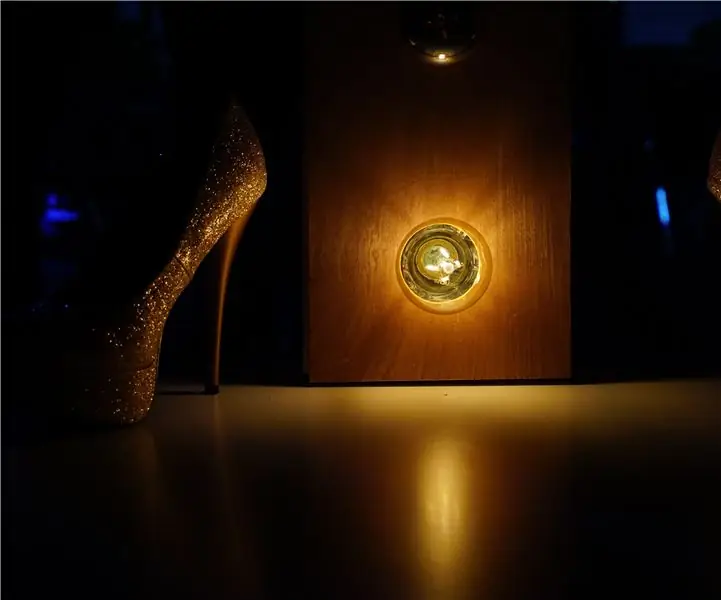
Índice:
- Suprimentos
- Etapa 1: Circuito 5V: Arduino
- Etapa 2: projetando a caixa
- Etapa 3: construindo a caixa
- Etapa 4: Instalando os soquetes na caixa
- Etapa 5: soldando os eletrônicos de baixa tensão
- Etapa 6: Conectando os componentes de 220 V
- Etapa 7: Snappers magnéticos (opcional)
- Etapa 8: O que eu faria de maneira diferente
2025 Autor: John Day | [email protected]. Última modificação: 2025-01-23 15:03
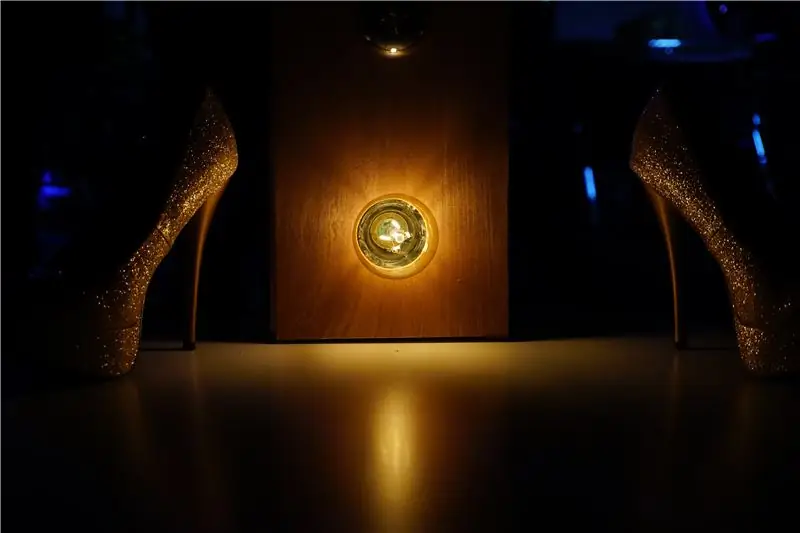
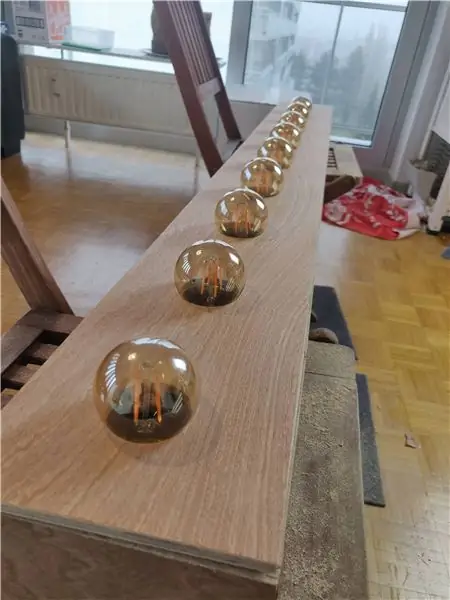
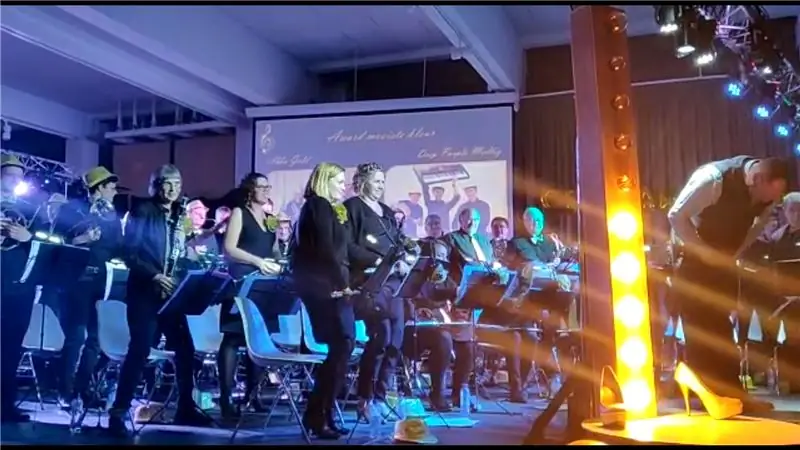
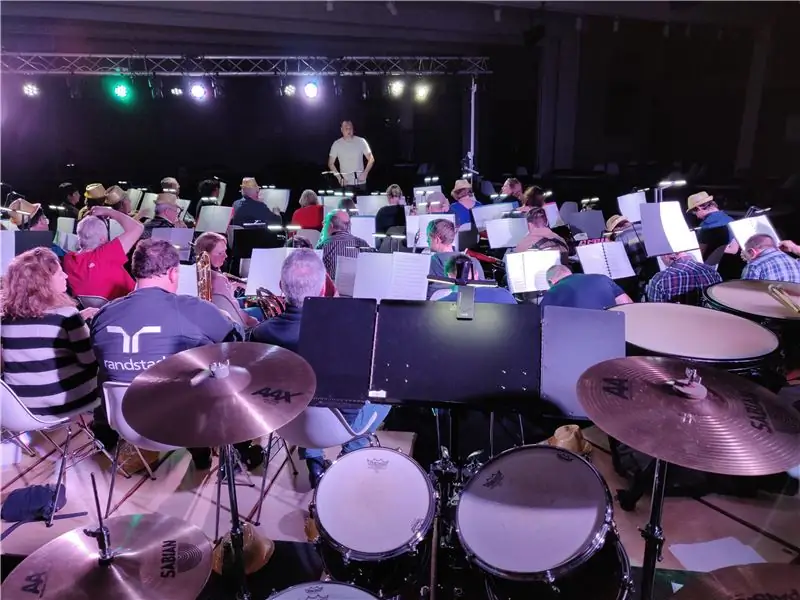
Por volta do ano de 2001 comecei a ter aulas de bateria. Depois de dez anos, em 2011, entrei na minha primeira banda de concertos e fiquei viciado. Fazer música juntos e tocar em um show é emocionante. Agora estou em uma banda de concerto diferente há mais de 5 anos. Temos dois shows por ano e várias comissões paralelas.
Como tema do nosso show de ano novo, queríamos realizar uma cerimônia de premiação para as melhores músicas que tocamos. A configuração foi que tocamos duas músicas em cada categoria. Por exemplo, "Gelo contra fogo", para o qual jogamos um medley de "Frozen" e um de "Como treinar seu dragão". O público deveria então votar na melhor música, que então receberia um prêmio impresso em 3D personalizado.
Durante o brainstorming durante os preparativos, tivemos muitas ideias sobre como fazer o público votar, de votos em papel a aplicativos. Mas todas essas sugestões exigem que o show seja interrompido para cada prêmio, distraindo seriamente o público. Quando um medidor de aplausos foi sugerido, todos nós sabíamos que atingimos o ouro. Mas algumas pesquisas online não revelaram nenhuma solução pronta para usar. Então, eu corajosamente me levantei, me declarei um fabricante novato e aleguei que poderia facilmente construir um do zero com um orçamento bastante pequeno.
