gire a peça para baixo. Comece o esboço fazendo um círculo com um diâmetro de 28,74 mm na base da peça anterior e extrude 130 mm.
Depois que a alavanca for criada, crie um novo esboço na base da alavanca. Desenhe duas linhas horizontais equidistantes da origem com 25,10 mm de comprimento. Depois, conecte as duas linhas com arcos tangentes com altura de 14mm. Assim que o esboço estiver concluído, faça a extrusão cega do novo esboço em 30 mm.
Usando a peça extrudada mais recente, crie um novo esboço no plano frontal e faça o esboço de um círculo que está a 14,95 mm de distância do topo e 12,55 mm de distância da lateral. Em seguida, corte a extrusão em tudo para criar um furo.
Com o corpo geral, esboce dois orifícios na parte inferior do corpo com diâmetros de 6 mm e distância de 36 mm um do outro, 15 mm de distância da parte inferior e 58,84 mm de distância do topo dos arcos tangentes. Depois, corte a extrusão em tudo para criar dois furos.
Na parte inferior da peça, crie um novo esboço. Faça linhas retas em ambos os lados de 14,93 mm. Faça uma linha horizontal de 28,74 mm para conectar as duas linhas. Desenhe um círculo com raio de 14,37 mm e alinhe-o ao círculo já no centro. Corte-o para fazer um semicírculo. Corte a extrusão em toda a figura em forma de rampa na parte inferior da peça para deixar uma borda arredondada.
* Para se preparar para a cavidade, crie um novo esboço no plano posterior. Desenhe um círculo com um raio de 20,57 mm, 15 mm de distância da parte inferior e 58,84 do arco tangente lateral. Depois de montar todas as peças juntas, você edita a peça dentro da montagem e usa o recurso de cavidade para criar os semicírculos.
No plano frontal, faça um novo esboço. Desenhe um círculo no centro com um diâmetro de 6,35 mm entre o círculo grande e os dois círculos pequenos próximos à parte inferior. Faça o círculo a 40,13 mm de distância da parte inferior e 33,70 mm de distância do arco tangente nas laterais. Depois, corte a extrusão em tudo para criar um pequeno círculo no centro.
* Esta etapa deve ser continuada posteriormente, após a montagem de todas as peças.
Etapa 3: Crie a junta no SolidWorks
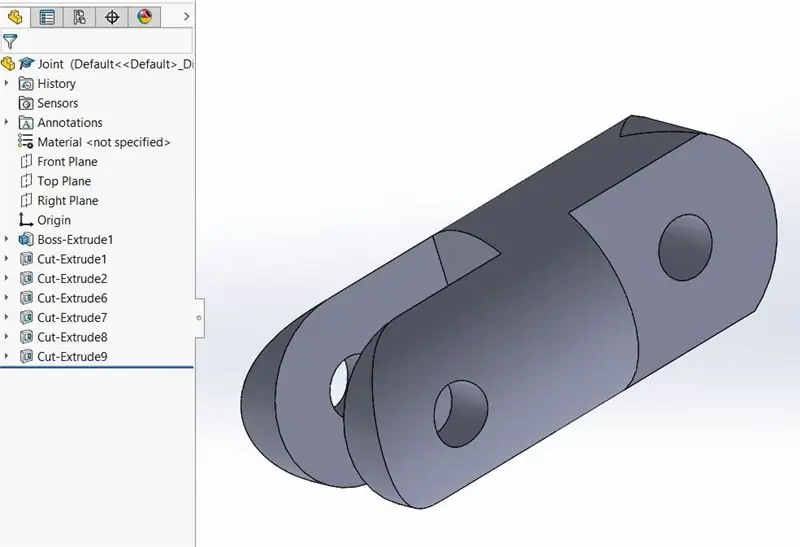
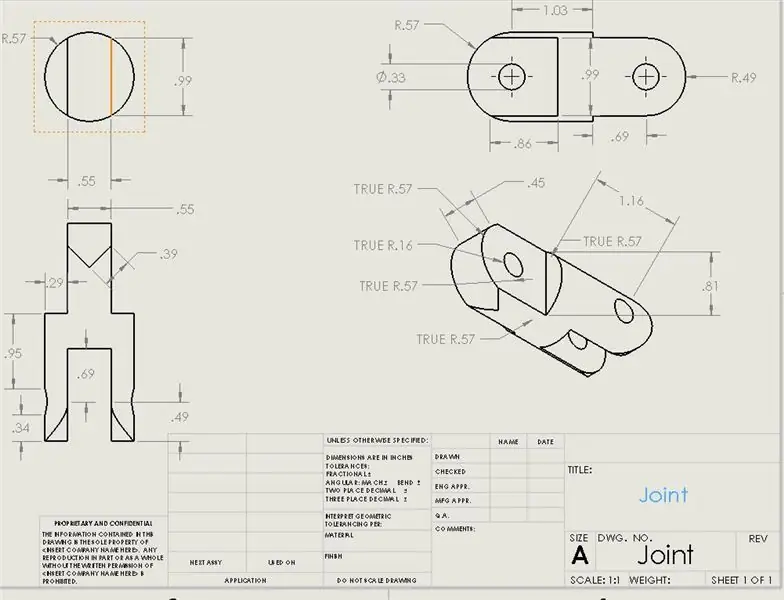
Para iniciar a união, comece criando um novo esboço na placa frontal e desenhe um círculo com o diâmetro de 28,74 mm. Faça a extrusão cega do círculo que acabou de ser esboçado em 120 mm.
Em seguida, gire a peça e faça o croqui na parte de trás. Desenhe duas linhas verticais com comprimento de 25,10 mm e 7,37 mm de distância da borda do círculo. e extrusão de corte usando "blind" e uma profundidade de 30 mm para ambas as regiões.
Em seguida, visualizando do plano direito, esboce um círculo na região que acabamos de cortar. O diâmetro deve ser de 8,38 mm com uma distância de 12,55 mm da borda superior e 14,95 mm da borda lateral. Faça um corte cego de 30 mm.
No plano certo, faça linhas retas em ambos os lados com 15,05 mm. Faça uma linha vertical de 28,74 mm para conectar as duas linhas. Desenhe um círculo com raio de 14,37 mm e alinhe-o ao círculo já no centro. Corte-o para fazer um semicírculo. Corte a extrusão em toda a figura em forma de rampa na parte inferior da peça para deixar uma borda arredondada.
Depois, visualizando do plano posterior, esboce duas linhas verticais com comprimento de 25,10 mm e 7 mm do centro. Faça um corte cego com profundidade de 35mm.
No plano direito, esboce um círculo na parte direita com o centro a 17,24 mm de distância da aresta esquerda da extrusão de corte cego da parte para criar um círculo
No plano direito, repita a figura em forma de rampa do lado esquerdo da peça.
