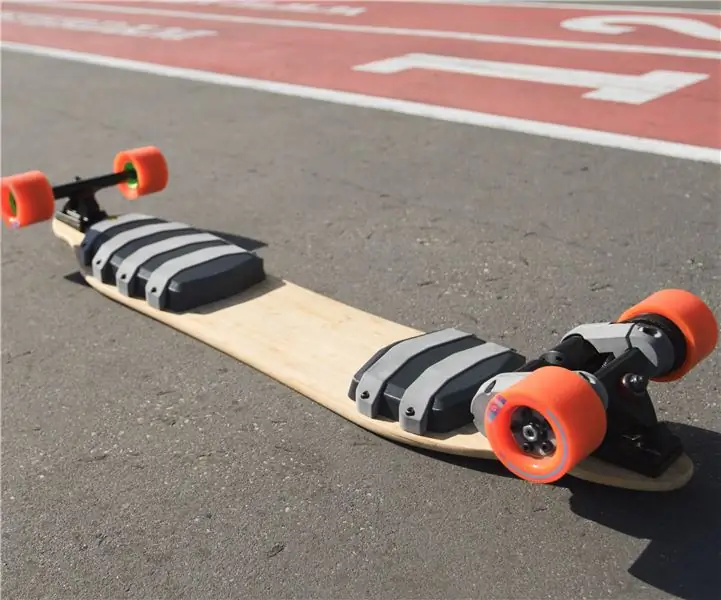
Índice:
2025 Autor: John Day | [email protected]. Última modificação: 2025-01-23 15:03
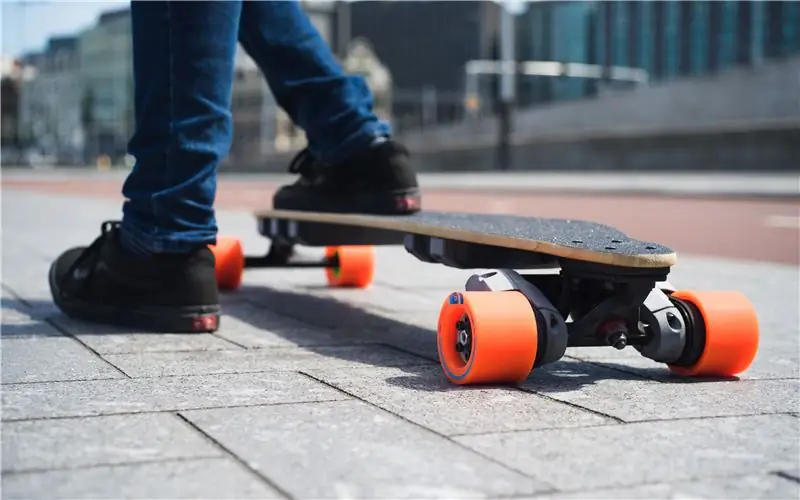
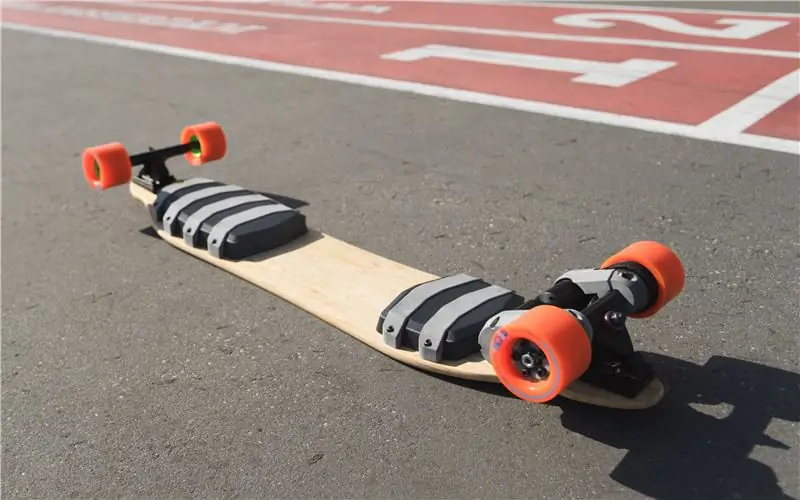
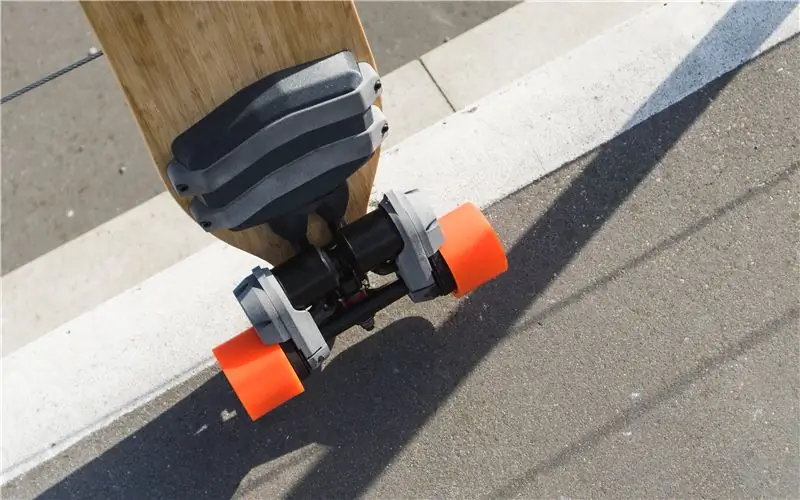
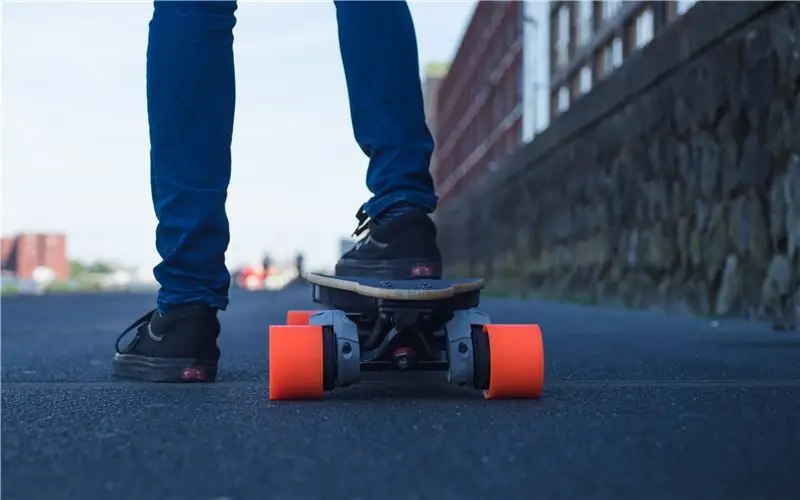
Este Instructable é uma visão geral do processo de construção do Fusion E-Board que projetei e construí enquanto trabalhava nos Hubs 3D. O projeto foi comissionado para promover a nova tecnologia HP Multi-Jet Fusion oferecida pelos hubs 3D e para mostrar várias tecnologias de impressão 3D e como elas podem ser combinadas de maneira eficaz.