Oh, cara, eu estava despreparado para a toca do coelho em que iria cair.
Suprimentos
Ferramentas
- Sua furadeira sem fio favorita
- Broca circular e outras brocas
- chaves de fenda
- Impressora 3D (opcional)
Caso
- Madeira compensada. (Eu escolho multiplex de 8 mm, mas olhando para trás, eu deveria ter optado por 12 mm ou até mais grosso)
- 4 X trava magnética da porta (opcional em retrospectiva)
- Parafusos
Eletrônica (5V)
- Arduino Nano
- Amplificador de microfone de eletreto - MAX4466 com ganho ajustável (ou semelhante, o que for adequado às suas necessidades)
- Módulo de relé de 8 canais 2 X 5V
- Transformador 220V para 5V
- fios, muitos curtos e um fio de quatro fios de vários metros para o controle 'remoto'
- dois interruptores
Eletrônica (220V)
- cabos elétricos padrão (sobras da construção da casa são ideais, mas são mais flexíveis)
- Soquete de alimentação CA com fusível (opcional, mas altamente recomendado)
- Lâmpadas à sua escolha
- Soquetes de lâmpada
Etapa 1: Circuito 5V: Arduino
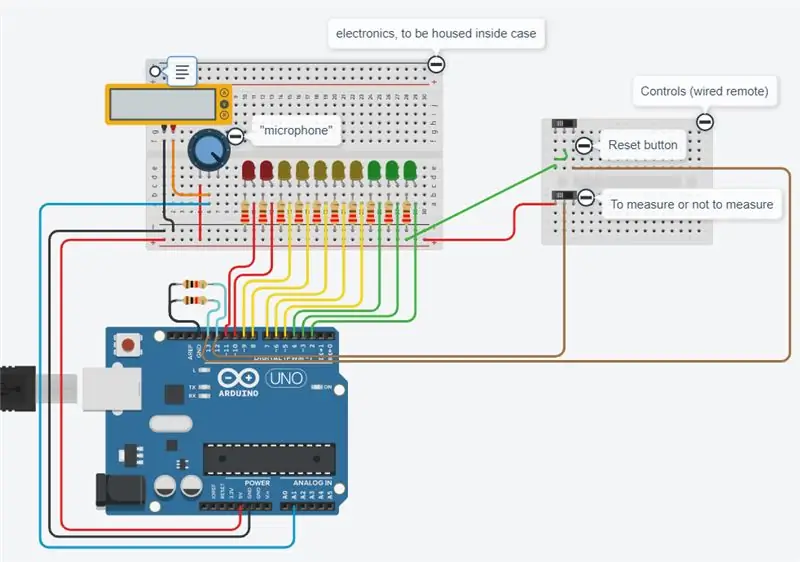
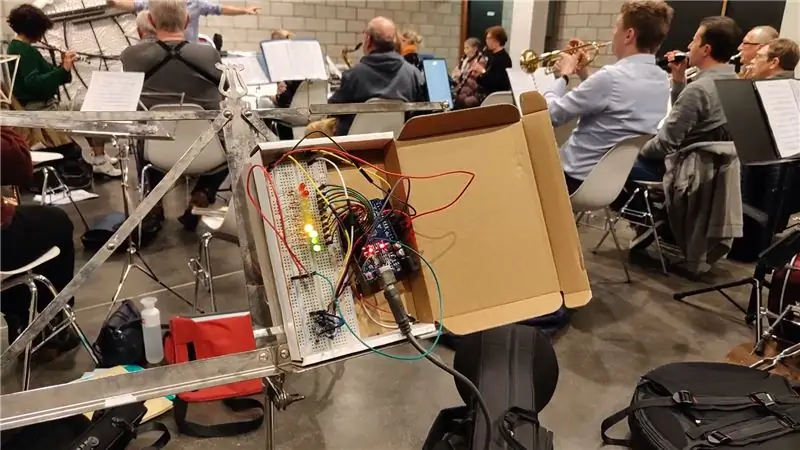
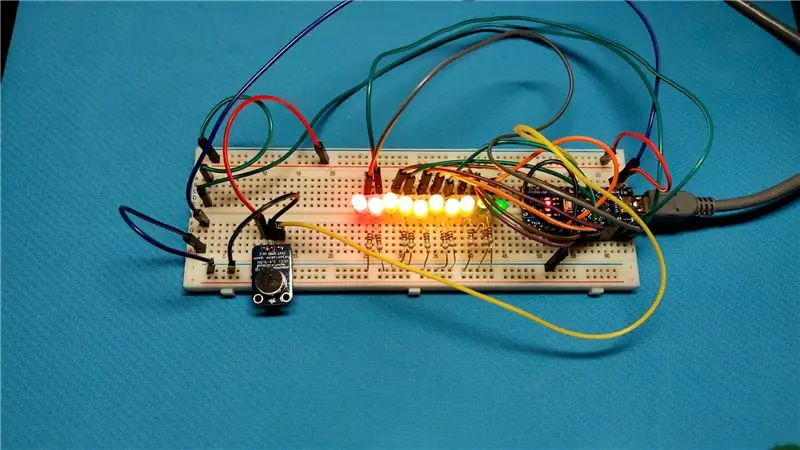
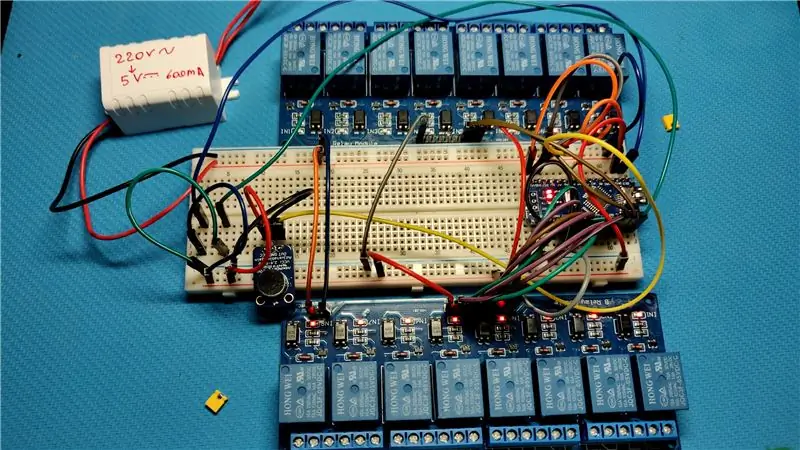
Existem três partes principais para esta construção: (1) a eletrônica de 5 V que fará o "pensamento difícil": ouvir e decidir quando e quais luzes acender; (2) o invólucro para encaixar tudo perfeitamente, esconde todos os 'crimes', e (3) o circuito de 220V que é controlado pelo circuito de 5V.
Vamos começar com o circuito de 5V, pois podemos construí-lo em pequena escala.
Não foi uma tarefa fácil encontrar recursos online. Eu imaginei dez luzes, que se acenderam de acordo com o volume dos aplausos, mas ninguém parecia ter feito isso antes. Então, comecei pequeno; No tinkerCAD, construo uma simulação online de como gostaria que as peças eletrônicas de 5V fossem. Você pode encontrar meu design muito rudimentar com código aqui: https://www.tinkercad.com/things/8mnCXXKIs9M ou abaixo nesta página como arquivo "Aplausos_1.0.ino".
Fazer uma versão de rascunho online e testar vários códigos do Arduino nesta simulação realmente me ajudou a obter uma visão melhor do que era necessário para esta construção. Desta forma, experimentei adicionar uma forma de controlar o comportamento do programa: acabei com dois interruptores. Um interruptor liga e desliga a medição, o outro redefine a pontuação de volta para 0/10.
Eu consegui todos os componentes necessários: alguns LEDs, resistores, um Arduino e, o mais importante, um microfone compatível com o Arduino.
Construí o circuito e testei tudo no ensaio seguinte, apenas para perceber que o microfone que comprei era sensível demais para meu uso. Apenas uma batida em uma proximidade razoável, ou apenas a banda tocando, saturaria o microfone dando uma pontuação de 10/10. Isso me levou a procurar um microfone com ganho variável. Eu finalmente decidi pelo amplificador de microfone Electret - MAX4466. Ele tem um parafuso muito pequeno na parte traseira com o qual você pode definir o ganho. (observação: eu também troquei o Arduino uno por um Arduino Nano sem nenhum motivo específico).