Etapa 4: Crie o braço de alavanca / alça no SolidWorks
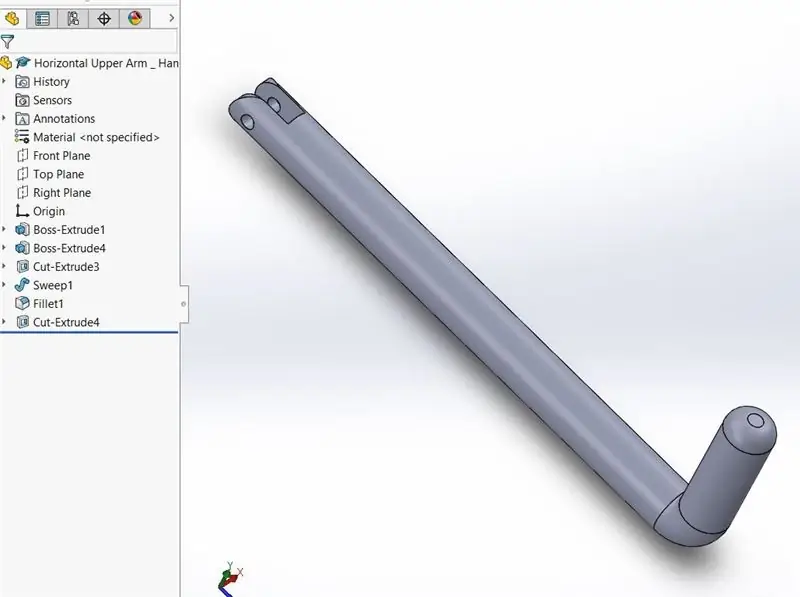
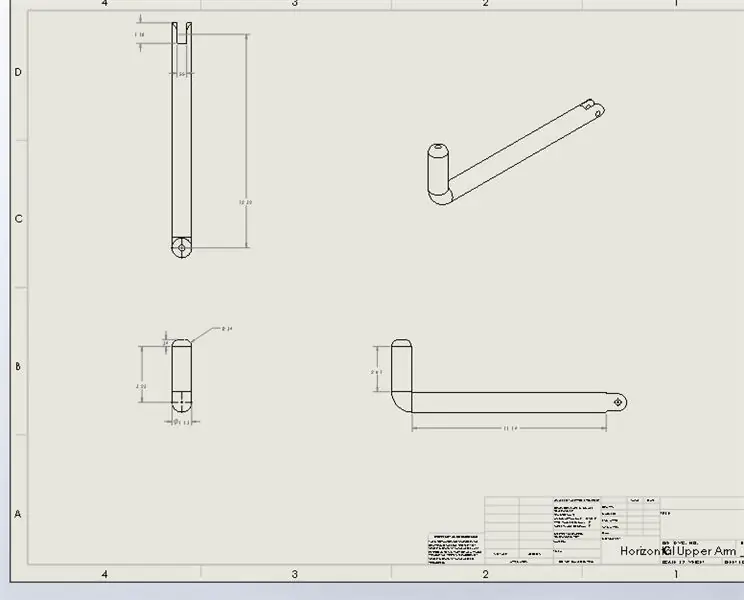
No plano frontal, esboce um círculo com um diâmetro de 28,75 mm na origem. Boss extrude 275 mm.
Em seguida, vá para o plano posterior e esboce duas linhas verticais com o comprimento de 25,10 mm e uma distância de 7 mm do centro. Extrude as duas linhas de modo que haja uma lacuna no meio com dimensão de extrusão de 35 mm.
Na peça que acabamos de extrudar, esboce um círculo com um diâmetro de 8,40 mm com uma distância de 17,76 mm do centro do círculo até a aresta e 12,56 mm da parte inferior da peça. Corte a extrusão em tudo para criar um furo.
No plano direito, crie uma linha curta com o comprimento de 9,24 mm que se conecta com a extremidade esquerda da peça. Desenhe um arco com raio de 30 mm. Em seguida, desenhe uma linha vertical que conecte a outra extremidade do arco com o comprimento de 76,39 mm. Depois que o esboço estiver concluído, faça uma varredura no esboço.
Depois, faça um fillet no topo da peça que acabamos de varrer 10 mm.
Por último, no plano certo, faça linhas retas horizontais em ambos os lados da peça com o furo que criamos com 17,78 mm de comprimento. Faça uma linha vertical de 25,10 mm para conectar as duas linhas. Desenhe um círculo com um raio de 12,56 mm e alinhe-o ao círculo já no centro. Corte-o para fazer um semicírculo. Corte a extrusão em toda a figura em forma de rampa na parte inferior da peça para deixar uma borda arredondada.
Etapa 5: Crie o descanso de braço no SolidWorks
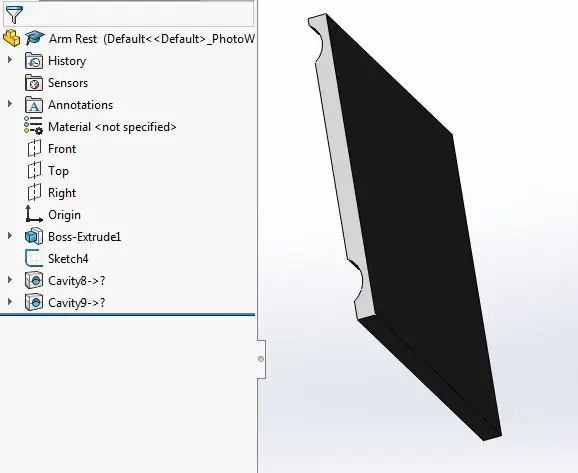
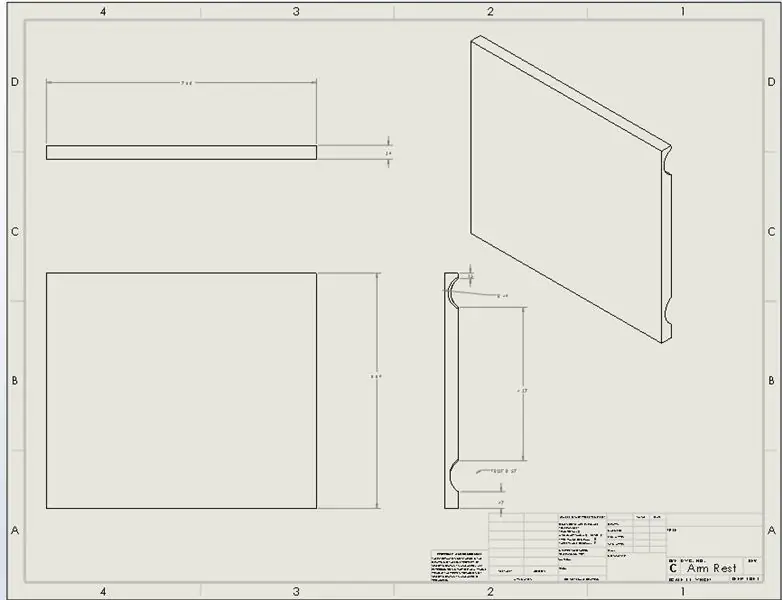
No plano frontal, esboce um retângulo com uma altura de 170 mm e comprimento de 195 mm e faça uma extrusão cega de 10 mm.
