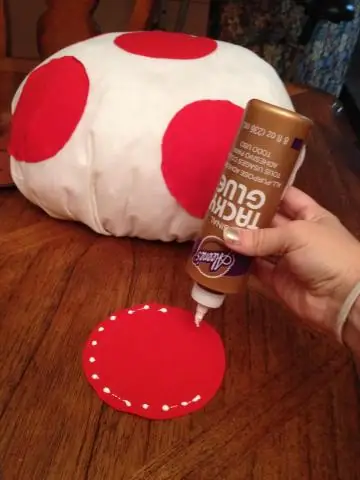
Índice:
2025 Autor: John Day | [email protected]. Última modificação: 2025-01-23 15:04
De um recurso: Notas do curso de design de alto-falante + materiais de vídeoNo passado, os serviços de reparo de alto-falantes eram escassos, muitas vezes caros, e a substituição de surrounds para DIY quase impossível de obter. A web melhorou isso, os arredores estão amplamente disponíveis, mas de qualidade variável. Mesmo assim, para alguns drivers Hi Fi antigos de tamanho incomum, surrounds genéricos de boa qualidade de tamanho adequado ou peças OEM com preços razoáveis não estão disponíveis. Os arredores do alto-falante feitos de espuma podem se deteriorar, especialmente em condições de umidade quente. Com menos frequência, os de borracha podem morrer ou rachar. Os arredores recentes às vezes são feitos resistentes aos climas tropicais e ultravioleta. Quando confrontados com altos custos de mão de obra, muitos estão preparados para lidar com a substituição DIY, e ambientes OEM ou genéricos, bem como guias de instruções, estão disponíveis na web. Se estiver fazendo uma restauração completa, o custo de uma peça OEM (surround, kit recone ou driver) pode ser justificado, para modelos vintage altamente valorizados. Drivers exóticos de gama completa e alto-falantes de reforço de som geralmente requerem especialistas. Para outros sistemas, bons sistemas, sem nenhum valor particular, e onde um substituto adequado não pode ser encontrado, criando o próprio surround, podem ser considerados. Não pode ser justificado em termos de $, mas pode ser abordado como uma experiência de aprendizagem única, reciclagem útil e um novo conjunto de habilidades, ou um suprimento potencial de cerveja de outras pessoas, caso se espalhe que você se tornou bom nisso. O driver pode não funcionar exatamente como o original, mas nos casos experimentados aqui e na maioria dos outros a frequência de ressonância e a resposta foram próximas, devido a alguma experiência no que procurar. A borda é um material impregnado de um lado (o lado não colado) com uma pequena quantidade de borracha de silicone apenas o suficiente para ser hermético e formado em um molde com um agente de desmoldagem para que não grude. A confecção do molde requer acesso a algumas máquinas e leva mais tempo, mas depois de feito, pode ser reutilizado para o mesmo tipo de driver. Os drivers mostrados aqui são vintage dos anos 80; um modelo Technics SBX e um Dynaudio 21W54, bons pilotos em sua época. Alguns drivers, por exemplo, JBL vintage, têm folga da bobina de voz muito pequena, que pode exigir a remoção da tampa de poeira e o uso de calços para centralização precisa. Se um sistema tiver um histórico desconhecido ou não for usado por um tempo, vale a pena verificar os componentes do crossover e outros drivers do sistema inicialmente. Verifique se não há danos às bobinas de voz antes de prosseguir. Praticar em um driver não crítico e fazer um novo surround quando uma tentativa anterior não saiu como o esperado, antes da montagem vale a pena. Vale a pena dar muita atenção à remoção de todos os restos da moldura antiga e da cola, para um resultado de boa aparência.
