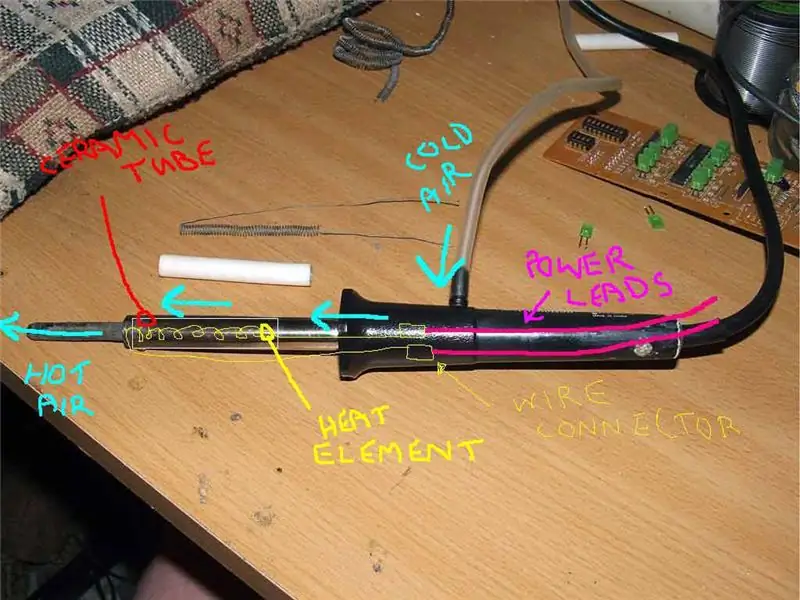
Índice:
- Etapa 1: do depósito de lixo para minha casa
- Etapa 2: o ventilador
- Etapa 3: Unidade do soprador
- Etapa 4: Elemento de aquecimento
- Etapa 5: Close Up do Elemento
- Etapa 6: tubo de cerâmica
- Etapa 7: O elemento e o tubo de cerâmica
- Etapa 8: The Gutz
- Etapa 9: o bocal
- Etapa 10: estaca quadrada em um orifício redondo
- Etapa 11: todas as coisas estão aqui
- Etapa 12: Soprador de vela:)
- Etapa 13: Fonte de alimentação regulada
- Etapa 14: Temp # 1
- Etapa 15: Temp # 2
- Etapa 16: Temp # 3
- Etapa 17: Fio de solda derretendo
- Etapa 18: Primeiro trabalho
2025 Autor: John Day | [email protected]. Última modificação: 2025-01-23 15:03
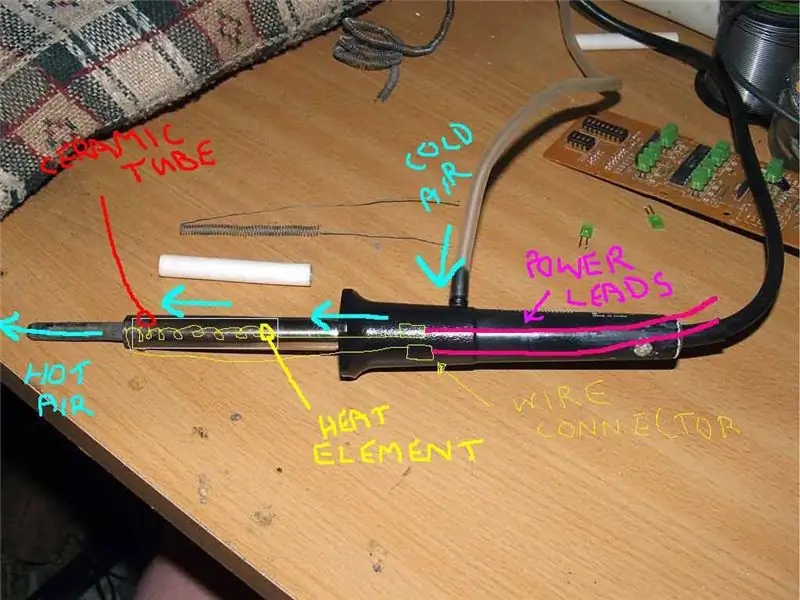
Esta é a minha primeira postagem eva de um artigo DIY na web. Então, desculpe-me por alguns erros de digitação, protocolo etc. As instruções a seguir mostram como fazer um ferro de solda a ar quente TRABALHADOR adequado para TODOS os usos que requerem solda. Este ferro de soldar a ar quente não se limita a dispositivos SMT (tecnologia de montagem em superfície) ou fio de solda super fino. Em menos de 15 segundos depois de ligar o bebê, alcancei mais de 300 graus centígrados de ar quente. Eu ainda tinha espaço para mais … lol. O custo para mim foi de menos de $ 10 dólares australianos. mais gasolina para meu carro chegar ao lixão local e voltar para casa novamente. Se você não tem uma fonte de alimentação regulada, tenho certeza de que uma ou duas fontes ATX conectadas em série forneceriam energia suficiente para energizar sua versão. Se você fizer isso dessa forma, um potenciômetro é essencial para ajustar a saída de amperagem, bem como a tensão CC. Esta unidade de furo é SEGURA de choque elétrico devido a riscos de alta tensão / corrente típicos de fontes de alimentação CA, mas se você tiver um relógio ruim … use proteção:)
Etapa 1: do depósito de lixo para minha casa
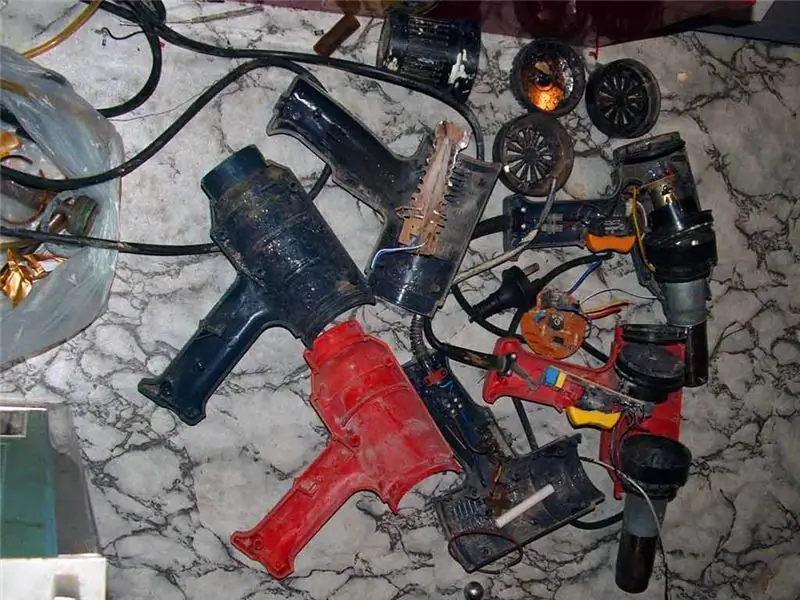
Eu não tinha muita fé de que seria capaz de tirar qualquer coisa útil dessas armas de ar quente quando as comprasse no lixão local por quase nada. Depois que os separei, algumas partes funcionaram e outras não. Era apenas uma questão de jogar fora os pedaços inúteis e ficar com os bons e depois um pouco mais para sobrar, caso meu ferro falhasse nos anos que viriam. Depois de coletar o que achei que poderia ser útil para tornar minha ideia realidade, coloquei todos eles diante de mim e ponderei sobre eles com alguns cafés e cigarros. INTRODUÇÃO: Ontem de manhã, meu ferro de solda de 50 watts cagou. Trágico eu sei … lol. A principal tragédia foi que eu não tinha $$$ para comprar outro. Bem, eu tinha uma soma de dinheiro, mas não o suficiente para me arranjar outra. Sou um fotógrafo freelance, um péssimo nisso, e estou trabalhando no uso de PWM (modulação por largura de pulso) para regular o suprimento de voltagem de pequenas baterias de chumbo-ácido retiradas de scooters velhas movidas a bateria. O material eletrônico para fazer meus reguladores de voltagem PWM eu