* Após a montagem, use o recurso de cavidade para criar os recuos no prisma retangular
Etapa 6: Crie a engrenagem no SolidWorks
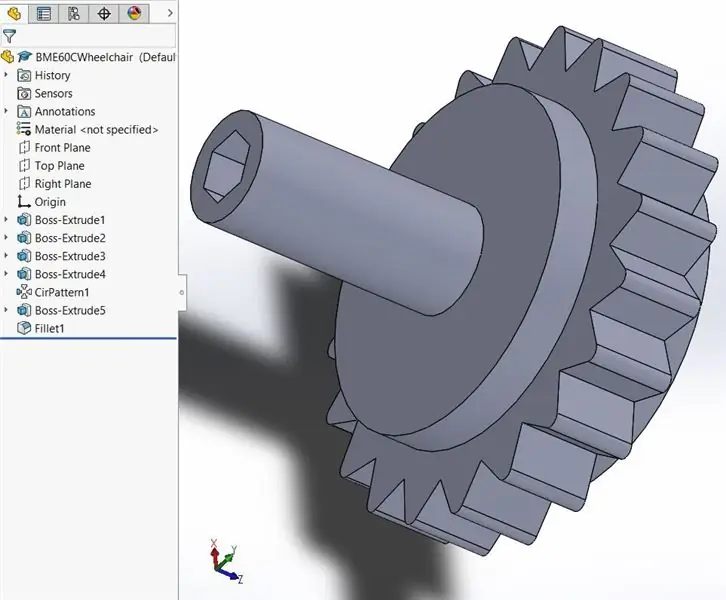
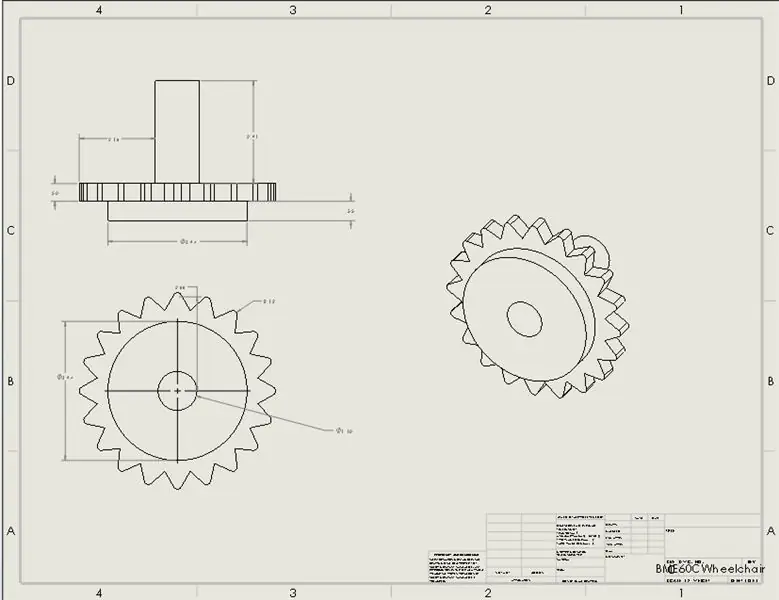
Para iniciar a engrenagem, crie um novo esboço no plano frontal e desenhe dois círculos do mesmo ponto com os diâmetros de 25,40 mm e 31,75 mm. Em seguida, faça a extrusão da saliência usando uma extrusão cega a 30 mm.
Assim que a extrusão estiver concluída, crie outro esboço no plano frontal e desenhe outro círculo com 31,75 mm de diâmetro e extrusão de 20 mm.
Em seguida, esboce no plano frontal um círculo com diâmetro de 100 mm e extrude 12,70 mm.
No topo da parte que acabamos de extrudar, desenhe um triângulo equilátero com lados de 30 mm. Extrude o triângulo de 12,70 mm.
Assim que a extrusão for concluída, use o recurso de padrão circular para ter 20 triângulos uniformes ao redor da peça. Em seguida, faça o fillet de todas as arestas dos triângulos.
No plano frontal, esboce outro círculo com diâmetro de 100 mm e extrude-o 13,97 mm.
Para criar o furo no meio da engrenagem, esboce um círculo no plano traseiro com o diâmetro de 27,94 mm e corte a extrusão até a superfície.
Etapa 7: Criar Pawl no SolidWorks
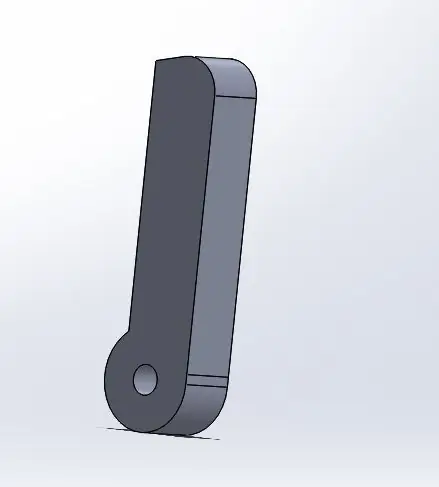
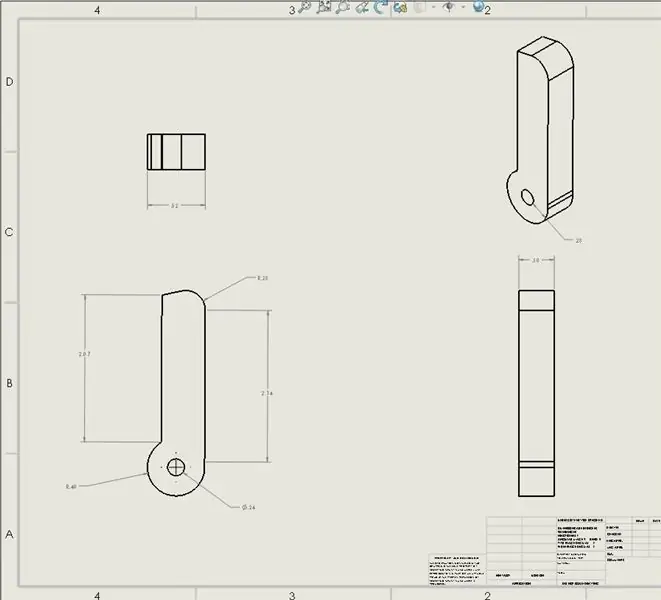
No plano frontal, desenhe uma linha vertical com comprimento de 2,07 polegadas. Depois, desenhe um arco com raio de 0,40 polegadas conectando-se com a parte inferior da linha vertical. Além disso, desenhe uma linha horizontal conectada com a borda superior da linha vertical. Usando as dimensões inteligentes, clique na aresta superior e na linha vertical e defina o ângulo como 78,00 graus.