O MAX4466 teve um desempenho melhor, mas também atingiu o máximo ao bater palmas nas proximidades, portanto, decidi também incluir o tempo das palmas como uma variável para a fórmula, em vez de apenas o volume dos aplausos. Também escrevi um pouco mais de um código elegante para esta versão 2.0 do software (mesmo que eu mesmo diga). Se um limite de volume fosse excedido, apenas a primeira luz acenderia, seguida por uma breve pausa durante a qual nenhuma luz poderia acender. Depois de esperar, o Arduino ouviria se o som ainda estava alto o suficiente para a segunda luz acender; nesse caso, a luz acende e o próximo período de espera é acionado. O tempo de espera aumentaria cada vez que uma nova luz acendesse. Um aplauso precisaria durar 22,5 segundos no volume máximo para que as luzes mostrassem 10/10. Você pode encontrar o código em tinkerCAD https://www.tinkercad.com/things/lKgWlueZDE3 ou abaixo como arquivo "Aplausos_2.0.ino"
Um teste rápido com os módulos de relé conectados em vez dos LEDs me ensinou que os relés estavam LIGADOS quando o sinal estava BAIXO e DESLIGADOS quando o sinal estava ALTO. Não há problema, apenas desligando alguns ATIVADOS e DESATIVADOS no código e estávamos prontos para começar.
Com tudo isso resolvido. Eu poderia começar a soldar tudo junto. Mas eu precisava saber quanto tempo todas as conexões dentro da caixa deveriam ter. Portanto, vamos primeiro construir a caixa externa e organizar todos os componentes nela.
Etapa 2: projetando a caixa
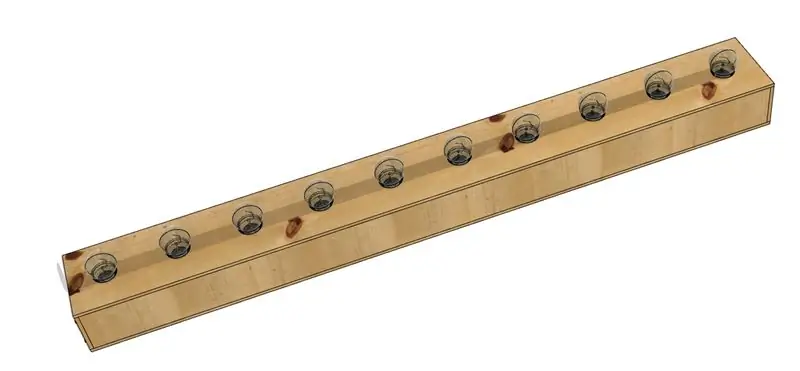
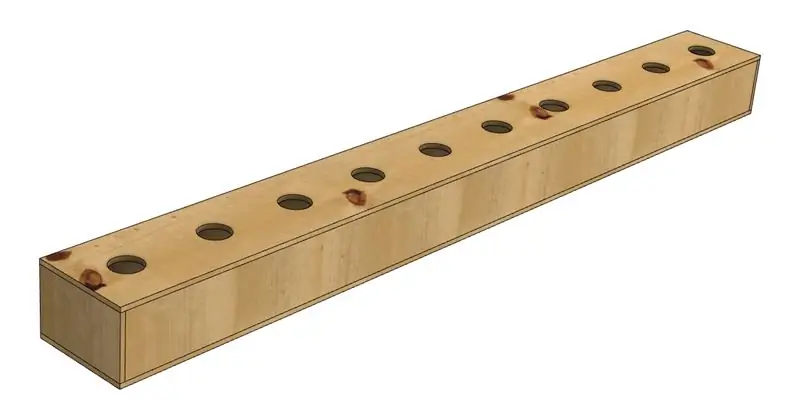
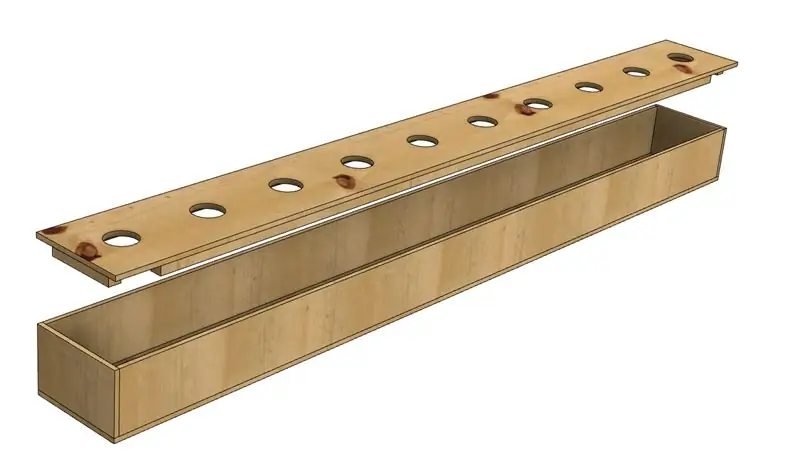
Um segundo aspecto dessa construção foi sua estética. O medidor de aplausos estaria no meio das atenções, então deveria pelo menos ter uma boa aparência. Optei por construir uma caixa de madeira porque tenho as ferramentas básicas para isso e é relativamente fácil.
Tendo aprendido no tinkerCAD que fazer experiências no mundo digital é altamente educacional, eu também projetei a caixa do medidor de aplausos no popular programa de CAD 3D Fusion360 antes de comprar qualquer um dos materiais necessários.
Ao longo de várias iterações, finalmente me decidi por este projeto (veja as fotos). É uma caixa retangular simples com as luzes saindo de orifícios circulares no painel frontal.
Parafusos feios no painel frontal foram evitados adicionando algumas barras de suporte no interior do painel frontal, onde mais tarde os encaixes magnéticos das portas seriam aparafusados. O sistema de fechamento magnético é, em retrospectiva, mais um recurso de segurança do que realmente necessário, já que as barras seguravam a placa frontal apenas por atrito.
Eu também adicionei a parte eletrônica ao meu design digital. Isso mudou algumas coisas, então já estava valendo a pena eu tê-lo projetado pela primeira vez no Fusion360. Por exemplo, a caixa precisava ser um pouco mais larga do que os 15 cm iniciais para que os relés se encaixassem nas laterais. Também acabei modelando e imprimindo em 3D suportes de plástico para as tomadas de luz que, por sua vez, manteriam as luzes no lugar. Essa me parecia ser a opção que me daria 'espaço de manobra' suficiente para erros futuros. (Eu sei que esses suportes também podem ser comprados como tal, mas isso me custou três vezes mais e eu estava dentro do orçamento)
Eu adicionei o arquivo F360 do meu design final aqui para você consultar e brincar com ele.
