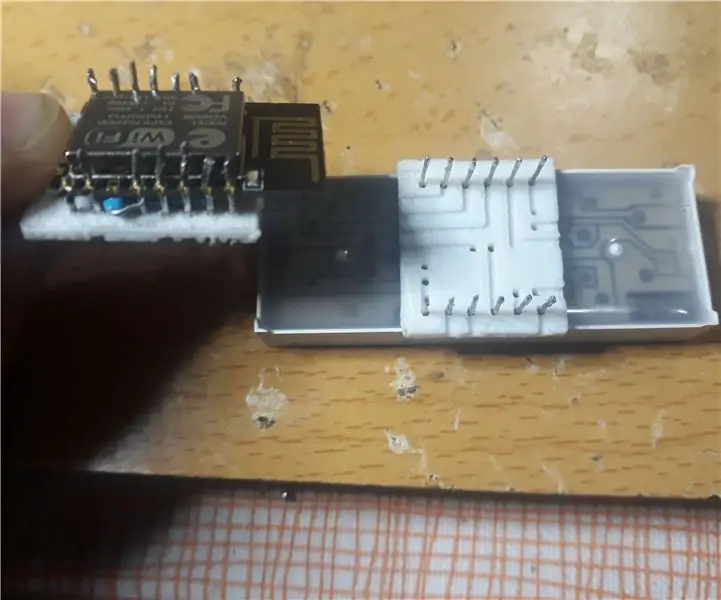
Índice:
2025 Autor: John Day | [email protected]. Última modificação: 2025-01-23 15:03
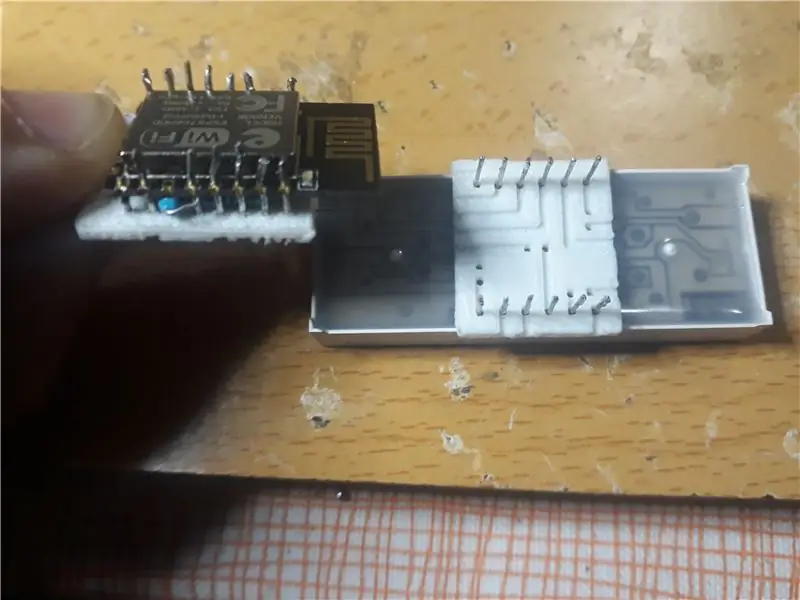
Quando consegui conectar um display de 4 dígitos e 7 segmentos ao meu Teensy, decidi que precisava começar a pesquisar sobre como fazer PCBs em casa de uma maneira mais fácil. A gravação tradicional é bastante entediante e perigosa, então rapidamente descartei isso. Uma boa ideia que tenho visto por aí são placas impressas em 3D que funcionam adicionando tinta condutora aos canais, mas isso parece bastante irregular para a condutividade. Existem também filamentos condutores especiais que você poderia usar em uma impressora de extrusão dupla, mas estou procurando algo básico e eficaz para o equipamento padrão que tenho.
Portanto, pensei em soldar diretamente e colocar componentes e conectores em impressões 3D.
Antes de começar, esteja avisado: estaremos imprimindo com ABS pois aguenta + 200ºC antes de deformar (para que possamos aplicar um pouco de solda com cuidado). Imprimir com ABS não é tão simples quanto com PLA, você precisa de uma impressora fechada e muitas configurações de calibração, mas quando você acerta, o resultado faz a diferença.
Para adicionar algum contexto, nos exemplos, estou criando uma PCB para a placa wi-fi ESP8266 12E para que possa conectá-la facilmente a qualquer outra coisa mais tarde (o objetivo final é uma tela 4d7seg).
O PCB me permite usar todos os seus pinos disponíveis, enquanto a maioria dos módulos por aí tem poucos pinos sobressalentes, ou tem muitos recursos adicionais que eu realmente não quero (como o NodeMCU).
Suprimentos
- Software de design de PCB (KiCad aqui, grátis). Nível inicial.
- Software de modelagem 3D (Blender aqui, grátis). Nível de usuário.
- Uma impressora 3D (Creality 3D Ender 3 Pro aqui, cerca de 200 €). Nível de usuário.
- Um invólucro para a sua impressora é fortemente recomendado ao usar o ABS - certifique-se de que você pode imprimir o ABS com sucesso antes de continuar este instrutível.
- Filamento de ABS (Smartfil ABS, cerca de 20 € / Kg). 3-15 gramas por PCB.
- Agulhas de costura (pegue algumas com a mãe). O tamanho dependerá do diâmetro dos pinos de seus componentes. Normalmente 0,5 mm ou 1 mm de diâmetro.