Etapa 1: Preliminares
Se o antigo contorno frágil estiver quase intacto, você pode estimar sua espessura e medir suas 4 dimensões, normalmente A B C D em uma guia de rede, para configurar os diâmetros interno e externo do molde, bem como a largura das partes planas. A largura do rolo é importante, mas se o contorno estiver ausente, estime C e B com a maior precisão possível com A e D adequados para fins de fixação. Alguma pesquisa na web ou inquérito a fóruns de áudio, pode revelar imagens ou dimensões para passar. Cones pesados de um 3 Way com curso de cone mais longo (Xmax) podem ter bordas de borracha ou de espuma um pouco mais espessa. com um rolo mais largo, em comparação com rolos mais estreitos em cones mais leves com uma resposta estendida e de Xmax mais baixo de, digamos, sistemas ventilados de 2 vias. Drivers de gama completa exóticos / vintage devem ser deixados para especialistas ou fóruns on-line DIY dedicados. C às vezes tem uma pequena saliência deliberada além da borda do cone por motivos de desempenho. Observe a polaridade dos fios antes de removê-los da caixa. Para aqueles com o equipamento, e curiosos sobre as comparações antes e depois, pode-se medir a freqüência de resposta do driver fora da caixa e a resposta na caixa, com e sem o crossover na faixa média e superior, apesar dos prováveis vazamentos de ar. Mas não é obrigatório apenas para fazer um sistema funcionar novamente. Na maioria dos casos, se o plano interno não estiver inclinado, ele ainda pode ser colado satisfatoriamente na parte superior ou inferior do cone quando a cola (PVA de reparadores de alto-falantes) está no estágio pegajoso.
Etapa 2: Fabricação de molde, parte 1
O molde é feito de uma placa circular de MDF de 25 mm de espessura girada a baixo RPM em um torno de madeira ou outro equipamento adequado. Precauções contra o pó se aplicam. Tenha cuidado, você tem um suporte resistente para a ferramenta de escultura e com espaços em branco de diâmetros maiores. Se um novato usar uma empresa de marcenaria local ou instalações em uma faculdade de comércio, pode ser aconselhável. Após o lixamento final, bastam algumas camadas de acrílico brilhante.
Etapa 3: Parte do Gesso do Molde Parte 2
A parte de MDF é cercada com fita de embalagem larga na borda externa, o orifício central coberto com fita adesiva e toda a superfície coberta com vaselina sem protuberâncias ou saliências. O gesso para moldagem é derramado (textura cremosa com cerca de 20 mm de espessura) batido para estimular a formação de bolhas na superfície e pode se fixar em uma superfície nivelada, para que não fique úmido e de cor branca, possivelmente durante um ou dois dias, para ter certeza, o a última parte da secagem pode ser feita com a fita removida. Marque onde as 2 peças estão alinhadas. Bata suavemente no mdf ao redor para liberar as 2 partes. Suavizar / preencher quaisquer bolhas de ar. Também pode ser aplicada uma camada fina de acrílico brilhante.
Etapa 4: Acabamento surround e fixação
O revestimento do material interlock de algodão elástico pode usar silicone de 2 partes de viscosidade média, aplicado finamente com um pincel, funciona melhor, pois tem uma vida útil mais longa e flui um pouco, mas custa mais. Se você quiser economizar, experimente o silicone do conjunto de ar para encanamento (em cartucho ou tubo de 300 gr) aplicado muito moderadamente com uma espátula, mas você tem que trabalhar muito rapidamente e o acabamento da superfície tende a ser irregular nas primeiras tentativas. VENTILAÇÃO e luvas de plástico são precauções úteis. Consulte a web para obter os agentes desmoldantes adequados ou pode tentar um filme plástico em cada lado do molde. Durante a configuração, alinhe as 2 partes do molde da forma como foram separadas originalmente. Aplique pressão suficiente uniformemente, mas não tanto a ponto de correr o risco de rachar o gesso. Um número de clipes de mola grandes pode ser suficiente, ou peso pesado (10s de KG para 10 - 12 pol.) Em uma superfície plana. Deixe durante a noite ou por mais tempo para 2 partes, corte no tamanho com uma tesoura afiada ou lâmina de aparar. Avalie o resultado quanto ao peso, (geralmente o mais leve possível, massa semelhante à espuma original é possível), aparência e, para não vazar mais tarde, quando exposto à luz, uma pequena pincelada de silicone servirá se houver algum. O PVA não adere ao silicone, portanto, o material de revestimento apenas no lado sem colagem. O silicone e algumas colas especiais irão aderir ao silicone de forma adequada, mas a remoção futura dos cones de papel é problemática. Se você revestiu o lado avesso do material, o silicone pode ser usado na moldura do driver para o contorno externo após a centralização ter sido totalmente verificada. As juntas de papelão ou cortiça na estrutura precisam de um planejamento caso a caso desde o início, resgate em uma única peça e, posteriormente, reinstalação. O rebordo abaixo foi rejeitado e mostra o que acontece quando muito é aplicado, ele permeia o lado da colagem e tem massa excessiva em comparação com o de espuma. As bordas de borracha mais pesadas e muito antigas podem rachar, por exemplo, Philips 10100 e 12100, então isso pode ser uma substituição se o aspecto da colagem for levado em consideração. Os drivers de gama completa com cones de papel muito leves como Philips AD4200M ou 9710 com uma moldura de papel corrugado, também têm um pequeno Xmax, o uso de uma moldura de rolo não é recomendado. Mas isso foi feito cortando-se o antigo contorno e usando um com um rolo estreito. Outro instrutível "Como refomar seu woofer" fornece detalhes extras de fixação surround. Proceda de acordo com os guias da web para fixação do driver, observando a orientação correta, ou seja, rolo para cima ou para baixo, colado na borda superior ou inferior do cone, etc. Assegure um deslocamento adequado do cone sem fricção. Verifique novamente os ohms do driver com um multímetro e Fres se necessário, antes da remontagem do sistema. Sente-se e aprecie ou receba a contribuição da cerveja.