Depois que o ângulo for definido, desenhe outra linha vertical que se conecte com a linha inclinada com um comprimento de 2,14 polegadas. Em seguida, faça o fillet da aresta dessa linha com a linha horizontal com um raio de 0,28 polegadas.
Quando o esboço estiver concluído, faça a extrusão da saliência usando uma extrusão cega de 0,5 polegadas. Para criar o furo no meio, esboce um círculo com um raio de 0,12 polegadas no centro da peça e use a extrusão de corte por toda parte.
Etapa 8: Criar botão de direção no SolidWorks
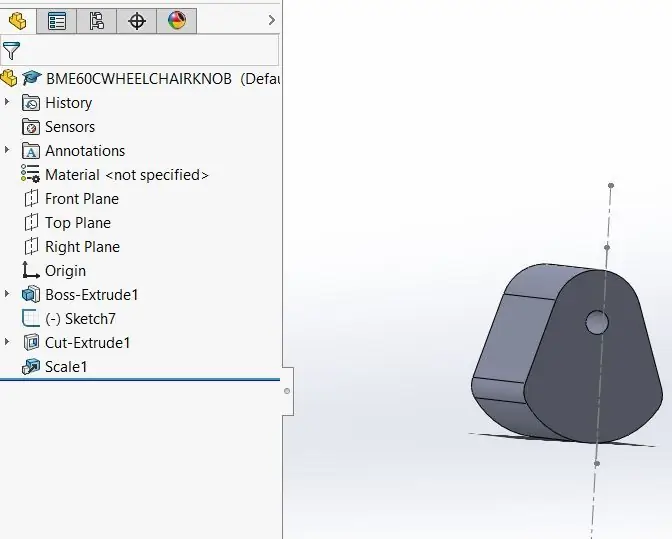
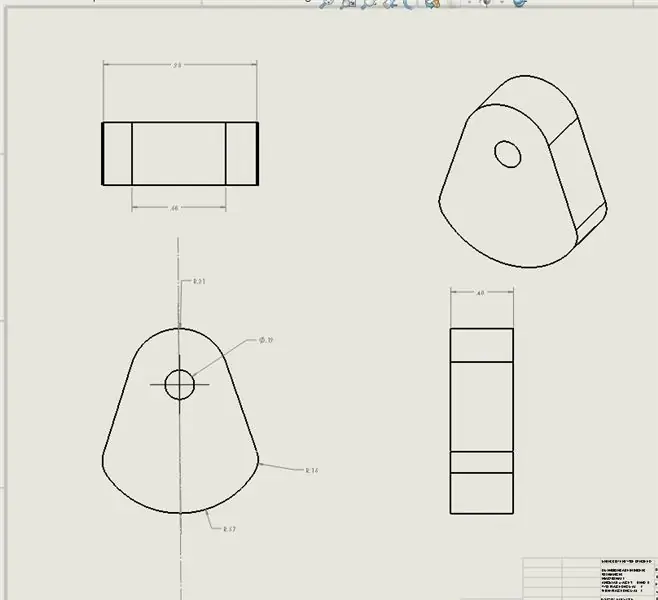
No plano frontal, esboce uma linha central vertical. Então, no topo da linha central, esboce um arco com um raio de 10 mm. Em seguida, em ambos os lados desenhe linhas inclinadas com o comprimento de 18,26 mm. Em seguida, desenhe um arco em ambos os lados com raio de 5 mm. Para conectar os dois lados, desenhe outro arco com raio de 18 mm. Extrude o esboço usando extrusão cega de 12,70 mm.
Para criar um furo, esboce um círculo com 5,90 mm de diâmetro e com o centro a 8 mm de distância da origem. Use extrusão de corte até a superfície.
Dimensione a parte sobre o centróide com fator de escala de 0,8 mm.
Etapa 9: Crie o suporte de tubo
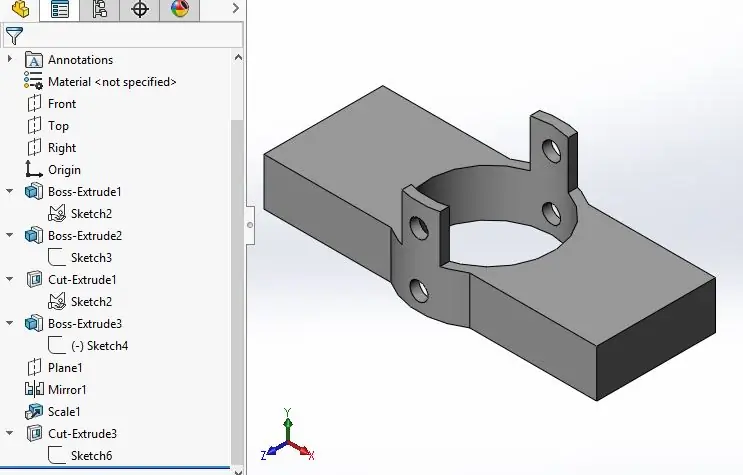
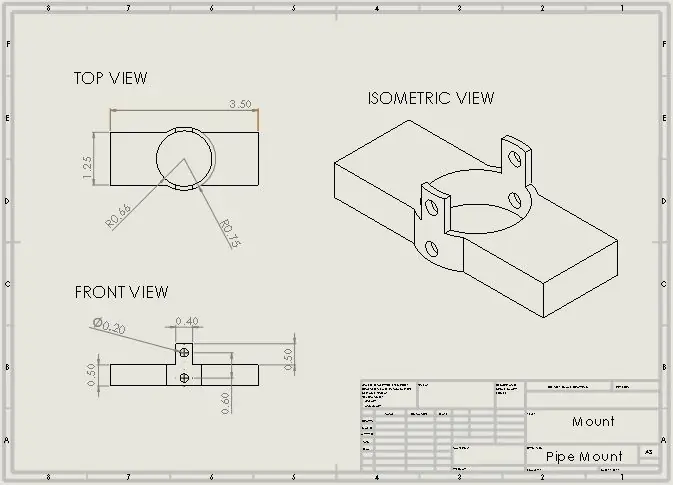
Para criar o suporte do tubo que fixará o braço da alavanca ao corpo da engrenagem, comece com um esboço de dois círculos. O círculo interno deve ter o diâmetro do tubo de PVC para que possa deslizar facilmente em torno dele, portanto, deve ter 1,3125 polegadas. O círculo externo deve ter cerca de 1,5 polegadas. Certifique-se de que os dois círculos são concêntricos e extrude a parte entre os dois círculos em 0,5 polegadas. Em seguida, esboce um retângulo que corresponda à face inferior do revestimento externo da engrenagem. Este seria um retângulo de 3,5 polegadas por 1,25 polegadas. Centralize este retângulo ao redor do círculo definindo a borda longa do retângulo a 1,75 polegadas de distância do centro do círculo e a borda curta do retângulo a 0,63 polegadas de distância do centro do círculo. Extrude o retângulo em 0,5 polegadas. Como algumas partes do retângulo ficam dentro do círculo interno, corte extrude o círculo interno para eliminá-lo. A seguir, a partir do plano superior da peça, esboce uma linha central do círculo até a parte externa da aresta extrudada. A partir deste ponto central na aresta extrudada, esboce um retângulo que vai de 0,2 polegada para ambos os lados. Extrude este pequeno retângulo em 0,5 polegadas. Crie um plano de referência voltado para a frente através do centro da peça e use a função de espelho para criar um retângulo extrudado idêntico no outro lado do círculo.