Etapa 3: construindo a caixa
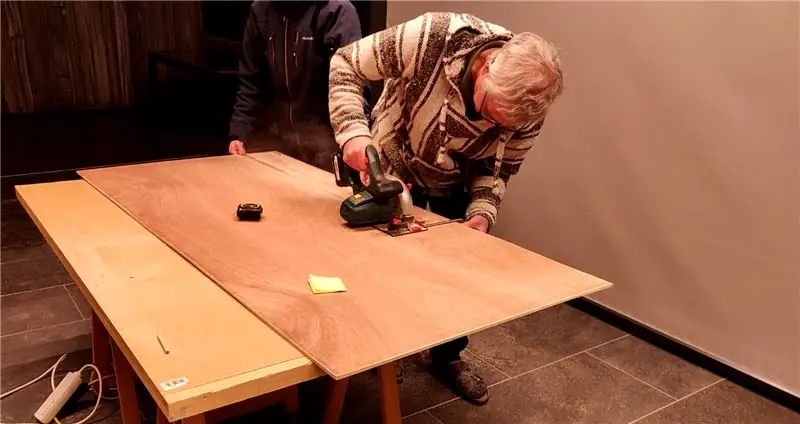
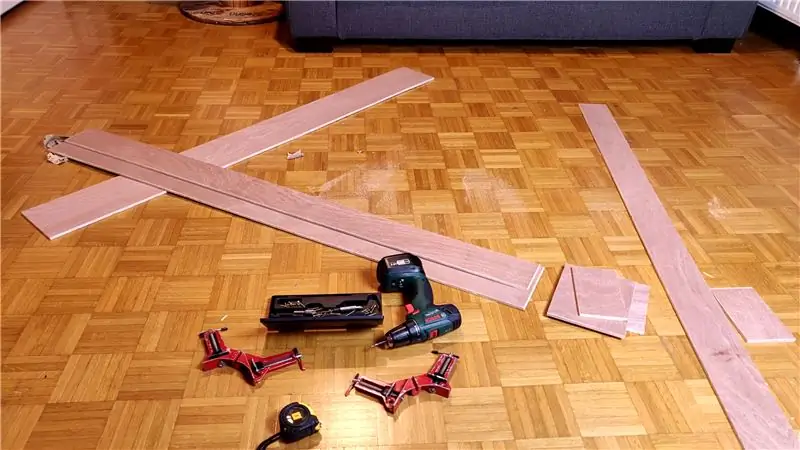
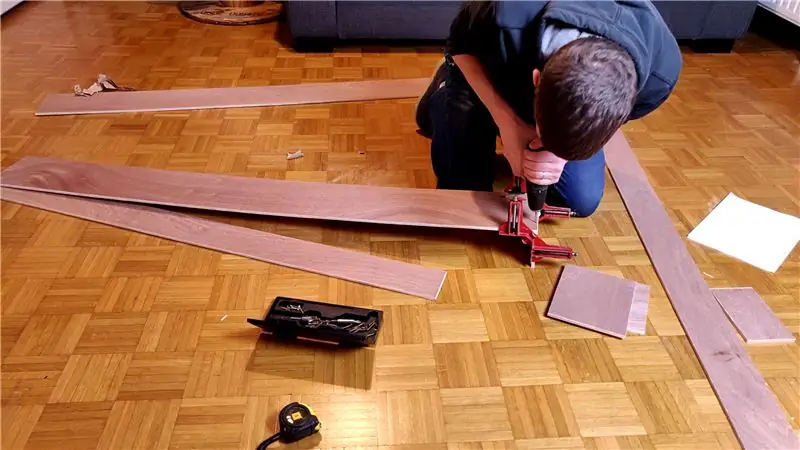
Com o desenho digital finalizado, era hora de ir à loja de ferragens, comprar uma grande folha de compensado e começar a cortar. Como eu realmente não tinha essas ferramentas 'chiques', fui à casa dos meus pais num fim de semana e cortei a madeira lá.
Meu projeto, entretanto, acabou produzindo uma folha cortada bastante exótica:
- 2 vezes 16,6x150cm para a frente e para trás
- 2 vezes 16,6x10,2cm para a parte superior e inferior
- 2 vezes 10,2x148,4cm para os lados
As barras de suporte no interior do painel frontal eram sobras e foram usadas como tal, caso contrário, o comprimento preferido seria de 134 cm e 12 cm.
Uma vez em casa, coloquei todas as peças no chão e com a ajuda de alguns grampos de canto (emprestados), comecei a pré-fazer os furos e a aparafusar as tábuas. Lembre-se de que os parafusos só vão na parte superior, inferior e posterior do medidor para puras reações estéticas.
Furar os furos e aparafusar todas as placas era uma tarefa precária devido ao compensado ter apenas 8 mm de espessura, muitas vezes me amaldiçoava por pensar que 8 mm seria grosso o suficiente.
O painel frontal precisava de alguns orifícios cuidadosamente espaçados de cerca de 5 cm de diâmetro. Marquei a linha central do painel frontal e comecei de um lado. O centro do primeiro furo era de 8 mm (a espessura do material) + 75 mm (metade de 150 mm) da borda da placa. Todos os outros orifícios estão separados por 150 mm. No final estava apenas 2mm errado quando marquei o décimo buraco… foi um bom dia!
A única broca circular que eu poderia pegar emprestada era 51 mm, mais do que perto o suficiente para eu começar a perfurar com alegria.
As guias da placa frontal foram coladas na parte interna da placa frontal com cola de madeira simples.
Etapa 4: Instalando os soquetes na caixa
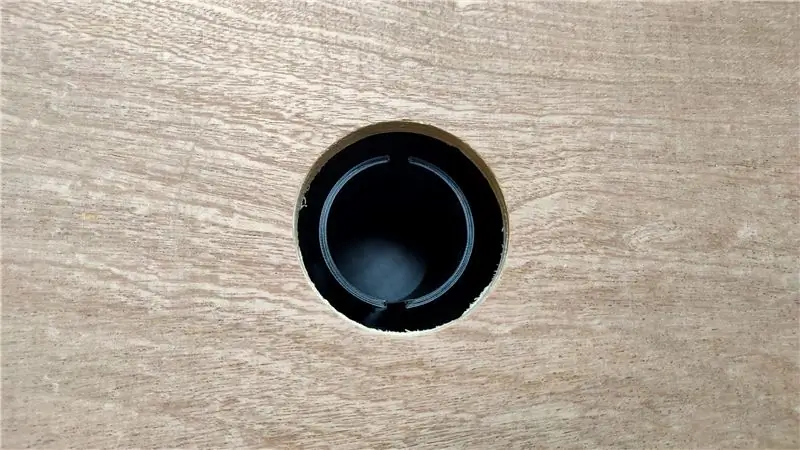
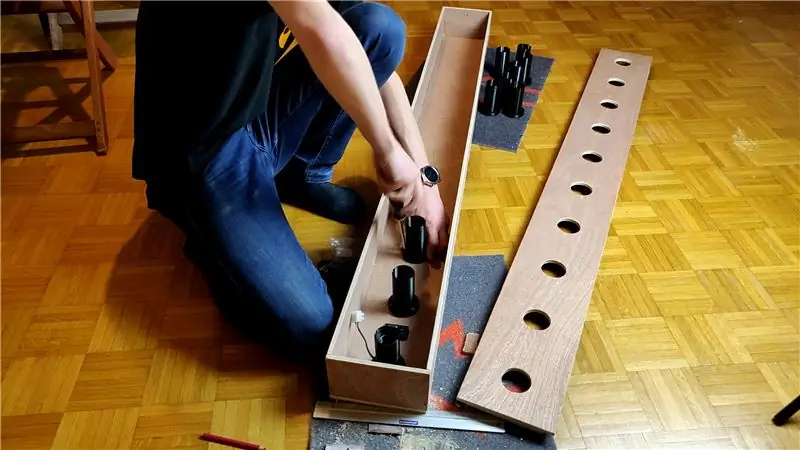
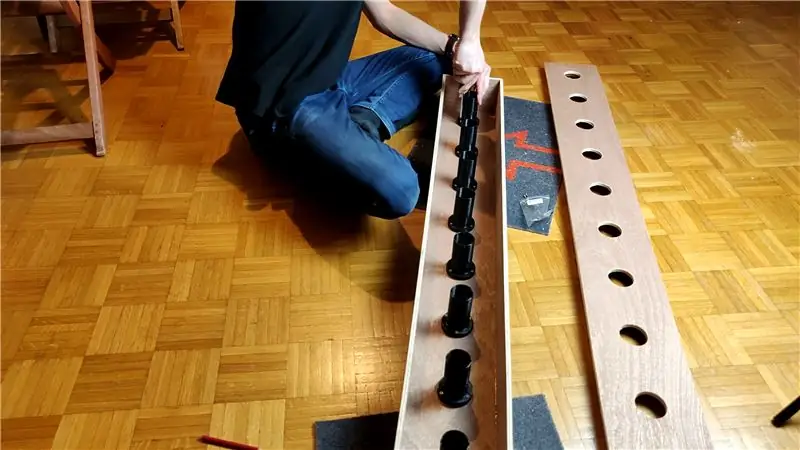
Os primeiros componentes que são montados em nossa caixa recém-construída são os suportes para soquetes de luz. A razão para isso é que os suportes devem ser posicionados centralizados sob cada orifício da placa frontal. Porque o suporte mantém as tomadas de luz em posição, que por sua vez terão as lâmpadas aparafusadas, e as lâmpadas são literalmente as únicas coisas saindo do painel frontal e, portanto, são as únicas que não podem ser movidas para outra posição dentro de nossa caixa. Como a posição deles é fixa, eles devem entrar primeiro, para garantir que eu não cometa um erro estúpido mais tarde.
