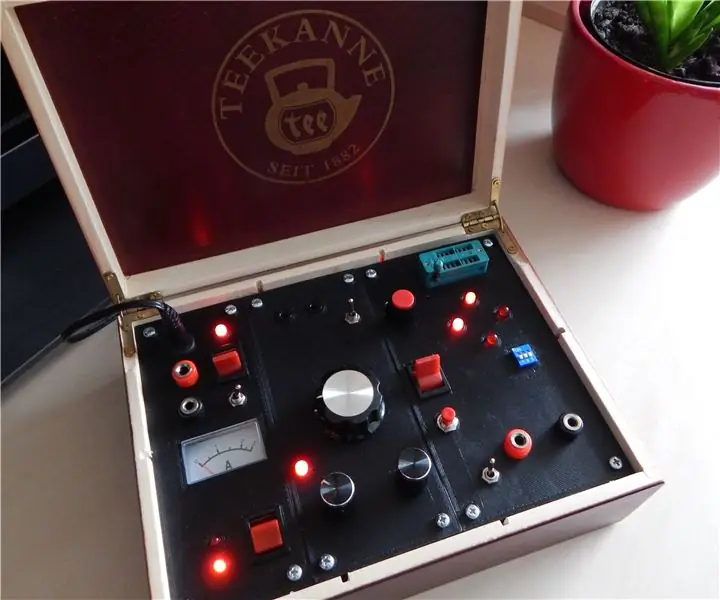
Índice:
- Etapa 1: DC e teoria de controle de passo
- Etapa 2: Diagrama de Circuito
- Etapa 3: esquemas
- Etapa 4: Componentes e ferramentas necessários
- Etapa 5: Design do painel frontal
- Etapa 6: impressão 3D e pintura em spray
- Etapa 7: Fiação do painel
- Etapa 8: Conectores da placa do painel
- Etapa 9: PCB
- Etapa 10: Arduino
- Etapa 11: Montagem e teste
- Etapa 12: Outro
2025 Autor: John Day | [email protected]. Última modificação: 2025-01-23 15:03

Há alguns meses, um amigo meu deu-me algumas impressoras jato de tinta e copiadoras descartadas. Eu estava interessado em colher suas unidades de fonte de alimentação, cabos, sensores e principalmente motores. Recuperei o que pude e queria testar todas as peças para ter certeza de que estavam funcionando. Alguns motores eram classificados em 12 V, alguns em 5 V, alguns eram de passo e outros eram motores CC. Se eu tivesse um dispositivo, onde pudesse simplesmente conectar o motor, definir a frequência, o ciclo de trabalho e selecionar um método de passo para testá-lo.
Decidi construí-lo sem usar processador de sinal digital ou microcontrolador. O humilde 555 ou tl741 como oscilador, contador 4017 e muitas portas lógicas para modos de motor de passo. No começo eu me diverti muito projetando o circuito, bem como projetando o painel frontal do dispositivo. Encontrei uma caixa de chá de madeira decente para colocar tudo dentro. Dividi o circuito em quatro partes e comecei a testá-lo em uma placa de ensaio. Logo, os primeiros sinais de frustração apareceram. Foi uma bagunça. Muitos portões, muitos ICs, fios. Não funcionou bem e eu estava pensando entre duas opções: Torná-lo muito simples - apenas para motores DC, ou deixá-lo de lado e terminar às vezes mais tarde … Escolhi a segunda opção.
Etapa 1: DC e teoria de controle de passo
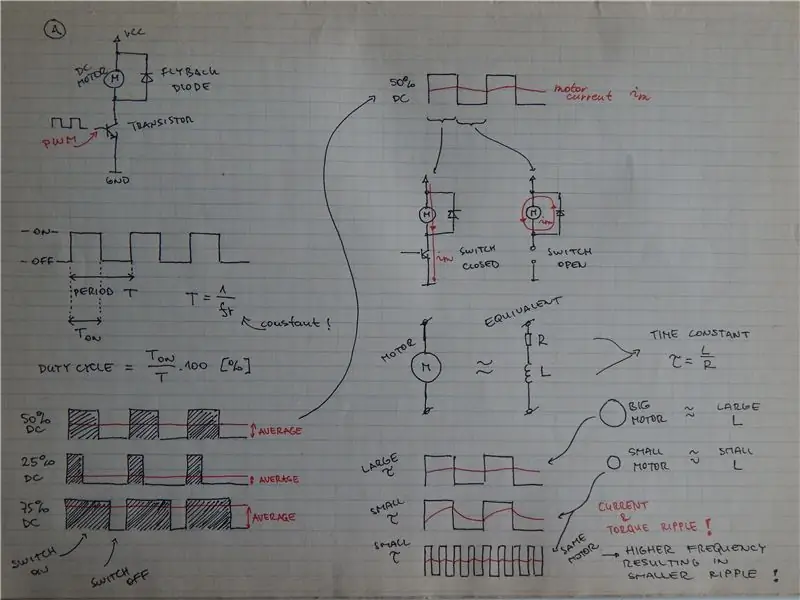
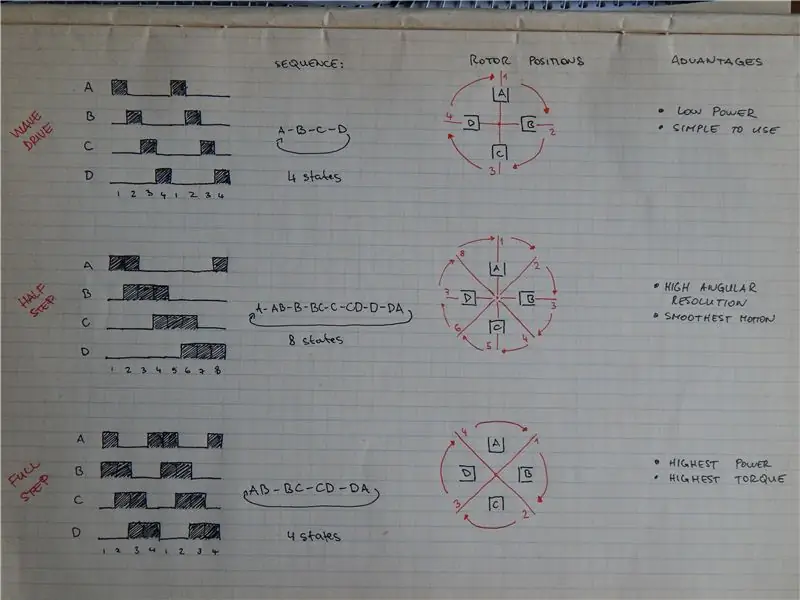
Motor DC
A forma mais comum de controlar um motor DC é através da chamada modulação por largura de pulso (PWM). O PWM é aplicado a uma chave específica e liga e desliga o motor. Na imagem você pode ver o período de comutação indicado e sua relação com a frequência, o tempo de comutação também é indicado. O ciclo de trabalho é definido como o tempo de comutação dividido pelo período total. Se mantivermos a frequência constante, a única maneira de alterar o ciclo de trabalho é alterar o tempo de ativação. Ao aumentar o ciclo de trabalho, o valor médio da tensão aplicada ao motor também aumenta. Devido à tensão mais alta, uma corrente mais alta flui através do motor CC e o rotor gira mais rápido.
Mas que frequência escolher? Para responder a essa pergunta, vamos examinar mais de perto o que é realmente um motor CC. Equivalentemente, ele pode ser descrito como um filtro RL (negligenciando o EMF de volta apenas por um momento). Se uma tensão é aplicada ao motor (filtro RL), a corrente aumenta com uma constante de tempo tau que é igual a L / R. No caso do controle PWM, quando a chave é fechada, a corrente que flui através do motor aumenta e diminui durante o tempo em que o interruptor está desligado. Neste ponto, a corrente tem a mesma direção de antes e flui através do diodo flyback. Motores com maior potência têm uma indutância maior e, portanto, uma constante de tempo maior do que motores menores. Se a frequência for baixa quando o motor pequeno é alimentado, ocorre uma rápida diminuição da corrente durante o tempo de desligamento, seguido por um grande aumento durante o tempo de ligamento. Esta ondulação de corrente também faz com que o torque do motor ondule. Nós não queremos isso. Portanto, ao alimentar motores menores, a frequência PWM deve ser mais alta. Usaremos esse conhecimento no projeto em etapas posteriores.
Motor de passo
Se quisermos controlar um motor de passo unipolar, usado em eletrônica de hobby, temos uma escolha de 3 opções básicas de controle (modos) - Wave drive (WD), Half Step (HS) e Full Step (FS). A seqüência de modos individuais e a posição do rotor são indicadas na figura (para simplificar, indiquei um motor com dois pares de pólos). Neste caso, Wave Drive e Full Step fazem com que o rotor gire 90 graus e pode ser alcançado repetindo 4 estados. No modo Half Step, precisamos de uma sequência de 8 estados.
