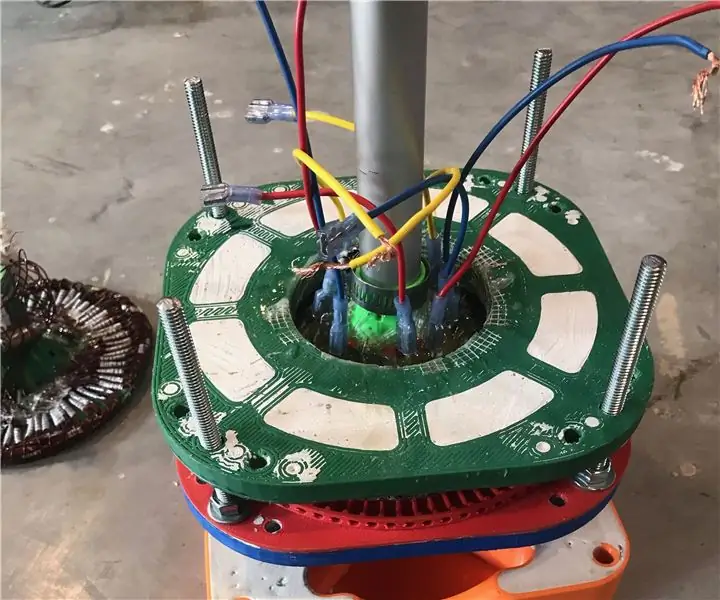
Índice:
2025 Autor: John Day | [email protected]. Última modificação: 2025-01-23 15:03
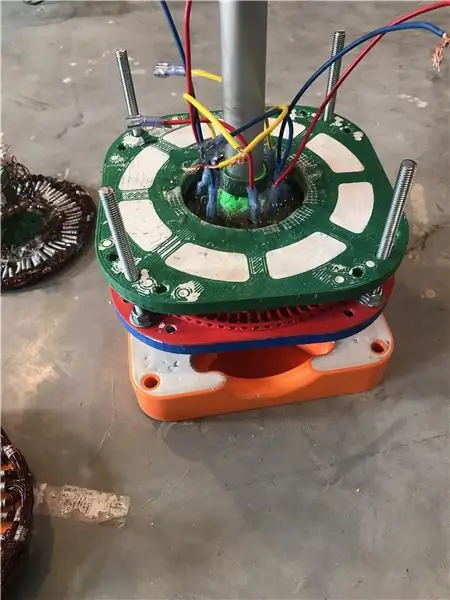
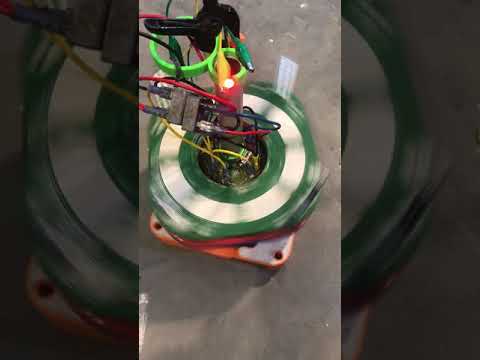
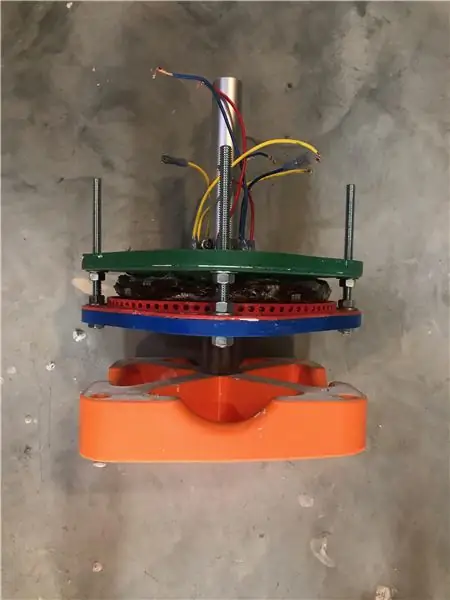
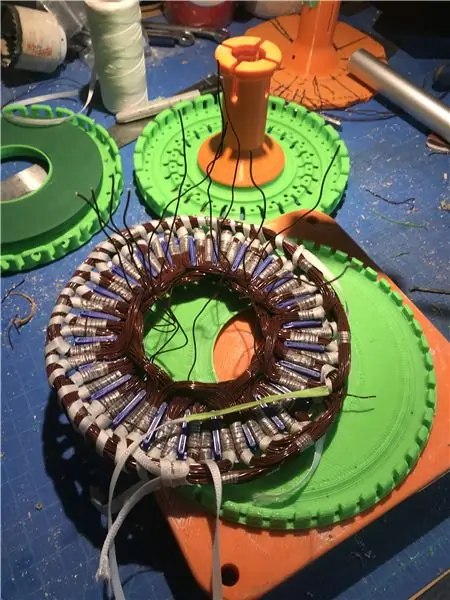
PARE!! LEIA ISTO PRIMEIRO !!! Este é o registro de um projeto que ainda está em desenvolvimento, fique à vontade para oferecer suporte.
Meu objetivo final é que esse tipo de motor / alternador possa se tornar um design de código aberto parametrizado. Um usuário deve ser capaz de inserir alguns parâmetros, como torque, velocidade, corrente, volts / rpm, tamanhos de ímã comuns e talvez espaço disponível, e uma série de arquivos de corte.stl e.dxf imprimíveis em 3D devem ser gerados.
O que fiz foi criar uma plataforma que pode validar um design simulado, que pode então evoluir para um dispositivo mais ideal pela comunidade.
Em parte, esse é um dos motivos pelos quais configurei isso com um dinamômetro. Um dinamômetro mede o torque e a velocidade para permitir a medição da HP, ou Watt do eixo. Neste caso, eu construí o alternador com um eixo estacionário de passagem, o que torna a configuração de um sistema dinamômetro mais simples e, portanto, pode ser configurado para ser acionado como um motor por um RC ESC (espero) e o torque medido na saída, assim como a velocidade, V e Amperes, permitindo determinar a eficiência do motor.
Para os meus propósitos, ele pode ser acionado por um motor de velocidade variável (excedente da furadeira sem fio, com engrenagem redutora) e a entrada de torque do eixo medida, bem como V e Amps de saída, permitindo que a eficiência real seja gerada e as cargas esperadas da turbina para ser simulado.