Como mencionei antes, existem tomadas de luz disponíveis comercialmente com um suporte integrado para montá-las perpendicularmente a uma parede, mas estas custam 4 vezes mais do que as simples que são feitas para pendurar no teto, sem nem mesmo fazer uma tentativa fraca de ta bonita. Então, optei por um suporte barato e impresso em 3D para os soquetes. (Arquivo STL abaixo). Ao fazer o design 3D, assegurei-me de que haveria espaço suficiente para "mexer" as tomadas em várias profundidades.
Imprimi apenas um suporte para verificar o design. Depois disso, imprimi 9 suportes de uma vez, enchendo completamente toda a minha placa de impressão e durando mais de 50 horas.
Eu marquei arbitrariamente a parte superior e inferior da placa frontal e da caixa (lembre-se de que obtive um desvio colossal de 2 mm entre o design digital e a realidade). Então comecei o processo tedioso de centralizar um suporte com a tampa no lugar, levantando cuidadosamente a frente, marcando sua posição com um lápis e movendo para o próximo suporte. Quando tudo foi dito e feito, eu verifiquei novamente todas as posições antes de finalmente parafusá-los na placa traseira.
Uma nota sobre os parafusos: meu design de suporte tem uma base bem grossa, isso é feito de propósito para garantir que meus parafusos de 16 mm de comprimento não fiquem para fora da minha placa traseira de 8 mm. Mais uma razão para escolher um compensado mais espesso. (Esqueça "viva, ame, ria" é "viva, ame e aprenda").
De qualquer forma, as tomadas de luz foram as próximas. Eu escolhi a altura preferida que eu queria que as lâmpadas sobressaíssem acima do painel frontal, e então medi a profundidade que os soquetes deveriam estar, novamente posicionando tudo com cuidado enquanto a frente estava fechada e levantando e medindo. Um pequeno detalhe: primeiro tive que desparafusar e quebrar um pedaço da extremidade do cabo de todos os soquetes que serviam como um alívio de tensão para os cabos quando estavam horrivelmente pendurados no teto, mas como eu os estava montando em suportes impressos personalizados, eles não tinham nenhuma função para mim. Pior ainda, o alívio de tensão fazia com que os cabos resistissem à curva apertada que eu os estava forçando, fazendo assim seu trabalho perfeitamente … então o alívio de tensão teve que ser eliminado para que os soquetes se encaixassem nos suportes da maneira que eu queria.
Colei todos os encaixes nos suportes e deixei endurecer durante a noite com elásticos segurando a pressão. Claro, eu esqueci fabulosamente que comprei 9 lâmpadas normais e uma gorda para a décima luz, esta luz maior é mais esférica em vez de em forma de pêra, exigindo um encaixe colocado mais perto da frente da caixa do que todas as outras luzes.(Viva e aprenda)
Fui, portanto, forçado a quebrar a cola (quebrando apenas um pouco minha impressão 3D) para liberar o encaixe e reposicioná-lo. Depois de muita cola para fixar o suporte e uni-lo ao encaixe na altura certa, foi feita a montagem dos encaixes.
Também aparafusei os conectores das tomadas de luz em um dos lados da placa traseira.
Etapa 5: soldando os eletrônicos de baixa tensão
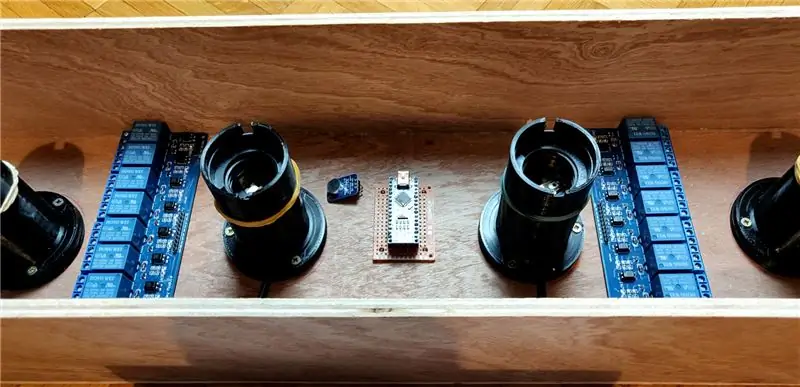
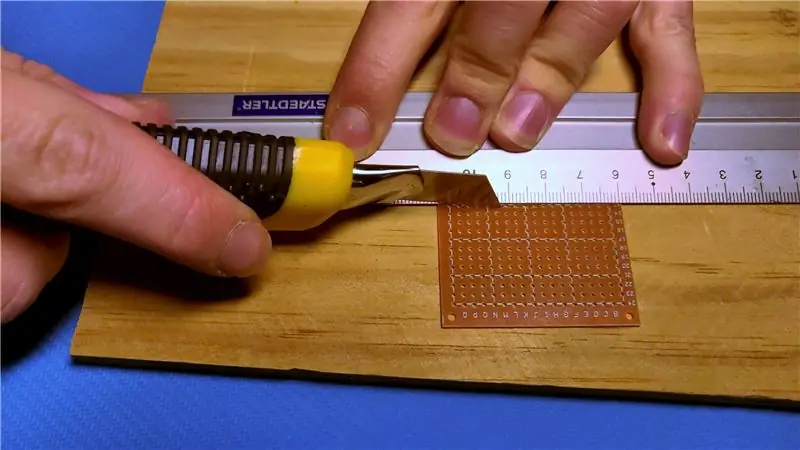
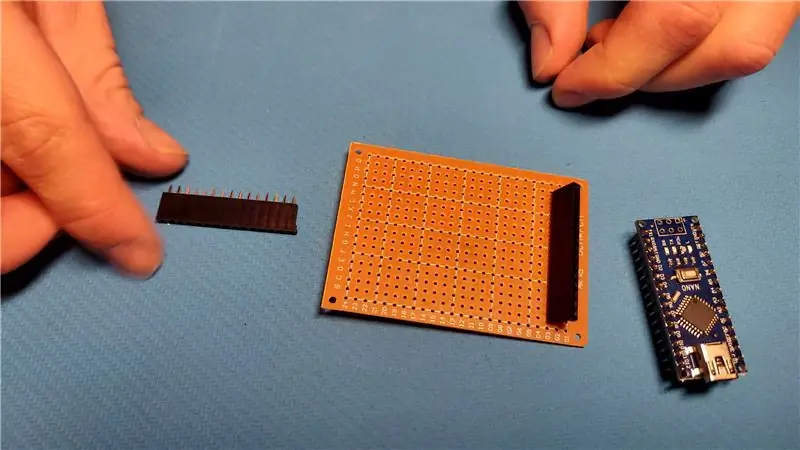
A próxima ordem do dia é "instalar a seco" todos os componentes eletrônicos de baixa tensão da caixa para se ter uma ideia de quanto tempo devem durar as conexões soldadas entre as peças.
Comecei colocando o Arduino no meio entre as luzes 5 e 6 e organizando os relés nos locais adjacentes acima e abaixo.
Percebi que nenhum parafuso de madeira caberia nos orifícios do Arduino nano. Isso é resolvido rapidamente soldando alguns cabeçotes fêmeas em uma placa de pão soldável. Os cabeçalhos conterão o Arduino e alguns orifícios perfurados na placa de circuito aceitarão os parafusos de madeira sem reclamações. Esta placa soldável também abrigará os conectores para o microfone a ser conectado, os conectores (com cabos) para ir para os relés e o cabo longo para a caixa de controle remoto.
Sobre a caixa remota; Eu precisava de dois interruptores no final de um cabo muito longo. Eu estou bem atrás do palco como percussionista, enquanto o medidor fica bem na frente do palco. Comprei 20m de fio 4 trançado que normalmente é usado para soldar tiras de LED. Para abrigar os dois interruptores, projetei e imprimi em 3D uma caixa simples (arquivos STL e F360 abaixo), mas qualquer caixa retangular com alguns recortes para os componentes e fios fará o trabalho.
Depois de medir a distância entre os componentes e tirar um excesso generoso dessa distância, aqueci o ferro de soldar e comecei a soldar.