A escolha do modo depende dos requisitos do sistema - se precisarmos de um grande torque, a melhor escolha é Full Step, se um torque mais baixo for suficiente e talvez alimentemos nosso circuito com a bateria, o modo wave drive é preferido. Em aplicações onde desejamos obter a mais alta resolução angular e movimento mais suave, o modo Half Drive é a escolha ideal. O torque neste modo é cerca de 30% menor do que no modo Full Drive.
Etapa 2: Diagrama de Circuito
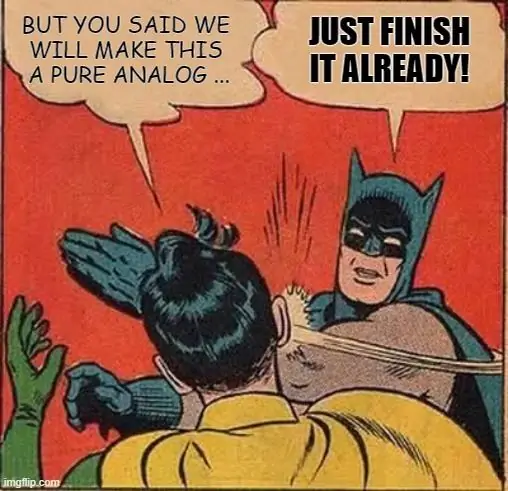
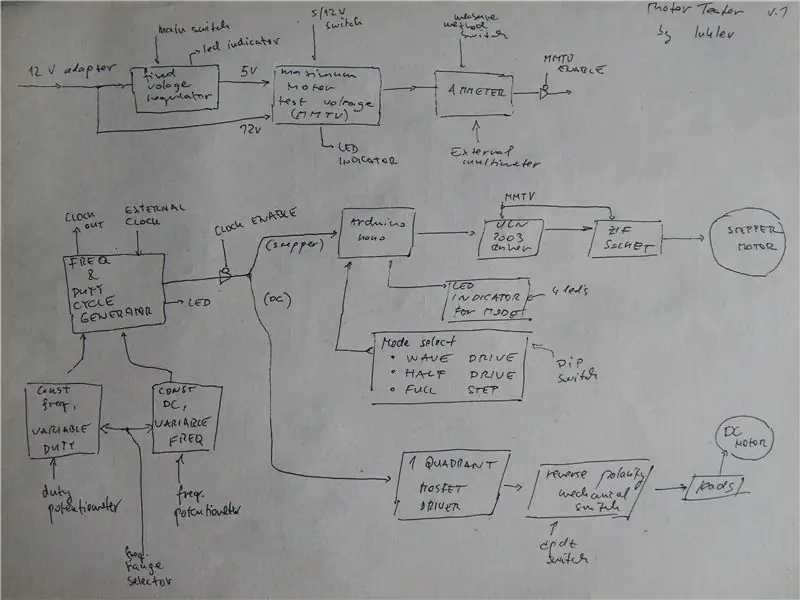
Este meme simples descreve apropriadamente meu processo de pensamento durante o design.
A parte superior do diagrama descreve a fonte de alimentação - um adaptador de 12 volts, que é reduzido para 5 volts por um regulador linear. Eu queria poder escolher a tensão máxima de teste do motor (MMTV) - 12 ou 5 volts. O amperímetro embutido contornará os circuitos de controle e medirá apenas a corrente do motor. Também seria conveniente poder alternar entre a medição de corrente interna e externa usando um multímetro.
O oscilador irá operar em dois modos: o primeiro é uma frequência constante e um ciclo de trabalho variável, e o segundo é uma frequência variável. Ambos os parâmetros poderão ser ajustados usando potenciômetros, e uma chave rotativa mudará os modos e faixas. O sistema também incluirá uma alternância entre o relógio interno e externo por meio de um conector jack de 3,5 mm. O relógio interno também será conectado ao painel por meio de um conector de 3,5 mm. Um interruptor e um botão para ativar / desativar o relógio. O driver do motor DC será um driver mosfet de canal N de quadrante único. A direção será alterada usando o interruptor dpdt mecânico. Os condutores do motor serão conectados por meio de conectores banana.
A sequência do motor de passo será controlada por um arduino, que também reconhecerá 3 modos de controle especificados pela chave dip. O driver do motor de passo será uln2003. O Arduino também controlará 4 LEDs que representarão a animação dos enrolamentos do motor alimentado nesses modos. O motor de passo será conectado ao testador por meio de um soquete ZIF.
Etapa 3: esquemas
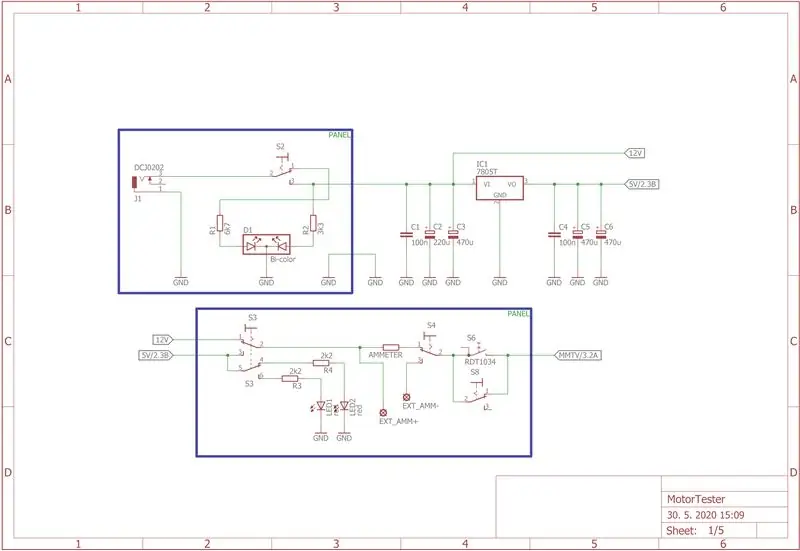
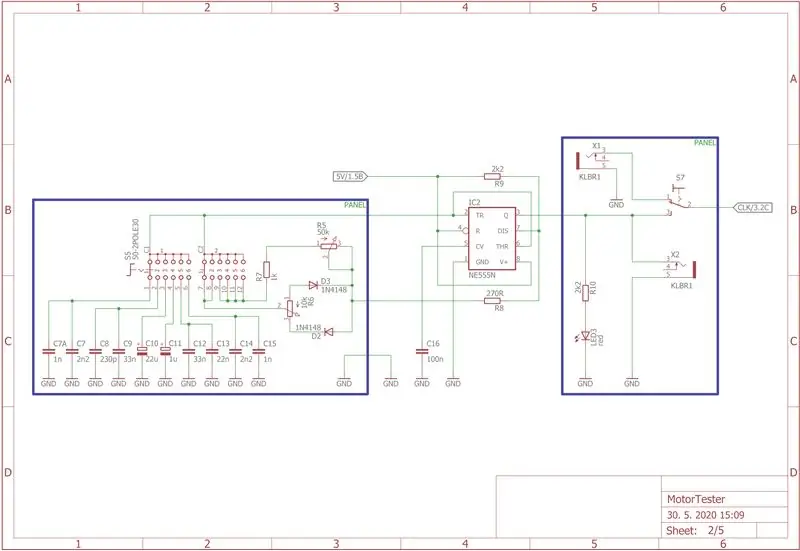
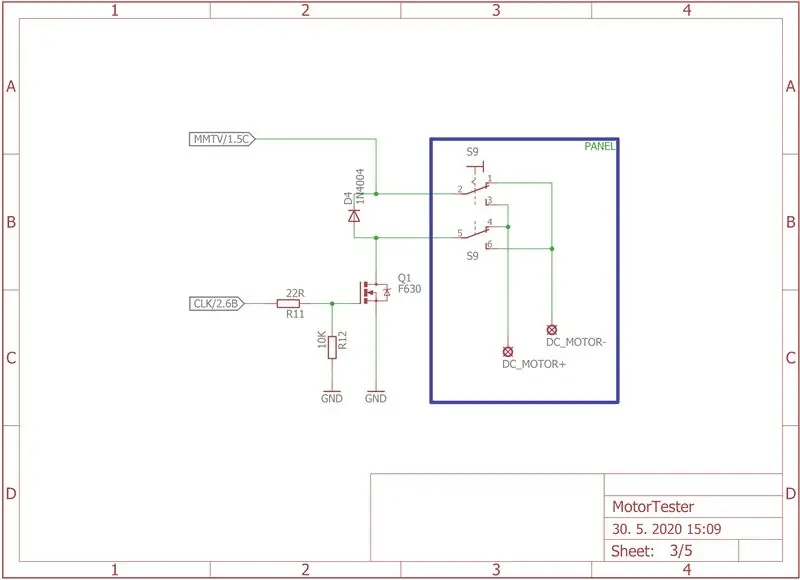
Os esquemas são divididos em cinco partes. Os circuitos enquadrados em caixas azuis representam os componentes que estarão no painel.