Ao imprimir peças em 3D, é sempre uma boa ideia dimensionar tudo ligeiramente para cima para evitar interferência ao colocar a peça na montagem. Nesse caso, toda a parte foi aumentada em 1,05. Por fim, esboce dois círculos de 1/4 de polegada de diâmetro definidos para ficarem na face frontal do centro da peça, um no retângulo pequeno e outro na lateral do círculo. Certificando-se de que os dois círculos estão relacionados verticalmente, eles podem ser cortados em toda a parte, cortando quatro círculos no total. Esses seriam orifícios nos quais os parafusos podem ser colocados para conectar o PVC ao corpo principal da caixa de engrenagens.
Etapa 10: Comece a montagem no SolidWorks
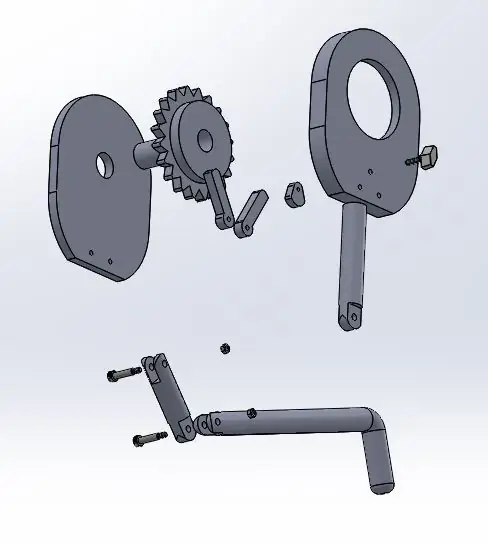
Primeiro, insira todas as peças que foram criadas nas etapas anteriores junto com o botão externo, parafusos e porcas, tornando o corpo da cadeira de rodas o componente básico.
Comece combinando o corpo e a engrenagem clicando na borda da engrenagem e na borda do corpo e use um mate concêntrico. Em seguida, clique na face da engrenagem e no corpo para criar um posicionamento coincidente.
Em seguida, posicione o corpo e o botão de direção clicando na face do botão de direção e no corpo para fazer um posicionamento coincidente.
Agora, posicione o botão externo e o corpo da cadeira de rodas clicando na face do botão externo e no corpo para criar um posicionamento coincidente.
Crie um mate concêntrico clicando na face do corpo e na face do botão externo.
Em seguida, faça um posicionamento concêntrico clicando na face do botão de direção e na aresta do corpo.
Agora clique nas faces do corpo e na lingueta para criar um posicionamento coincidente e repita para a outra lingueta.
Crie o mate tangente clicando na face do botão de direção e na lingüeta e repita para a outra lingüeta.
Em seguida, crie um mate coincidente clicando na face do corpo e na caixa externa e faça um mate concêntrico clicando na face do corpo e na aresta da caixa externa. Em seguida, faça com que a face do corpo e a face da caixa externa sejam paralelas.
Crie um ângulo limite que tenha um valor máximo de 78 graus e um valor mínimo de 35 graus para a face do corpo e a face da lingueta e repita para a outra lingueta
Depois, mate a junta e o corpo clicando na face de ambos para criar um mate concêntrico. Em seguida, crie um posicionamento de largura centralizado para ambas as faces da junta e do corpo.
Em seguida, crie um posicionamento concêntrico para a aresta do braço de alavanca e a aresta da junta. Crie outro posicionamento de largura centralizado para ambas as faces da junta e do braço de alavanca.
Faça outro posicionamento concêntrico para a face da junta e o parafuso. Em seguida, crie um posicionamento tangente clicando na face da junta e na face do parafuso.
No plano direito, esboce duas linhas de eixo para futura referência de acoplamento, sendo a primeira linha onde o corpo encontra a junta e a segunda onde a junta encontra o braço de alavanca.
Em seguida, crie um posicionamento concêntrico clicando na face do braço de alavanca e no segundo parafuso. Uma vez acoplado, crie outro mate tangente com ambas as faces de ambos os componentes.
Com o primeiro eixo desenhado anteriormente, mate a aresta da primeira porca e o eixo para criar um mate concêntrico.
Use um posicionamento coincidente para a face do primeiro parafuso e da primeira porca e repita para o segundo parafuso e porca.
Faça um mate concêntrico com a aresta da segunda porca e do segundo eixo.
Crie outro posicionamento concêntrico com a face do corpo e a face externa do primeiro parafuso. Além disso, faça um posicionamento coincidente para essas peças.
Faça um mate concêntrico para a face da lingueta e a face externa do terceiro parafuso.
Crie o posicionamento coincidente com a face do corpo e a face externa do terceiro parafuso.
Em seguida, crie outro posicionamento concêntrico clicando na face da caixa externa e na face externa do terceiro parafuso e torne-as coincidentes.
Faça um mate concêntrico clicando na face do corpo e na face da lingueta e torne-as coincidentes. Repita para a outra lingüeta.
Faça um posicionamento concêntrico clicando na face do botão de direção e no botão externo.
Por último, posicione a face do corpo e a aresta do botão de direção para criar um posicionamento concêntrico.
Etapa 11: Solicite peças da McMaster-Carr
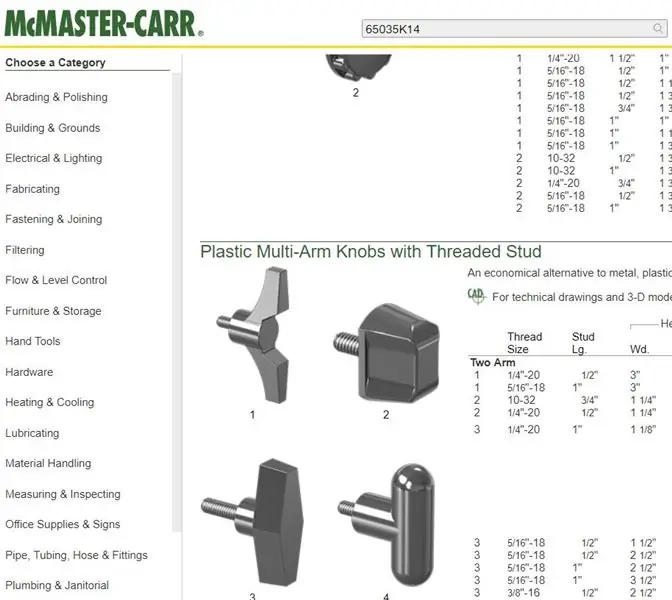
Encomende o botão de plástico de dois braços (botão externo), parafuso de ombro de aço de liga, porcas sextavadas de aço e abraçadeiras de cabo da McMaster-Carr. Os números dos itens são 65035K14, 92981A205, 90592A016 e 70215K61, respectivamente.