Soldar todas as conexões requer alguma paciência e, acima de tudo, alguma concentração para fazer a coisa certa. Incluí o esquema de fiação que usei para fazer todas as conexões, mas esteja ciente de que sua fiação pode ser um pouco diferente se você usar componentes diferentes. (Ou se eu cometi um erro no meu diagrama)
No final, minha fiação parecia como se um pássaro estivesse tentando fazer ninho ali. No entanto, milagrosamente não houve erros e nada começou a soltar fumaça ao ligar o aparelho.
Com tudo conectado, eu poderia aparafusar todas as placas de circuito no painel traseiro em espaçadores impressos em 3D. Esses espaçadores têm duas funções: (1) é sempre uma boa ideia deixar algum espaço entre as placas de circuito e a placa em que você as monta. E (2) já reclamei que tenho parafusos de 16 mm e contraplacado de 8 mm e que, portanto, estou em constante perigo de aparafusar os parafusos diretamente na madeira? Sim, os impasses também garantiam que meus parafusos não alcançassem a outra extremidade da caixa de madeira compensada.
[NOTA] Em retrospectiva, eu recomendaria usar 5 relés por módulo de relé. Minha ideia de usar dois módulos de relé de 8 canais era permitir um relé quebrado; nesse caso, eu simplesmente teria que mudar as conexões e o medidor de aplausos estaria ligado e funcionando novamente. Isso também dividiria as conexões de 220 V um pouco melhor entre os dois módulos, tornando o gerenciamento de cabos um pouco mais … gerenciável. (Viva e aprenda)
Etapa 6: Conectando os componentes de 220 V
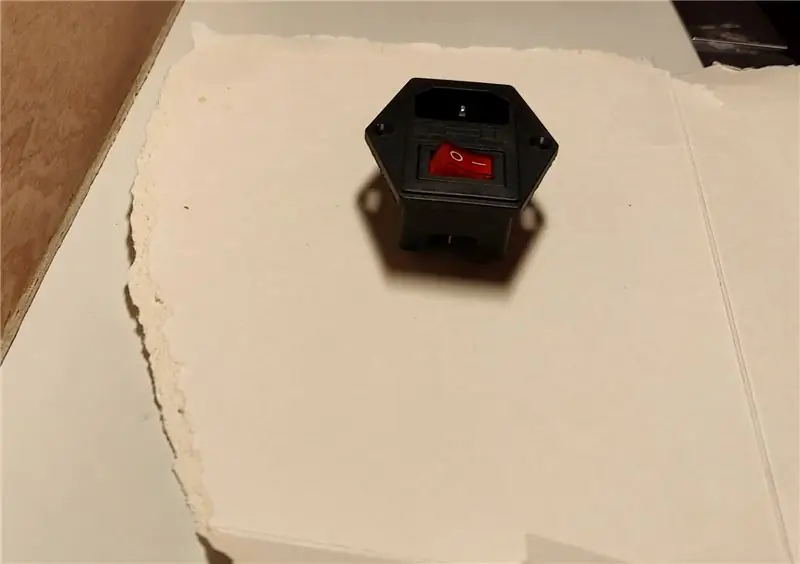
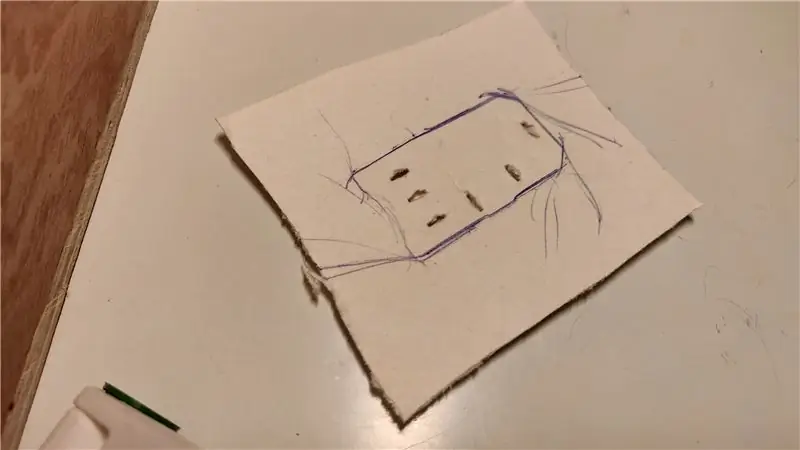
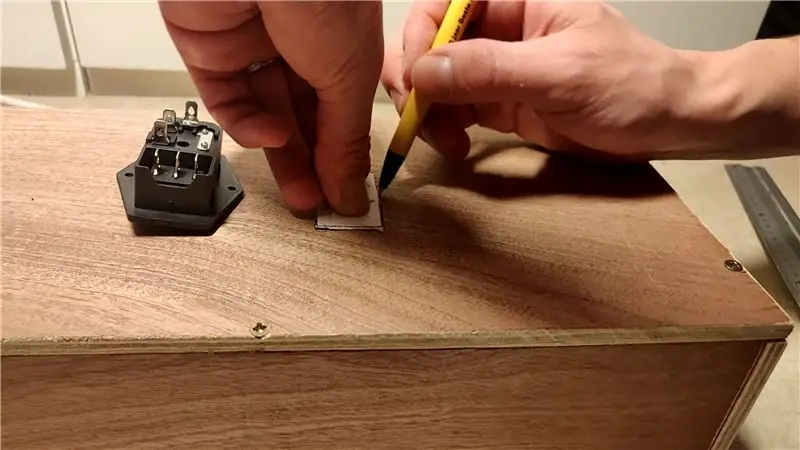
Com todos os componentes de baixa tensão no lugar, é hora de um trabalho sério e instalar o circuito de tensão principal.
Nem é preciso dizer que, ao trabalhar com os fios, você NÃO os conecta, em hipótese alguma, à rede elétrica !!!!!
Junto com o técnico que iria instalar e controlar as luzes de nosso próximo show, decidimos usar uma tomada com fusível como entrada de energia para o medidor de aplausos. Isso garantiu que qualquer cabo de qualquer comprimento pudesse se encaixar e fornecer energia ao nosso medidor.
Além disso, isso adicionaria uma camada de segurança à nossa configuração: esses conectores são equipados com um fusível que explode acima de uma determinada amperagem, garantindo que nada armazene fogo se não for suposto.
Para instalar este plug, precisamos de suas medidas exatas. No entanto, tem uma forma bastante complexa. Então, a coisa mais simples que eu poderia fazer é pressionar o plugue em um pedaço de papelão e traçar os contornos do plugue. As linhas de contorno podem então ser cortadas produzindo um molde que pode ser transferido para a madeira.
Ao marcar e recortar o local para o plugue, lembre-se que já existem componentes instalados na parte interna do medidor que não podem mais ser movidos, limitando os possíveis locais onde o plugue pode sair da caixa. O mesmo vale para o orifício de saída do fio de 20m de comprimento para o controle 'remoto'.
Normalmente você cortaria o buraco com uma serra de vaivém, mas eu não tenho esse dispositivo e estava impaciente, então simplesmente fiz buracos ao longo dos contornos e cortei o buraco com uma lâmina afiada. Isso funciona, mas não posso recomendá-lo, pois quase cortei meus dedos fora.
Agora é apenas uma questão de conectar tudo. Fiz um esquema de fiação do circuito de 220v para fácil referência. O fio quente é conectado a todas as luzes em paralelo, enquanto o fio neutro é interrompido pelos relés antes de conectar as luzes. É tão simples quanto isso. Apenas certifique-se de conectar a luz correta ao relé correto, ou você terá que reconectar a extremidade de controle de 5 V ou os fios de 220 V para consertar seu erro.
Há um instrutivo sobre como conectar seus fios ao soquete de alimentação com fusível que explica tudo melhor do que eu poderia, então vá até lá, mas lembre-se de voltar aqui (https://www.instructables.com/id/Wire- Up-a-Fused-AC-Male-Power-Socket /)
[NOTA] Para conectar os fios neutros aos relés colocados centralmente, conectei um fio ao soquete com fusível e o dividi em dez antes de conectá-lo aos relés. Eu estava planejando passar pelos cabos neutros nos relés, conectando todas as entradas dos relés em paralelo entre si. No entanto, os terminais do relé não aceitavam mais de um cabo, o que me obrigou a pensar em outra solução. Para fazer essa divisão, é aconselhável usar algum tipo de conector. Eu não tinha isso (e estava impaciente) e apenas amarrei todos os cabos juntos em um grande nó antes de isolar o inferno fora dele. Não recomendo este 'nó' por motivos de segurança elétrica. ESPECIALMENTE devido à sua proximidade com a placa Arduino. No entanto, parece funcionar muito bem.