obtenho desoldando velhas fontes de alimentação ATX e televisores etc. material. De qualquer forma, de volta ao cerne desta apresentação:) Uma pesquisa de duas horas no Google na WWW revelou que muitas pessoas converteram seus ferros de soldar em ferros de solda de ar quente. Mas eles estavam todos trabalhando antes de modificá-los e o meu estava morto desde o início … lol. Além disso, as outras criações que vi na web limitaram-se em grande parte à remoção dos bits eletrônicos SMT menores. Eu percebi que, em minha rápida revisão das "criações" de outras pessoas, todas elas tinham a mesma falha e problema básico: expor o ar frio suficiente que passa por seus dispositivos para aquecer o elemento antes de deixar o ferro de solda. A maioria das pessoas teve idéias de inserir cobre ou malha de ferro no barril próximo ao elemento para aumentar a área de superfície do elemento de aquecimento exposta à passagem pelo ar mais frio. Minha experiência com este método usado por outros, me lembrou de meus experimentos de resfriamento Peltier anteriores que usei mais tarde para meu aquário marinho … isso foi com problemas de transferência de calor. Oopsy… foi rastreado;) De qualquer forma, eu sempre quis remover componentes em massa de placas de PCB usando aquelas pistolas de ar quente que destroem tinta e destroem carvão. Mas eu não tenho o $$$ para isso também! Então pensei em fazer um ferro de solda que pudesse funcionar como uma pistola de ar quente e também um ferro de solda delicado. Então, depois de várias xícaras de café e muitos cigarros e muitas outras pesquisas no Google, eu tinha no fundo da minha mente uma ideia de todos os gadgets de que precisava para conseguir um ferro de solda funcionando … para o lixão local. Eu amo o lixo… tanta coisa útil e barata também !! Muito parecido com entrar em uma loja de ferragens para navegar pelas janelas. $ 10 dólares ozzy mais tarde, eu deixei o lixão com 2 laptops e três pistolas de ar quente para remoção de tinta. As armas já tinham visto dias melhores e eu não tinha muita esperança de conseguir deles algo que pudesse funcionar. Os laptops que estou guardando para as telas de LCD que usarei para o meu projetor de filmes DIY:) Mas esse é outro projeto. Em casa, separei os canhões de ar. Eu amo separar as coisas … algo do qual nunca cresci quando era criança. DESCULPE, mamãe e papai !!!
Etapa 2: o ventilador

Parte da montagem do ventilador dos sopradores do removedor de tinta. Ventilador de 17 VCC mostrado aqui. Tirei a ponte retificadora e o capacitor e usei esse tipo de ventoinha, pois era tudo o que eu tinha para fornecer ar para o ferro de solda. Posteriormente, esta foi uma situação de sorte, pois eu tinha a quantidade certa de fluxo de ar passando e em contato direto com o elemento de aquecimento.
Etapa 3: Unidade do soprador
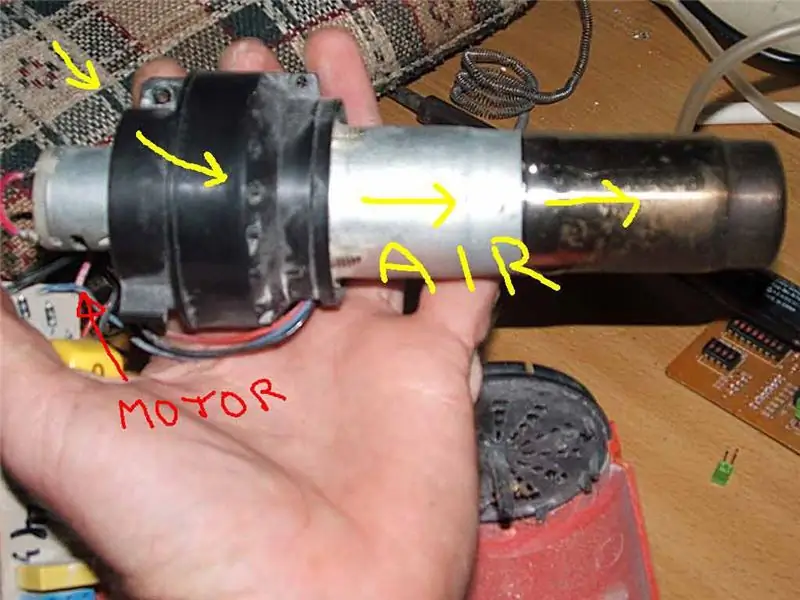
Esta é a unidade de soprador essencial que fornece ar frio através do elemento de aquecimento. Usei toda essa montagem como meio de bombear o ar. Não tinha ideia de como conectaria essa coisa.