Eu projetei e construí um longboard elétrico motorizado, que pode ser usado para viagens curtas a moderadas ou combinado com transporte público para oferecer um alcance de viagem muito mais amplo. Tem uma velocidade máxima elevada, é muito manobrável e é facilmente transportado quando não está a ser utilizado.
Etapa 1: Processo de Design
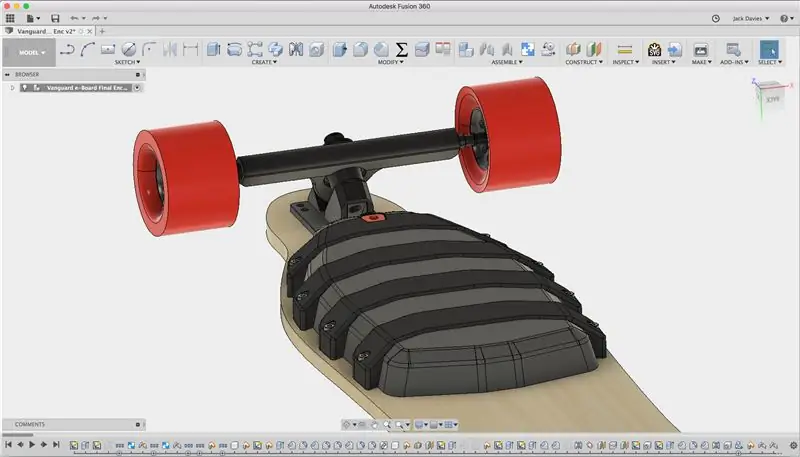
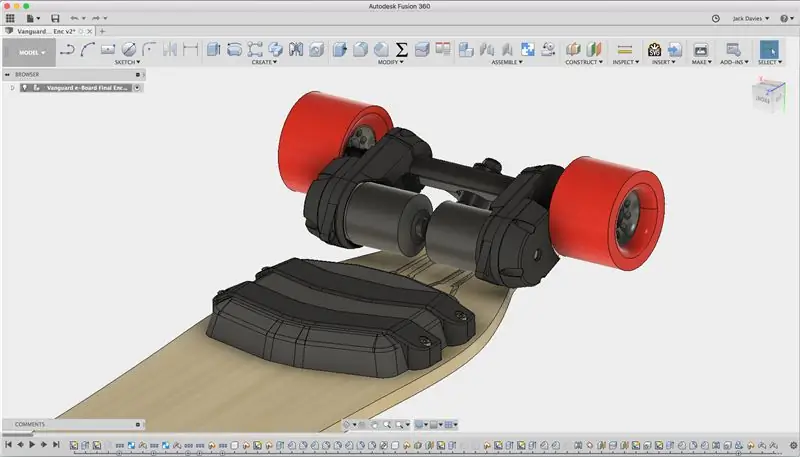
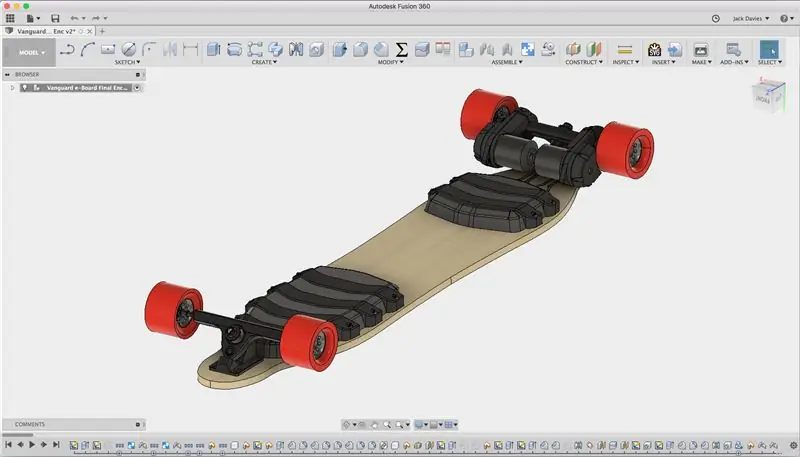
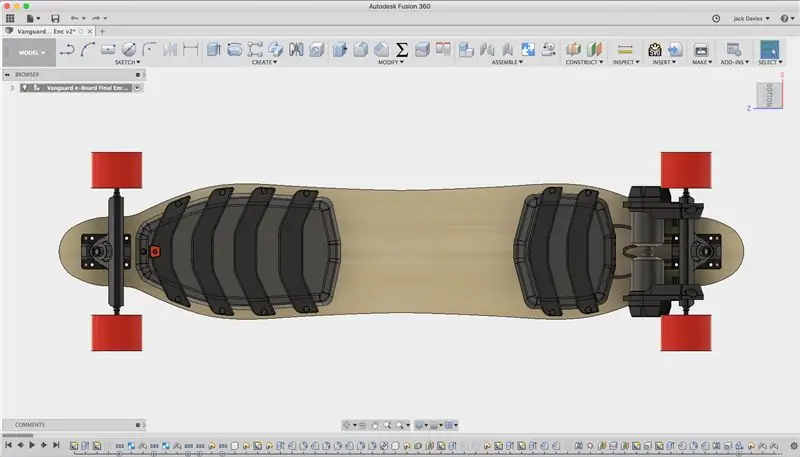
Comecei o projeto identificando os principais componentes padrão do longboard; caminhões, convés e rodas. Essas eram peças prontas para uso, então usei-as como ponto de partida do design. A primeira etapa foi projetar o trem de força, que inclui os suportes do motor, a configuração da engrenagem e algumas modificações nos caminhões. O tamanho e a posição dos suportes do motor ditariam o tamanho e a localização dos gabinetes, por isso era importante que isso fosse concluído primeiro. Calculei os requisitos de velocidade máxima e torque desejados, o que me permitiu selecionar os motores e a bateria para a placa. A relação de engrenagens também foi calculada e os tamanhos das polias foram selecionados, juntamente com o comprimento da correia de transmissão. Isso me permitiu calcular o tamanho correto dos suportes do motor, o que garantiu uma correia bem tensionada.
A próxima etapa foi projetar os invólucros da bateria e do controlador de velocidade (ESC). O deck selecionado é predominantemente composto de bambu, portanto, é bastante flexível, dobrando-se substancialmente no meio. Tem a vantagem de ser confortável de conduzir, pois absorve os