- Soldador de estanho e um soldador (cerca de 15 € em uma loja local). Além de todos os acessórios adequados para soldagem: suporte de soldador, lâmpada, prancha, pinça, óculos de proteção, máscara … os acessórios são da responsabilidade do usuário, apenas certifique-se de que se sente confortável e seguro durante o trabalho!
- Muita paciência, mente criativa e uma boa base (tente pesquisar no Google e estudar muito antes de colocar as mãos).
Etapa 1: Protótipo e Esquema
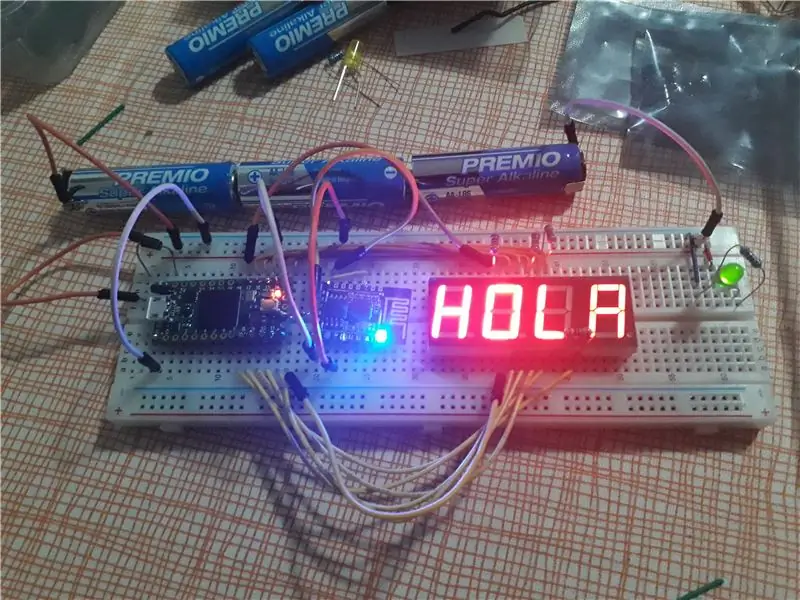
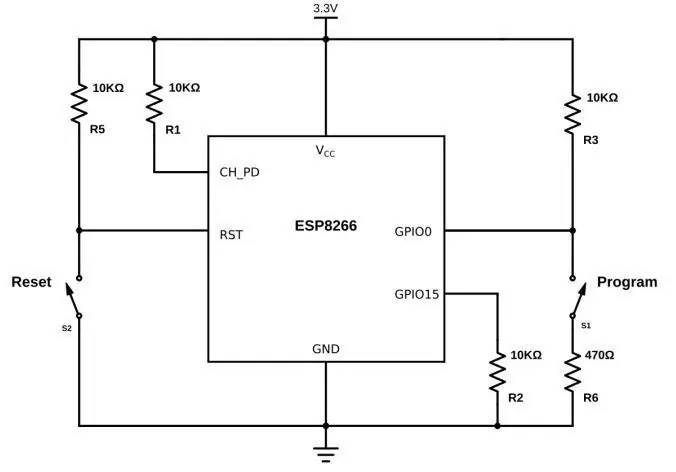
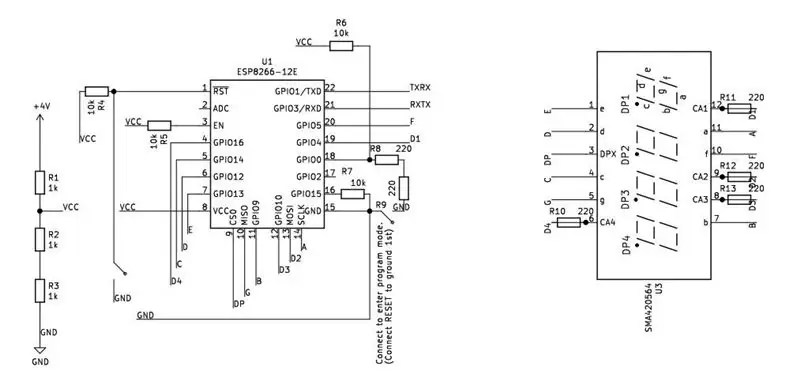
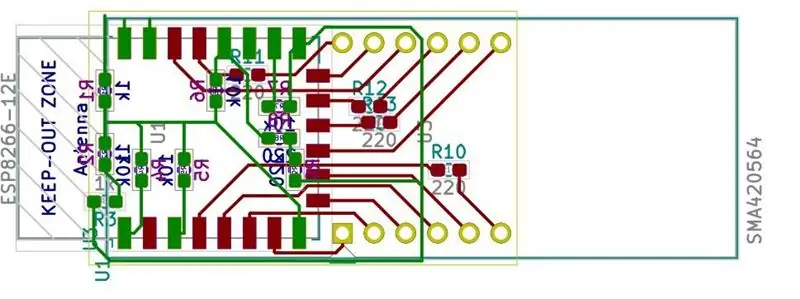
A menos que esteja seguindo o esquema de outra pessoa, você deve construir seu circuito elétrico seguindo as especificações do fabricante. Teste um protótipo de circuito e, quando estiver funcionando, esboce todas as conexões e componentes.
Assim que tiver um esboço e estiver confortável com um entendimento claro do seu circuito, obtenha detalhes no software EDA de sua preferência. Isso ajudará a otimizar e verificar seu projeto.