Etapa 4: Elemento de aquecimento
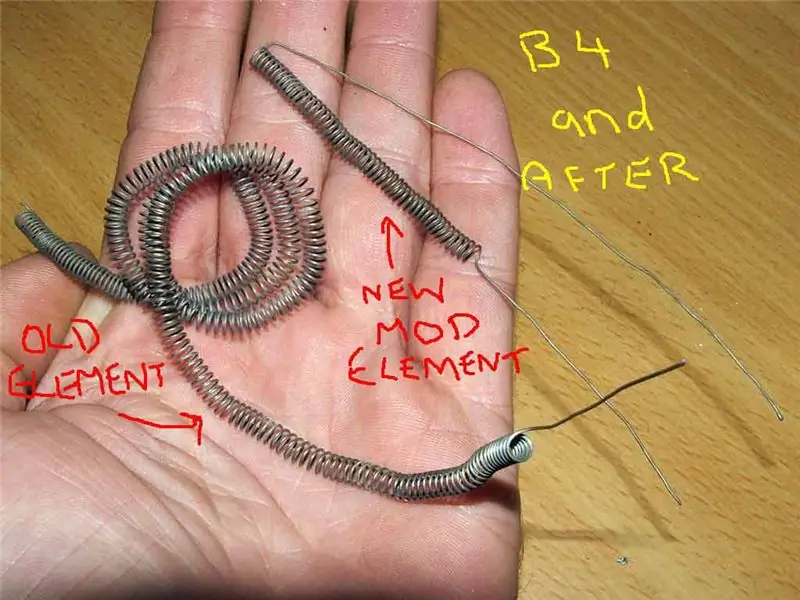
Não se esqueça do elemento de aquecimento. Ao fazer longos comprimentos de arame reto, dobre as curvas e certifique-se de não ter dobras acentuadas. Current não gosta de curvas fechadas. VISÃO GERAL: Eu descobri que dois ventiladores estavam com os rolamentos gastos e um estava ótimo. Eu tinha dois elementos de aquecimento quebrados e alguns discos e tubos isolantes de cerâmica. Realmente não há muito para esses bebês … me faz pensar por que eles são tão caros. Tudo o que eles são é um elemento de aquecimento e um motor. Uma ponte retificadora ficava entre a tensão de alimentação CA e o motor do soprador de ar. Isso foi encorajador, pois eu queria ligar minha fonte de alimentação para a ideia na minha cabeça com baixa tensão CC. Não gosto de brincar com a rede elétrica de 240 volts AC. Os motores foram classificados para 17 volts DC. Isso é perto o suficiente dos meus desejados 12volts DC. Liguei meu ventilador escolhido que não tinha rolamento e funcionou. Kewl. Também vi que uma das armas tinha cilindros ocos de cerâmica que eram usados para segurar os elementos de aquecimento. Inseri um dos cilindros em meu tubo de metal de solda. Ele se encaixou perfeitamente. Isso também foi muito encorajador. Eu ainda não tinha ideia de como seria a ideia final. Seja adaptativo e use o que está disponível é o meu lema. Eu já havia puxado meu ferro de soldar morto também para ver como funcionava e se poderia consertá-lo. Seu elemento foi recheado. Também notei que dependia de aquecimento condutivo para aquecer a ponta. Meu conceito desde o início era passar ar frio pelo cilindro oco, expô-lo a um elemento de aquecimento e expulsar o ar quente pela ponta. Muito parecido com um mini decapante de tinta de ar quente. Esse conceito nunca mudou, mas as ideias de como eu cheguei a esse fim mudavam constantemente, à medida que desenvolvia inúmeras novas ideias com o que tinha à minha frente na minha bancada de trabalho.
Etapa 5: Close Up do Elemento
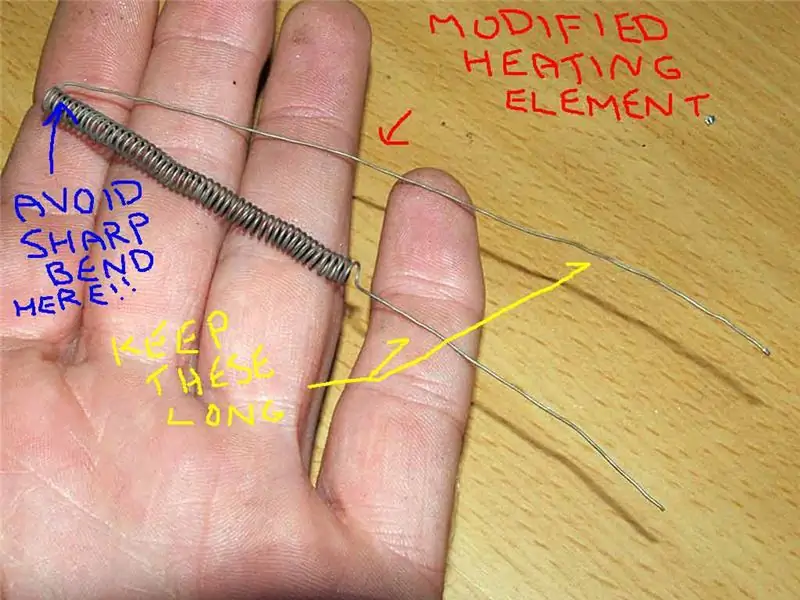
A ideia de manter os comprimentos retos longos é ter algum espaço para brincar ao colocá-los todos juntos. O comprimento final decidido foi ligeiramente maior do que este. Eu coloquei um curto-circuito na bateria de 12 volts e, embora a bateria estivesse meio descarregada, consegui obter um pouco de calor kewl dela. Achei que alguns comprimentos extras de bobina podem ajudar a dessensibilizar os fluxos de temperatura durante pequenas mudanças de tensão.
Etapa 6: tubo de cerâmica
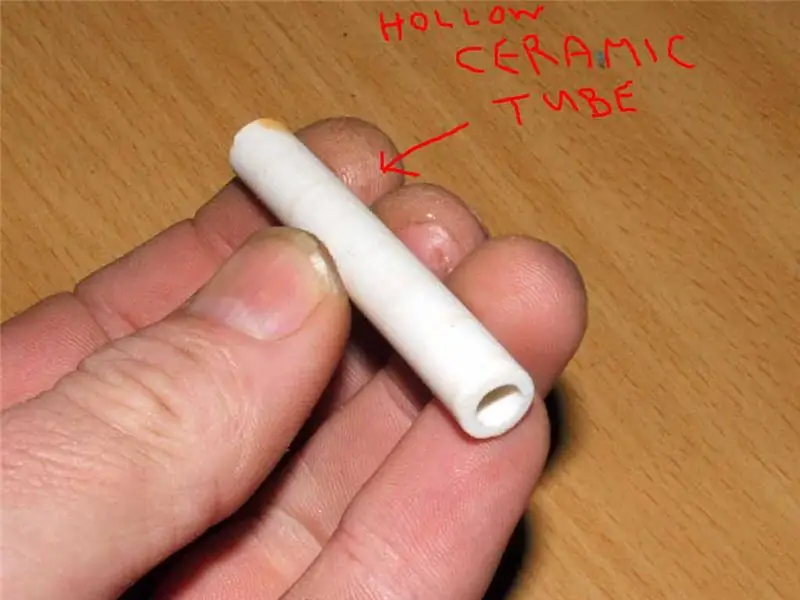
Achei que este tubo seria a melhor coisa desde bacon e ovos, não fiquei desapontado:) Esta é uma das hastes isolantes usadas para separar os elementos de aquecimento uns dos outros dentro das pistolas de ar quente. O elemento correu para fora desta haste. Meu objetivo era colocar o elemento dentro da haste e ter ar frio passando por ele e ar superaquecido saindo por ele. Como tudo isso aconteceria, eu ainda não tinha ideia … exceto algumas imagens selvagens de como o produto final poderia ser e ser parecido.