solavancos da estrada e não os transfere para o condutor. No entanto, isso também significa que um gabinete dividido é necessário para abrigar a bateria e os componentes eletrônicos, já que um gabinete de comprimento total não seria capaz de se flexionar com a placa e faria contato com o solo durante a operação. Os controladores eletrônicos de velocidade (ESC) foram colocados mais próximos dos motores devido a restrições elétricas. Como os motores são fixados por meio dos caminhões, a posição muda durante as curvas, portanto, o gabinete teve que ser projetado para permitir a folga dos motores.
O sistema de bateria foi colocado na outra extremidade do convés e abrigou os componentes eletrônicos relacionados à energia. Isso inclui a bateria, composta por 20 células de íon de lítio 18650, o sistema de gerenciamento da bateria, o botão liga / desliga e a tomada de carga.
Usei o Autodesk Fusion360 para todo o processo de design, este software me permitiu modelar rapidamente os componentes dentro da montagem principal, o que acelerou consideravelmente o tempo de desenvolvimento. Eu também usei os recursos de simulação do Fusion360 para garantir que as peças fossem fortes o suficiente, especialmente os suportes do motor. Isso me permitiu realmente reduzir o tamanho dos suportes, pois pude verificar os requisitos de resistência e deflexão e remover o material, mantendo um fator de segurança adequado. Depois que o processo de design foi concluído, foi muito fácil exportar as peças individuais para impressão 3D.
Etapa 2: sistema de transmissão
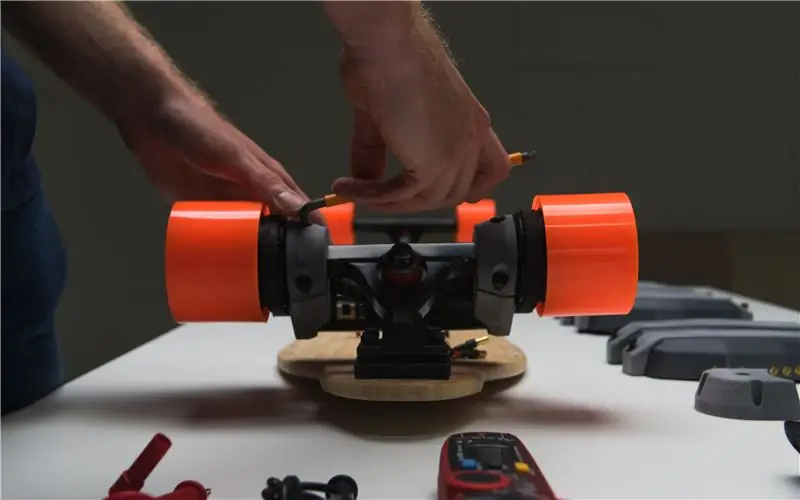
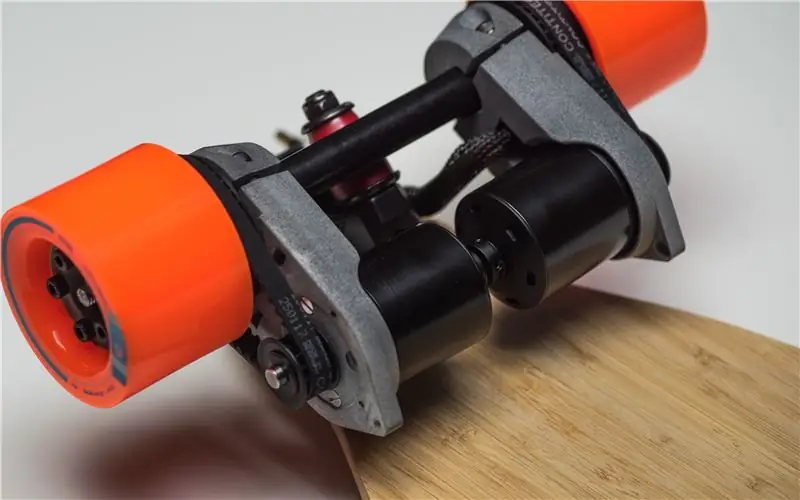
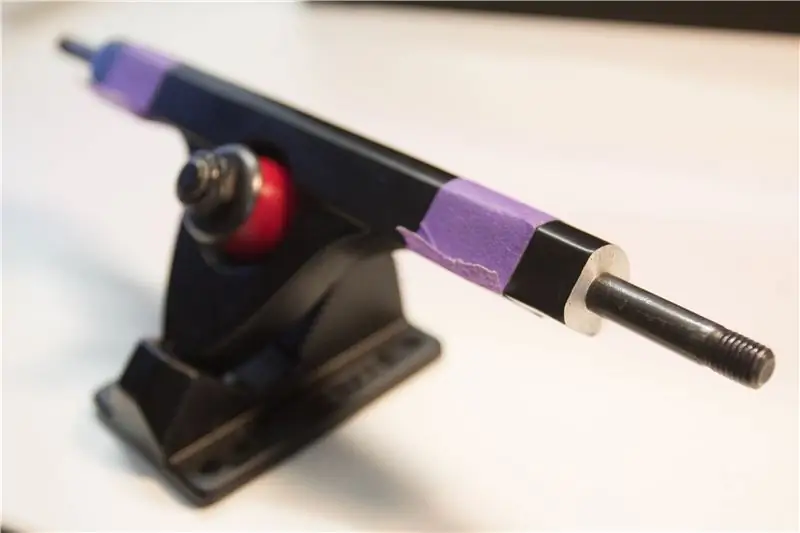