Desenhe seu esquema e use-o como um guia para o design de seu PCB. O software EDA como Eagle ou KiCad permite adicionar seus componentes específicos, com pinagens e dimensões realistas, para que você possa projetar seu circuito elétrico precisamente em torno deles.
Estou usando o KiCad, que é gratuito e fácil de entender para começar. Tudo o que sei é graças a Brian Benchoff @ https://hackaday.com/2016/11/17/creating-a-pcb-in… e alguns posts relacionados, então siga suas orientações para terminar com um bom design de PCB.
As imagens nesta seção estão relacionadas a:
- Teste o protótipo do ESP8266 e um display de 4 dígitos e 7 segmentos (conectado a um Teensy 4).
- Um diagrama de fiação de referência para uma placa wi-fi ESP8266 12E.
- Um esquema KiCad para um display de 4 dígitos e 7 segmentos funcionando através do ESP8266 e um divisor de tensão (este é o meu objetivo final).
- Uma saída de design KiCad PCB.
Etapa 2: modelo 3D
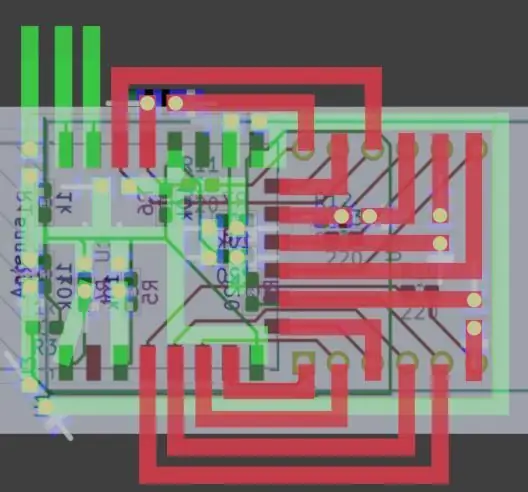

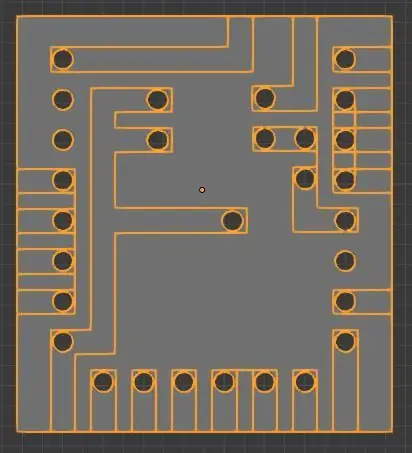
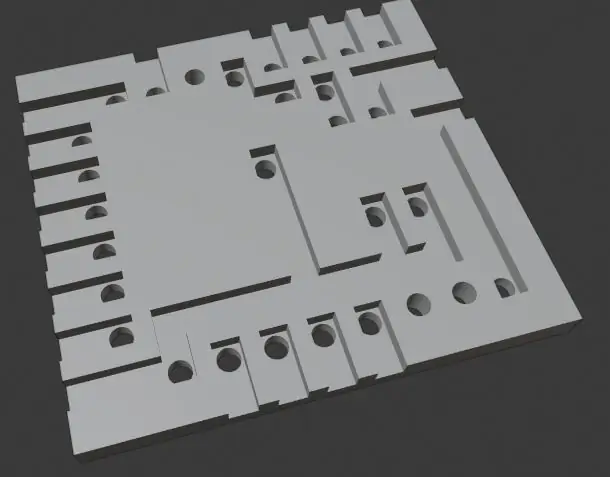
Depois de ter um projeto de PCB no papel, você deve dar a ele um pouco mais de realismo em um software de modelagem 3D. Isso também preparará seu arquivo para a impressora 3D. É assim que eu faço no Blender:
- Crie uma malha plana e adicione sua imagem de design de PCB sobre ela. Certifique-se de que está em escala e as dimensões são realistas, pois isso servirá como um "papel vegetal".
-
Crie componentes simplificados prestando atenção especial à localização e tamanho exatos dos PINS que se conectam ao seu PCB. Obtenha as especificações do fabricante on-line ou meça você mesmo para obtê-las com precisão suficiente. Observe alguns escurecimentos padrão que você pode usar como referência:
- Para placas use aviões. Para uma placa de circuito impresso de lado único, uso 1,5 mm de espessura, pois mais fina do que isso não obtive bons detalhes ao imprimir (isso também depende das configurações e recursos da impressora, mas falaremos disso mais tarde). Para uma placa de circuito impresso de dupla face, usei 2,5 mm de espessura.
- Para pinos, use cilindros com diâmetro mínimo de 1 mm para capturá-los pela impressora.
-
Para canais, use cubos com largura mínima de 1,2 mm. Você apenas extrudará faces para obter seus canais.
- Localize seus componentes de acordo com o design de seu PCB. Se seus componentes forem realistas o suficiente, você pode usar isso para verificar se há conflitos, mas sempre deixe espaço adicional ao redor de cada elemento.
- Rastreie seu circuito elétrico. Coloque uma malha de cubo no local do primeiro pino. Em seguida, no modo de edição, extrude as faces em uma linha reta seguindo o desenho. Novamente, mantenha as coisas simples, usando linhas de 90º e use tantos canais quanto você considerar. Além disso, permita uma separação de pelo menos 0,8 mm entre as paredes, caso contrário, eles serão perdidos durante a impressão. A Figura 1 abaixo mostra algumas rotas modificadas após a modelagem com dimensões reais, pois a rota ideal era muito estreita para ser viabilizada.