Etapa 7: O elemento e o tubo de cerâmica
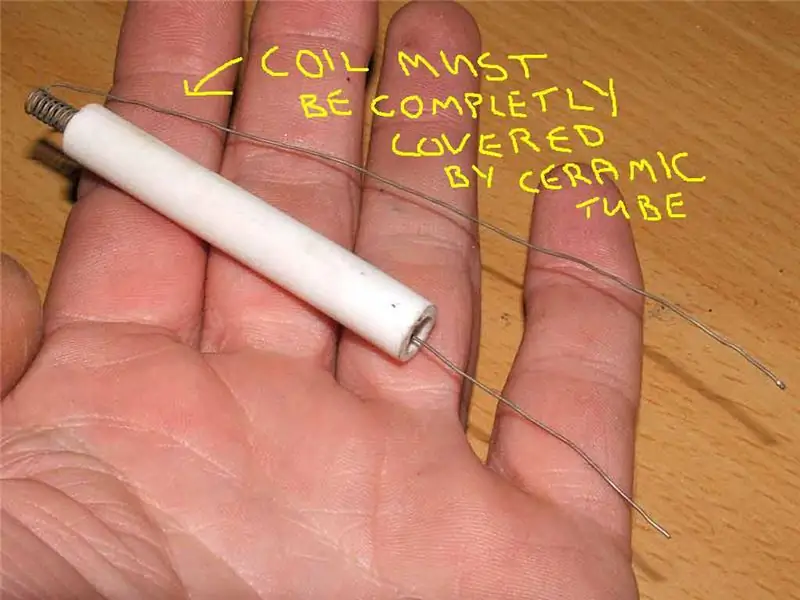
Este é essencialmente o fim operacional de tudo. VISÃO GERAL: Primeiro, eu precisava de um elemento de aquecimento. Achei que poderia reduzir o tamanho dos elementos de aquecimento quebrados classificados para 240 volts CA para caber dentro do tubo de cerâmica e fazê-lo funcionar silenciosamente bem com 12 volts. A amperagem era um problema para se preocupar e poderia ser corrigido variando o comprimento da bobina para obter a saída de calor desejada. Bobina demais e terei de usar mais volts e / ou amperes … muito pouco e superaquecimento a bobina e rompi o link. Eu experimentei alguns comprimentos de bobina usando a energia de minhas pequenas baterias de chumbo-ácido de 12 volts e encontrei um comprimento que emitia calor suficiente (145 graus centígrados) como valor inicial. Inseri a bobina no tubo de cerâmica, garantindo que não houvesse curvas acentuadas e fios retos suficientemente longos saindo da bobina. Os comprimentos longos deveriam me dar espaço suficiente para brincar quando eu fosse colocar esse bebê dentro do cabo do meu ferro de soldar. Além disso, os comprimentos longos me permitiram colocar o elemento de aquecimento mais longe da alça do ferro. Parece que todo o ferro de solda foi feito para ter engenharia reversa para uso com fluxo de ar quente. Percebo que outras pessoas na web tiveram pensamentos semelhantes.
Etapa 8: The Gutz
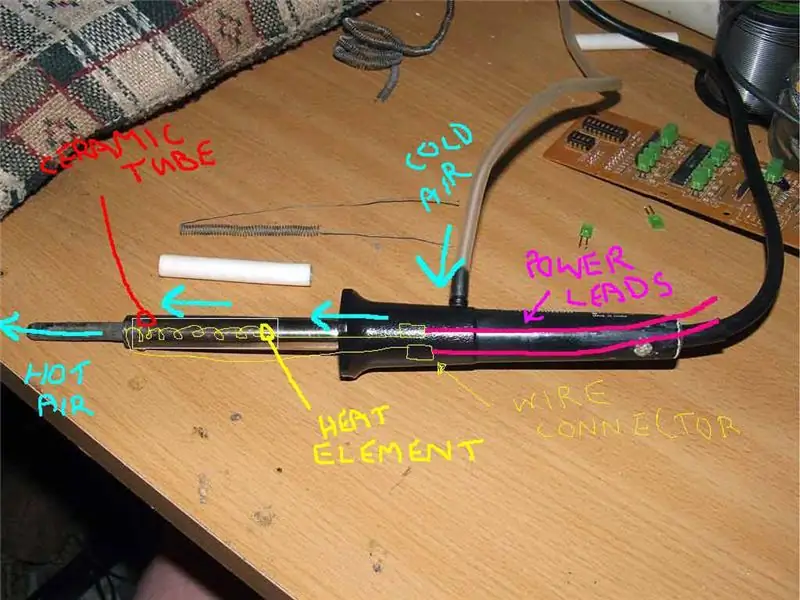
O básico de tudo. Na verdade, não muito. Mas muito eficaz além do que eu esperava. VISÃO GERAL: com o elemento dentro do eixo da solda, percebi que precisava isolar o cabo que subia do lado de fora do eixo do invólucro de metal. Eu tinha vários tamanhos diferentes de tubos isolantes de calor para consertar isso. Em seguida, tive que remodelar o eixo levemente em uma forma oval para encaixar o elemento de aquecimento de cerâmica com o tubo de isolamento térmico de fio adicionado. A próxima etapa foi ver se eu ainda poderia fazer com que o ar passasse pelo elemento com o isolamento adicionado. Eu podia ver uma luz através do outro lado do poço que me dizia que estava tudo bem. Agora, a parte fácil era usar os conectores de terminal de fio usados anteriormente pelo ferro para unir as extremidades do elemento de aquecimento às extremidades do fio de energia da bateria. Usei o cabo AC de 240 volts usado anteriormente para o ferro, pois queria um fio grosso capaz de lidar com alguns amperes.