Concluí a construção do sistema de transmissão primeiro, para garantir a folga adequada para o gabinete eletrônico. Selecionei caminhões Calibre para usar, pois eles têm um perfil quadrado perfeito para fixar os suportes do motor. No entanto, o eixo era um pouco curto demais para permitir que os dois motores fossem usados no mesmo caminhão, então precisei estendê-lo para permitir que as rodas se encaixassem.
Consegui isso cortando parte da carroceria de alumínio do gancho do caminhão, expondo mais o eixo de aço. Em seguida, cortei a maior parte do eixo, deixando cerca de 10 mm que eu poderia enroscar com uma matriz M8.
Um acoplador poderia então ser aparafusado e outro eixo roscado adicionado a ele, efetivamente estendendo o eixo. Usei o composto de retenção Loctite 648 para fixar permanentemente o acoplador e o novo eixo para garantir que não se desparafusasse durante o uso. Isso permitiu que os dois motores se encaixassem no caminhão e forneceu bastante espaço para as rodas.
O trem de força foi impresso principalmente com a tecnologia HP Multi-Jet Fusion, para garantir rigidez e resistência durante altas acelerações e frenagens, onde as maiores forças seriam transferidas.
Uma polia especial foi projetada para travar nas rodas traseiras, que foi então conectada à polia do motor com uma correia HTD 5M. Uma capa impressa em 3D foi adicionada para fornecer proteção ao conjunto da polia.
Etapa 3: Gabinetes de nervura
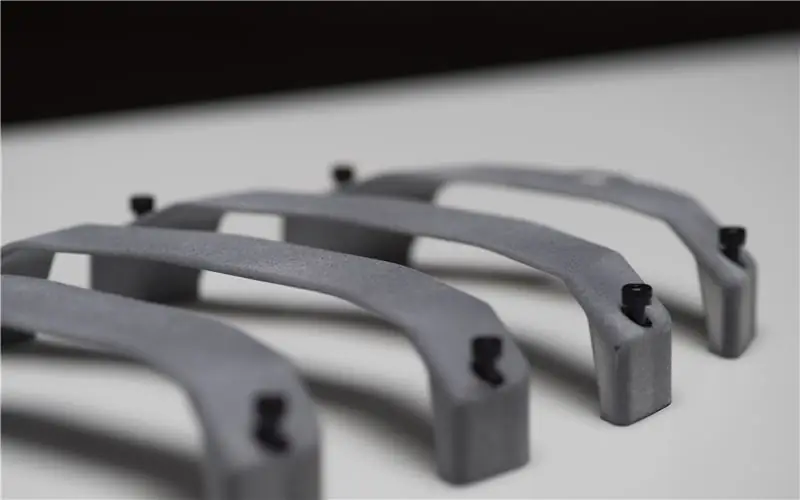
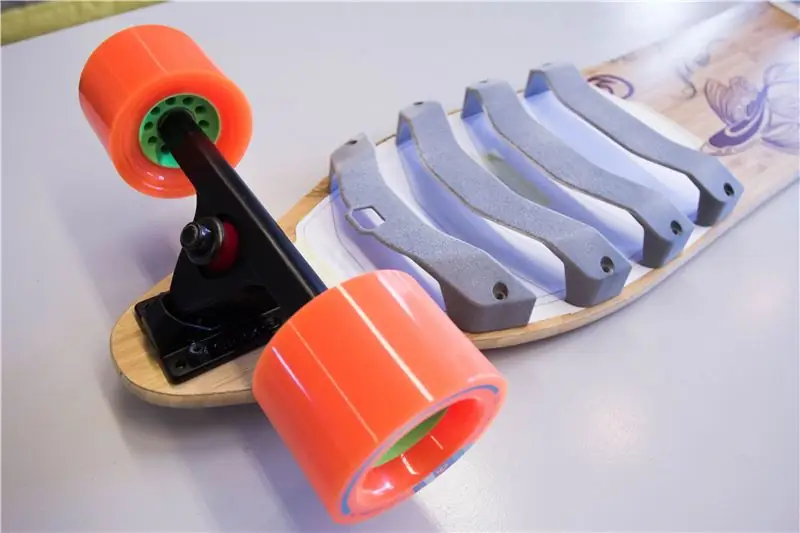
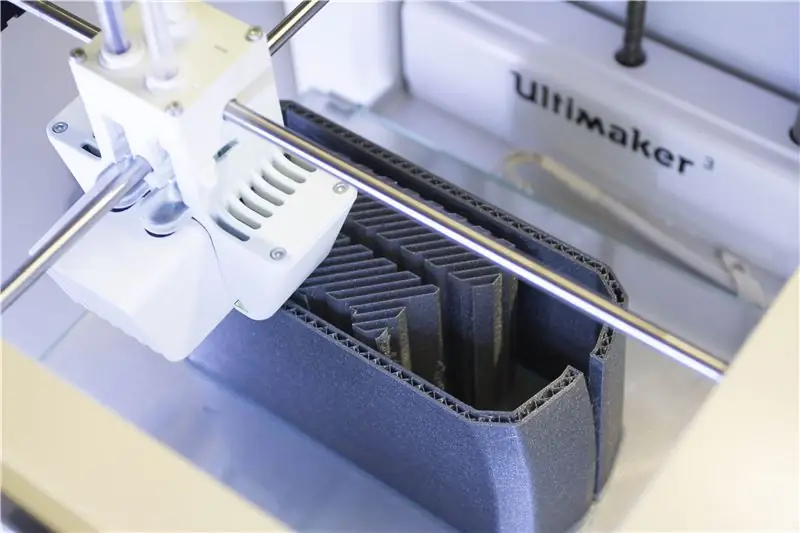