Neste modo, espero usar um RC ESC capaz de frenagem regenerativa e talvez um Arduino para controlar a carga que meu VAWT carrega para atingir o MPPT (Multi Power Point Tracking).
MPPT é usado no controle solar e também no controle de turbinas eólicas, mas é um pouco diferente para o vento. Com a energia eólica, um grande problema é que, à medida que a velocidade do vento dobra de 10km / h para 20km / h, a energia disponível do vento aumenta pelo cubo, ou seja, 8 vezes. Se 10W estivessem disponíveis a 10km / h, então 80W estariam disponíveis a 20km / h. É ótimo ter mais energia, mas a saída dos alternadores apenas dobra quando a velocidade dobra. Portanto, se você tiver o alternador perfeito para um vento de 20km / h, sua carga pode ser tão forte que a 10km / h ele nem dará partida.
O que o MPPT faz é usar um interruptor de estado sólido de serviço pesado para desconectar e reconectar um alternador muito rapidamente. Ele permite que você ajuste a quantidade de carga que um alternador carrega, e o Multi, do MPPT, significa que você pode definir cargas diferentes para velocidades diferentes.
Isso é muito útil, pois todos os tipos de turbinas coletam sua energia máxima quando a carga é combinada com a energia disponível, ou velocidade do vento.
TÃO
Esta não é uma receita, embora acredite que poderia ser copiada do que postei, e ficaria feliz em fornecer mais informações, mas sugiro que a melhor opção seria sugerir melhorias para mim, antes que o concurso de circuitos e sensores termine, para que eu possa considerar, responder e talvez melhorar isso instrutível.
Vou continuar a atualizar, revisar e adicionar informações, então, se for interessante agora, você pode querer verificar novamente em um momento, mas espero terminar um pouco antes que o concurso de Sensores termine em 29 de julho de 19 de julho.
Além disso, não sou uma fera particularmente social, mas gosto de um tapinha nas costas de vez em quando, e essa é uma das razões pelas quais estou aqui:-) Diga-me se você está gostando de ver meu trabalho e quer ver mais por favor:-)
Este projeto surgiu porque eu queria uma carga controlável para testar meus projetos de turbina, e queria que fosse facilmente reproduzível, para que outros pudessem usá-la também. Para isso, me limitei a projetar algo que pudesse ser construído apenas com uma impressora FDM, sem a necessidade de outras ferramentas de máquina. Não parece haver muitos produtos comerciais que preencham a necessidade de um alternador de alto torque, baixa velocidade e não dentado, embora haja alguns da China. Em geral, não há muita demanda porque os sistemas de engrenagens são muito baratos e a eletricidade é muito barata.
O que eu queria era algo que produzisse cerca de 12 V a 40-120 rpm e cerca de 600-750 W a 120-200 rpm. Eu também queria que fosse compatível com controladores PMA trifásicos baratos do mundo RC (controladores eletrônicos de velocidade do ESC). Um requisito final era que fosse um rotor externo (a caixa ou carcaça com imãs gira, enquanto o eixo com estator é estacionário), com um eixo que passa por toda a caixa e um estator que se fixa ao eixo.
Este instrutível é um trabalho em andamento e estou postando para que as pessoas possam ter uma visão do processo, não tanto porque acho que deveriam copiá-lo. Uma coisa importante que eu mudaria é que a placa de proteção do fio que construí não é nem de longe forte o suficiente para canalizar adequadamente os campos magnéticos ao redor do anel, então uma grande parte do fluxo magnético pago nesses magnetos é desperdiçado na parte de trás. Quando refazer o projeto, o que farei em breve, provavelmente o farei com as placas de suporte magnéticas como placas de aço de corte cnc. O aço seria razoavelmente barato, muito mais forte e simplificaria a maior parte dessa construção. Foi interessante fazer os compostos FDM / fio / gesso como ilustrei aqui, e com PLA carregado de ferro, as coisas teriam sido diferentes também. Decidi, porém, que queria algo que realmente durasse, então placas de aço.
Fiz um bom progresso nesta versão, que usarei para testar este VAWT. Ainda não cheguei lá em termos de desempenho de baixa tensão. Acho que minha potência / torque está na estimativa certa, vou atualizar conforme as coisas progridem, mas neste ponto o que eu tenho tem uma boa chance de ser a carga controlável de que preciso. Quando em curto-circuito, parece ser capaz de fornecer bastante resistência ao torque, mais do que o suficiente para testar a turbina. Só preciso criar um banco de resistência controlada e tenho um amigo que está me ajudando com isso.
Uma coisa que irei abordar brevemente é que, como muitas pessoas agora, eu tenho uma impressora 3D (PLA usando FDM) há alguns anos, da qual me diverti de 20 a 30 kg. Muitas vezes acho isso frustrante, pois peças de qualquer tamanho / resistência são caras e muito lentas para imprimir ou baratas, rápidas e frágeis.
Eu sei quantos milhares dessas impressoras 3D estão por aí, muitas vezes não fazendo nada porque demoram muito ou custam muito para fazer peças úteis. Eu vim com uma solução interessante para peças mais rápidas e mais resistentes da mesma impressora e PLA.
Eu estou chamando de "estrutura derramada", onde o objeto impresso (composto de uma ou mais partes impressas, e às vezes rolamentos e eixos), é feito com espaços vazios projetados para serem despejados cheios de um enchimento líquido de endurecimento. É claro que algumas das escolhas óbvias para um enchimento derramado seriam algo como epóxi carregado com fibra de vidro cortada de fio curto, que poderia ser usada para montagens de alta resistência e peso leve. Estou experimentando algumas ideias de custo mais baixo e mais ecológicas também. O outro lado dessa montagem de "estrutura vazada", é que a cavidade ou vazio que você vai preencher, pode ter elementos de pequeno diâmetro de alta tração, amarrados pré-tensionados no "molde / plugue" impresso, o que forma a estrutura resultante um compósito em materiais e em estrutura, parte Stressed Skin (a bainha de PLA), mas com um núcleo de alta resistência à compressão que inclui também elementos de alta resistência à tração. Vou fazer um segundo instrutível apresentando isso, então falarei sobre isso aqui, apenas para cobrir como ele pertence a esta compilação.