Etapa 9: o bocal
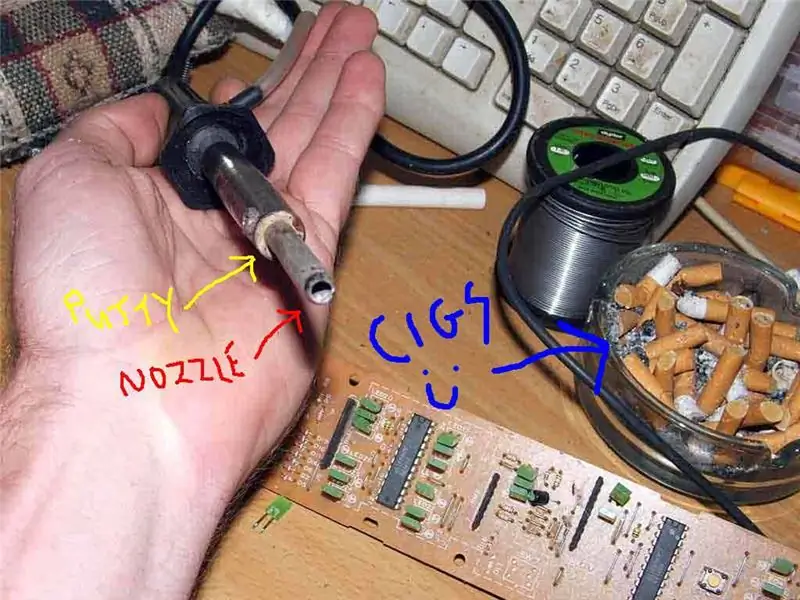
O bico é na verdade o que ficava dentro do ferro. O elemento de aquecimento para o fornecimento de 240v AC foi enrolado em torno disso e a haste de aquecimento de cobre usada para soldar o material ficava dentro do tubo oco. VISÃO GERAL: marquei na alça da tampa de plástico onde haveria um espaço oco para eu perfurar um orifício e insira um pouco de tubo uma vez que a unidade estava montada. Mais tarde, o ar seria bombeado por esse tubo. Foi importante acertar isso, então usei compassos e algumas marcas para obter o comprimento certo. O próximo problema que encontrei foi conseguir um bico para a ponta. Eu inverti o eixo interno usado anteriormente para segurar o elemento de aquecimento e dremel o flange e ele se encaixou perfeitamente. Agora tenho um bico !! O próximo passo foi usar um bico do meu aquário que se encaixaria na alça e encaixaria também no tubo de plástico que terá o ar fluindo por ele. Fiz um furo onde o "X" marcava o local, tomando cuidado para não pressionar muito a broca. Eu teria feito isso com o gutz removido, mas senti que poderia escapar sem perfurar as vísceras se tivesse cuidado. Esse arranjo funcionou, mas é apenas temporário, pois quero ver se o conceito funcionou. Posteriormente, adicionarei alguma retenção mecânica aqui, usando um bico de rosca ou algo assim. Com o ferro de solda quase totalmente unido, eu precisava resolver o problema de colocar ar na coisa. Não tinha bomba de ar usada para aquário. Eu tenho um aquário, mas não uso, são tão ineficientes. O que eu tenho são os péssimos sopradores de ar das pistolas de ar quente que peguei no depósito de lixo. Esses bebês são enormes em comparação com o pequeno tubo que tenho que colocar no ferro de solda.
Etapa 10: estaca quadrada em um orifício redondo
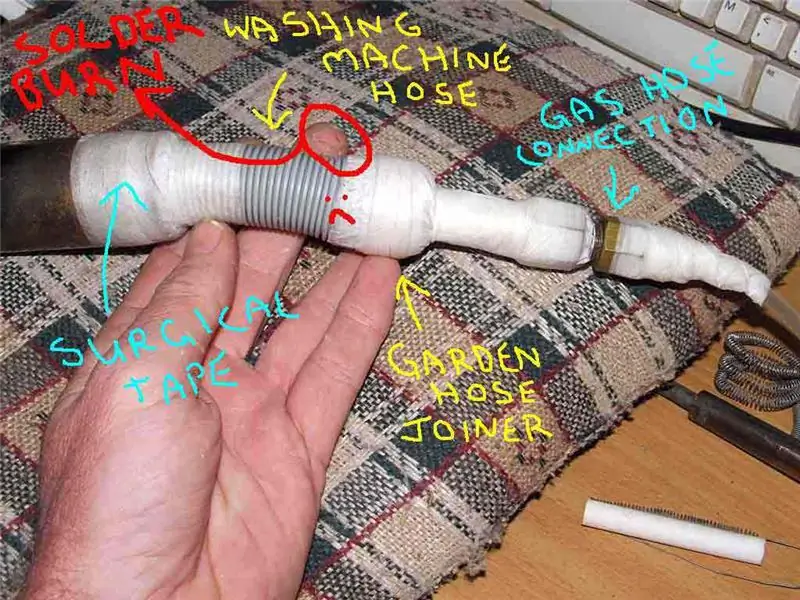
Meu maior desafio foi decidir como encaixar minha pequena mangueira em uma enorme saída de soprador com o que eu tinha pela casa. VISÃO GERAL: Eu viajei para o galpão de trás e juntei todos os tubos e bitz que achei que seriam úteis e comecei a encaixar um pino quadrado em um orifício redondo. Acabei usando um pedaço de tubo de uma velha máquina de lavar, um conector de mangueira de jardim, um pequeno pedaço de tubo de 1/4 de polegada e um bico de gás de latão e pilhas de esparadrapo. Liguei o soprador de ar e peguei uma boa brisa de ar forte no final do tubo. O projeto será corrigido posteriormente em relação às obstruções ao fluxo de ar, etc. que existem com esta engenhoca. Pretendo trabalhar no efeito venturi para aumentar ainda mais a saída de ar no bico sem aumentar a velocidade do ventilador. Em seguida, simplesmente enganchei o pequeno tubo no mamilo que se projetava da alça do ferro de solda.
Etapa 11: todas as coisas estão aqui
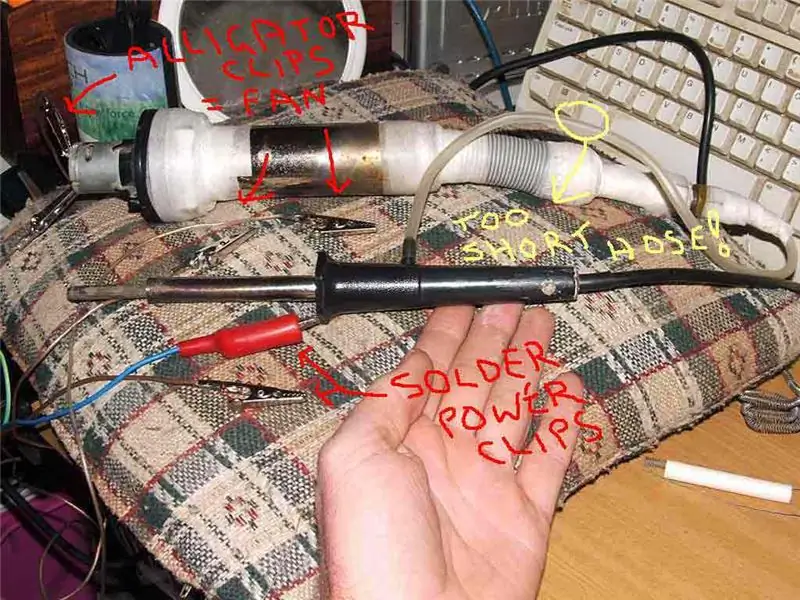
O soprador e o ferro de solda são tudo o que há para fazer isso.