- Crie seu PCB adicionando um cubo plano (escurece conforme acima).
- Grave seus canais e buracos na placa adicionando modificadores booleanos ao seu objeto PCB. Isso cortará a parte do tabuleiro que cruza o objeto de destino do modificador booleano.
As figuras 3 e 4 mostram o resultado final da placa ESP8266 (modelo 3D na figura 2).
Depois disso, você deverá ver uma impressão 3D de seu PCB.
A última etapa é exportar o modelo corretamente.
- Certifique-se de que todas as faces apontam para fora ("Modo de edição - Selecionar tudo" e depois "Malha - Normais - Recalcular fora").
- Certifique-se de que todas são faces individuais ("Modo de edição - Selecionar tudo" e, em seguida, "Borda - Divisão de borda").-- Se você omitir essas duas etapas, poderá encontrar detalhes ausentes em seu software Slicer.--
- Exportar como. STL ("Somente seleção" para exportar apenas o PCB final e "Unidades de cena" para manter a escala das coisas).
Etapa 3: Software Slicer
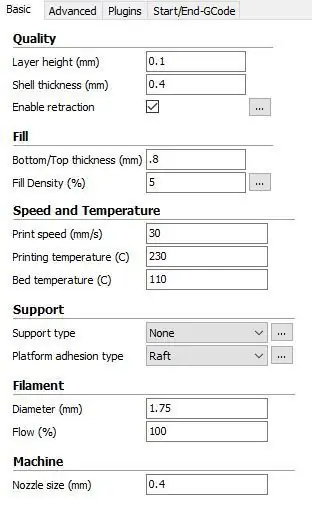
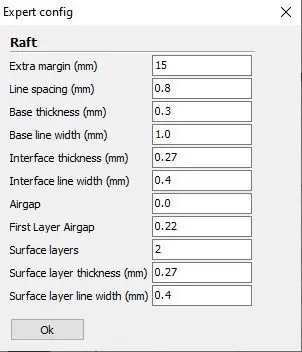
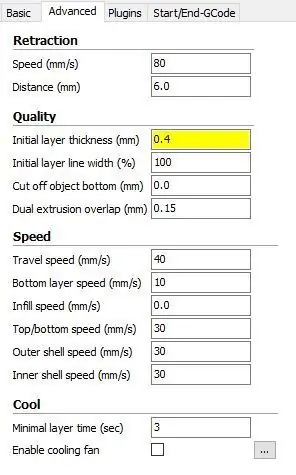
As impressoras 3D geralmente fornecem um software "Slicer" para processar os modelos 3D (em.stl ou outros formatos) e calcular a rota necessária para imprimi-lo (geralmente no formato.gcode). Eu tenho um Creality Ender 3 e não mudei do Creality Slicer fornecido, mas você pode aplicar essas configurações a qualquer outro software.
Estou dedicando uma seção inteira às configurações do fatiador, pois são muito importantes ao imprimir ABS, o que é bastante complicado devido a empenamento, encolhimento e rachaduras. Imprimir um PCB também está no limite das impressoras 3D padrão devido à precisão necessária.
Abaixo, estou compartilhando as configurações que uso no Creality Slicer para impressão detalhada de ABS de PCBs. Eles diferem das configurações padrão em:
- Paredes e camadas finas (para fornecer detalhes suficientes - isso pode exigir algumas iterações para o resultado desejado, a menos que você esteja satisfeito com minhas configurações).
- Use uma jangada. A chave está na base, a qual você deve ter um cuidado especial. (Eu permito um deslocamento de 10 mm do modelo para evitar que qualquer empenamento mínimo afete a impressão). Além disso, não há separações entre as linhas de jangada para obter uma boa base sólida. Se você acertar sua base, está tudo feito. Se você vir qualquer canto dobrando em sua base, você certamente está condenado.
- Velocidade lenta. Estou usando cerca de 1/4 da velocidade padrão (isso permite uma boa colocação do filamento e, portanto, aderência e qualidade geral).
- Temperaturas de ABS (leito: 110ºC, bico: 230ºC)
- Ventilador desativado (recomendado para manter a temperatura constante para ABS).