Etapa 1: Lista de Materiais e Processo
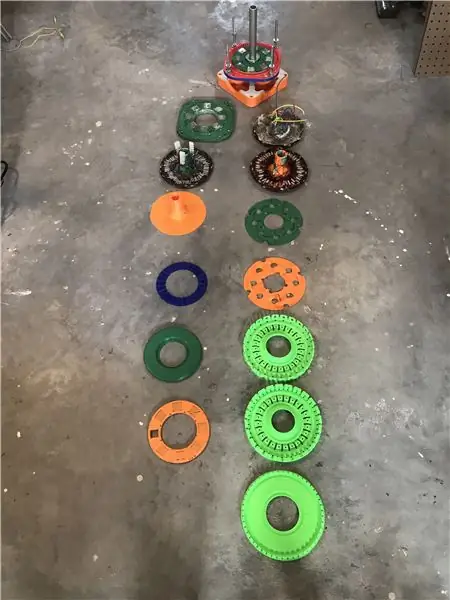
O PMA consiste em 3 conjuntos, cada conjunto contendo ou usando uma variedade de peças e materiais.
De cima (lado do rolamento) para baixo (lado do estator), 1. Porta-rolamentos e matriz de rolamento superior
2. Estator
3. Matriz de ímã inferior
1. O porta-rolamentos e a matriz de ímã superior
Para isso, usei as peças impressas em 3D listadas acima
- 150mm8 pólo superior mag e suporte de rolamento CV5.stl,
- placa interna do lado do rolamento
- placa externa do lado do rolamento
- Rolamento de autoalinhamento de 1 "ID (como usado em blocos de almofada padrão ++ adicionar link de internet),
- 25 'de arame de aço galvanizado 24g
- 15 'de 10g de fio de aço galvanizado
- 2 rolos de lã de aço grossa
Opcionalmente, o fio de aço pesado e a lã de aço podem ser substituídos por placas de suporte de aço, corte a laser / jato de água ou uma placa de suporte magnética impressa em 3D pode ser possível (mas alguns fios de aço pesados ainda são uma boa ideia, pois resistem à deformação plástica sobre Tempo). Eu tentei fundir uma placa de apoio com epóxi carregado com pó de óxido de ferro e tive algum sucesso. Melhorar o acoplamento de fluxo entre os ímãs na matriz lateralmente usando uma placa de apoio mais eficaz deve aumentar os Volts para fora em rpms mais baixos. Também é bom ter em mente que este é o principal componente estrutural, e a placa traseira transfere as forças dos ímãs para os postes de levantamento. As forças magnéticas que puxam as placas uma em direção à outra podem ser de centenas de libras, e as forças aumentam exponencialmente (em cubos, à terceira potência) conforme as placas se aproximam. Isso pode ser muito perigoso, e deve-se ter cuidado com as ferramentas e quaisquer outros objetos que possam ser atraídos para a placa montada ou para as costas!
Usei cerca de 300 pés de fio magnético revestido de 24g nos enrolamentos, que abordarei em detalhes mais tarde.
Etapa 2: Fabricação das placas magnéticas
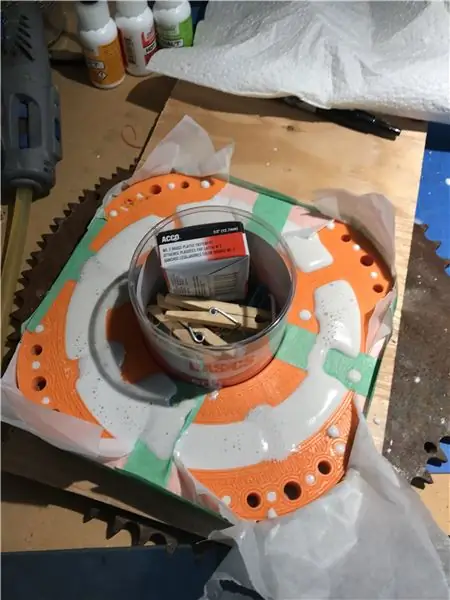
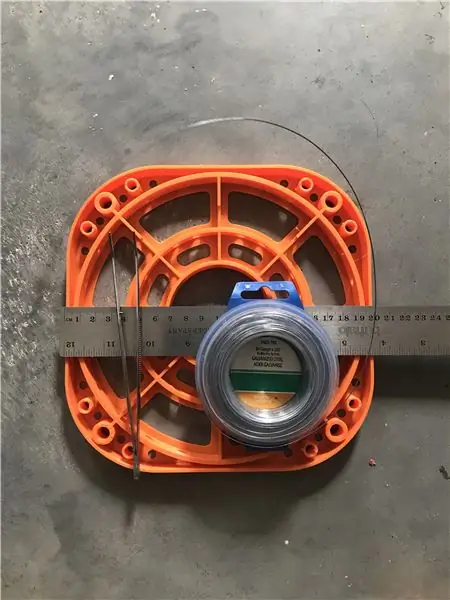
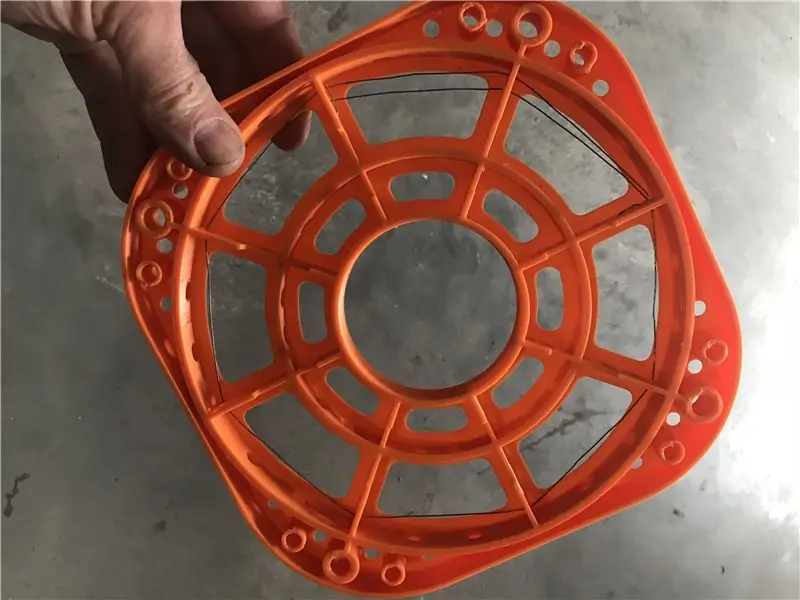
Neste alternador de fluxo axial, para minimizar o desgaste e maximizar a saída, estou usando duas matrizes de ímã, uma em cada lado das bobinas do estator. Isso significa que nenhum núcleo magnético é necessário para atrair o campo magnético através dos enrolamentos de cobre, como fazem a maioria das geometrias motor / alt. Existem alguns projetos de fluxo axial que usam núcleos de ferris, e posso tentar alguns experimentos dessa forma no futuro. Eu gostaria de experimentar alguns materiais carregados com ferro para impressão em 3D.