- Fonte de energia
- Oscilador
- Driver DC
- Driver Arduino Stepper
- Driver Logic Gates Stepper
Folha nº 5 é a razão pela qual deixei este projeto mentindo. Esses circuitos formam sequências para os modos de controle mencionados anteriormente - WD, HS e FS. Esta parte foi substituída pelo arduino completamente na folha nº. 4. O esquema completo do Eagle também está anexado.
Etapa 4: Componentes e ferramentas necessários

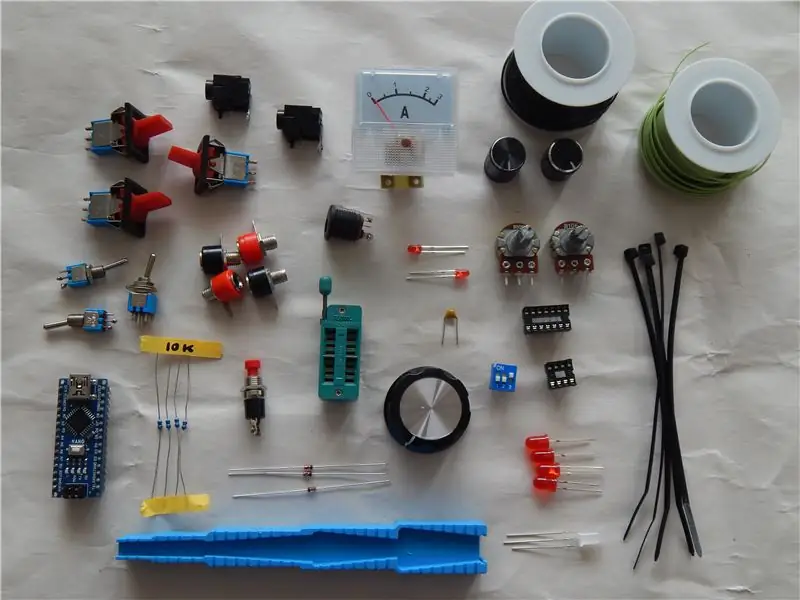
Componentes e ferramentas necessários:
- Multímetro
- Paquímetro
- Cortador de papelão
- Marcador
- Pinças
- Alicate fino
- Alicate de corte
- Alicate para decapagem de arame
- Ferro de solda
- Solda
- Colofonia
- Fios (24 awg)
- 4x switch spdt
- 2x switch dpdt
- 4x banana jack
- Botão de apertar
- Soquete ZIF
- 2x jack de 3,5 mm
- Conector DC
- Arduino nano
- Interruptor DIP de 3 pólos
- LED 2x 3 mm
- LED 5x 5 mm
- LED bicolor
- Botões do potenciômetro
- Soquetes DIP
- PCB universal
- Conectores Dupont
- Abraçadeiras plásticas
E
- Potenciômetros
- Resistores
- Capacitores
com os valores escolhidos, correspondendo às faixas de frequência e brilho dos LEDs.
Etapa 5: Design do painel frontal
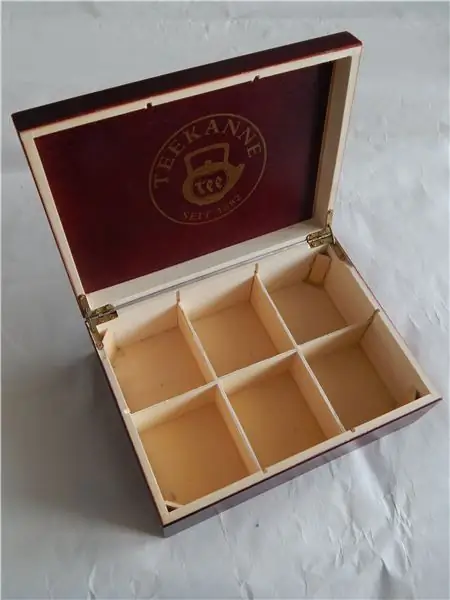
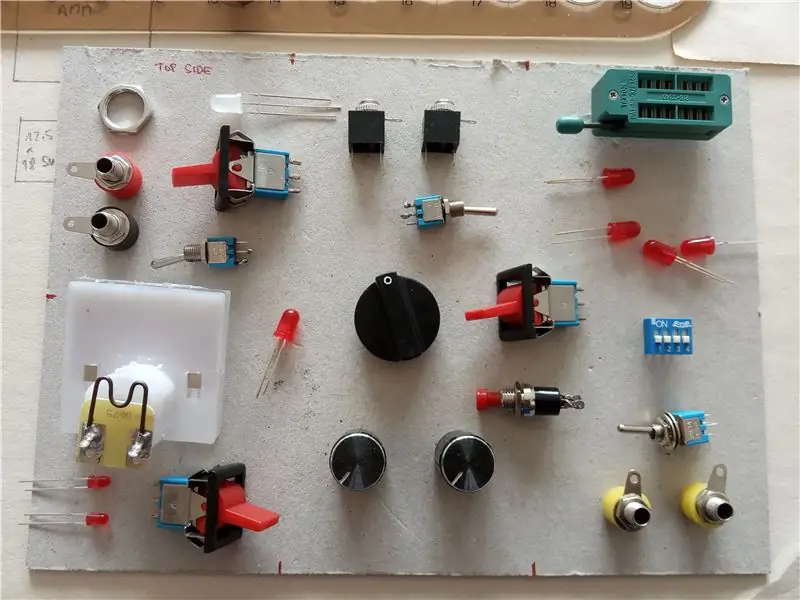
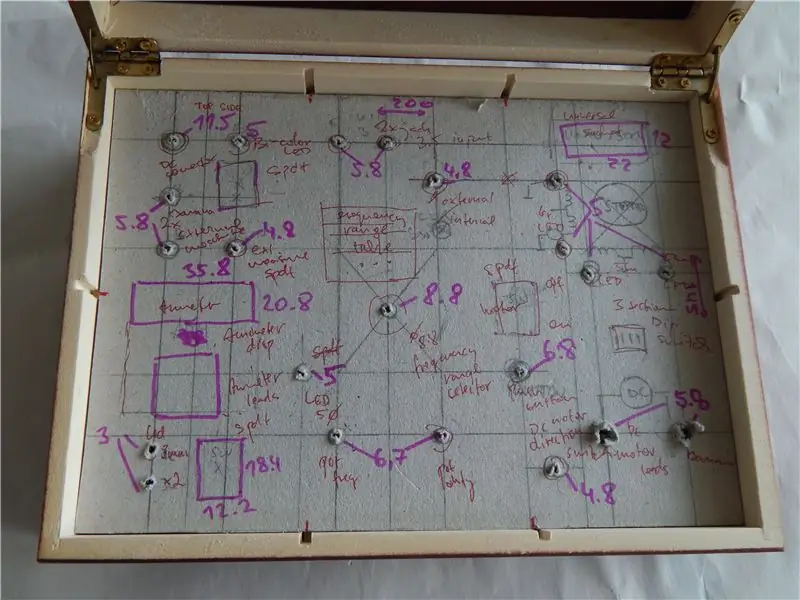
O testador foi colocado em uma velha caixa de chá de madeira. Primeiro medi as dimensões internas e depois cortei um retângulo de papelão duro, que serviu de gabarito para a colocação dos componentes. Quando fiquei satisfeito com a colocação das peças, medi cada posição novamente e criei um design de painel no Fusion360. Dividi o painel em 3 partes menores, para simplificar a impressão 3D. Também projetei um suporte em forma de L para fixar os painéis nas laterais internas da caixa.