Etapa 4: Imprimir
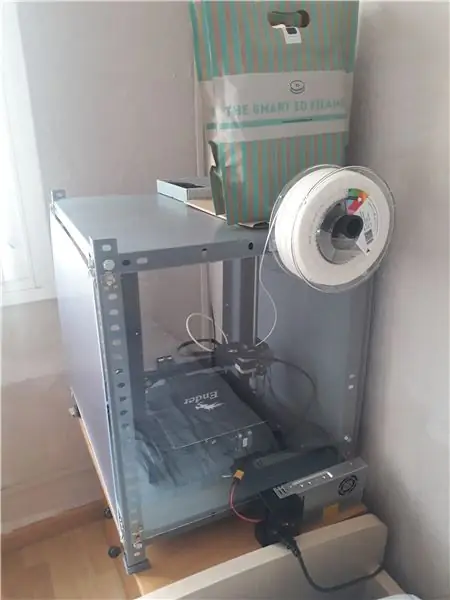
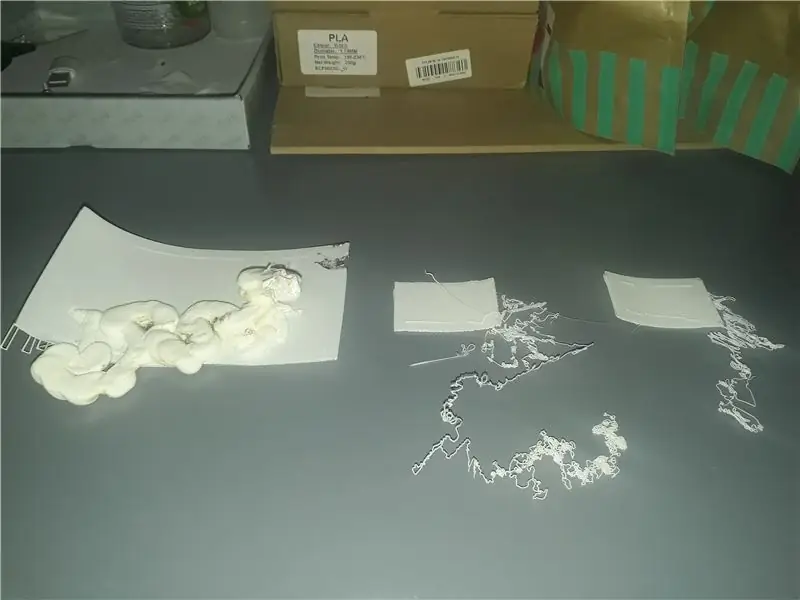
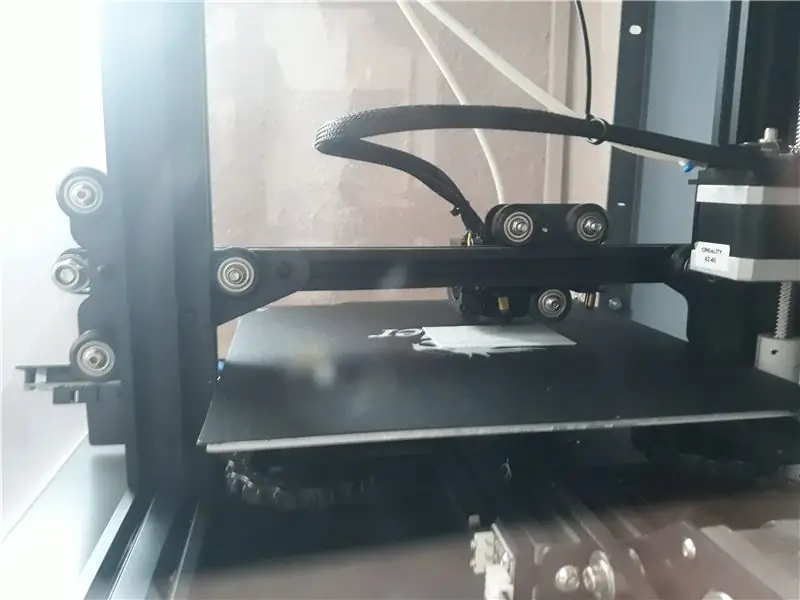
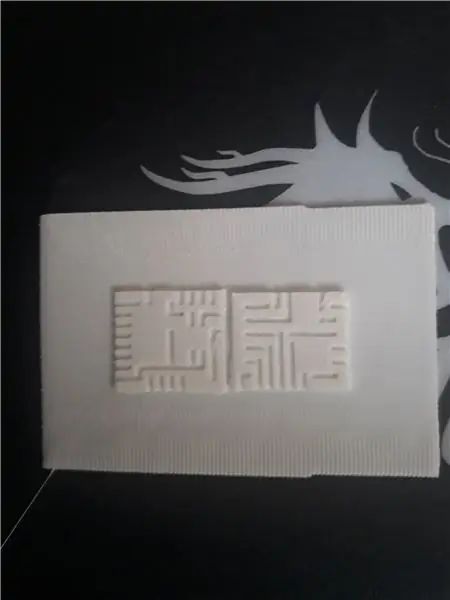
Finalmente, envie seu.gcode para sua impressora e faça com que seu PCB seja fabricado. Algumas dicas que você deve seguir:
- Encase sua impressora 3D. Um gabinete manterá sua temperatura muito mais estável, o que é um forte requisito para impressão em ABS. Certifique-se de manter a CPU e a fonte de alimentação fora do gabinete, assim como seu filamento. Se você conseguir imprimir em ABS sem um invólucro, compartilhe seu truque, pois isso me deixou louco.
- Pré-aqueça sua impressora por um tempo. No PLA você pode imprimir imediatamente, mas com o ABS meu conselho é pré-aquecer com as configurações do ABS (cama: 110ºC, bico: 230ºC) por 10-15 minutos para criar a atmosfera certa antes de começar a imprimir.
- Imprima lentamente, mas com segurança. Conforme mencionado anteriormente, reduzi a velocidade de impressão padrão para 1/4 no arquivo de configuração. Isso mostra ser lento o suficiente para ter um bom resultado, mas você pode gerenciar a velocidade de impressão durante a impressão, regulando a taxa de alimentação se quiser otimizá-la um pouco mais. Observe que velocidades altas levarão a movimentos muito repentinos que não colocarão o filamento de maneira eficaz ou podem colidir com a malha e soltá-la.