Etapa 7: Snappers magnéticos (opcional)
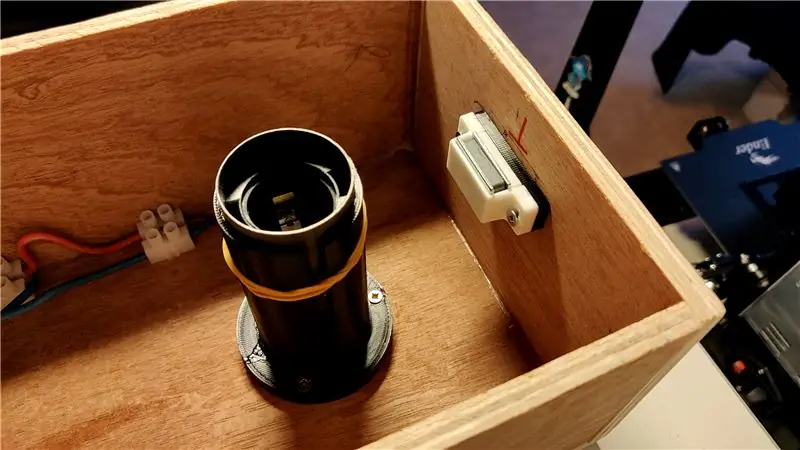
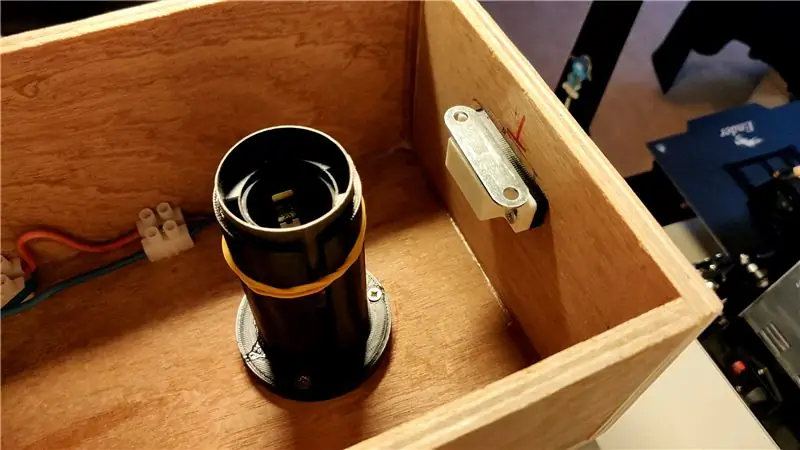
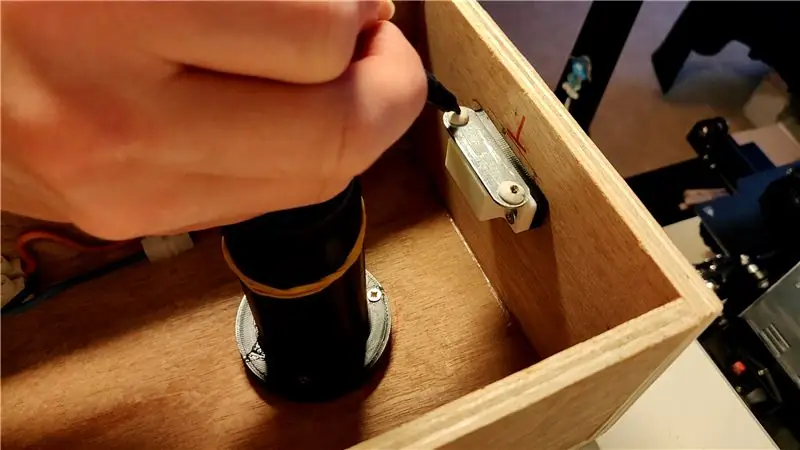
Esta etapa é totalmente opcional, uma vez que as guias do painel frontal seguram suficientemente a placa frontal apenas com a fricção. Decidi incluir os snappers apenas como um recurso de segurança, para que o painel frontal não se soltasse sem eu querer que se soltasse
Passei muitas noites acordado pensando em qual seria o melhor método para segurar o painel frontal da caixa onde ele pertencia. No final, acabei usando fechos de porta magnéticos. Duvido que seja o termo oficial para esses dispositivos bacanas, mas você os reconhecerá imediatamente. Os snappers magnéticos são mais comumente usados para manter as portas do armário fechadas sem usar uma fechadura.
Fixei a parte magnética na parte externa do medidor de aplausos (painel superior, inferior, esquerdo ou direito). Isso foi feito por meio de espaçadores e parafusos personalizados impressos em 3D (yadda yadda yadda, parafusos longos, madeira fina, você já conhece a história ☺)
As placas de metal foram aparafusadas à madeira das guias. Esta também foi a primeira vez que a madeira foi realmente espessa o suficiente para não usar nenhum espaço (yay). No entanto, tive alguns problemas para determinar a posição das placas de metal. Eu encontrei uma solução:
- Anexe a parte magnética à caixa
- coloque a placa de metal no ímã em sua posição perfeita
- nos orifícios da placa, coloque uma pequena bola de "Pritt-buddy" (uma espécie de cola do tipo goma de mascar para prender cartazes nas paredes sem alfinetes, goma de mascar regular provavelmente funcionaria bem)
- com um marcador de álcool, faça um ponto na bola Pritt-buddy no local onde os buracos estão
- feche a tampa, transferindo assim um pouco da tinta de marcador para a madeira
- Levante a tampa e tadaa! Você fez uma pequena marcação onde seus parafusos devem ficar
- remova os amigos e a placa e aparafuse-a na posição correta, primeiro tente
- passo 8: lucro
Coloquei quatro snappers magnéticos na caixa: um embaixo, um em cima, um no meio à esquerda e um no meio à direita.
Os pargos que escolhi tinham uma força de retenção de 6 kg. Com quatro deles, eles forneceram força suficiente para quase levantar a caixa inteira apenas pelo painel frontal.
Etapa 8: O que eu faria de maneira diferente
Ao fazer esse medidor de aplausos, muitas vezes amaldiçoei meu passado por tomar decisões tolas. Vou listar aqui as lições mais importantes que aprendi:
-
USE MADEIRA MAIS ESPESSA. Sério, fazer uma caixa de compensado de 8 mm é possível, mas apresenta muitos desafios e exige que alguns compromissos sejam feitos.
- Em primeiro lugar, a perfuração piloto em todos os orifícios para os parafusos é um desafio porque não há tolerância para brocas com ângulos incorretos.
- Em segundo lugar, os parafusos que eu tinha eram de 16 mm (já mencionei isso antes?). Isso me forçou a fazer alguns ressaltos ao aparafusar na madeira para evitar que os parafusos saíssem do outro lado, mas, ao mesmo tempo, isso significava que os parafusos não estavam penetrando fundo o suficiente para obter tração suficiente para segurar alguns componentes.
- ….