Etapa 6: impressão 3D e pintura em spray
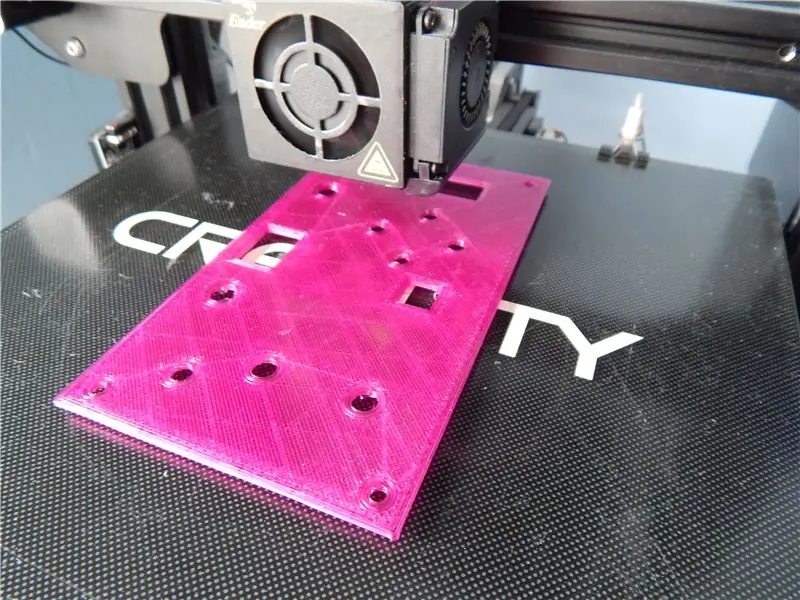
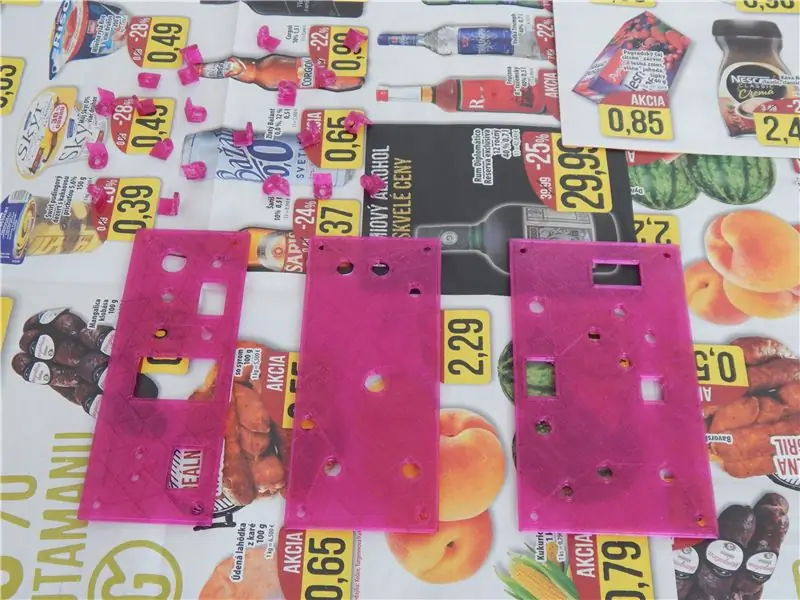
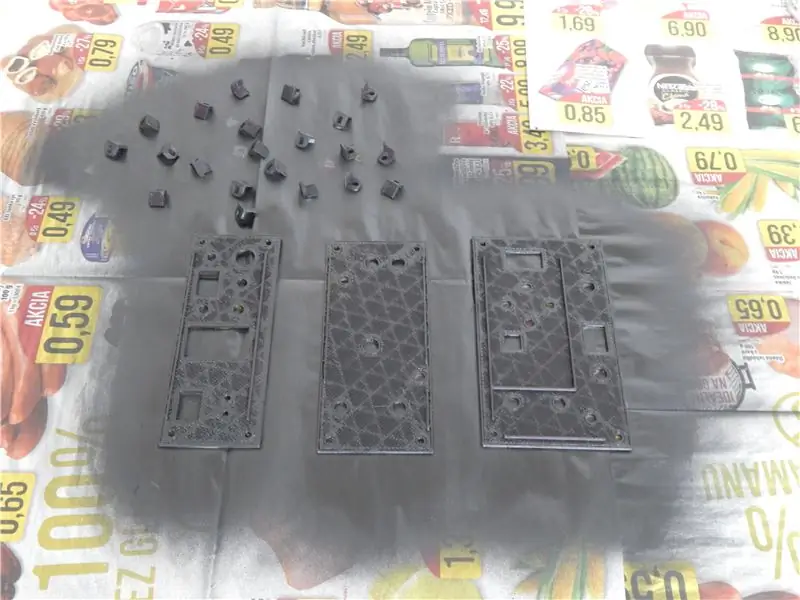
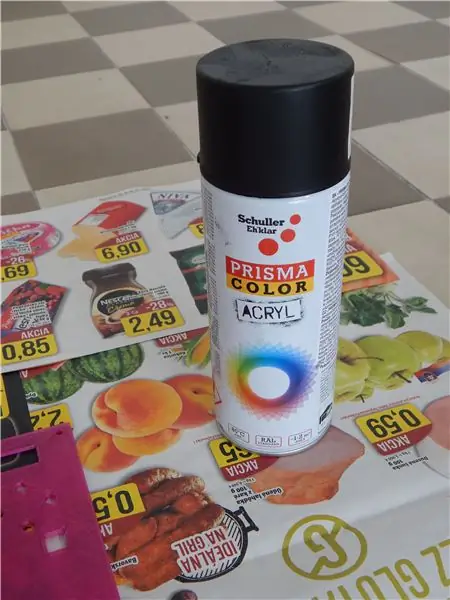
Os painéis foram impressos em impressora Ender-3, a partir do material residual que tinha em casa. Era um petg rosa transparente. Após a impressão, borrifei os painéis e suportes com tinta acrílica preta fosca. Para uma cobertura completa, apliquei 3 demãos, coloquei do lado de fora por algumas horas para secar e ventilar por cerca de meio dia. Tenha cuidado, os vapores da tinta podem ser prejudiciais. Sempre use-os apenas em uma sala ventilada.
Etapa 7: Fiação do painel
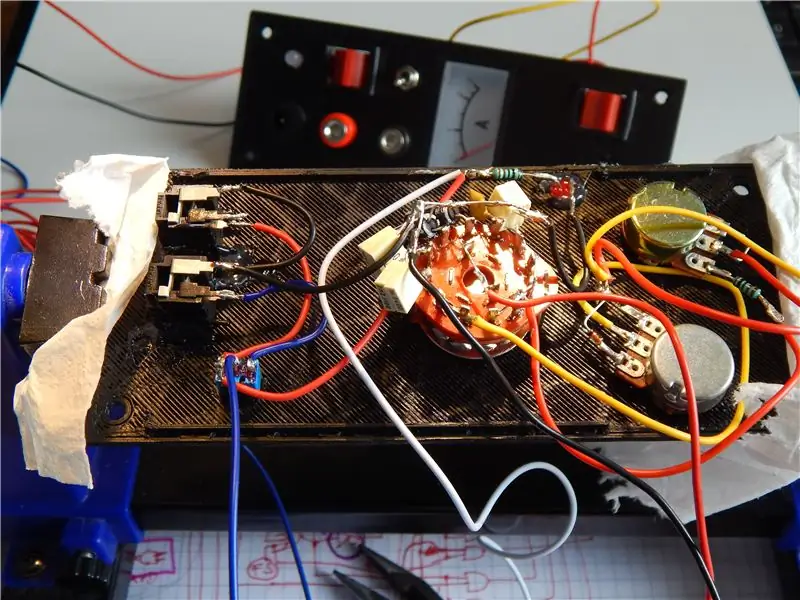
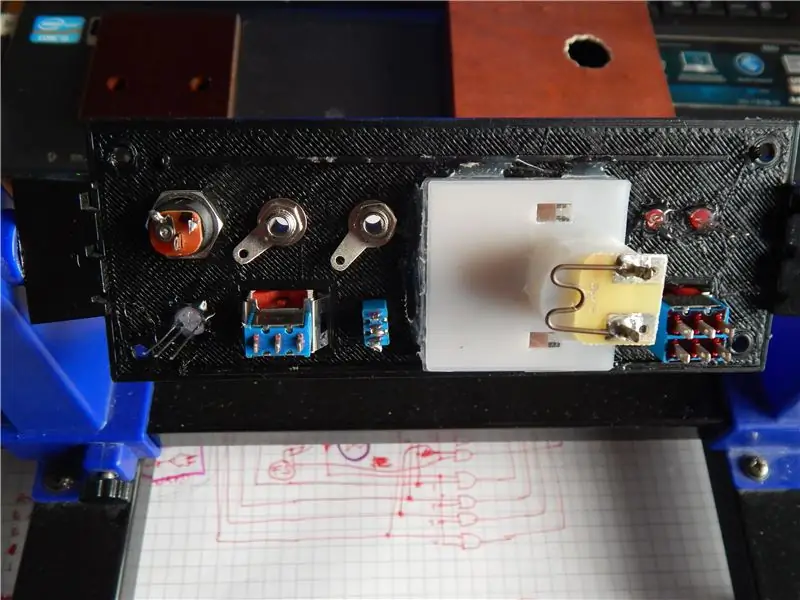
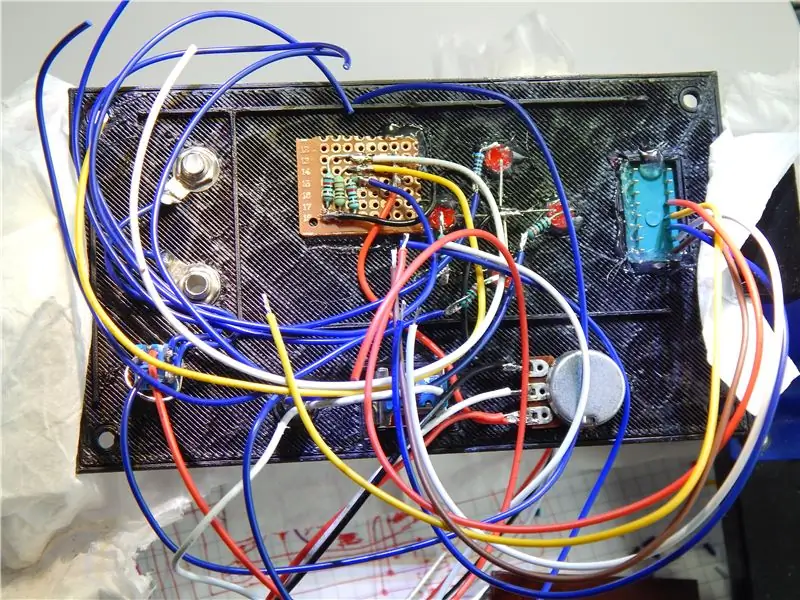
Pessoalmente, meu favorito, mas a parte mais demorada (peço desculpas antecipadamente por não usar os tubos retráteis, eu estava com falta de tempo - caso contrário, eu definitivamente os usaria).