- Construa uma boa base. A chave no ABS é conseguir uma base bem fixa. Se a base falhar e se desprender, o modelo se foi (veja algumas tentativas desastrosas abaixo). Com as dicas acima (encaixe, pré-aquecimento e baixa velocidade) você deve conseguir uma boa base e um bom acabamento. Mas, ao contrário do PLA, que deixo sem supervisão por horas, o ABS precisa de mais atenção.
- Esteja vigilante, especialmente no início. Reiterando o acima exposto, a chave é a base. Certifique-se de que o primeiro contorno externo está bem definido. Isso conduzirá o resto da adesão da primeira camada. Às vezes, o filamento não pega de imediato ou é arrastado de sua localização. Você deve localizar isso logo o suficiente para corrigir qualquer nivelamento ou limpeza da placa de base. Sempre preste atenção para empenamento, se você vir cantos subindo, eles provavelmente vão acabar descolando toda a base e estragando toda a impressão. Mesmo que a base permaneça no lugar, o empenamento tornará este canto deformado.
Etapa 5: Arame e solda
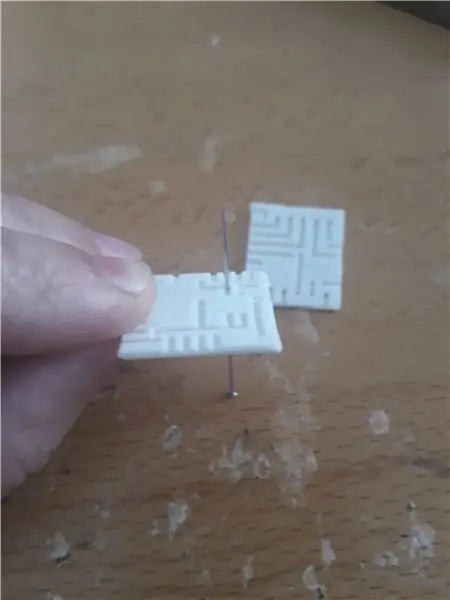
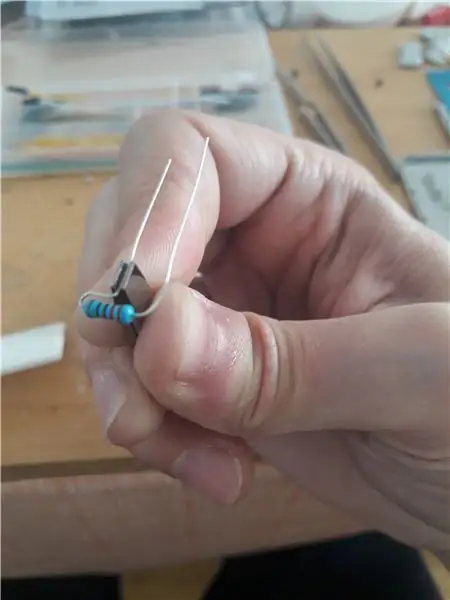
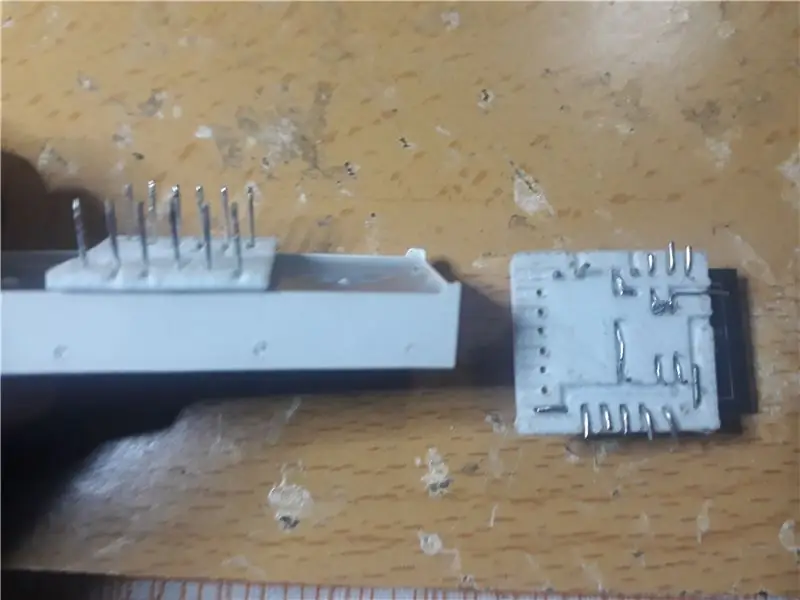
Agora é hora de colocar tudo no lugar:
- Verifique o acabamento dos canais e orifícios. Especialmente os orifícios costumam ser perdidos ou sobrepostos pela impressora. Use uma agulha de costura se precisar reabrir algumas delas. Claro, se você não obteve uma impressão plana devido a empenamento, ou não obteve os detalhes que esperava, verifique as configurações da impressora ou até mesmo as dimensões do seu modelo 3D.
- Coloque seus componentes. Módulos, resistores, capacitores ou leds que possuem seus próprios pinos podem ser instalados facilmente. Você pode dobrar um pouco o próprio fio para inseri-lo nos canais, de modo que seja mais fácil amarrá-lo mais tarde.