Recomendado:
Alto-falantes DIY 50 Cents (SEM ELETRICIDADE!): 4 etapas
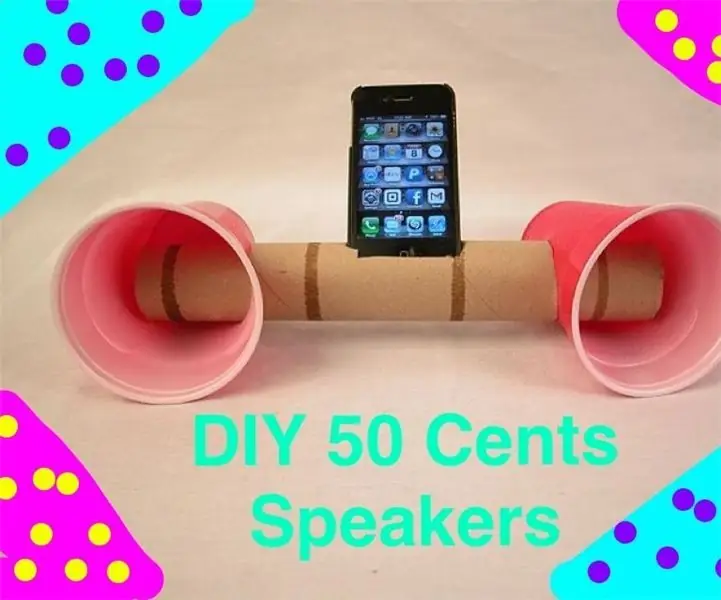
Alto-falantes DIY 50 Cents (SEM ELETRICIDADE!): Esses alto-falantes são uma maneira fácil e portátil de amplificar sua música! Além disso, a estrutura de papelão permite que você funcione sem eletricidade! Você pode desmontá-lo e remontá-lo novamente e novamente. Esses alto-falantes baratos vão economizar dinheiro e tempo
Alto-falantes de prateleira com dock para ipod (Parte I - Caixas de alto-falantes): 7 etapas
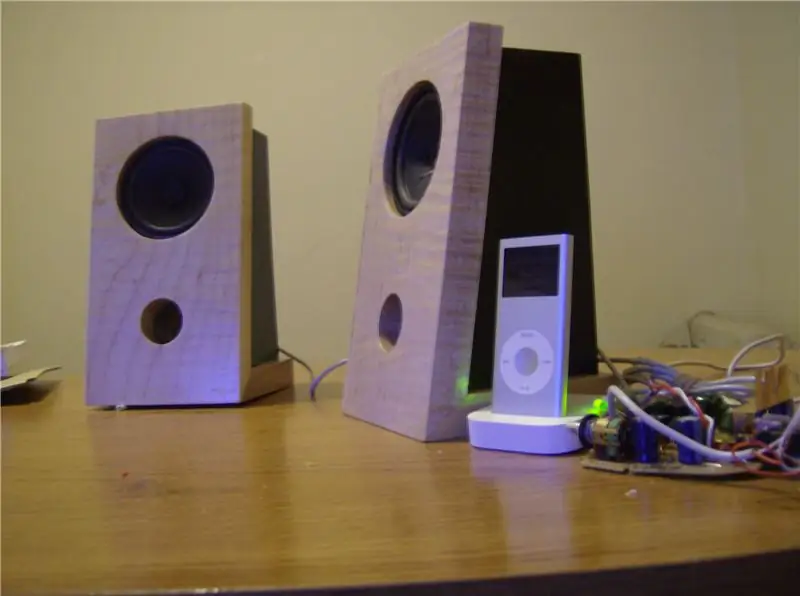
Alto-falantes de prateleira com dock para ipod (Parte I - Caixas de alto-falantes): Comprei um ipod nano em novembro e, desde então, queria um sistema de alto-falantes atraente para ele. No trabalho, um dia, percebi que os alto-falantes do computador que uso funcionavam muito bem, então fui ao Goodwill mais tarde e encontrei um par de alto-falantes ok por $
Adicionar lâmpadas de batida a seus alto-falantes portáteis ou alto-falantes de PC : 5 etapas
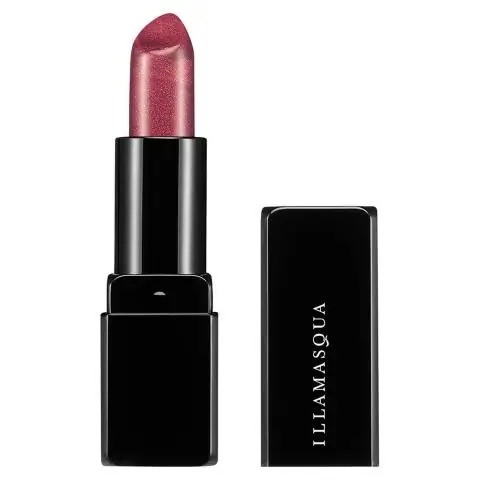