- apenas use madeira mais grossa
Recomendado:
E-dohicky a versão eletrônica do medidor de energia a laser de Russ Dohicky: 28 etapas (com fotos)
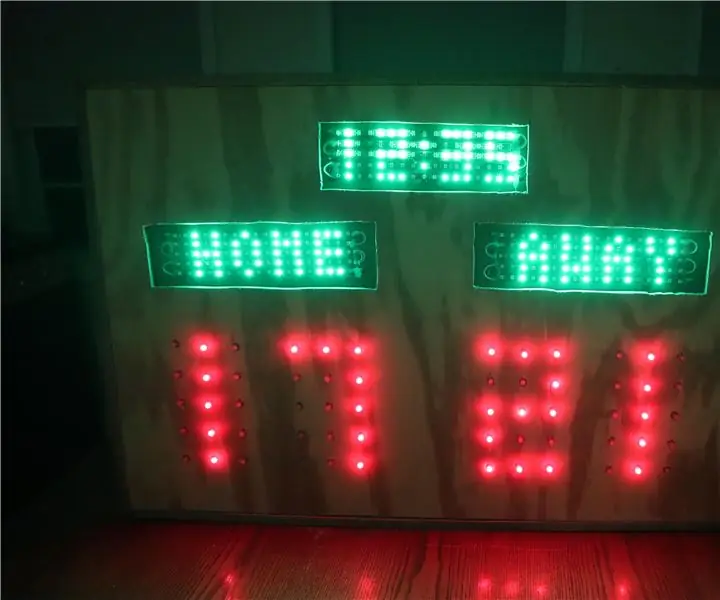
E-dohicky a versão eletrônica do medidor de energia a laser de Russ Dohicky: ferramenta de energia a laser.e-dohicky é a versão eletrônica do dohicky de Russ SADLER. Russ anima o excelente canal SarbarMultimedia youtube https://www.youtube.com/watch?v=A-3HdVLc7nI&t=281sRuss SADLER apresenta um acessório fácil e barato
Circuito de aplausos DIY: 5 etapas
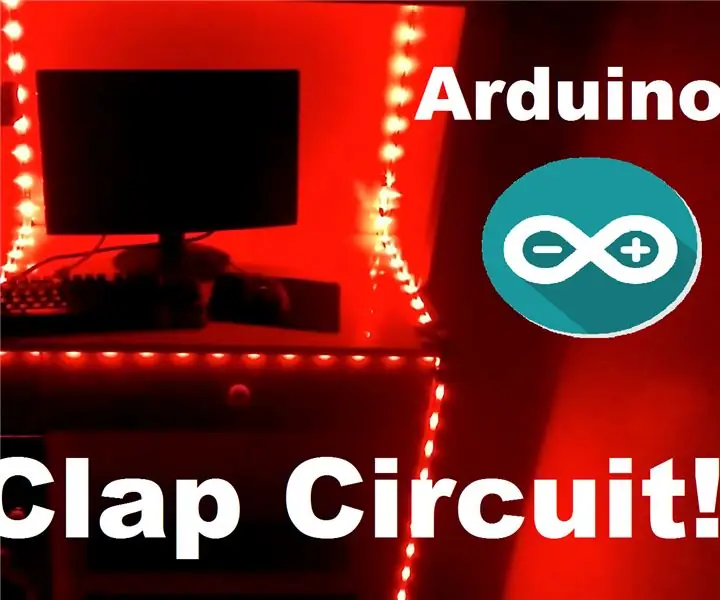
Circuito de aplausos DIY: Olá pessoal! Bem-vindo de volta a outro instructables de Let's Innovate. Desta vez, vou mostrar como fazer um circuito simples que permite ligar ou desligar seus aparelhos com apenas 3 palmas bem cronometradas. Tenho um vídeo sobre o assunto, que fornece a
Como fazer aplausos? Interruptor ON / OFF -- Sem qualquer IC: 6 etapas
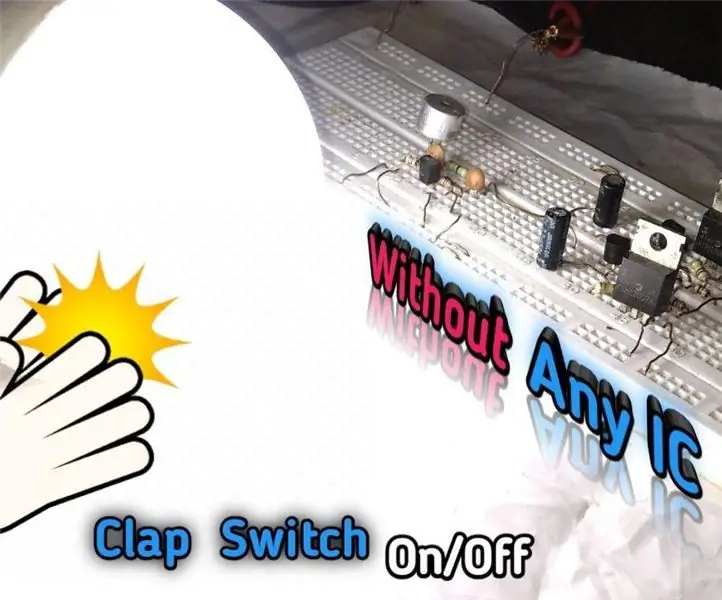
Como fazer aplausos? Interruptor ON / OFF || Sem qualquer IC: Este é um aplauso ON Of Switch sem qualquer IC. Você pode aplaudir? Primeira vez, então a lâmpada? ON E aplaude segunda vez a lâmpada? DESLIGADO. Este circuito é baseado em flip-flop SR. Componentes 1. Transistores NPN BC547 (4 unidades) 2. Resistores de 10k (5 unidades) 3. 1K Resist
Matriz de LEDs ativados por aplausos: 4 etapas
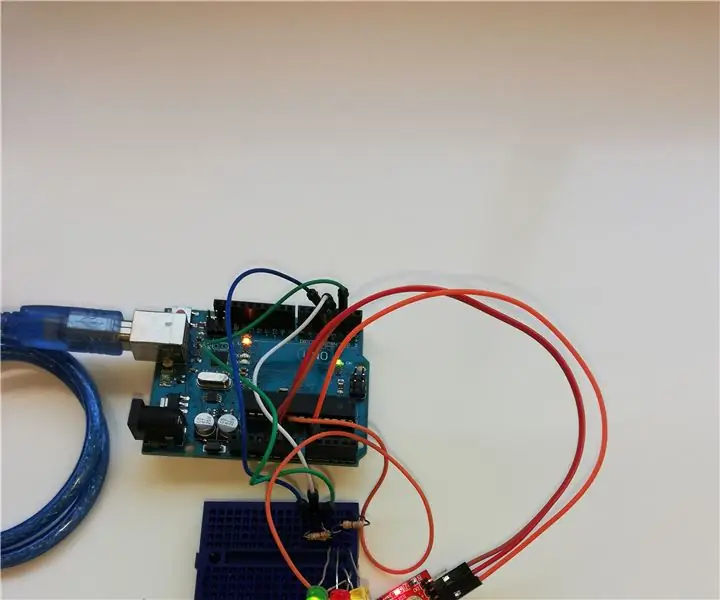
Matriz de LEDs ativados por palmas: Ao final deste instrutível, você será capaz de construir um dispositivo que ouve ruídos altos como palmas e responde a eles ligando ou desligando 3 LEDs. Acima está uma imagem do resultado final
Clap Switch (40 aplausos em 5 segundos): 4 etapas (com imagens)
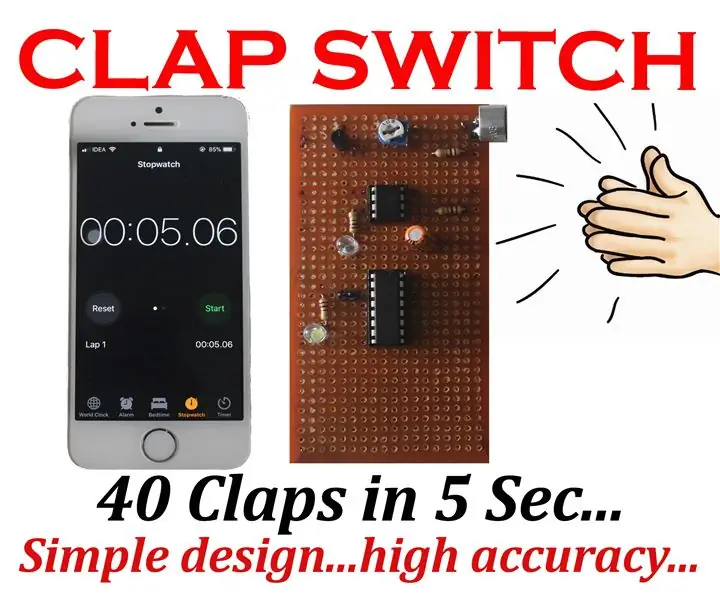
Clap Switch (40 aplausos em 5 segundos): Clap Switch tem a capacidade de LIGAR / DESLIGAR qualquer componente elétrico conectando a saída do circuito a um interruptor de relé. Aqui vamos fazer uma troca de palmas com poucos componentes e com explicações muito boas. Comparado com todos os outros interruptores de aplauso