- Adicione fio e solda. Use quaisquer pinos ou jumpers que se encaixem no canal e corte-os no comprimento, de forma que você só precise soldar em pontos de junção específicos. Não deveríamos precisar soldar tudo, embora eu tenha a tendência de fazer isso quando as coisas não acendem. No meu caso, eu tive que conectar todos os pinos do ESP8266, e é aqui que era fundamental ter boas habilidades de soldagem (que eu não). O resto do tabuleiro era bem simples de fazer.
Etapa 6: Teste sua placa
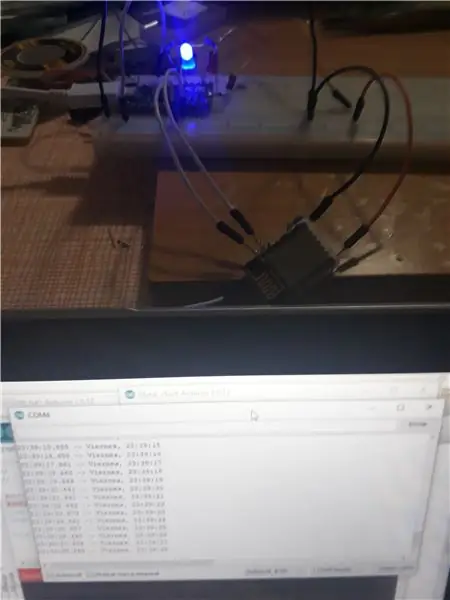
Se você tiver certeza de que fez tudo certo, conecte-o.
Para a prototipagem, estou executando o ESP8266 na conexão serial Teensy 4.
Enquanto fazia os testes na placa nua, carreguei um programa que carregava a hora local via wi-fi. Como você pode ver, tudo estava funcionando bem. Espero que você também tenha obtido um bom resultado com esta técnica.
Recomendado:
Motor sem escova impresso em 3D: 7 etapas (com imagens)
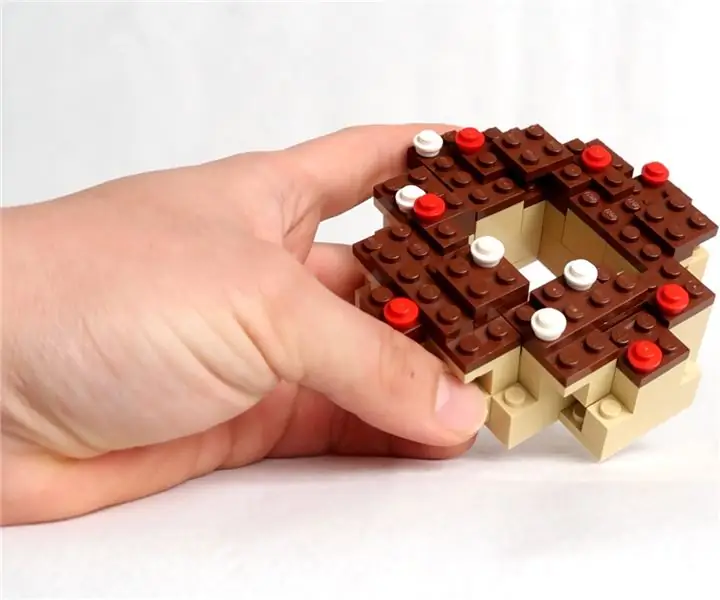
Motor sem escova impresso em 3D: Eu projetei este motor usando o Fusion 360 para uma demonstração no tópico de motores, então eu queria fazer um motor rápido, mas coerente. Ele mostra claramente as partes do motor, para que possa ser usado como um modelo dos princípios básicos de funcionamento presentes em um brus
Amplificador impresso em 3D de um instrumento musical elétrico: 11 etapas (com imagens)
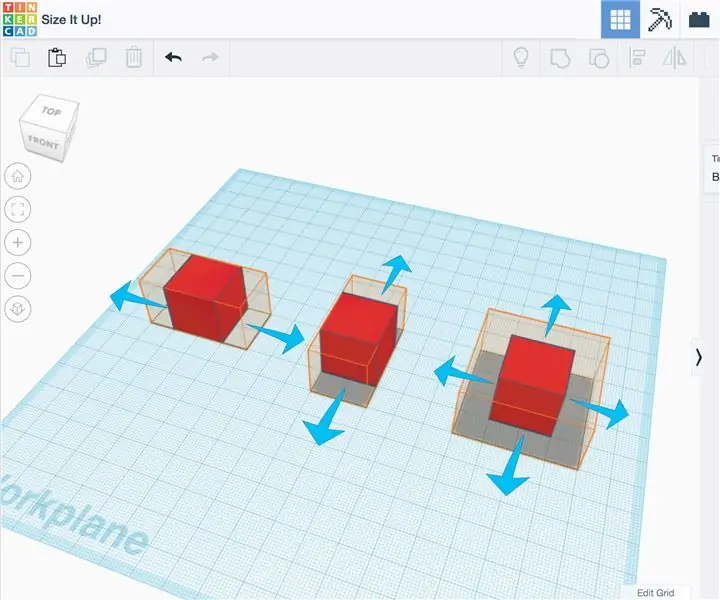