Etapa 12: Obtenha as peças na loja de ferragens
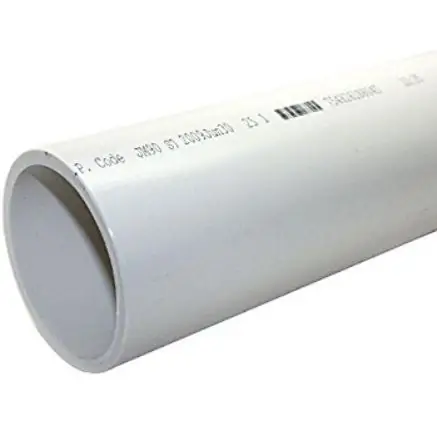
Em uma loja de ferragens local, obtenha o seguinte:
- Folha de acrílico 18 "x 24" x 0,220"
- Adesivo transparente (adesivo E6000)
- Tampa de soquete de PVC de 1 (2)
- Tubo de ponta plana de PVC de 1 x 10 '
- 1 cotovelo de PVC de 90 graus (2)
Etapa 13: fabricando as peças
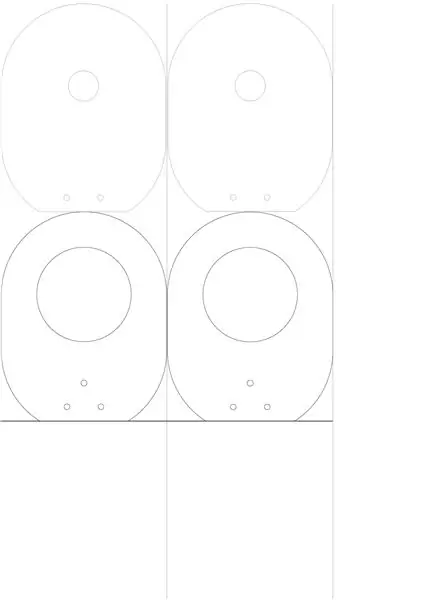
Peças impressas em 3D: prepare as peças do SolidWorks e as converta em arquivos STL. A partir daí, coloque as peças no software Makerware e faça o layout das peças que precisam ser impressas (carcaça do corpo, engrenagens, peça de montagem, linguetas, botão de direção, travas de apoio de braço *). Se as peças não couberem na base da impressora, espere para reimprimir novamente. Ao imprimir, certifique-se de adicionar suportes e balsas para evitar que as impressões falhem.
Peças cortadas a laser: Usando acrílico de 18 "por 24", as placas frontal e posterior do revestimento externo do corpo podem ser fabricadas. Isso pode ser feito pegando a face frontal de ambas as placas no SolidWorks e salvando-as como um arquivo DWG. Eles podem então ser carregados para o software de corte a laser (neste caso, Epilog), no qual sua orientação pode ser configurada conforme mostrado pela imagem. Dois de cada serão recortados do acrílico e, do material restante, dois retângulos serão recortados. Os retângulos servirão como apoios de braços.
Peças cortadas à mão: Pegue os tubos e corte-os em comprimentos diferentes (dois de 4,5 polegadas para o cabo, dois de 4,5 polegadas para a junta, dois de 6,5 polegadas para a alavanca e dois de 13,25 polegadas para o braço). A partir daí, corte as peças do braço de 13,25 polegadas em uma extremidade (30 ou 35 mm) no meio do outro lado do tubo e faça um orifício de 1/4 a 15 mm das bordas do tubo. Corte e perfure dois dos Peças de junta de 4,5 polegadas da mesma maneira, mas em ambos os lados do tubo de PVC de junta. Faça o mesmo (corte e fure) em um lado do braço de alavanca, tubo de 6,5 polegadas.
* Recuos de apoio de braço ou todo o apoio de braço na etapa anterior podem ser usados.
Etapa 14: Junte todas as peças
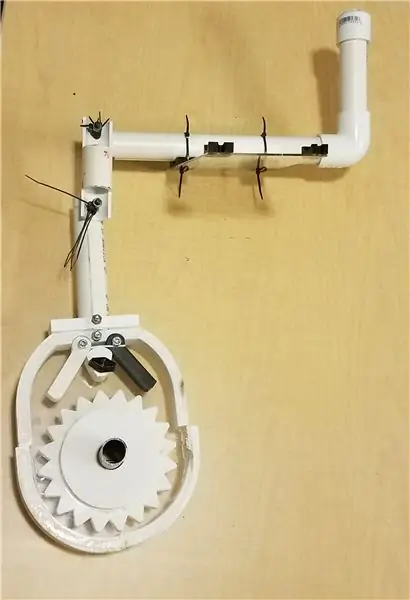
Montagem do corpo:
Pegue as peças externas do corpo cortadas a laser e as peças de concha impressas em 3D. Pegue um lado do invólucro externo e cole as peças da concha de acordo com as bordas do invólucro. Depois, pegue um elástico e enrole nas duas linguetas. Coloque as linguetas em seus respectivos locais e use o parafuso parcialmente roscado e coloque-o através do orifício do corpo e das linguetas. Depois, pegue o botão de direção e o botão de plástico. Coloque o botão de plástico através do revestimento externo e gire os dois juntos com o revestimento externo entre os dois. Por fim, coloque a engrenagem em seu respectivo orifício e coloque a tampa superior do revestimento externo na engrenagem e cole a carcaça no revestimento externo superior. Deixe descansar e secar. Lembre-se de prender também os dois parafusos parcialmente roscados com as porcas sextavadas após colocar e colar a tampa superior na carcaça.
Pegue o tubo de PVC com alavanca de 6,5 polegadas e cole-o na parte inferior do corpo. A partir daí, deixe descansar e secar. Pegue a peça montada e deslize-a pelo tubo até que ela fique plana na face inferior do corpo. Pegue uma broca de 1/4 de polegada e faça os furos no tubo e através do corpo em seus respectivos lugares. Prenda os parafusos com uma porca sextavada.