Uma das principais decisões de projeto que tomei foi separar os gabinetes, o que resultou em uma aparência limpa e permitindo que o deck flexível funcionasse sem qualquer rigidez adicional dos gabinetes. Eu queria transmitir os aspectos funcionais da tecnologia HP Multi Jet Fusion, então decidi imprimir por FDM o corpo principal dos gabinetes, o que reduziu os custos, e depois usei as peças HP para apoiá-los e prendê-los ao convés. Isso proporcionou uma estética interessante ao mesmo tempo em que era muito funcional.
Os invólucros impressos FDM foram divididos ao meio para ajudar na impressão, pois o material de suporte pode ser eliminado da superfície externa. A linha de divisão foi cuidadosamente posicionada para garantir que ficasse escondida pela peça HP quando presa à placa. Orifícios para as conexões do motor foram adicionados e conectores de bala folheados a ouro foram colados no lugar
Inserções roscadas foram embutidas no deck de bambu para prender os gabinetes à placa e foram lixadas rente à superfície da placa para garantir que não houvesse espaço entre o deck e o gabinete.
Etapa 4: Eletrônica
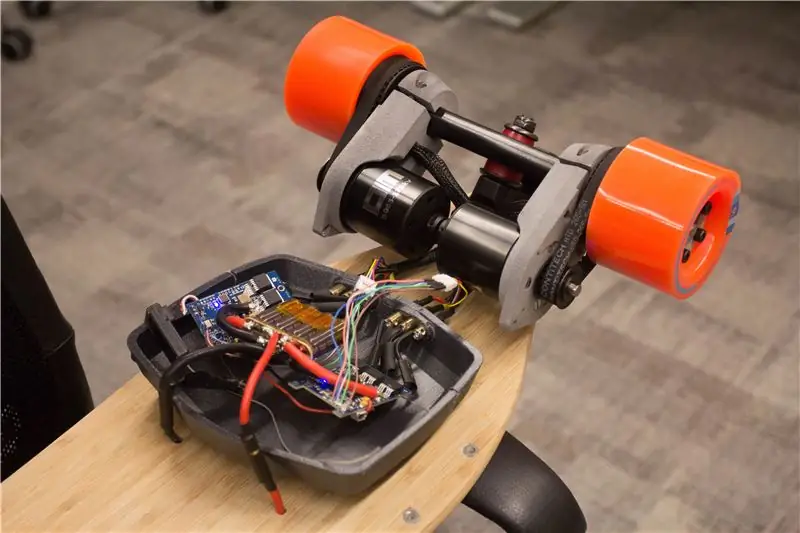
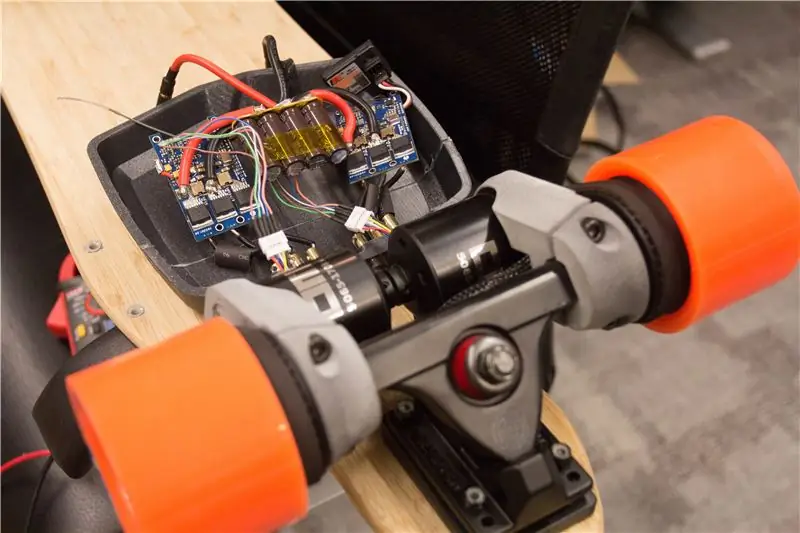
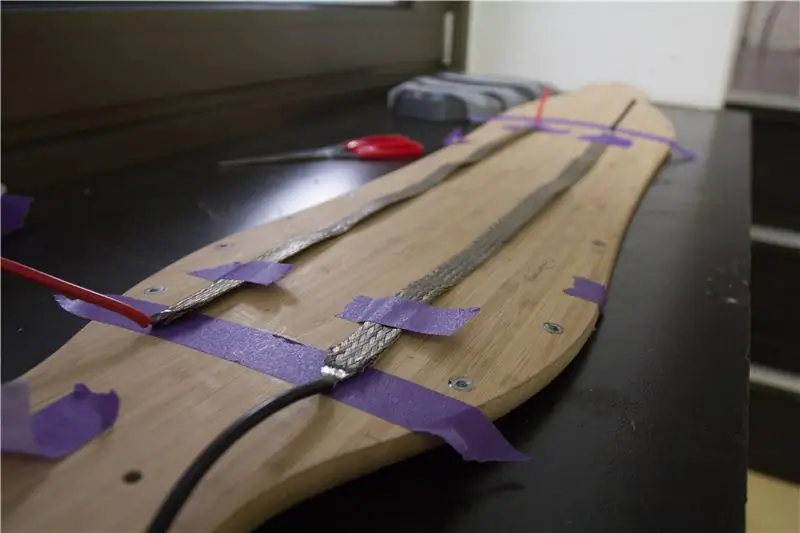
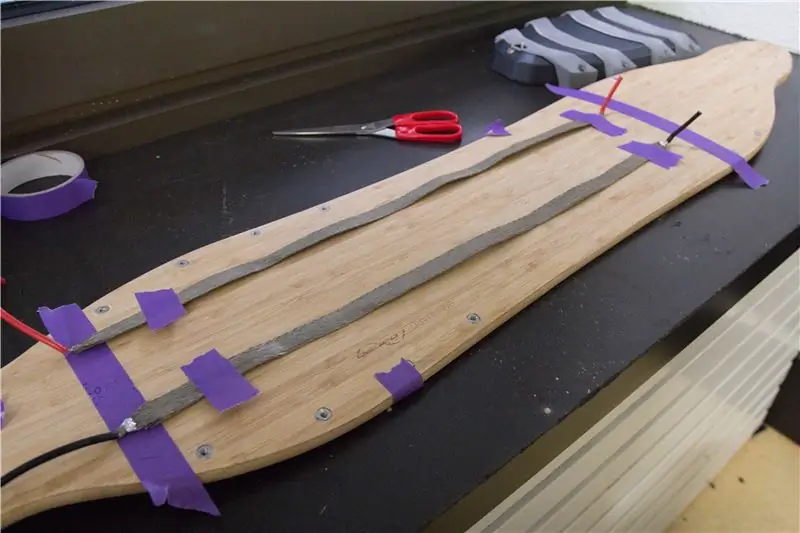
A eletrônica foi cuidadosamente escolhida para garantir que a placa fosse poderosa, mas também intuitiva de usar. Esta placa pode ser potencialmente perigosa se ocorrer algum mau funcionamento, portanto, a confiabilidade é um fator muito importante.
O pacote de bateria é composto de 20 células individuais de íon de lítio 18650 que são soldadas por pontos para formar um pacote de 42v. 2 células são soldadas em paralelo e 10 em série; as células que usei eram Sony VTC6. Usei um soldador local para soldar as abas de níquel para formar o pacote, pois a soldagem cria muito calor que pode danificar a célula.