Neste caso, escolhi uma matriz de ímã de 8 polos em um círculo de 150 mm, usando ímãs de terra rara de 1 "x1" x 0,25 ". Esse tamanho era para garantir que todas as peças caberiam em uma cama de impressão de 210 mm x 210 mm. Em geral, eu dimensionei este alternador primeiro entendendo que quanto maior o diâmetro, melhor em termos de volts por rpm, então o tornei tão grande quanto caberia confortavelmente na minha cama de impressão. Para sua informação, há mais de um motivo pelo qual maior é melhor: mais espaço para ímãs, quanto mais longe os ímãs estão do centro, mais rápido eles viajam e há mais espaço para o cobre também! Todas essas coisas podem se somar rapidamente! No entanto, uma conclusão a que cheguei é que nesta faixa de tamanho, um convencional O sistema de fluxo pode ser uma construção doméstica melhor. Rotores pequenos não têm muito espaço e as coisas podem ficar bem apertadas, especialmente se você estiver fazendo um eixo passante como fiz neste projeto. Além disso, se o seu ímã (comprimento radial) é pequeno em relação ao diâmetro do rotor, como neste, (cerca de 6 "de diâmetro para 1" ímã), então o ventoi ng fica um pouco estranho com o enrolamento da extremidade interna tendo apenas cerca de metade do comprimento do enrolamento externo.
De volta à instrução! A maneira como montei as placas magnéticas deste alternador é primeiro colando a placa magnética (verde) na flange vermelha / placa traseira. Em seguida, coloquei a placa magnética em algumas camadas finas de madeira compensada (cerca de 0,75 de espessura) e coloquei as duas em uma placa de aço pesada, para permitir que os ímãs fixassem o conjunto no lugar. Em seguida, enrolei o fio de aço no atrás das placas magnéticas. Isso não saiu bem como eu esperava. O forte campo magnético puxou o fio em direção ao centro dos ímãs, e eu não tive sucesso em dobrar cada fileira de fio para encaixar perfeitamente no próximo ponto, sem empurrar o primeiro envoltório. Esperava poder apenas enrolar o fio e o fluxo magnético travaria. Em seguida, tentei cortar anéis de fio, e isso foi melhor, mas ainda está longe do que eu esperava em termos de obter uma placa de suporte consistente e agradável do fio. Maneiras mais complexas de fazer isso são possíveis e podem valer a pena experimentação futura. Também tentei usar lã de aço, compactada no campo magnético, como uma placa de suporte ou fluxo caminho de retorno. Isso parecia funcionar, mas a densidade real do ferro não parecia ser muito alta, então eu pensei Não testei sua eficácia, em parte porque acreditava que a estrutura do fio era importante para as cargas mecânicas nas placas magnéticas. A lã de aço também pode valer a pena uma investigação futura, no entanto, placas de aço com corte a jato de água são provavelmente a próxima opção que tentarei.
Em seguida, peguei a parte impressa em 3D laranja e teci o fio nela e ao redor, ao longo do que me parecia ser as direções de maior carga, parafuso a parafuso e parafuso a centralizar algumas vezes em cada canto. Também enrolei em torno dos orifícios dos parafusos onde toda a barra de rosca passa como postes de levantamento para manter e ajustar o espaçamento entre as placas.
Depois de me certificar de que a placa magnética e o flange eram bons o suficiente, e a placa de fundo laranja estava satisfatoriamente enfiada com arame de reforço, juntei os dois com cola. É preciso ter cuidado, pois essa junta de cola precisa ser à prova d'água ou fechada. Tive vazamentos nas duas primeiras vezes e está uma bagunça, gasta muito gesso e é mais estressante do que você precisa. Eu recomendo manter um pouco de cola azul ou outro chiclete, como adesivo não permanente, para corrigir vazamentos rapidamente. Assim que as peças estiverem unidas, preencha com o material de reforço de sua escolha. Usei um gesso duro modificado com cola PVA. O gesso deve atingir 10 000 psi de compressão, mas não muito em tensão (daí o fio). Gostaria de experimentar epóxi com vidro picado e cabosil, ou concreto e aditivos.
Uma coisa útil sobre o gesso é que, uma vez que ele chute, você tem um pouco de tempo onde fica duro, mas frágil e vazamentos ou bolhas podem ser facilmente raspados ou arrancados.
Neste projeto, existem duas placas magnéticas. Um deles tem um rolamento, uma unidade autocompensadora de mancal padrão de 1 . Eu pressionei o meu na matriz magnética no início. Para a aplicação para a qual o projetei, um segundo rolamento estará localizado na turbina acima do alternador, então eu usava apenas um rolamento autocompensador. Isso foi um pouco chato no final. Essas peças também poderiam ser montadas com cada placa magnética tendo um rolamento, se os fios de saída do estator fossem conduzidos internamente através do eixo montado. permitir que hélices de contra-rotação sejam montadas em um eixo / tubo comum não rotativo.