Adicione lâmpadas de batida aos seus alto-falantes portáteis ou alto-falantes do pc …: você já quis que seus pequenos alto-falantes de áudio portáteis ou alto-falantes do pc tivessem a mesma aparência de se você estivesse no clube ?? Bem, neste instrutível, mostraremos como obter sua fala através do site e do som do clube
Alto-falantes portáteis / alto-falantes com bateria: 7 etapas
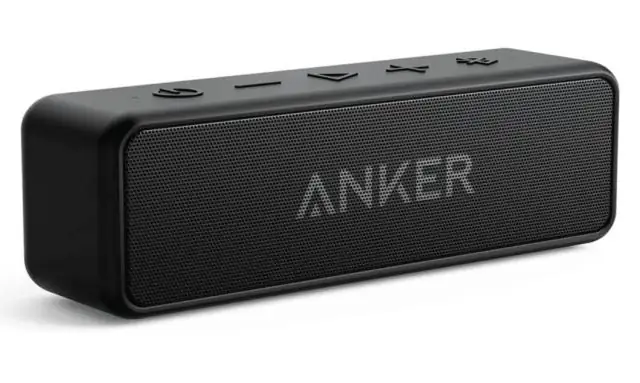
Alto-falantes portáteis / alto-falantes com bateria: Oi pessoal. Este é meu primeiro instrutível. Aproveite! Então, hoje vou mostrar a vocês como fazer de alto-falantes de pc antigos a alto-falantes com bateria. É bem básico e tenho muitas fotos .;)
Alto-falantes de teto montados em caixas de alto-falantes falsos: 6 etapas
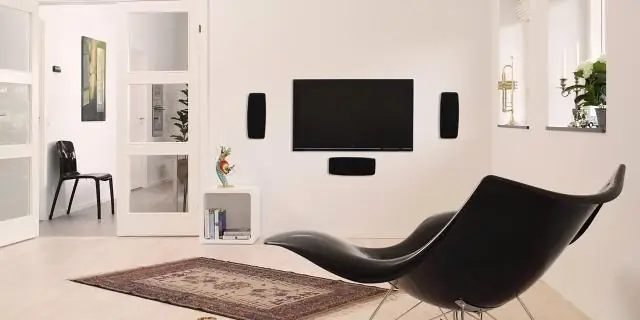
Alto-falantes de teto montados em caixas de alto-falantes falsos: A ideia aqui é usar um alto-falante de teto de alto padrão, adquirido com desconto em um site de leilão, reempacotá-lo para o dever de som surround. Aqui eu usei um EV C8.2. Vão no varejo por cerca de 350 $ o par. Comprei-os no Ebay por tão pouco