Montagem do descanso de braço:
Com o apoio de braço, basta colocar e colar os entalhes nos 4 cantos do apoio de braço. Em seguida, faça dois furos (furos de 5/32 '') em cada lado dos entalhes e coloque laços de zíper através deles. Os recortes maiores podem então ser alinhados e ziptied para o tubo de PVC de 13 polegadas do braço da alavanca. O recorte menor deve ser alinhado e posteriormente preso ao braço da cadeira de rodas antes do uso.
Montagem do braço de alavanca:
Coloque a tampa no tubo de alça de 4,5 polegadas e coloque o cotovelo com segurança do outro lado. Com a outra abertura do cotovelo, coloque o tubo do braço de 13 polegadas e conecte-o a um lado da junta (tubo de 4,5 polegadas) com um parafuso de ressalto. No outro lado da junta, pegue outro parafuso de ombro e junte-o à peça do braço da alavanca (tubo de 6,5 polegadas). Pegue uma porca sextavada e prenda o parafuso de ressalto. Como os parafusos de ombro são parcialmente rosqueados, as juntas nas quais eles são fixados podem ser frágeis. Para tornar as juntas mais firmes e seguras, coloque cerca de cinco fechos em volta de cada parafuso de ombro para apertar cada junta.
Etapa 15: Teste Iterativo
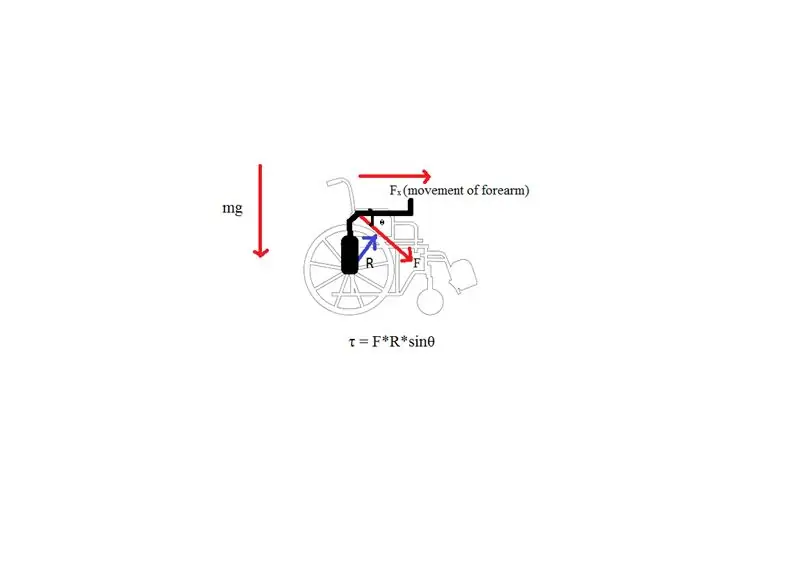
Para testar, certifique-se de obter acesso a uma das cadeiras de rodas.
Prenda o braço da alavanca ao volante. Certifique-se de que as peças se encaixem onde devem ir e certifique-se de que certas partes estão paralelas às respectivas partes da cadeira de rodas, como o apoio de braço. Certifique-se de que os orifícios feitos no tubo de alumínio e no corpo do braço da alavanca estejam alinhados. Se as partes forem desproporcionais, volte e faça algumas alterações de dimensão.
Assim que as dimensões e relações estiverem corretas, peça a um testador que se sente na cadeira de rodas e use o braço de alavanca. Conforme mostrado no diagrama de corpo livre, o testador irá empurrar para frente horizontalmente para criar uma força diagonal que seria usada para criar um torque e impulsionar a cadeira de rodas para frente. Analise quaisquer problemas: fragilidade da junta, excesso ou falta de espaço horizontal, quebra de peças etc.
Analise os problemas e redesenhe novamente.
Em nosso protótipo, a cadeira de rodas se movia, mas em um ritmo lento. A parte do corpo não terminou de colar a tempo, então o braço da alavanca quebrou durante nosso teste. Além disso, a junta pode ter sido muito grande e frouxa e pode não ter havido uma quantidade suficiente de espaço horizontal e movimento no braço de alavanca, ambos restringindo a quantidade de força exercida por impulso.
Etapa 16: Página de contribuições
Contribuições individuais para sistema de apoio
Gerente de Projeto: Sophia Ynami 12732132
- A gerente de projeto, Sophia Ynami, era responsável por garantir que cada membro do grupo fosse responsabilizado por suas respectivas funções e que todas as tarefas fossem concluídas em tempo hábil. Eu ajudei no processo de montagem final, bem como testei e fiz ajustes no dispositivo antes da execução final.
Fabricante: Yvonne Szeto 94326050
- O fabricante, Yvonne Szeto, foi responsável por preparar os diferentes componentes para a montagem. Fui responsável por obter as matérias-primas cortadas a laser, perfuradas e imprimindo peças diferentes em 3D. Também montei os diferentes componentes juntos.
Engenheiro de Materiais: Willis Lao 15649487
- O engenheiro de materiais, Willis Lao, foi responsável por decidir quais materiais usar para cada componente do projeto e solicitá-los / buscá-los na McMaster Carr / Home Depot. Também contribuí com os Instructables escrevendo a introdução, a análise de custos, o processo passo a passo de criação das peças e a montagem.
Testador: Matthew Maravilla 25352925
- O testador, Matthew Maravilla, foi responsável por supervisionar e analisar o método de teste iterativo, incluindo o teste do braço de alavanca e a dimensão do relatório ou alterações de peça a serem ajustadas. Também fui responsável pelo esboço e pela maioria dos Instructables.
Designer Principal: Anthony Cheuk 30511803
- O designer principal, Anthony Cheuk, foi o responsável por criar um design viável levando em consideração os diferentes materiais que poderiam ser usados e preparando os arquivos e o design para a fabricação (impressão 3D e corte a laser).