Etapa 3: Criação do estator

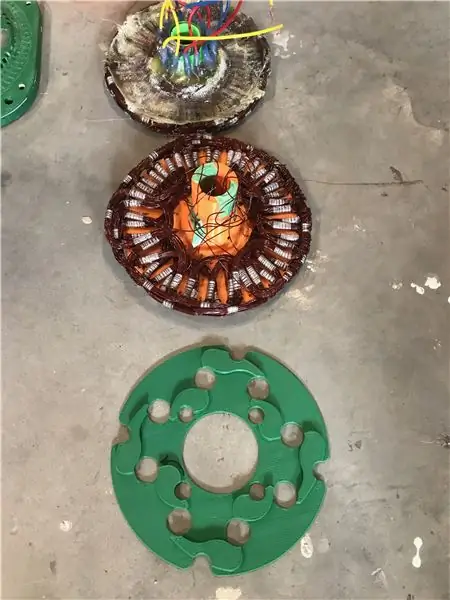
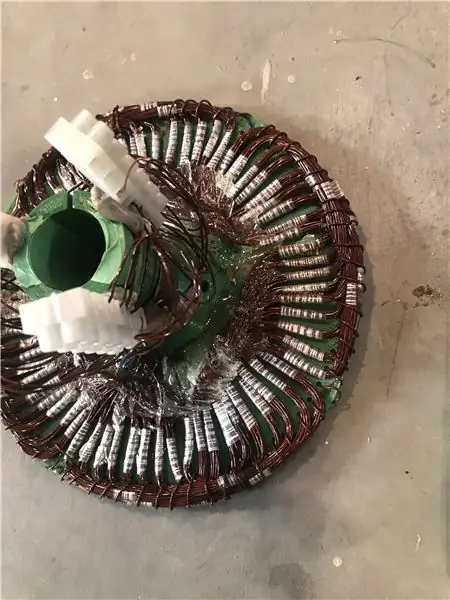
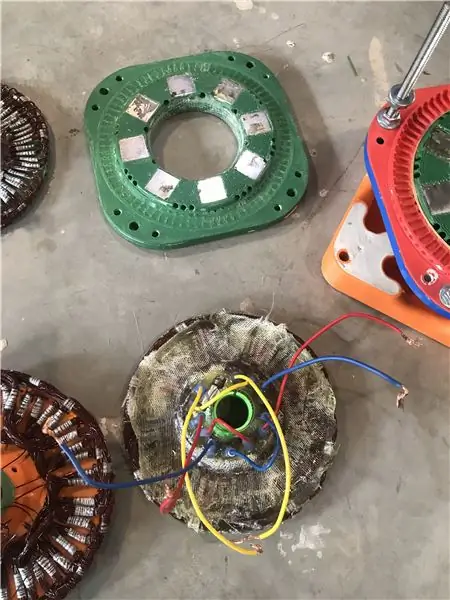
Mantendo meu tema de tentar explicar o que fiz e por que parecia uma boa ideia na época, o estator exigirá um pouco mais de espaço.
Em um PMA, geralmente os enrolamentos são estacionários, enquanto os conjuntos magnéticos giram. Nem sempre é o caso, mas quase sempre. Em um conjunto de fluxo axial, com o entendimento da "regra da mão direita" fundamental, entende-se que qualquer condutor que encontrar um campo magnético giratório, terá corrente e tensão geradas entre as pontas do fio, com a quantidade de corrente útil sendo proporcional para a direção do campo. Se o campo se mover paralelamente ao fio (por exemplo, em um círculo ao redor do eixo de rotação), nenhuma corrente útil será gerada, mas correntes parasitas significativas serão geradas, resistindo ao movimento dos ímãs. Se o fio for perpendicular, a saída de tensão e corrente mais alta será alcançada.
Outra generalização é que o espaço dentro do estator, por onde passa o fluxo magnético em rotação, para potência máxima de saída, deve ser preenchido com o máximo possível de cobre, todo radialmente colocado. Este é um problema para sistemas de fluxo axial de pequeno diâmetro, pois neste caso, a área disponível para cobre perto do eixo é uma fração da área na borda externa. É possível obter 100% de cobre na área mais interna encontrada pelo campo magnético, mas dentro dessa geometria isso só leva a talvez 50% na borda externa. Esta é uma das razões mais fortes para ficar longe de projetos de fluxo axial que são muito pequenos.
Como eu disse anteriormente, este instrutivo não é sobre como eu faria de novo, mas sim para apontar algumas direções que parecem promissoras e mostrar alguns dos buracos que podem ser alcançados neste caminho.
Ao projetar o estator, eu queria torná-lo o mais flexível possível em termos de saída de volts por rpm e queria que fosse trifásico. Para obter eficiência máxima, por meio da minimização das correntes parasitas geradas, qualquer "perna" (cada lado de uma bobina deve ser considerado uma "perna") deve encontrar apenas um ímã por vez. Se os ímãs estiverem próximos, ou se tocando, como é o caso em muitos motores rc de alta potência, durante o tempo em que a "perna" está passando pela reversão do fluxo magnético, serão desenvolvidas correntes parasitas significativas. Em aplicações de motor, isso não importa tanto, pois a bobina é energizada pelo controlador quando está nos locais certos.
Eu dimensionei o conjunto de ímãs com esses conceitos em mente. Os oito ímãs na matriz têm cada um 1 "de diâmetro e o espaço entre eles é de 1/2". Isso significa que um segmento magnético tem 1,5 "de comprimento e espaço para 3 x 1/2" "pernas". Cada "perna" é uma fase, portanto, em qualquer ponto, uma perna está vendo um fluxo neutro, enquanto as outras duas estão vendo um fluxo crescente e um fluxo decrescente. A saída trifásica perfeita, embora dando ao ponto neutro tanto espaço (para minimizar as correntes parasitas) e usando ímãs quadrados (ou em forma de torta), o fluxo quase atinge o pico no início, permanece alto e depois cai para zero rapidamente. Acho que esse tipo de saída é chamado de trapezoidal e pode ser difícil para alguns controladores que eu entendo. Ímãs redondos de 1 "no mesmo aparato dariam mais de uma onda senoidal verdadeira.
Geralmente, esses alternadores caseiros foram construídos usando "bobinas", feixes de arame em forma de donut, onde cada lado do donut é uma "perna" e várias bobinas podem ser fixadas juntas, em série ou paralelas. Os donuts são dispostos em um círculo, com seus centros alinhados com o centro do caminho do ímã. Isso funciona, mas existem alguns problemas. Um problema é que, uma vez que os condutores não são radiais, uma grande parte do condutor não está passando a 90 graus para o campo magnético, então correntes parasitas são geradas, que aparecem como calor na bobina e resistência à rotação na matriz magnética. Outro problema é que, como os condutores não são radiais, eles não se encaixam tão bem. A saída é diretamente proporcional à quantidade de fio que você pode colocar neste espaço, então a saída é reduzida por "pernas" não radiais. Embora seja possível e às vezes seja feito em projetos comerciais, enrolar uma bobina com pernas "radiais, unidas superior e inferior, requer 2x mais enrolamento final do que um enrolamento serpentino onde a parte superior de uma perna é unida ao topo da próxima perna apropriada e, em seguida, a parte inferior dessa perna é unida à próxima perna apropriada, e assim por diante.