Suportes ajustáveis ajudam muito na montagem e manuseio de painéis. Também é possível usar a chamada terceira mão, mas prefiro a titular. Cobri suas alças com um pano de tecido para que o painel não fosse arranhado durante o trabalho.
Inseri e aparafusei todos os interruptores e potenciômetros, LEDs e outros conectores no painel. Posteriormente, estimei o comprimento dos fios que irão conectar os componentes do painel e também aqueles que serão usados para conectar ao pcb. Eles tendem a ser um pouco mais longos e é bom aumentá-los um pouco.
Quase sempre uso fluxo de solda líquido ao soldar conectores. Eu aplico uma pequena quantidade no pino e, em seguida, estanho e conecto ao fio. O fluxo remove qualquer metal oxidado das superfícies, tornando muito mais fácil soldar a junta.
Etapa 8: Conectores da placa do painel
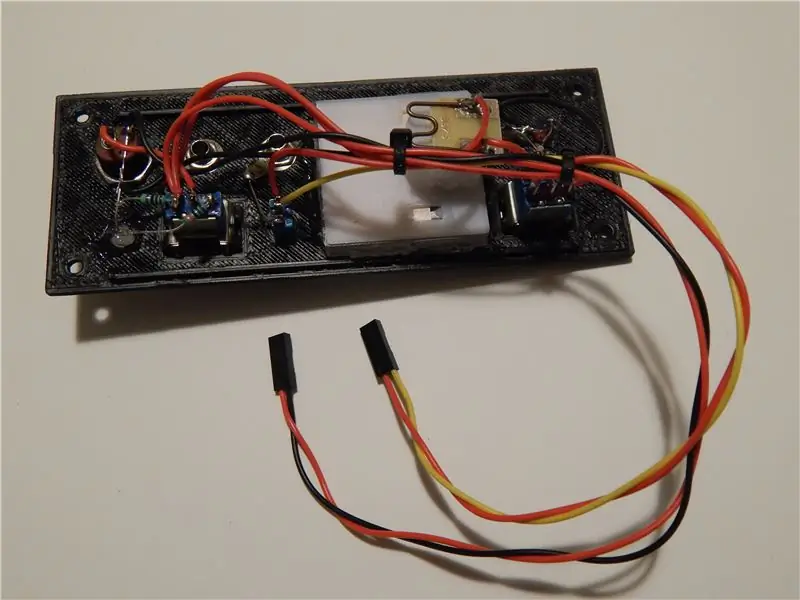
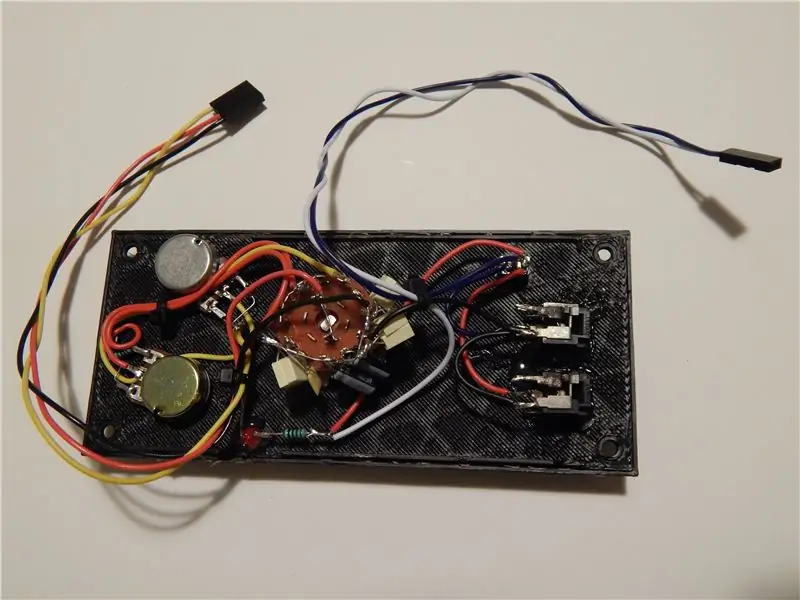
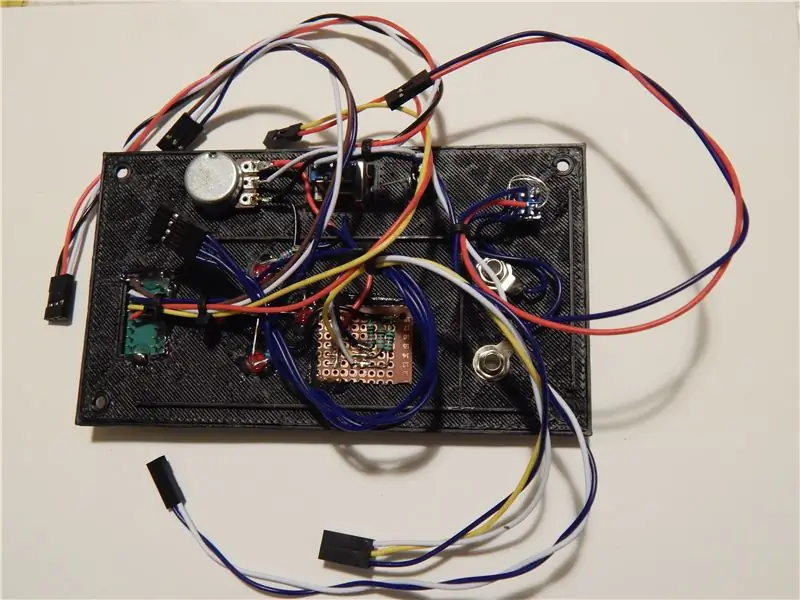
Para conectar o painel ao pcb, usei conectores do tipo dupont. Eles estão amplamente disponíveis, baratos e, o mais importante, pequenos o suficiente para caber confortavelmente na caixa escolhida. Os cabos são dispostos de acordo com o esquema, em pares, trigêmeos ou quádruplos. Eles são codificados por cores para serem facilmente identificados e fáceis de conectar. Ao mesmo tempo, é prático para o futuro não se perder em um emaranhado uniforme de fios. Finalmente, eles são presos mecanicamente com braçadeiras de plástico.