A energia do compartimento da bateria foi transferida para a caixa do controlador de velocidade usando um cabo trançado achatado que passava logo abaixo da fita adesiva na parte superior do deck. Isso permitiu que os cabos ficassem 'ocultos' e eliminou a necessidade de passar cabos na parte inferior, o que teria uma aparência feia.
Como esta é uma placa de motor duplo, dois controladores de velocidade são necessários para controlar cada motor de forma independente. Eu usei o controlador de velocidade VESC para esta construção, que é um controlador projetado especificamente para skates elétricos, o que o torna muito confiável para esse uso.
Os motores usados são 170kv 5065 out-runners que podem produzir 2200W cada, o que é muita potência para esta placa. Com a configuração de engrenagem atual, a velocidade máxima das placas é de cerca de 35 MPH e acelera muito rapidamente.
A última etapa foi criar um controle remoto para controlar a placa. Um sistema sem fio foi preferido devido à operação mais fácil. No entanto, era importante garantir alta confiabilidade de transmissão, pois uma queda na comunicação poderia ter sérios problemas de segurança, especialmente em altas velocidades. Depois de testar alguns protocolos de transmissão de rádio, decidi que a radiofrequência de 2,4 GHz seria a mais confiável para este projeto. Usei um transmissor de carro RC pronto para uso, mas reduzi significativamente o tamanho transferindo os componentes eletrônicos para uma pequena caixa de mão que foi impressa em 3D.