O outro grande fator em alternadores de fluxo axial deste tipo (ímãs girando acima e abaixo do estator), é a folga entre as placas. Esta é uma relação de lei do cubo, conforme você reduz a distância entre as placas em 1/2, a densidade do fluxo magnético aumenta em 8x. Quanto mais fino você puder fazer seu estator, melhor!
Com isso em mente, fiz um gabarito de enrolamento de 4 lóbulos, montei um sistema para medir cerca de 50 pés de fios de arame e enrolei o gabarito 6 vezes, criando feixes de arame com cerca de 6 mm de diâmetro. Eu coloco no anel espaçador azul, amarrando-os pelos orifícios para que as pontas do fio saiam por trás. Isso não foi fácil. Foi ajudado um pouco por ter cuidadosamente amarrado os feixes para que não se soltassem, e por tomar meu tempo e usar uma ferramenta de modelagem de madeira lisa para empurrar os fios no lugar. Uma vez que todos estavam amarrados no lugar, o anel espaçador azul foi colocado na maior das banheiras formadoras verdes claras, e com a ajuda da ferramenta formadora de rosca verde escuro, do outro lado da banheira verde claro, cuidadosamente prensada e plana com um torno de bancada. Esta cuba de formação tem uma ranhura para a torção do arame de amarração. Isso leva tempo e paciência enquanto você gira cerca de 1/5 de volta, pressiona, gira e continua. Isso torna o disco plano e fino, enquanto permite que os enrolamentos das extremidades se empilhem. Você pode notar que meu enrolamento de 4 lóbulos tem "pernas" retas, mas as conexões internas e externas não são redondas. Isso deveria tornar mais fácil para eles empilhar. Não funcionou muito bem. Se eu estivesse fazendo isso de novo, faria os enrolamentos da extremidade interna e externa seguirem caminhos circulares.
Depois de achatá-lo e afiná-lo, e as bordas compactadas, enrolei uma fita plana ao redor da borda para compactá-la, e outra para cima, para baixo e ao redor de cada perna e depois na próxima a ela também. Depois de fazer isso, você pode remover os fios de amarração e mudar para a cuba de prensagem menor e voltar ao torno e pressioná-lo o mais fino e plano possível. Quando estiver plano, remova-o da cuba de prensa. Em vez do processo complexo de encerar cuidadosamente e revestir moldes como esse com compostos desmoldantes, geralmente uso apenas algumas camadas de filme plástico (da cozinha). Coloque algumas camadas no fundo do molde e coloque a fibra de vidro sobre o envoltório elástico. Em seguida, adicione o tubo de montagem do estator, que se encaixa na parte superior da cuba de formação verde claro, mas tem uma camada de envoltório elástico e fibra de vidro entre eles. Em seguida, adicione o enrolamento do estator de volta ao lugar para empurrar para baixo o envoltório elástico e a fibra de vidro e travar o tubo de montagem do estator no lugar. Em seguida, volte ao torno e pressione novamente. Depois de encaixar bem na banheira, com o envoltório elástico e a fibra de vidro inseridos, um pano de fibra de vidro é adicionado (com um orifício no centro para o tubo de montagem do estator).
Agora está pronto para derramar o material de ligação, epoxi ou resina de poliéster são comumente usados. Antes que isso seja feito, uma preparação cuidadosa é importante, pois uma vez que você inicia este processo, você não pode realmente parar. Usei uma placa de base impressa em 3D que fiz anteriormente, com um orifício de 1 "no centro e uma placa plana ao redor. Usei um tubo de alumínio de 16" de 1 ", em que o tubo de montagem do estator se encaixaria e seria mantida perpendicularmente à placa plana. A cuba de formação verde, o enrolamento do estator e o tubo de montagem do estator foram deslizados para baixo para se assentarem na placa plana. Antes de misturar o epóxi, primeiro preparei 4 pedaços de filme retrátil e coloquei cuidadosamente uma quinta peça no rosquinha formando verde escuro, para que tivesse o mínimo de rugas na face contra o enrolamento do estator. Depois de misturar o epóxi e despejá-lo no tecido de fibra de vidro, coloquei cuidadosamente o envoltório elástico em torno do tubo de 1 "e coloquei o verde formando um anel em cima dele. Eu também preparei alguns rotores de freio velhos, que deram um pouco de peso, e se encaixaram perfeitamente no donut de formação verde. Depois disso, coloquei um pote invertido em cima dos rotores do freio e, em cima do pote, empilhei cerca de 100 libras de coisas. Deixei isso por 12 horas e saiu com cerca de 4-6 mm de espessura.