Etapa 12: Soprador de vela:)
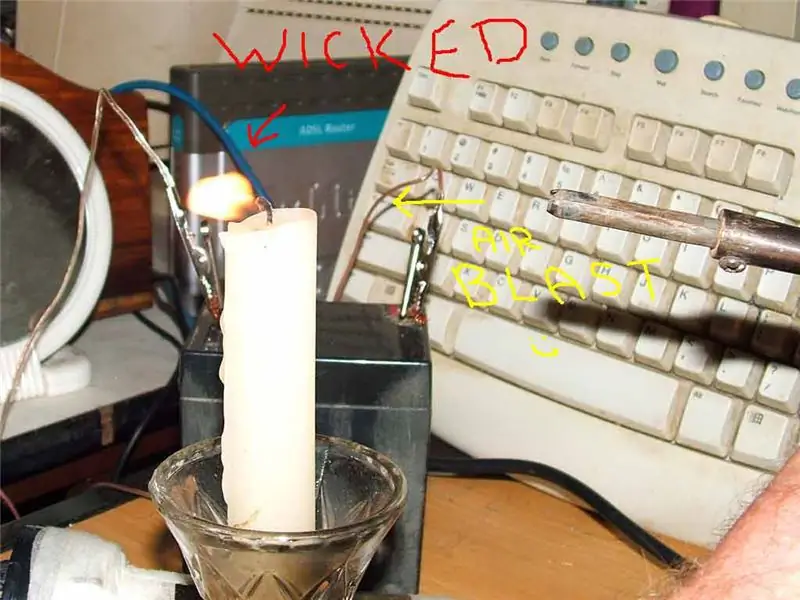
A força do ar quente é a chave para remover todo aquele calor bom do elemento de aquecimento dentro do ferro de solda. A tentativa e erro devem fornecer a quantidade certa de fluxo de ar através do elemento de aquecimento que irá efetivamente aquecer o ar frio soprado na câmara de aquecimento e fora do bico até a temperatura desejada. Um fluxo de ar muito rápido e o ar não terão tempo suficiente para aquecer aos níveis desejados. Acho que tive sorte, pois não precisava me preocupar com essa parte. O benefício adicional de ter uma bobina usada para aquecimento com ar fluindo para a câmara que contém o elemento de aquecimento, é que a turbulência resultante distribui o ar de maneira mais uniforme, reduzindo as perdas de energia durante o aquecimento do ar frio.
Etapa 13: Fonte de alimentação regulada
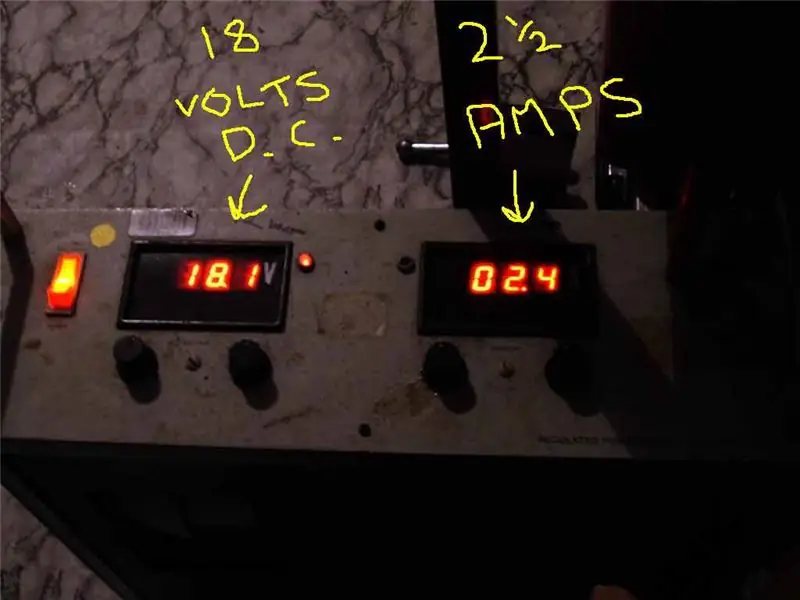
Este velho fiel ex R. A. A. F. unidade viverá além dos meus anos. Muitos recursos e feitos na Austrália. Esta é a estatística operacional de pico desejada que atingiu 310 graus centígrados. Levei menos de 15 segundos para atingir essa temperatura de uma inicialização a frio. Muito melhor do que esperar vários minutos para um ferro de solda padrão aquecer. Observo que a 16 volts, a temperatura de pico estava em 270 graus centígrados ímpares. A 18 volts, a temperatura de pico foi de 310 graus centígrados. Portanto, posso calcular a matemática para prever as faixas de temperatura que saem do bocal em tensões e amperagens variadas. A distância linear entre essas faixas é determinada pela bitola do fio do elemento, seu comprimento e também o CFM do fluxo de ar através do bico.
Etapa 14: Temp # 1
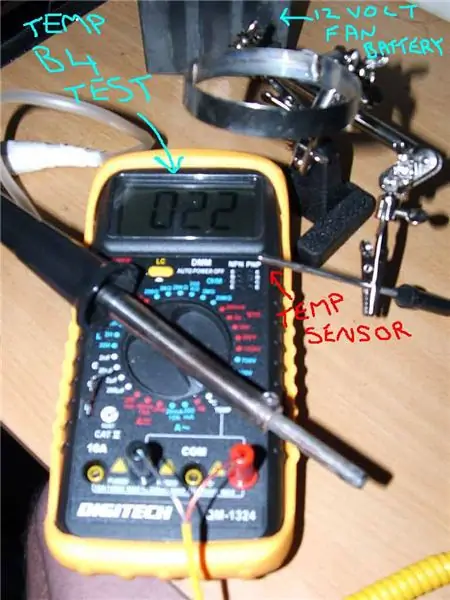
Temperatura ambiente. Pronto para o grande show … lol
Etapa 15: Temp # 2
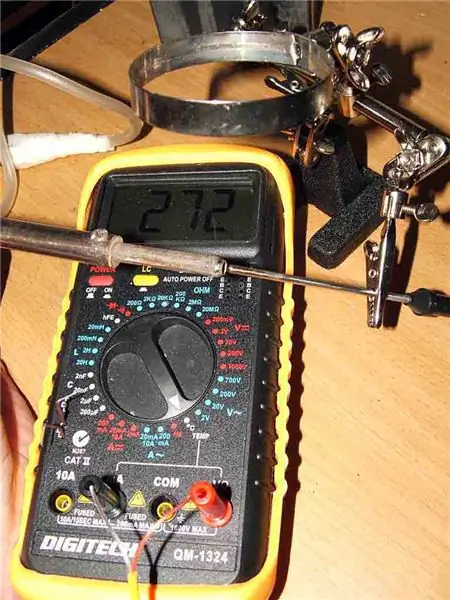
Ligado e subindo. Assistir a esses números aumentar foi uma verdadeira corrida. Percebi que o elemento dentro do poço ainda não estava brilhando quando olhei para o bico, mostrando que poderia atingir temperaturas substancialmente mais altas antes da falha do elemento, usando o fio do elemento de aquecimento das pistolas de ar quente de tinta destruídas. Depois de fazer uma peça de trabalho mais permanente, farei experiências com vários diâmetros de bico, pois acho que um bico menor seria excelente para remover componentes únicos e um bico mais largo para chips IC e outras coisas.