Um amplificador impresso em 3D de instrumento musical elétrico: Definição do projeto. Espero fazer um amplificador imprimível para uso com um violino elétrico ou qualquer outro instrumento elétrico. amplificador ativo e mantê-lo pequeno
Banco de energia abaixo de $ 10! - DIY - Impresso em 3D: 6 etapas (com imagens)
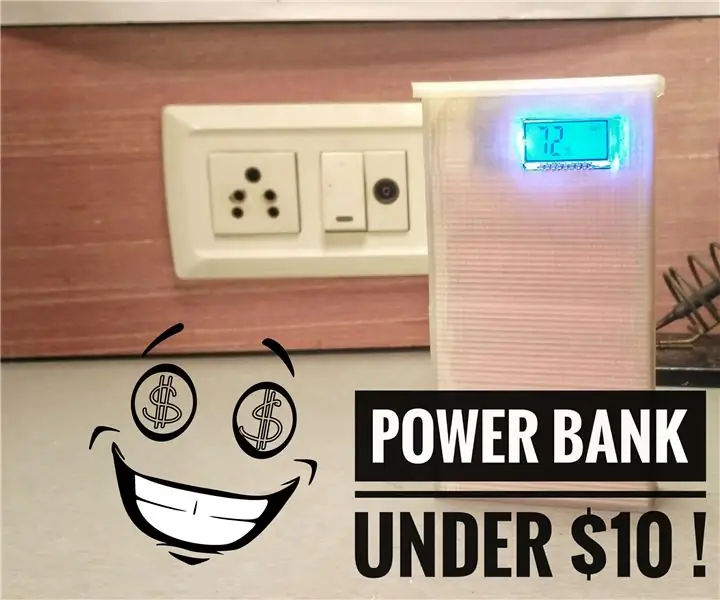
Banco de potência abaixo de $ 10! | DIY | Impresso em 3D: a indústria de smartphones de hoje está produzindo telefones muito potentes do que esperávamos nos anos 90, mas há apenas uma coisa que falta a eles, ou seja, bateria, eles são os piores. E a única solução que temos agora é um banco de energia. Neste vídeo, vou mostrar como
Um robô simples impresso em 3D: 11 etapas (com imagens)
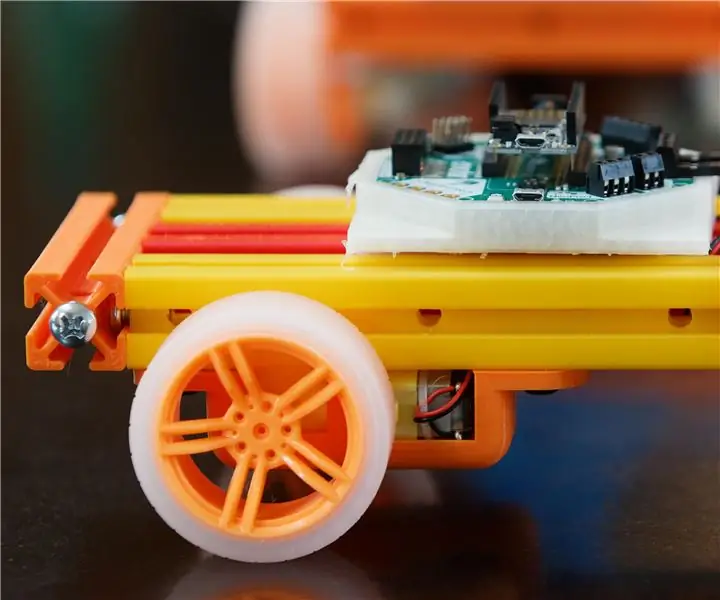
Um robô impresso em 3D simples: Permita-me namorar a mim mesmo. Eu cresci com conjuntos de montagem e depois LEGO. Mais tarde, usei o 8020 para construir protótipos de sistemas que projetei. Normalmente havia pedaços de sucata pela casa que meus filhos usavam como sua versão de um conjunto de montagem
Robô quadrúpede equipado com Arduino impresso em 3D: 13 etapas (com imagens)
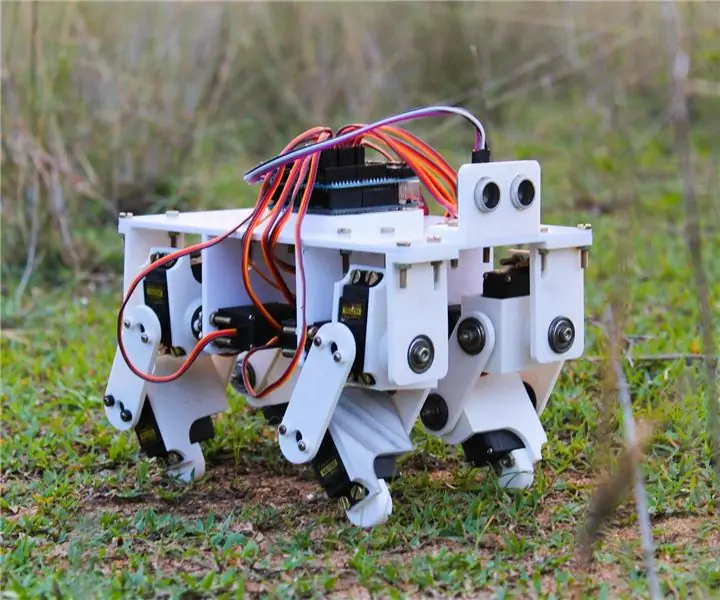
Robô quadrúpede movido a Arduino impresso em 3D: pelos Instructables anteriores, você provavelmente pode ver que tenho um grande interesse por projetos robóticos. Depois do Instructable anterior onde construí um bípede robótico, decidi tentar fazer um robô quadrúpede que pudesse imitar animais como o cachorro