Etapa 9: PCB
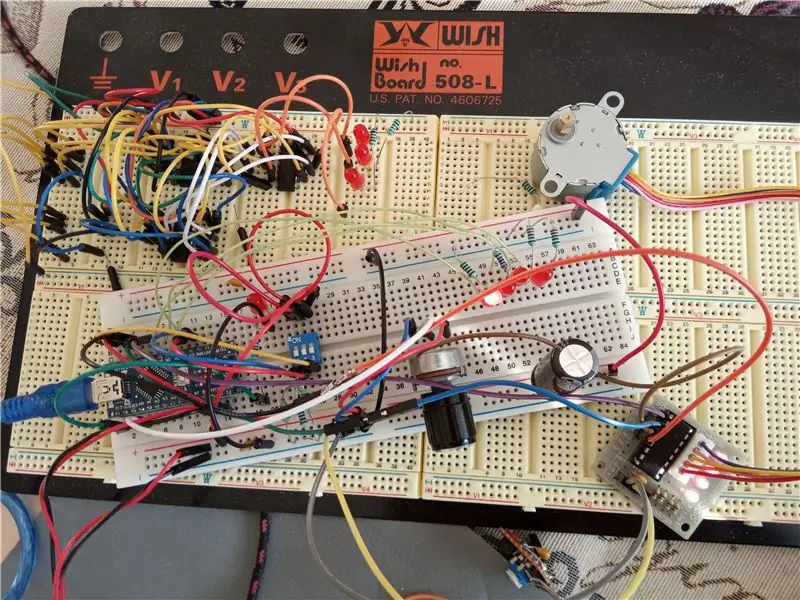
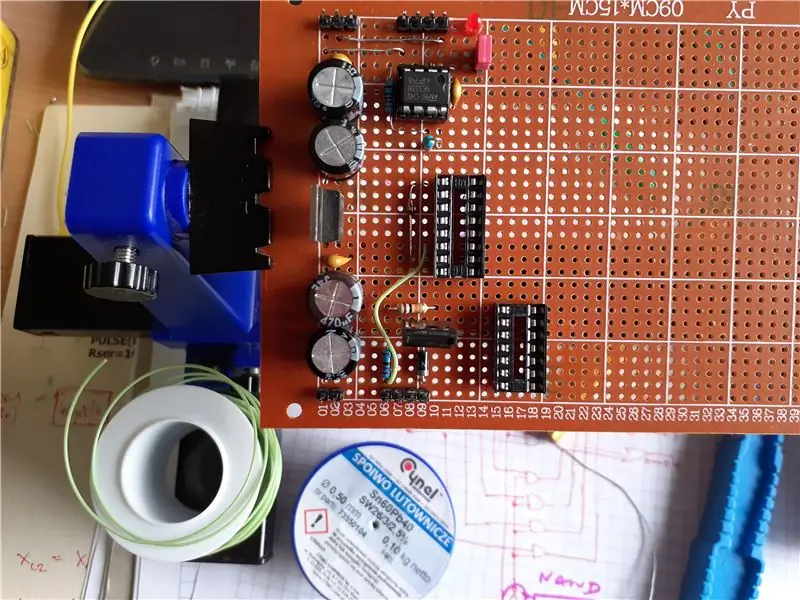
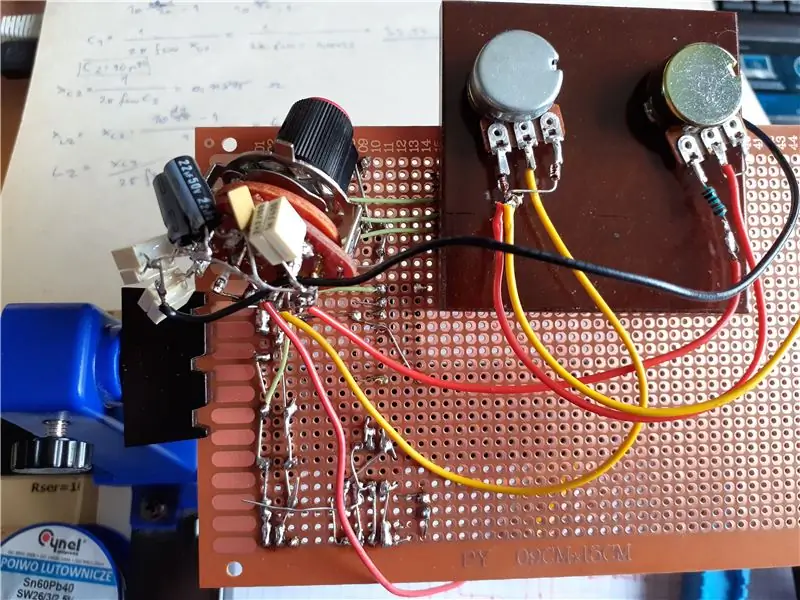
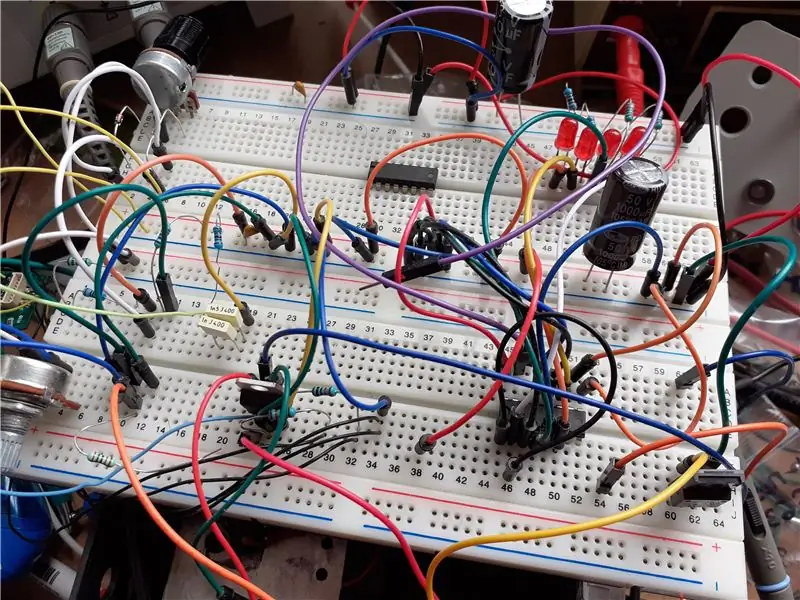
Como a parte do diagrama que fica fora do painel não é extensa, resolvi fazer um circuito em um pcb universal. Usei um pcb normal de 9x15 cm. Coloquei os capacitores de entrada junto com o regulador linear e dissipador de calor no lado esquerdo. Posteriormente, instalei soquetes para IC 555, contador 4017 e driver ULN2003. O soquete para o contador 4017 permanecerá vazio, pois sua função é assumida pelo arduino. Na parte inferior, há um driver para o mosfet F630 do canal N.
Etapa 10: Arduino
A conexão do sistema com o arduino está documentada na planilha esquemática nº. 4. o seguinte arranjo de pinos foi usado:
- 3 entradas digitais para chave DIP - D2, D3, D12
- 4 saídas digitais para indicadores LED - D4, D5, D6, D7
- 4 saídas digitais para driver de passo - D8, D9, D10, D11
- Uma entrada analógica para potenciômetro - A0
Os indicadores LED que representam os enrolamentos individuais do motor acendem lentamente quando os enrolamentos são realmente alimentados. Se a velocidade de piscar dos LEDs correspondesse aos enrolamentos do motor, veríamos isso como uma iluminação contínua de todos eles. Eu queria conseguir uma representação clara e simples e as diferenças entre os modos individuais. Portanto, os indicadores LED são controlados independentemente em intervalos de 400 ms.
As funções de controle do motor de passo foram criadas pelo autor Cornelius em seu blog.