Etapa 16: Temp # 3
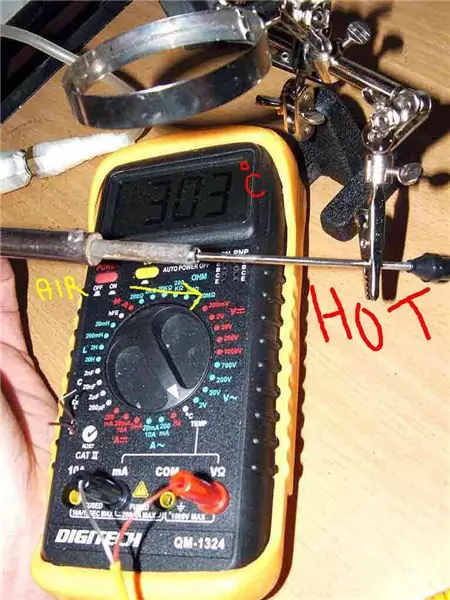
Eu tenho mais de 310 graus centígrados. Poderia ter conseguido mais, mas não era necessário para o que eu pretendia usar este bebê. Também estava ficando paranóico demais com relação a ver esses números aumentarem … Resumo Geral: Liguei o soprador e encontrei vários vazamentos de ar. Eu os lacrei com massa sólida de fixação. A hora da verdade está próxima. Agora eu precisava de uma fonte de energia. Pensei em pequenos transformadores, mas queria fornecimento variável de voltagem e amperagem, para que pudesse descobrir as condições de operação de pico. Peguei meu velho regulador de voltagem AUSTRALIAN MADE (ex-estoque R. A. A. F.) e o conectei ao meu ferro. Todo o material feito hoje que recebemos é feito na China e não é confiável como o diabo. Este bebê foi feito para durar e funcionar. Eu tinha o ventilador conectado à minha bateria separado do elemento de aquecimento de solda. As razões eram óbvias:) Acendi um cigarro e me preparei para o pior … comecei com baixa tensão DC … os amplificadores são calibrados automaticamente pelo regulador. Deixei meu multímetro de lado para medir a temperatura do ar quente. Para encurtar a história (risos), a 16volts DC e pouco mais de 2 amperes… a temperatura alcançada foi de 275 graus centígrados… KEWLIES !!! Eu alcancei minha temperatura desejada. Cortei um fio de solda de 1 mm como queijo suíço. Consegui remover LEDs de uma placa de circuito impresso sem nem mesmo fritá-los ou meus dedos que seguravam os LEDs do outro lado da placa. O eixo de metal do ferro de solda estava muito MAIS FRESCO do que quando operava com menos de 240 volts. Eu poderia tocar a haste de metal sem queimar os dedos. Estava bastante quente onde o elemento está, mas ainda assim muito mais frio. O que torna a minha diferente das outras criações que vi na WWW? Eu tenho um elemento de aquecimento em espiral com uma grande área de superfície de bom calor (risos) que tem ar frio passando diretamente por eles. As outras unidades que vi usam o elemento de aquecimento do ferro de solda original, uma haste condutora de cobre que absorve o calor do elemento e envia o calor para a ponta, um pouco de tela de arame na cavidade de ar para aumentar a exposição da superfície ao ar frio exposto ao calor. Removi todas aquelas barreiras condutoras e aumentei a eficiência aos montes.
Etapa 17: Fio de solda derretendo
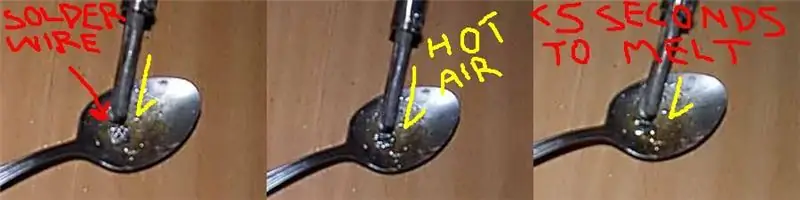
Derreteu esta bola de arame de solda como sorvete no sol de verão
Etapa 18: Primeiro trabalho
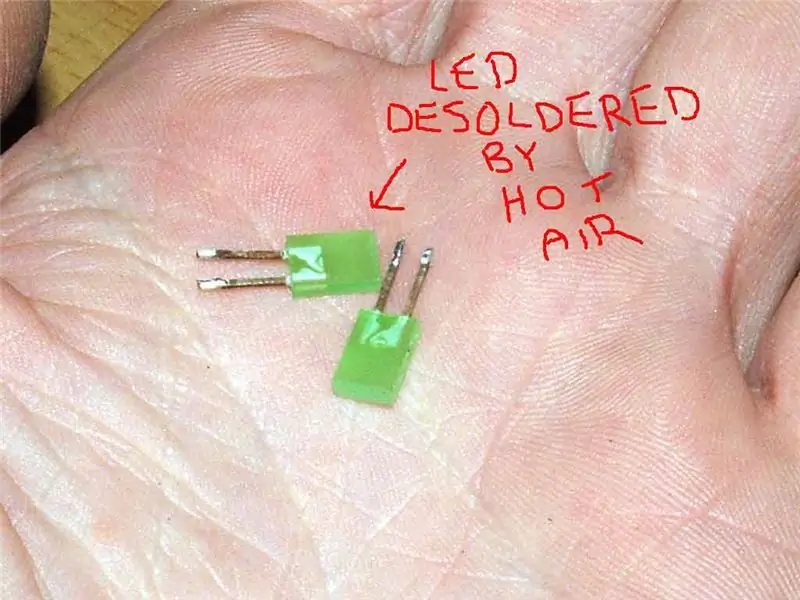