Etapa 5: Vídeo promocional e painel finalizado
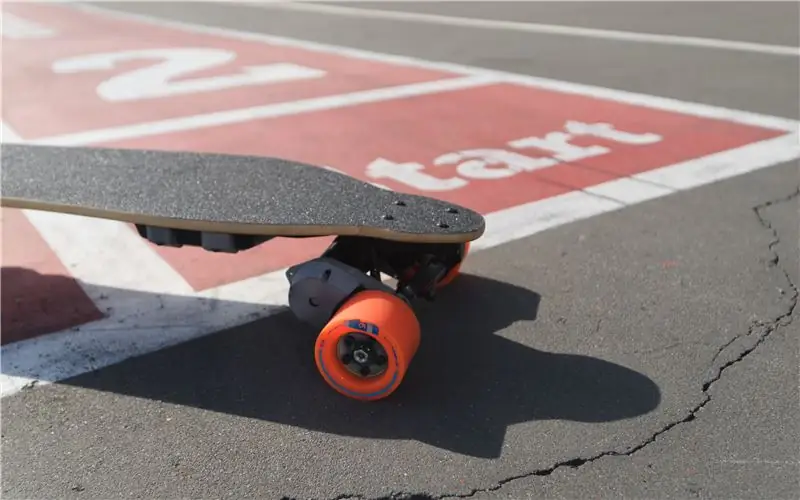
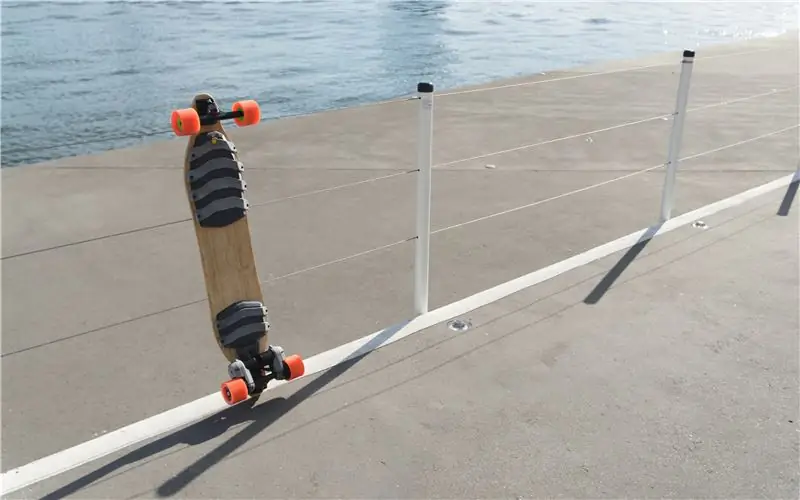
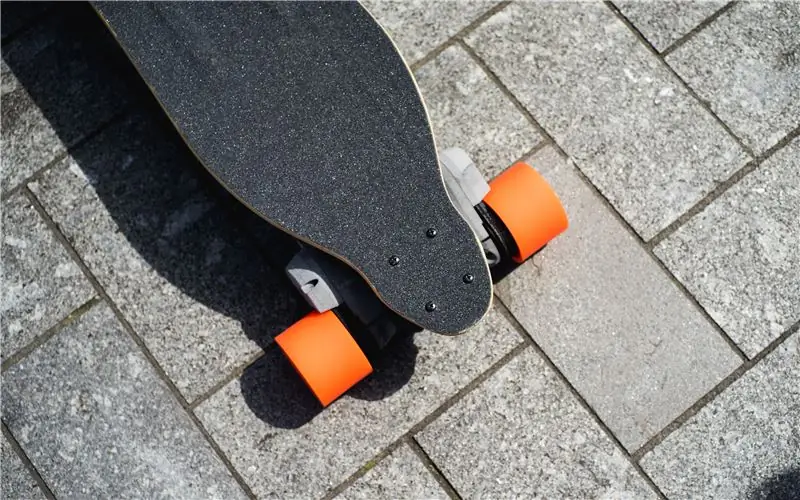
O projeto agora está concluído! Criamos um vídeo incrível do tabuleiro em ação, você pode conferir abaixo. Muito obrigado aos Hubs 3D por me permitirem fazer este projeto - verifique-os aqui para todas as suas necessidades de impressão 3D! 3dhubs.com
Recomendado:
Amplificador impresso em 3D de um instrumento musical elétrico: 11 etapas (com imagens)
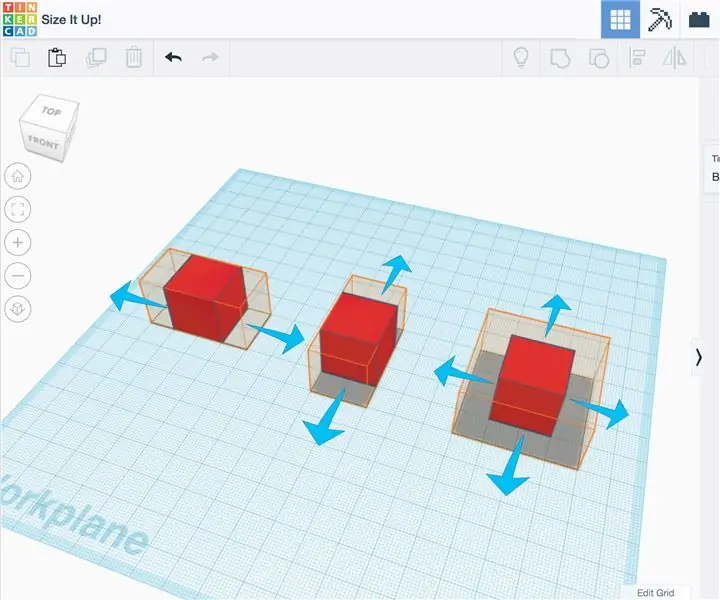
Um amplificador impresso em 3D de instrumento musical elétrico: Definição do projeto. Espero fazer um amplificador imprimível para uso com um violino elétrico ou qualquer outro instrumento elétrico. amplificador ativo e mantê-lo pequeno
Carro de brinquedo elétrico movido a RC: 10 etapas (com fotos)
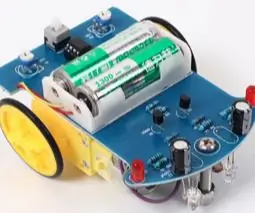
Carro de brinquedo elétrico movido a RC: Por: Peter Tran 10ELT1 Este tutorial detalha a teoria, projeto, fabricação e processo de teste para um carro de brinquedo elétrico movido a controle remoto (RC) usando os chips HT12E / D IC. Os tutoriais detalham as três fases do design do carro: Cabo amarrado Infrar