Etapa 4: Teste e Sensores
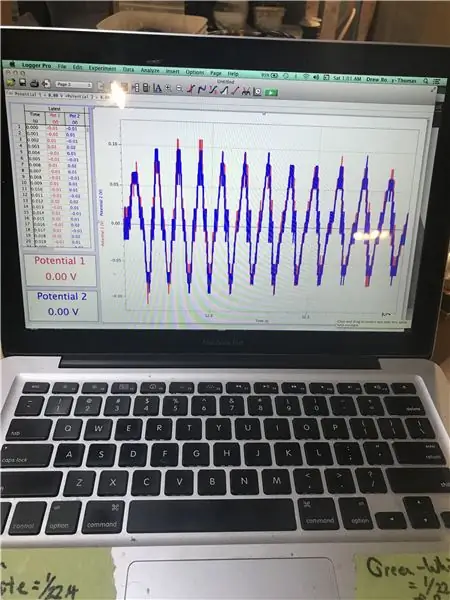
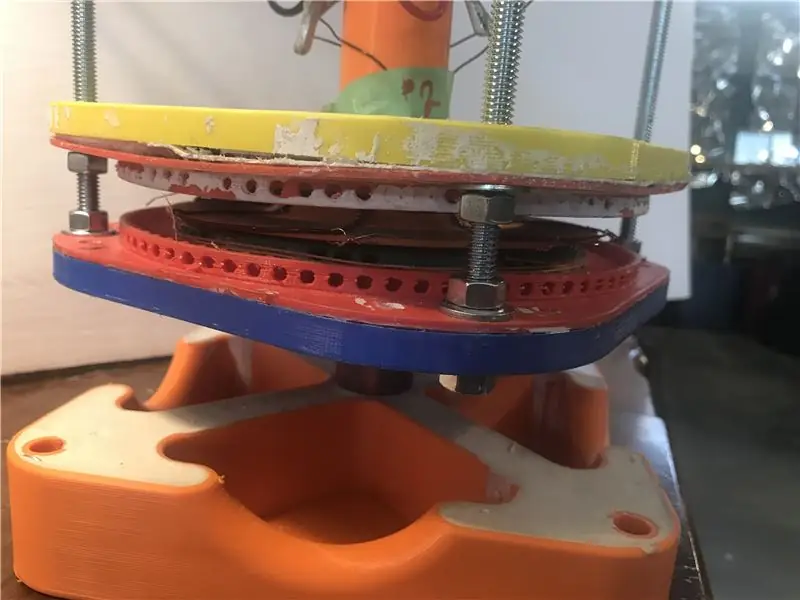
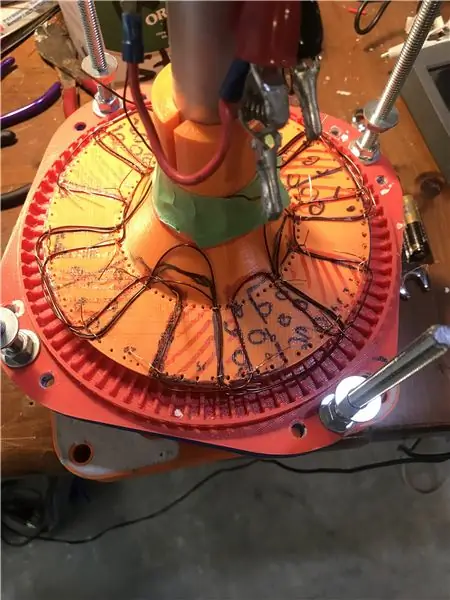
Existem várias entradas e saídas mensuráveis do alternador e medi-las todas ao mesmo tempo não é fácil. Tenho muita sorte de ter algumas ferramentas da Vernier que tornam isso muito mais fácil. Vernier fabrica produtos de nível educacional, não certificados para uso industrial, mas muito úteis para experimentadores como eu. Eu uso um registrador de dados Vernier, com uma variedade de sensores plug and play. Neste projeto eu uso sondas de corrente e tensão baseadas em Hall, para medir a saída do alternador, um sensor óptico para dar a velocidade do alternador e uma célula de carga para medir a entrada de torque. Todos esses instrumentos são amostrados cerca de 1000 vezes por segundo e gravados no meu laptop, usando o registrador Vernier como um dispositivo de passagem AD. No meu laptop, o software associado pode executar cálculos em tempo real com base nas entradas, combinando dados de torque e velocidade para fornecer potência do eixo de entrada em tempo real em Watts e dados de saída em tempo real em Watts elétricos. Eu não terminei este teste, e a opinião de alguém que tem um melhor entendimento seria útil.
Um problema que eu tenho é que este alternador é realmente um projeto paralelo, então não quero gastar muito mais tempo nele. Do jeito que está, acho que posso usá-lo para uma carga controlável para minha pesquisa VAWT, mas eventualmente gostaria de trabalhar com pessoas para refiná-lo, de modo que seja uma combinação eficiente para minha turbina.
Quando comecei a pesquisar VAWT há cerca de 15 anos, percebi que testar VAWTs e outros motores primários é mais complexo do que a maioria das pessoas imagina.
Um problema principal é que a energia representada em um fluido em movimento é exponencial para sua taxa de movimento. Isso significa que, à medida que você dobra a velocidade de um fluxo, a energia contida no fluxo aumenta 8x (é ao cubo). Isso é um problema, pois os alternadores são mais lineares e, em geral, se você dobrar a rotação de um alternador, obtém cerca de 2x os watts.
Essa incompatibilidade fundamental entre a turbina (dispositivo de coleta de energia) e o alternador (potência do eixo para energia elétrica útil) torna difícil escolher um alternador para uma turbina eólica. Se você escolher um alternador compatível para sua turbina eólica que gerará a maior potência disponível com ventos de 20 km / h, provavelmente não começará a girar até 20-25 km / h, pois a carga do alternador na turbina será muito alta. Com essa combinação de alternador, uma vez que o vento está acima de 20 km, não só a turbina irá capturar apenas uma fração da energia disponível no vento de alta velocidade, a turbina pode acelerar e ser danificada porque a carga fornecida pelo alternador não é alta o suficiente.
Na última década, uma solução tornou-se mais econômica devido à queda no preço dos eletrônicos de controle. Em vez de tentar corresponder a uma faixa de velocidades, o projetista calcula a velocidade máxima em que o dispositivo deve operar e escolhe um alternador com base na quantidade de energia e na velocidade ideal para a turbina nessa velocidade, ou um pouco acima. Este alternador, se conectado à sua carga, normalmente forneceria muito torque na faixa de baixa velocidade, e a turbina sobrecarregada não capturaria toda a energia que poderia ter se estivesse carregada corretamente. Para criar a carga adequada, é adicionado um controlador que desconecta momentaneamente o alternador da carga elétrica, permitindo que a turbina atinja a velocidade adequada e o alternador e a carga sejam reconectados. Isso é chamado de MPPT (Multi Power Point Tracking). O controlador é programado de forma que conforme a velocidade da turbina muda (ou a tensão do alternador aumenta), o alternador é conectado ou desconectado, cerca de mil vezes por segundo, para corresponder à carga programada para aquela velocidade ou tensão.