Eu removi isso de um PCB antigo em um piscar de olhos. VISÃO GERAL: Assim que eu conseguir um tubo de plástico mais longo e retrabalhar este protótipo em um arranjo mais permanente, terei peças sobressalentes suficientes para cuidar desse bebê nos próximos anos. As melhorias que farei são ajustar as configurações de temperatura por meio de potenciômetros de compensação e usar meus outros bitz e peças para montar um painel LCD com configurações exibidas como temperatura, tensão e amperagem e, claro, alguns fusíveis e talvez um capacitor no motor. Eu já conheço a condição operacional média e posso ajustar de acordo a partir daí. Um ponto a lembrar é que ao desligar a unidade, desligue primeiro o elemento, deixe o ar passar por um minuto para resfriar a unidade. Implementarei um cronômetro para este bit mais tarde. Claro que não posso fazer isso sem um ferro de solda funcionando, mas agora tenho um …
Recomendado:
Lente macro faça você mesmo com AF (diferente de todas as outras lentes macro faça você mesmo): 4 etapas (com fotos)
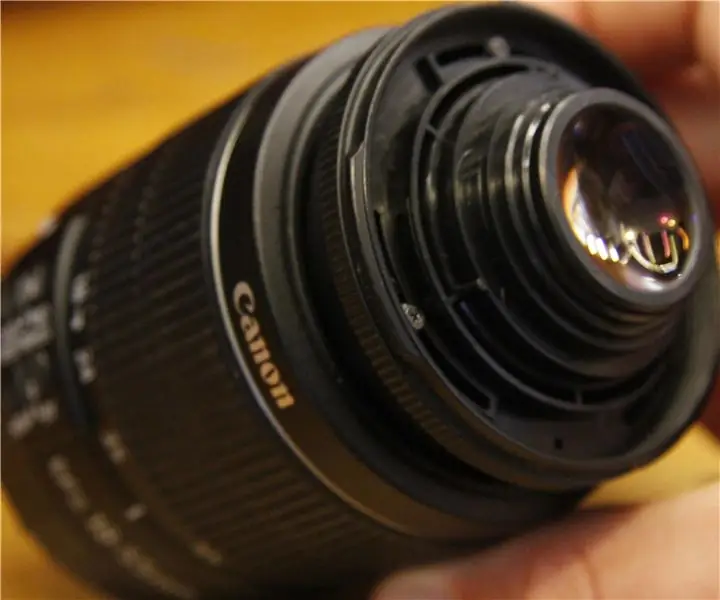
Lente macro faça você mesmo com AF (diferente de todas as outras lentes macro faça você mesmo): Já vi muitas pessoas fazendo lentes macro com um kit de lentes padrão (geralmente de 18-55 mm). A maioria deles são lentes fixadas na câmera ao contrário ou com o elemento frontal removido. Existem desvantagens para ambas as opções. Para montar a lente
Faça você mesmo uma maneira barata e fácil de estanho seu PCB usando o ferro de solda: 6 etapas
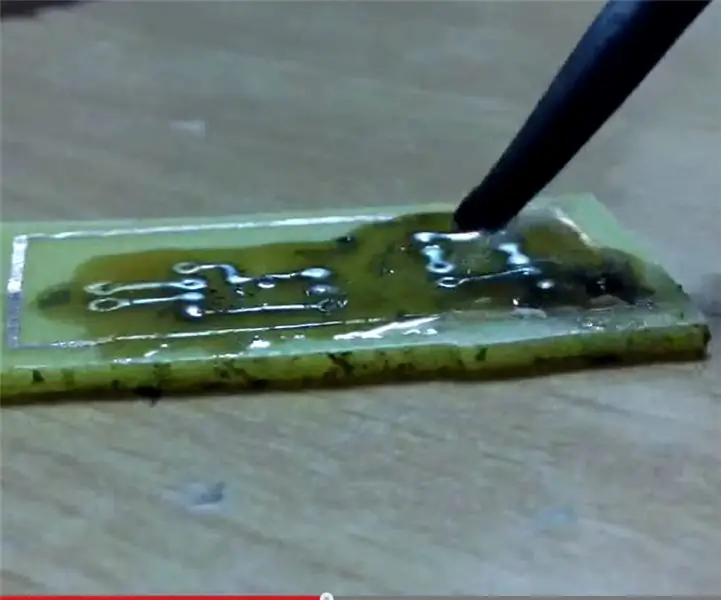
Faça você mesmo uma maneira barata e fácil de estanhar seu PCB usando ferro de solda: Quando eu era um iniciante em impressão de PCB e soldagem, sempre tive o problema de que a solda não grudava no lugar certo ou os vestígios de cobre se rompiam, ficavam oxidados e muitos mais . Mas me familiarizei com muitas técnicas e hacks e um deles foi
Construir um Mini Sistema Hidropônico Faça Você Mesmo e Jardim de Ervas Hidropônico Faça Você Mesmo com Alertas de WiFi: 18 etapas
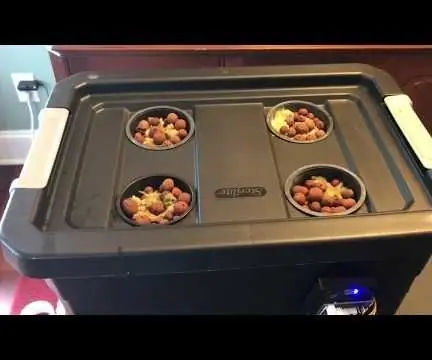
Construa um Mini Sistemas Hidropônicos DIY e Jardim de Ervas Hidropônico DIY com Alertas de WiFi: Neste tutorial, mostraremos como construir um sistema #DIY #hidropônico. Este sistema hidropônico DIY regará em um ciclo de irrigação hidropônico personalizado com 2 minutos ligado e 4 minutos desligado. Ele também monitorará o nível de água do reservatório. Este sistema
Atualize a panela de autorregulação faça você mesmo com Wi-Fi em um alarme de sentinela de detecção de movimento faça-você-mesmo plantador: 17 etapas
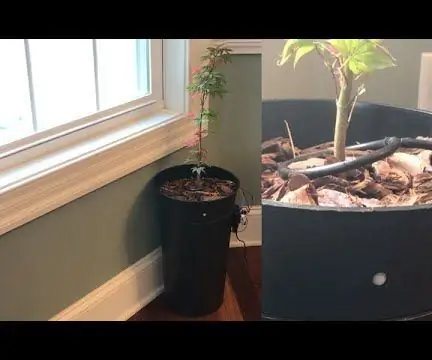
Atualize a panela self-watering DIY com Wi-Fi em um alarme Sentry de detecção de movimento DIY Plantador: neste artigo, mostraremos como atualizar sua panela self-watering DIY com WiFi para uma panela self-watering DIY com Wi-Fi e alarme Sentry de detecção de movimento. Se você não leu o artigo sobre como construir uma panela autônoma do tipo faça-você-mesmo com Wi-Fi, pode encontrar
Faça uma faca quente usando um ferro de soldar: 4 etapas (com fotos)
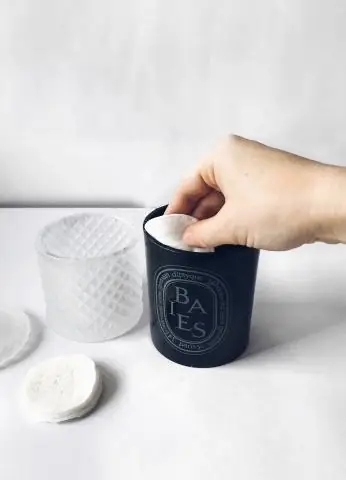
Faça uma faca quente usando um ferro de soldar: Você está tendo problemas para cortar plásticos com uma faca comum? Então aqui está um mod de ferramenta simples que você pode fazer, transformar um velho ferro de soldar e uma lâmina x-acto em uma faca quente! Esta ideia de faca quente não é realmente minha, achei essa ideia feita por alguém