Etapa 11: Montagem e teste
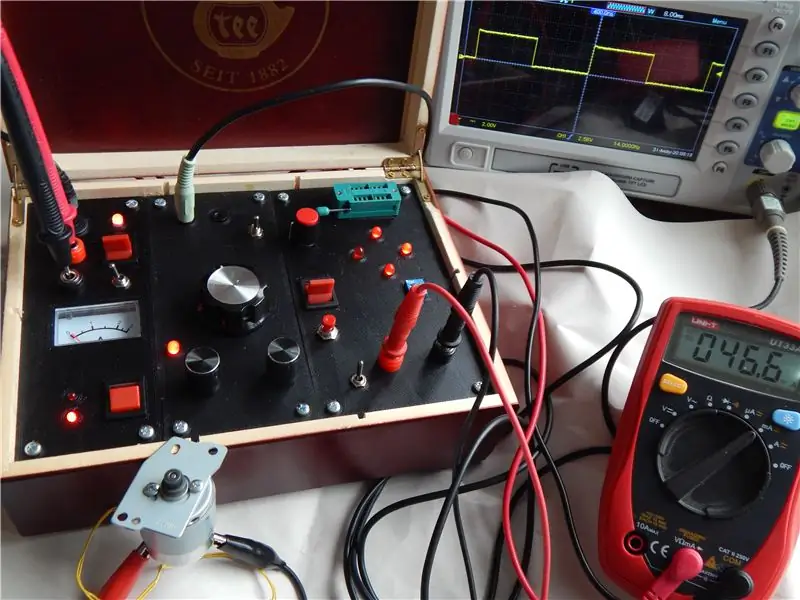
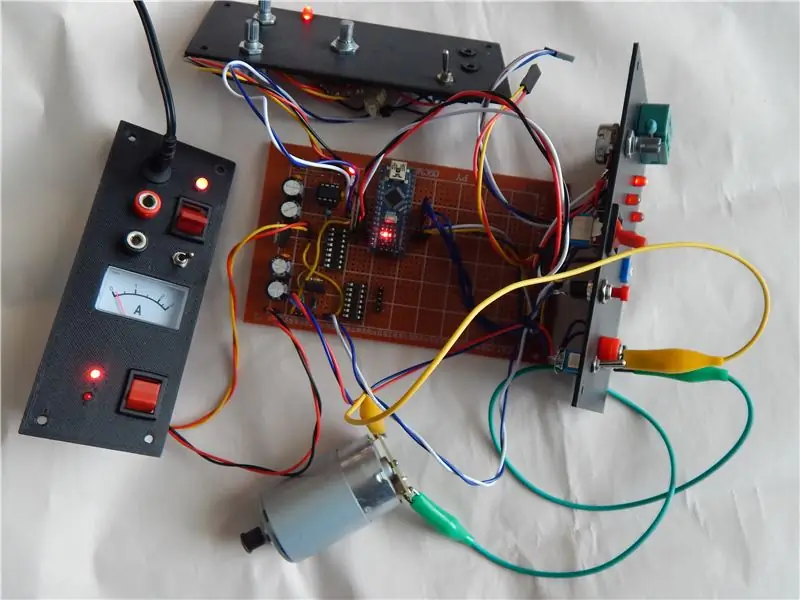
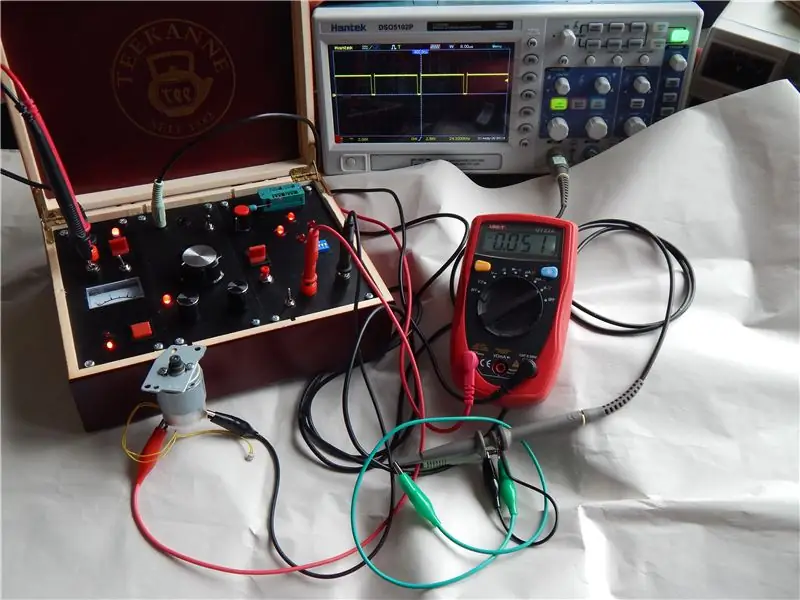
Por fim, conectei todos os painéis ao pcb e comecei a testar o testador. Eu medi o oscilador e seus intervalos com um osciloscópio, bem como o controle de freqüência e ciclo de trabalho. Não tive grandes problemas, a única mudança que fiz foi adicionar capacitores de cerâmica em paralelo aos capacitores eletrolíticos de entrada. O capacitor adicionado fornece atenuação da interferência de alta frequência introduzida no sistema por elementos parasitas do cabo adaptador DC. Todas as funções do testador funcionam conforme necessário.
Etapa 12: Outro
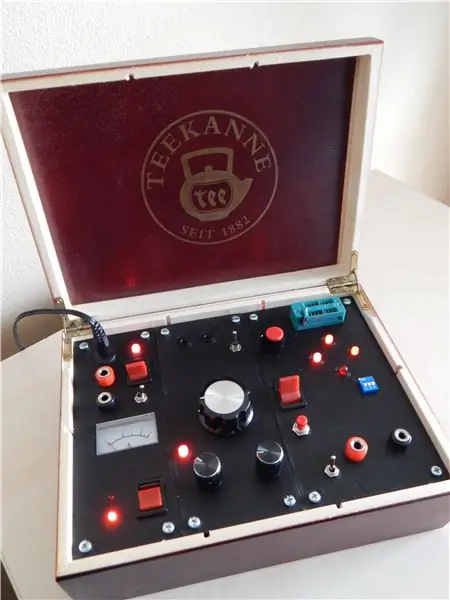
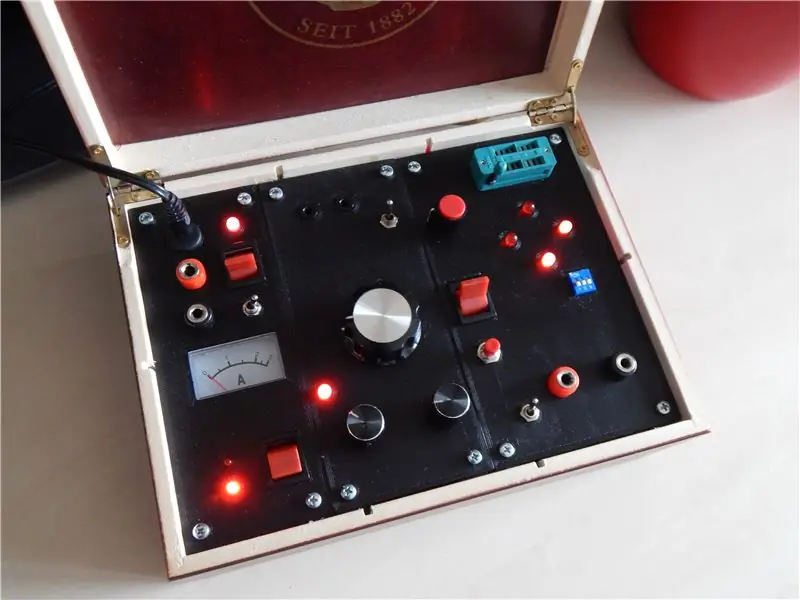
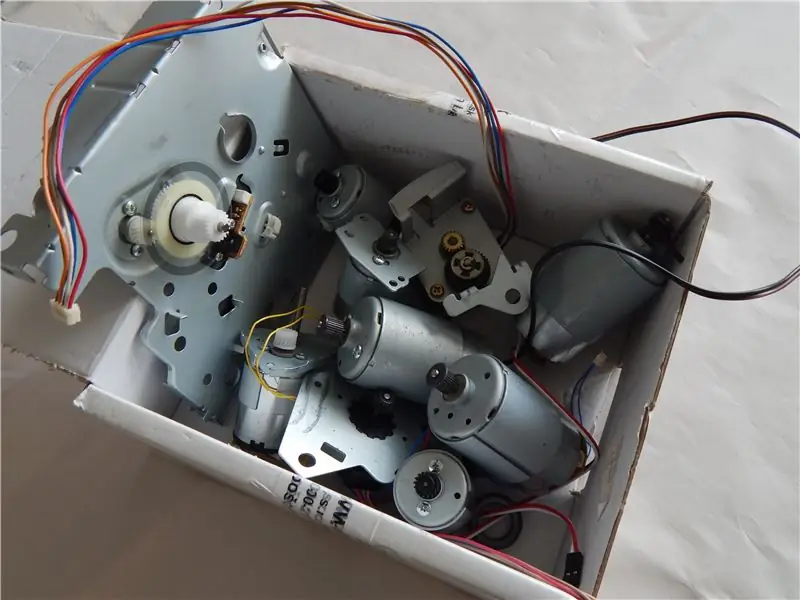
Agora posso finalmente simplesmente testar todos os motores que consegui salvar ao longo dos anos.
Se você estiver interessado na teoria, esquema ou qualquer coisa sobre o testador, não hesite em entrar em contato comigo.
Obrigado pela leitura e pelo seu tempo. Fique saudável e seguro.