Recomendado:
Sensor de direção de fluxo: 16 etapas
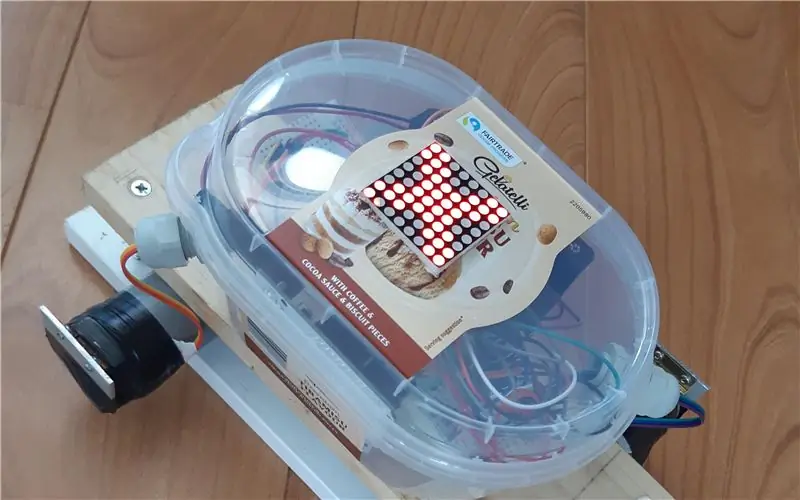
Sensor de direção de fluxo: De sensor zal de stromingsrichting in één dimensie meten, namelijk stroming naar links of naar rechts. De sensor bestaat uit twee buizen die beiden loodrecht op de stromingsrichting staan. Beide buizen hebben een klepje die opengaat als er stroming
Alternador GO Kart: 4 etapas
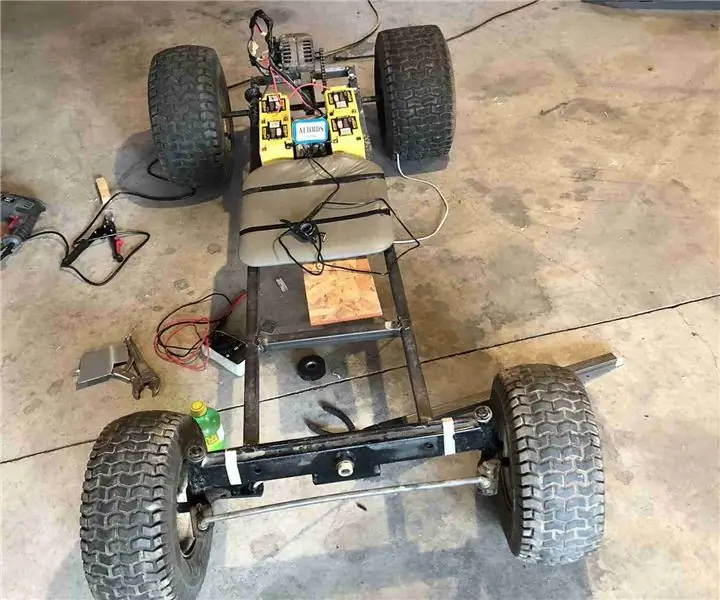
Alternador GO Kart: Bem, olá, este não é realmente um como fazer, mas sim um compartilhamento de informações. Então, para começar: Meu nome é AJ, sou um estudante de intercâmbio da Alemanha nos Estados Unidos. Eu fiz o Go kart em um esforço para uma aplicação no MIT. Eu queria fazer um seguidor
Medição de fluxo com medidores de fluxo de água (ultrassônico): 5 etapas (com imagens)
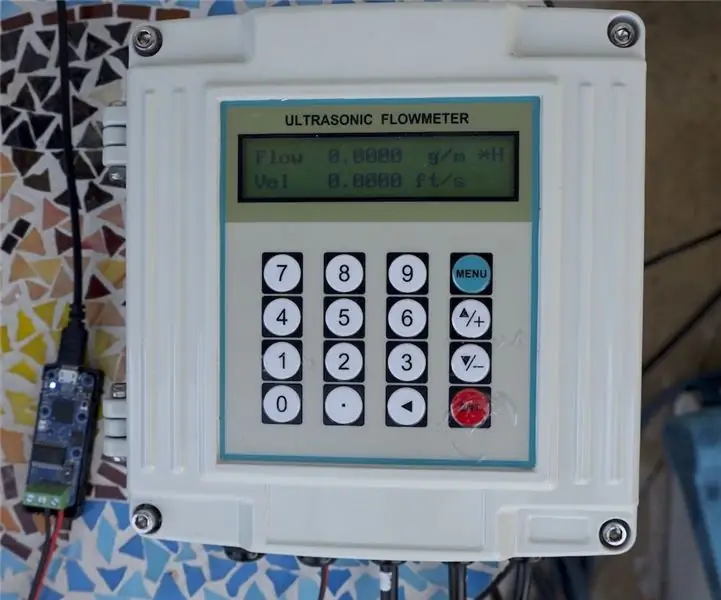
Medição de vazão com medidores de vazão de água (ultrassônico): a água é um recurso crítico para o nosso planeta. Os seres humanos precisam de água todos os dias. E a água é necessária para uma variedade de indústrias e nós, humanos, precisamos dela todos os dias. À medida que a água se tornou mais valiosa e escassa, a necessidade de monitoramento eficaz e o homem
Autoexcite um alternador sem qualquer gerador DC, banco de capacitores ou bateria: 5 etapas (com fotos)
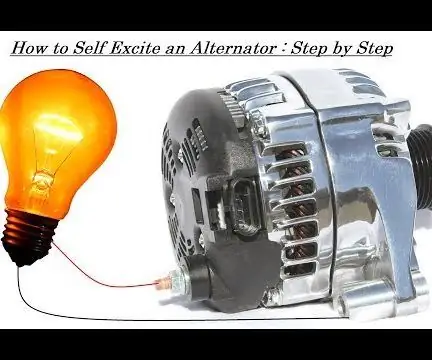
Autoexcite um alternador sem qualquer gerador DC, banco de capacitores ou bateria: Olá! Este instrumento é para converter um alternador excitado por campo em um alternador autoexcitado. A vantagem deste truque é que você não terá que alimentar o campo deste alternador com uma bateria de 12 volts, mas em vez disso ele se auto-alimentará para que você
Alternador de som: 9 etapas
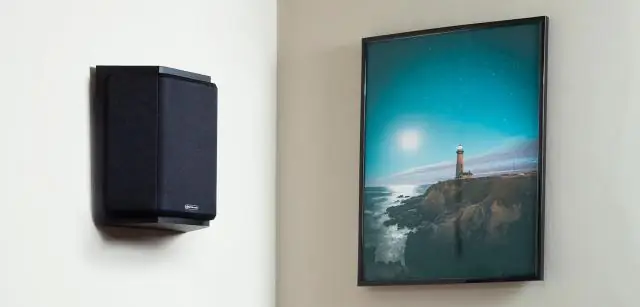
Comutador de som: Você já teve sua música no máximo no trabalho e não percebeu que alguém estava tentando falar com você? Pior ainda, você já quis dormir no trabalho, mas não tinha uma boa maneira de acordar se alguém (como seu chefe) estivesse para entrar em você