Recomendado:
Cadeira de rodas baseada em acelerômetro para pessoa com deficiência física: 13 etapas
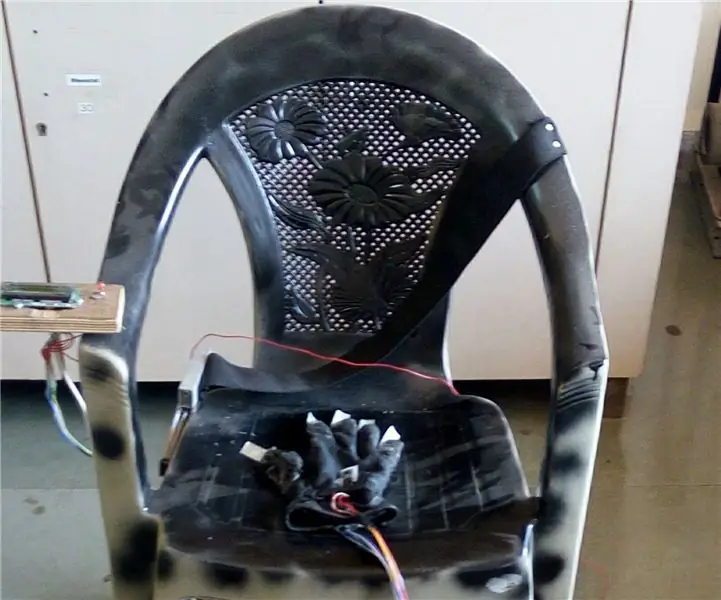
Cadeira de rodas baseada em acelerômetro para pessoas com deficiência física: Em nosso país de 1,3 bilhão de habitantes, ainda temos mais de 1% da população idosa ou com deficiência, que precisa de suporte para a mobilidade pessoal. Nosso projeto tem como objetivo atender aos seus requisitos de mobilidade com tecnologia inteligente. O problema
Cadeira de rodas para cães: 4 etapas
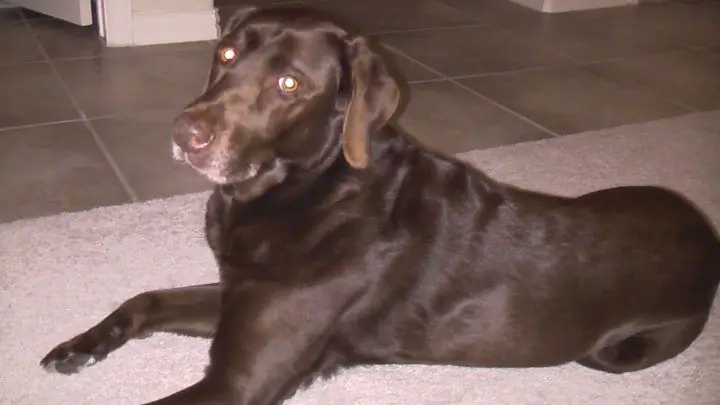
Cadeira de rodas para cães: Olá, hoje vou mostrar-lhes como fazer uma cadeira de rodas para cães para o seu cão. Tive essa ideia pesquisando na internet para ver como as pessoas podem curtir mais os cães mais velhos. Eu realmente não precisava de um porque meu cachorro tem 2 anos, mas o cachorro da minha tia, que tem 8
D4E1 - DIY - Tecnologia Assistiva: Bandeja ajustável para cadeira de rodas: 7 etapas (com fotos)
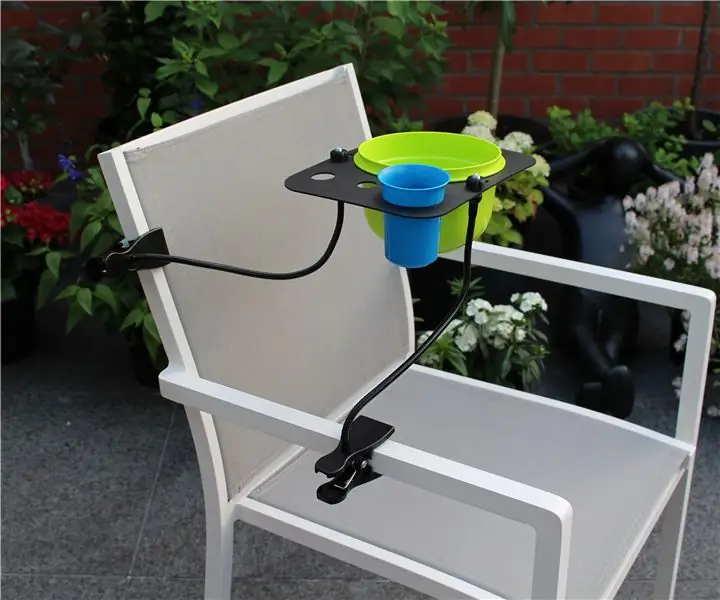
D4E1 - DIY - Tecnologia Assistiva: Bandeja ajustável para cadeira de rodas: Kjell tem uma deficiência congênita: quadriparesia discinética e não consegue comer sozinho. Ele precisa da ajuda de um monitor, um terapeuta ocupacional, que o alimenta. Isso traz dois problemas: 1) O terapeuta ocupacional fica atrás do volante
Auxiliar de crochê para cadeira de rodas: 18 etapas
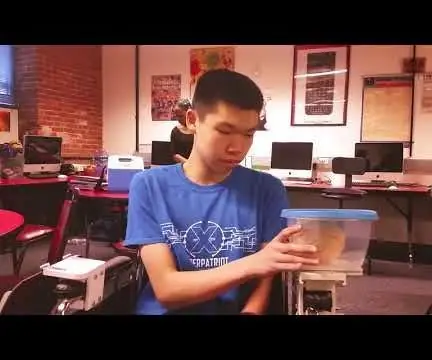
Auxiliar de Crochê para Cadeira de Rodas: Um indivíduo com lesão cerebral adquirida que não usa uma das mãos tem dificuldade para segurar o fio para fazer tricô e crochê. Ela também tem dificuldade de distribuir o fio sem enredá-lo na cadeira de rodas. Tricotar é um
Câmera retrovisora para cadeira de rodas elétrica: 10 etapas (com fotos)
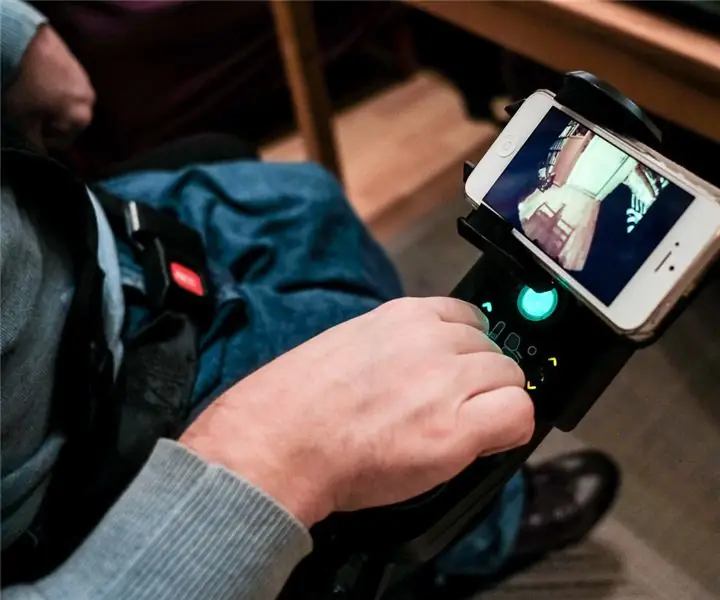
Câmera de visão traseira para uma cadeira de rodas elétrica: Meu irmão usa uma cadeira de rodas elétrica Invacare TDX, que é fácil de manobrar em todas as direções, mas devido à visibilidade limitada para trás, é difícil dirigir para trás em espaços limitados. O objetivo do projeto é construir uma câmera retrovisora