Recomendado:
Motor de passo controlado por motor de passo sem microcontrolador !: 6 etapas
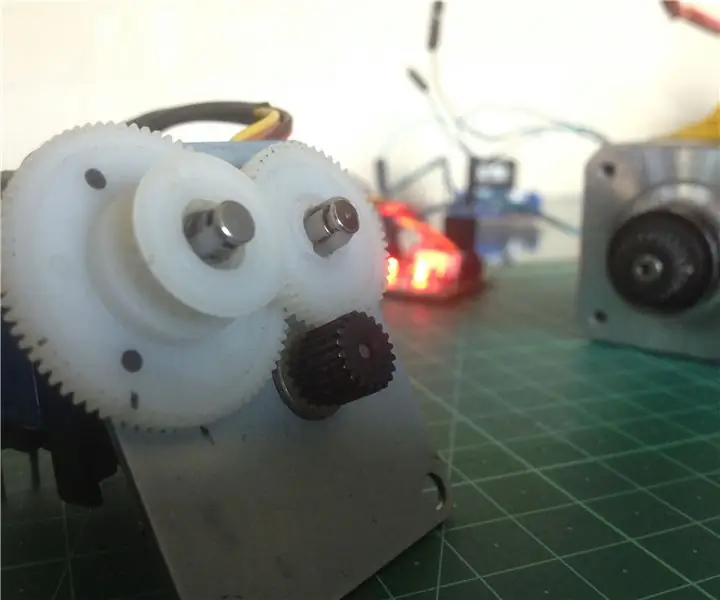
Motor de passo controlado por motor de passo sem microcontrolador !: Neste instrutivo rápido, faremos um controlador de motor de passo simples usando um motor de passo. Este projeto não requer circuitos complexos ou um microcontrolador. Então, sem mais delongas, vamos começar
Motor de passo controlado por motor de passo sem microcontrolador (V2): 9 etapas (com imagens)
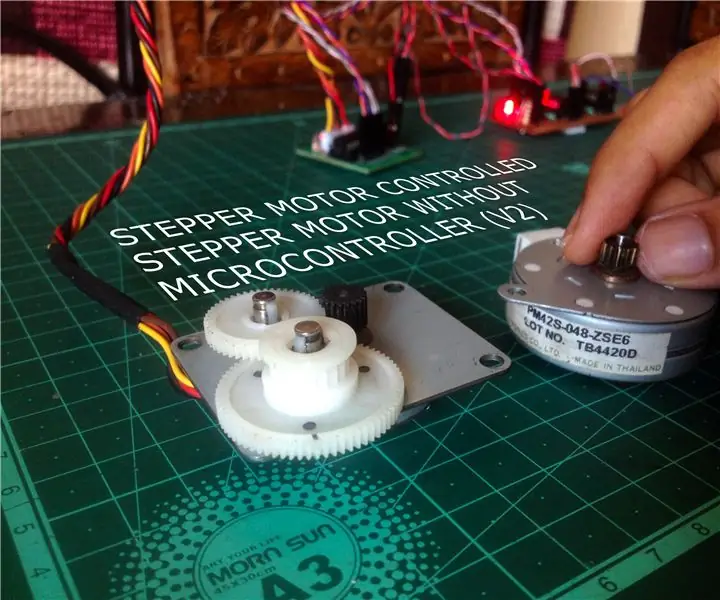
Motor de passo controlado por motor de passo sem microcontrolador (V2): Em um dos meus Instructables anteriores, mostrei como controlar um motor de passo usando um motor de passo sem um microcontrolador. Foi um projeto rápido e divertido, mas veio com dois problemas que serão resolvidos neste Instructable. Então, sagacidade
Locomotiva modelo com motor de passo controlado - Motor de passo como codificador giratório: 11 etapas (com imagens)
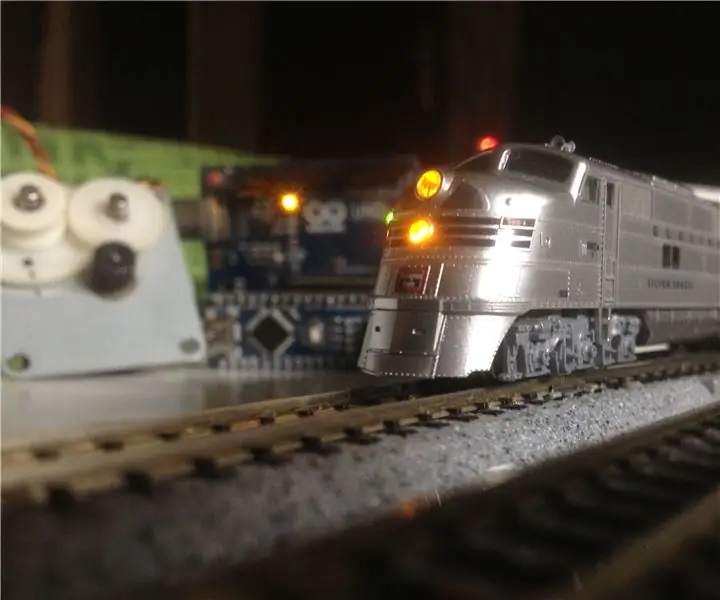
Locomotiva modelo com motor de passo controlado | Motor de passo como codificador giratório: Em um dos instrutíveis anteriores, aprendemos como usar um motor de passo como codificador giratório. Neste projeto, agora usaremos aquele motor de passo girado em codificador rotativo para controlar um modelo de locomotiva usando um microcontrolador Arduino. Então, sem fu
Motor de passo controlado por motor de passo - Motor de passo como codificador giratório: 11 etapas (com imagens)
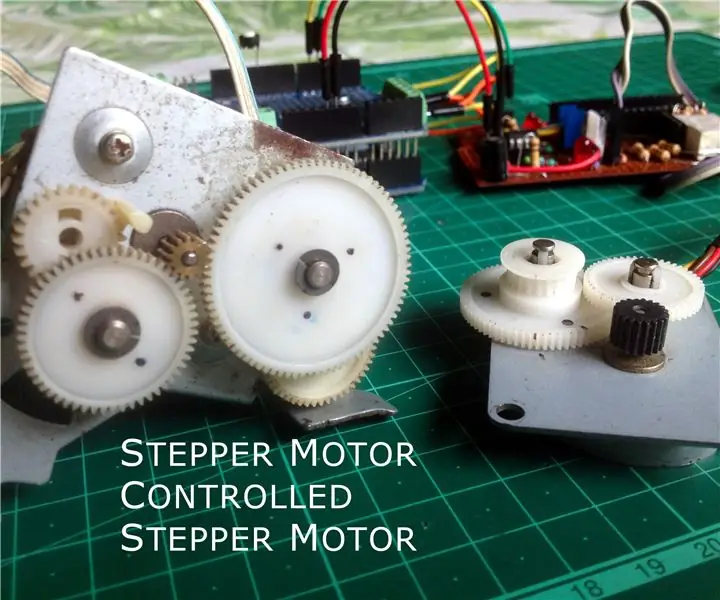
Motor de passo controlado por motor de passo | Motor de passo como codificador rotativo: Você tem alguns motores de passo por aí e quer fazer alguma coisa? Neste Instructable, vamos usar um motor de passo como um codificador rotativo para controlar a posição de outro motor de passo usando um microcontrolador Arduino. Então, sem mais delongas, vamos
Ciclop 3d Scanner My Way Passo a Passo: 16 Passos (com Imagens)
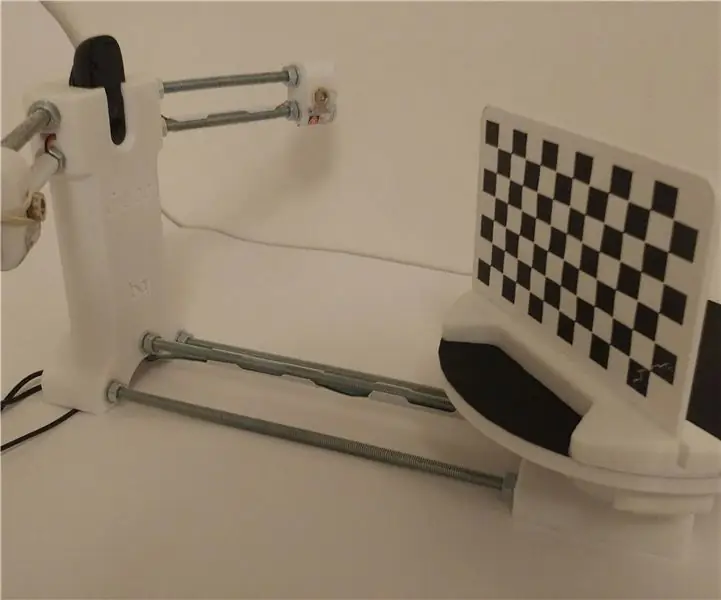
Ciclop 3d Scanner My Way Passo a passo: Oi pessoal, vou realizar o famoso scanner Ciclop 3D. Todas as etapas que estão bem explicadas no projeto original não estão presentes. Fiz algumas correções para simplificar o processo, primeiro Eu imprimo a base e depois reestilizo o PCB, mas prossigo