Interruptor deslizante elétrico impresso em 3D (usando apenas um clipe de papel): 7 etapas (com fotos)
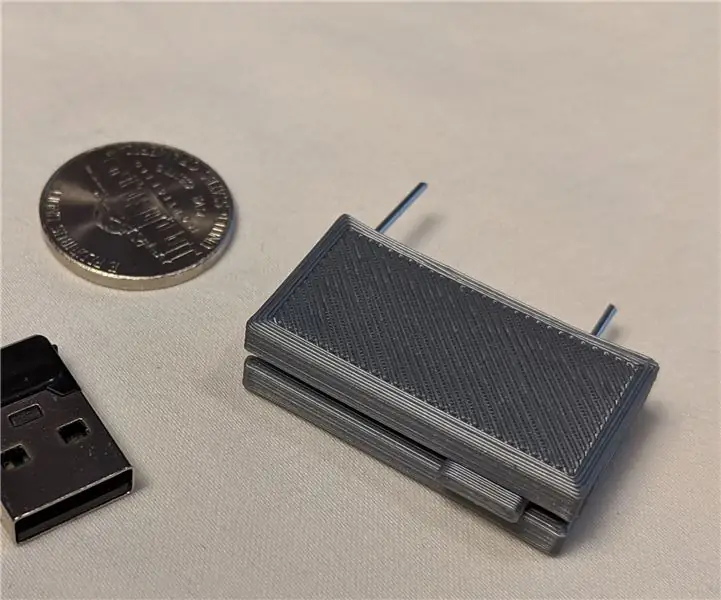
Interruptor deslizante elétrico impresso em 3D (usando apenas um clipe de papel): Eu me envolvi em conectar meus próprios pequenos projetos elétricos ao longo dos anos, principalmente na forma de clipes de papel, papel alumínio e papelão remendado com cola quente. Recentemente comprei uma impressora 3D (a Creality Ender 3) e fui procurar f
Faça seu próprio longboard motorizado elétrico: 8 etapas (com fotos)
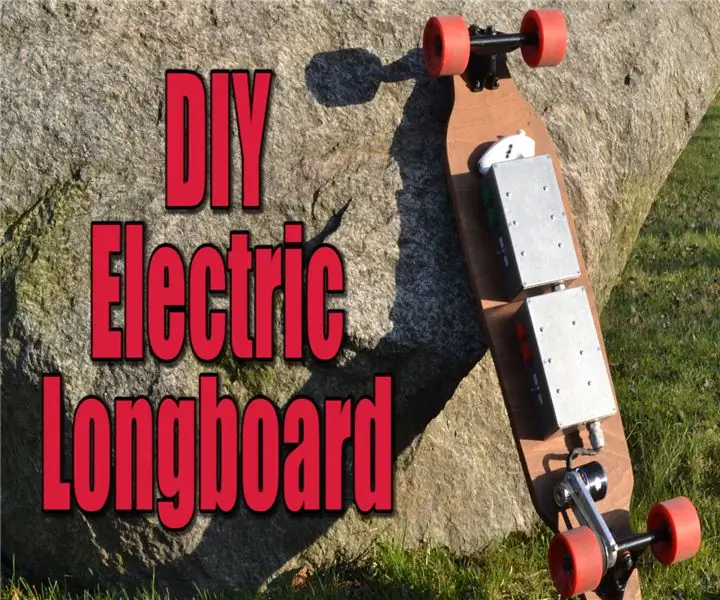
Faça seu próprio longboard motorizado elétrico: Neste projeto, vou mostrar como construir um longboard motorizado elétrico a partir do zero. Pode atingir velocidades de até 34 km / he viajar até 20 km com uma única carga. Os custos estimados são em torno de 300 $, o que o torna uma boa alternativa ao comércio
Thrush elétrico: 6 etapas (com fotos)
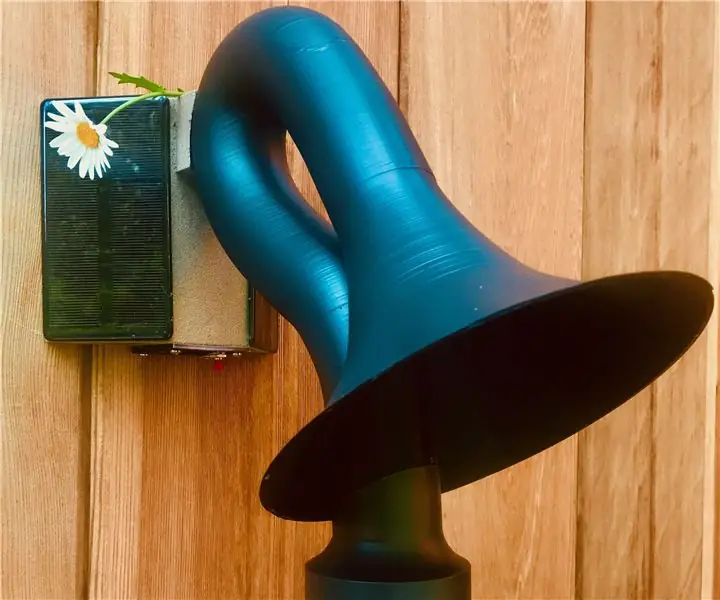
Tordo elétrico: Sentado no convés no final da noite, fiquei realmente surpreso com o chamado ressonante de um pequeno pássaro sentado em um galho nu no topo de uma bétula distante. A chamada é incrivelmente potente para o ouvido. Pertence a uma família de cantores únicos - tordos. T